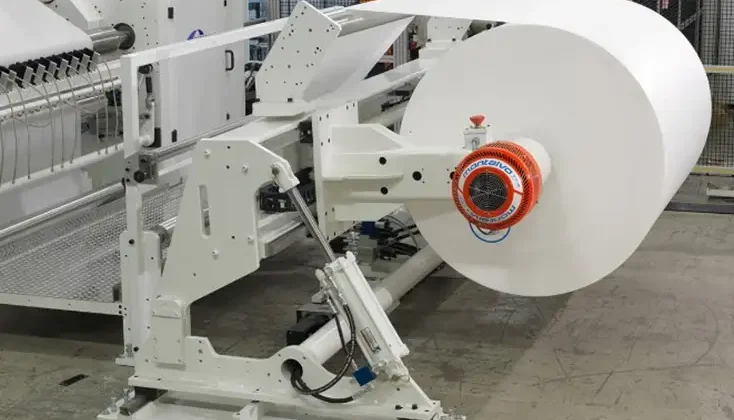
By Michael Pappas, president, Catbridge Machinery
Many converters seek to optimize their converting departments by improving slitter/rewinder efficiency. This requires understanding the causes of downtime as well as understanding how to keep machines running at the optimum speed for specific applications. Through an in-depth analysis of job and production data, converters can get a better sense of which machine features can make the most significant impact for their particular types of work. Efficiency features will vary depending on a converter’s output, production cycles and job mix. Sample data for different types of converters demonstrate how various machine technologies can affect production numbers, providing at least two to three times more productivity.
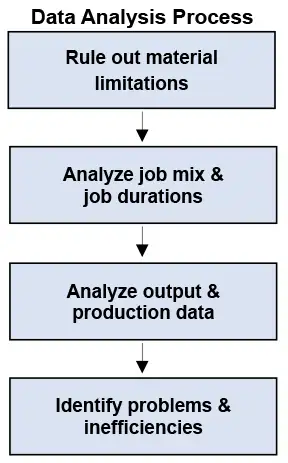
Gathering and analyzing data
Gathering and analyzing data are critical for optimizing a converting department. To identify the proper solution, converters must first identify the problem that needs to be solved. This can be achieved through a process of examining a department’s workload, including materials, frequency of job setups, level of operator intervention required, production data and packaging considerations.
Converters often advise that their machinery is unable to produce the required number of finished rolls per shift or that they struggle with various jobs, which increases their downtime. Are those limitations, however, due to the machinery or the material? Verify the source. A slitter/rewinder may not be running at full capacity, for example, because the material needs to be inspected for defects that require flagging or splicing.
The next step is analyzing job mix. Converters need to determine if they are processing primarily short-runs, medium-runs or long-runs throughout the job mix. Look at the workload of the entire converting department and the duration of different jobs. How many rewind sets or linear feet are processed for each type of job? Do most jobs have short durations, with 10 or less rewind sets, or longer durations of more than 20 rewind sets?
Workload will be an important factor when exploring options. Converters with a lot of different short-run jobs will benefit from certain features that provide easier setups, while converters with a lot of longer-run jobs will benefit from features that automate repetitive tasks.
Converters also need to look at general output and production data. For example, what range of materials does the converter handle, and what various slitting methods are used? Do the orders require a significant number of narrow cuts, or are they mainly processing wide cuts? What speed are the machines running per product type? What are the minimum and maximum diameters of finished rolls?
This analysis will help the converter identify where potential obstacles are located (see Figure 1). Is the department experiencing a significant amount of downtime, speed inefficiencies or an inability to produce the required number of finished rolls needed per shift/week/month? Are there any concerns with roll formation, finished-roll quality or costly waste? Is the packaging process causing a delay in getting the machine back up and running between sets? Is it becoming difficult to hire experienced operators for dated assets?
It’s also helpful to examine performance details. Look at the time spent on various tasks to identify factors that may have a significant impact on roll production. What is the run time for a product set? How much time is spent loading the master roll and doing the initial setup for a job? How much time is spent between sets, after the machine stops, to cut the web, tape and remove finished rolls, then load and tape new cores?
The data will guide solutions. With detailed job and output data, converters gain a better understanding of a department’s workload and the performance of current assets. They can identify inefficiencies and areas for improvement. Detailed data also provide a basis for comparing current production numbers with production numbers achieved with different technologies and equipment.
Determining solutions
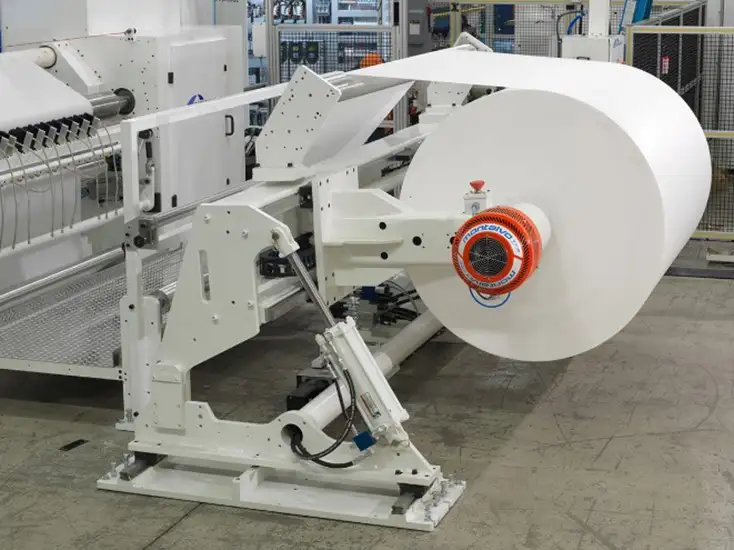
To optimize efficiency, converting departments need to find ways to keep slitter/rewinders running at the highest level for their applications. Many different technologies reduce downtime and increase run time while maintaining excellent finished-roll quality. After careful data analysis, converters can explore a range of solutions that provide the versatility, productivity and technology needed for the best possible results.
The best practices for converting efficiency will vary depending on a converter’s work. Best practices include:
- Easily moving materials on and off machines: When feasible, use shaftless floor-pickup unwinds to load jumbo rolls and cantilevered rewinds to unload finished rolls.
- Simplifying machine setups: Make setups easier with features such as short web paths, automatic knife positioning and core placement tools.
- Automating repetitive tasks: Reduce downtime between sets with technologies such as automated cut transfer, core loading and roll unloading systems.
- Increasing speed when possible: Machine speed will depend on factors such as material and slitting method.
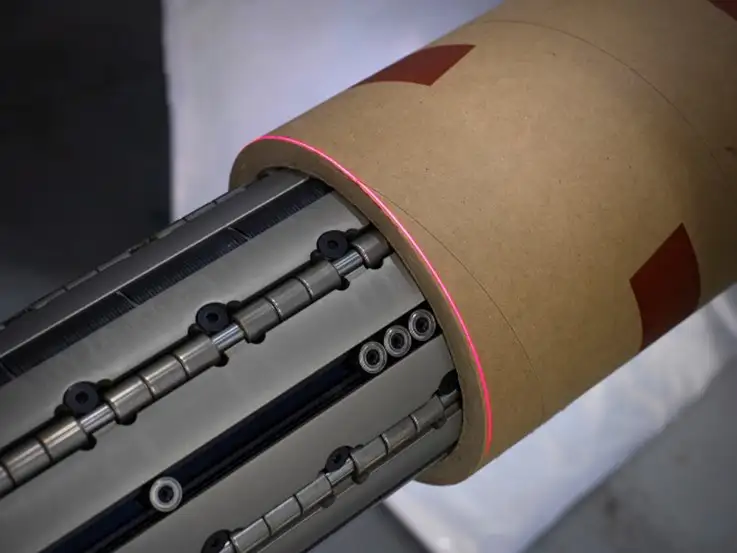
Applicable best practices vary based on job mix. For most jobs, converters can benefit from shaftless pickup unwinds (see Figure 2) and cantilevered rewinds for quickly loading and unloading materials. Converters primarily running a variety of short-run orders benefit from easy setups, using features such as knife positioning, laser core placement (see Figure 3) and short web paths. For medium-run orders, converters can look at machine speeds and automating tasks such as cutoff transfer and finished-roll discharge (see Figure 4). For certain long-run orders, automatic core loading and turrets are worth considering.
Applicable best practices depend on output and production data. Various automation technologies are advantageous, for example, when converters are producing narrow rolls with lots of setups or short-footage rolls with lots of changeovers.
Oftentimes, it makes sense to optimize new machinery for work done the majority of the time, not work done occasionally. For instance, if a converter is doing cuts over 2 in. 80% of the time, newer assets can be optimized for that 80%, particularly if the other work is at small volumes. Some departments retain an older asset for infrequent work.
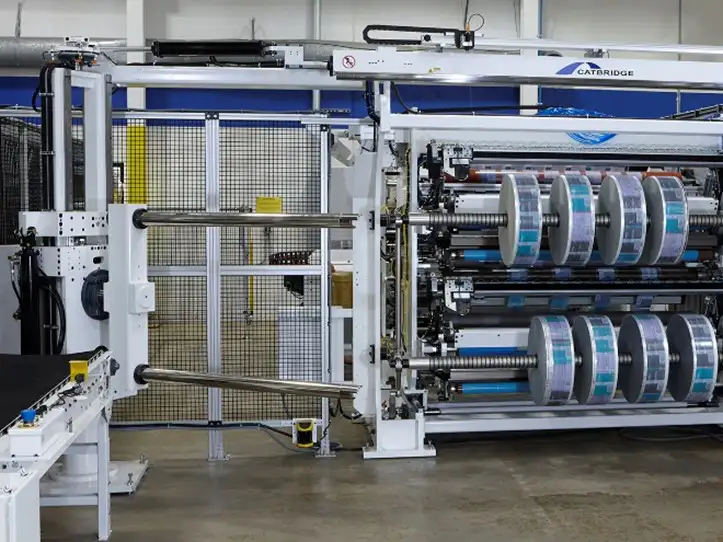
Converters can consult with an expert if they need assistance. Not all converters have easily accessible data or analysis tools. An expert can help gather and analyze data for a converting department, as well as assess different approaches for improving efficiency.
Comparing converting scenarios
The following examples compare machines and technologies in different converting scenarios (see Tables 1-3). These scenarios range from decreasing downtime between sets for repetitive jobs to decreasing job-setup times for varied, short-run jobs.
Table 1 compares production times for a surface winder vs. an automated cut-transfer center winder repetitively slitting and rewinding large narrow rolls of a paper product. The cut-and-transfer system significantly reduces downtime, automatically cutting the web, sealing finished rolls and securing the web to new cores. Additionally, an unloading system automatically pushes finished rolls off cantilevered rewind shafts and onto an unloading tree. For this job, downtime between sets is 360 secs with the surface winder and 90 secs with the center winder, resulting in a 155% increase in footage per 8-hr shift.
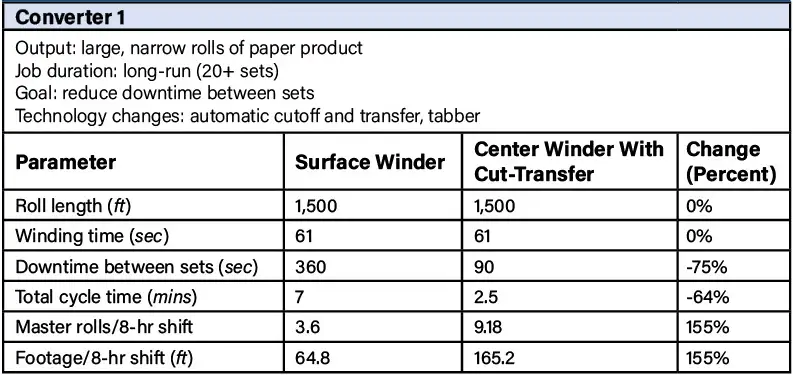
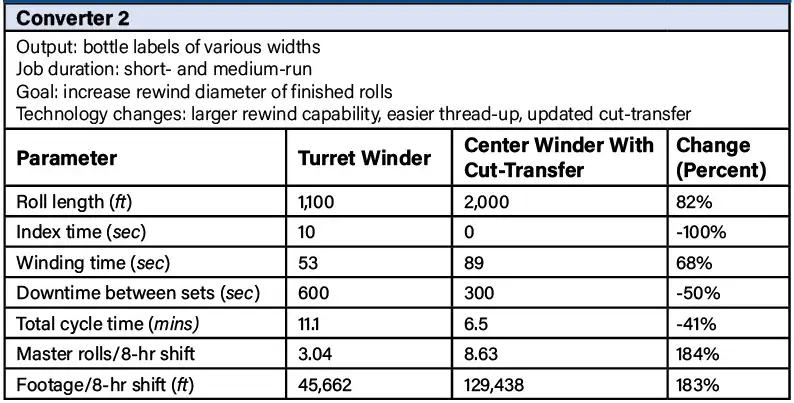
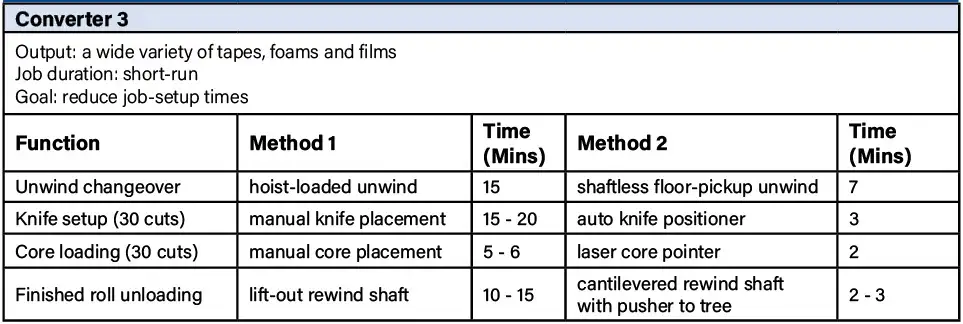
Table 2 shows the difference between an older turret with a simple cut-transfer system and maximum 24-in. rewind diameter and a center winder with an advanced cut-transfer system and 32-in. rewind diameter. Used to produce bottle labels of various widths, both machines offer technologies including shaftless floor-pickup unwinds, automatic knife positioning, laser core placement and roll unloading systems. The center winder with the modern cut-transfer, however, reduces downtime between sets and also enables easier web threading. Additionally, producing larger rolls requires fewer changeovers, allowing for longer run times. The larger rolls save time in the downstream process. If downtime were the same for both machines and only the rewind diameter increased, the converter could gain over 60% more footage per 8-hr shift. With bigger rewind diameters and improved cut transfer, the footage-per-shift increase jumps to almost 200%.
Table 3 compares the time required for various setup tasks, such as knife setup and core loading. Setup times will vary, depending on the number of cuts. Technologies that reduce job setup times are ideal for converters running a variety of short-run orders. For added versatility, newer machines offer features such as multiple slitting methods and interchangeable rewind-shaft styles.
Whether upgrading now or in the future, converters can investigate ways to reduce downtime, increase run times and improve output quality. Various technologies are available for different types of converting jobs and products. After gathering data and identifying shortcomings, converters can evaluate the impact of current slitter/rewinder technologies on current or planned work.
Conclusion
To optimize a converting department and find practical, cost-effective solutions, data analysis is key. The best solutions are based on a converter’s unique workload, product and performance data. Converters can use this data to explore a range of slitter/rewinder options, focusing in on technologies and assets that will meet their needs and substantially improve production.
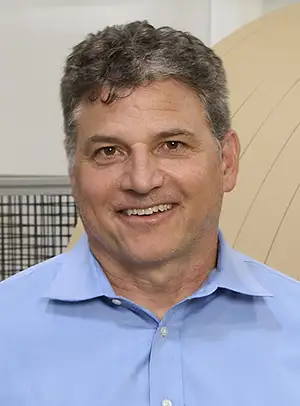
Michael Pappas, president and co-founder of Catbridge Machinery (Montville, NJ), holds an engineering degree from Bucknell University and has more than 30 years of experience in the converting industry. He has developed standard and specialized slitter/rewinders for a wide range of products, as well as extrusion, laminating, coating and printing systems. Michael has patented a variety of slitter innovations, including automatic knife-positioning systems, turret-automation technologies and specialized roll-unloading systems. He presently serves on the International Converting Exhibition and Conference (ICEC USA) Steering Committee and also is an affiliate member of the Pressure Sensitive Tape Council. Michael can be reached at 973-808-0029, email: sales@catbridge.com, www.catbridge.com.