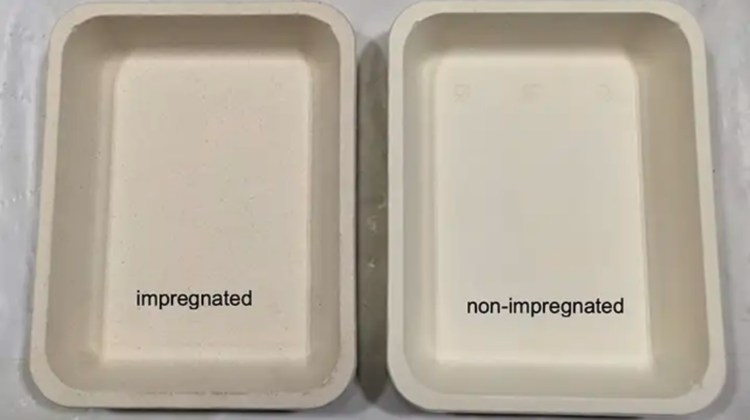
By Gene Plavnik, president, Heat Technologies, Inc. (HTI)
Editor’s Note: This technical paper describes tests with single-use, recycled paper-fiber bowls coated and impregnated with biodegradable coatings and impregnated with plant additives. The issues with flexible-paper substrates are common – sustainability and biodegradability. All results are transferable to web-based processes.
Introduction
We see the public movement in making our everyday life free of harmful chemicals, having more consumer products made as sustainable, biodegradable, compostable, growing literally day-by-day. This trend of making things around us safer has become a reality and, fortunately, is irreversible. In turn, industry responds to these demands by developing and producing innovative products from biodegradable materials that make our life and economy more sustainable.
One important area of implementation of this transition to a circular economy on the global scale is in food packaging. Specifically, we can see that sustainable paper-based packaging products slowly but surely can replace plastic ones. Discussions on biodegradability in packaging, replacing plastic with paper in various converting- and packaging-related applications, take place in various national and international technical conferences, symposia and so on.
As a result of discussion held at several technical conferences, Danish Technological Institute, (DTI), in Taastrup, Denmark, and Cellucomp, Ltd., a UK-based producer of plant-based additives and coatings Curran® and Reef®, respectively, approached this firm (HTI), a US-based company, with a request to conduct ultrasonic-drying tests of single-use food containers (such as recycled-paper fiber bowls) to evaluate economic and engineering feasibility of the implementation of these products within the biodegradable segment of food packaging. Additional examples of these applications are yogurt cups, salad bowls, containers for prepared meals, ground-meat tray packaging, single-serve cups for oatmeal and other hot cereals, sausage packaging and more.
Test background and definitions
The purpose of the tests was to establish a difference in the food-packaging properties between two groups of bowls. One group was impregnated by a sugar-beet additive, Curran, manufactured by Cellucomp, and the other one was thermoformed without any biodegradable additives. Both groups were projected to be quality-control tested by DTI after completion of the drying tests by HTI. DTI was responsible for specific tests on permeability. The tests were Cobb 1800 and moisture transmission rate (MTR) or water-vapor transmission rate (WVTR). DTI also was responsible for the delivery of both types of bowls to HTI.
The delivered bowls were of the same size, configuration and base weight. These two groups had an equal number of bowls – 16 per group. The bowls that contained the Curran additive were marked as CX, and the others that were thermoformed without it were marked as NC X. Four bowls were left as control samples and later marked as CNCX and CC X, where X – is a specific number for each sample. Cellucomp was responsible for the delivery of the Curran dispersion (coating.) A sufficient amount of the Reef dispersion was delivered to HTI for the tests.
The test program had the following milestones:
- Coat both types of bowls (impregnated and non-impregnated with Curran) with Reef coating and dry it by this firm’s Spectra HE Ultra ultrasonic dryer.
- Establish the operating parameters of the ultrasonic dryer that are needed for efficient drying, including projected physical size of the dryer, throughput range, line speed, temperature and energy consumption.
- Perform quality-control tests of the dried bowls on acceptability by major food-related technological parameters to establish the best engineering practice for the 3D containers. This was the responsibility of DTI. The bowls were to be tested for water absorption via two industry standard gravimetric tests: Cobb 1800 test and moisture (water-vapor) transmission rate (MTR or WVTR).
- If coating and impregnating of the bowls is necessary based on the above said results of the analyses, optimum range of the coatweights in grams/sq meter (gsm) needs to be established for best future engineering practices.
- Comparison of Spectra HE Ultra drying technology with high-velocity convective technology.
Following are major definitions of the related parties, the equipment, drying tests, quality-control tests and data matrix used in this test program.
- HTI Spectra HE Ultra Drying System – patented heat and mass-transfer technology that uses high-intensity ultrasound to increase mass transfer of the moisture by disrupting the boundary layer formed on the material, whether it is coated or not. In addition, HTI’s Spectra HE Ultra technology allows accelerated drying without creating migration of solids, or “skinning” of the coating, if coating is applied.
- Curran, later identified by Curran as micro-fibrillated cellulose platelets (MFCP) manufactured by Cellucomp. These platelets are derived from sugar beets. Curran is used as a paper pulp additive.
- Reef – later mentioned as Reef, an acrylic-based water dispersion, 37% solids, hydrophobic, also contains Curran MFCP.
- Single-serve molded paper-fiber bowls (impregnated and non-impregnated) were manufactured by Kiefel Technologies (Denmark) using a Natureformer KFT 90 wet-thermoforming line.
- Cobb 1800 is a testing procedure that determines the amount of water absorbed into the surface by uncoated and coated paper, paperboard and corrugated fiberboard samples in a set period of time – in this particular test, 1,800 seconds. Water absorbency is measured in gsm. The water absorbency of a material has a strong influence on the variety of converting processes. Main standards regulating Cobb tests are ISO 17025, UK standard BS EN 20535, ISO 535, US TAPPI Standard T441 and ASTM D3285.
- Moisture transmission and water-vapor transmission rate test involves a container sealed by the material to be tested, such as a cut bottom of the molded pulp tray and containing a desiccant (e.g. calcium chloride or silica gel). The weight gain or loss due to moisture permeation of the weight-gain curve is used to calculate the MTR (WVTR). The main standards regulating gravimetrical MTR (WVTR) measurements are ASTM E96-22 and ISO 2528.
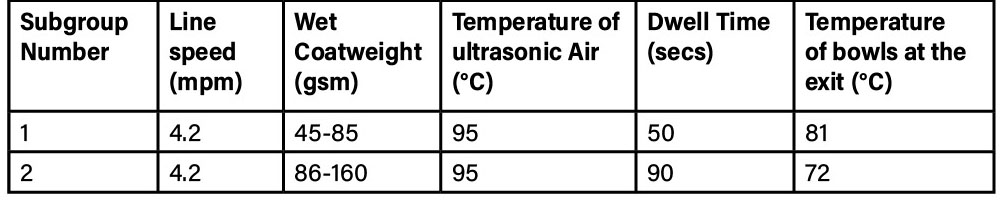
Methodology of the tests
Following are the step-by-step procedures that were used in the test program:
- Identify all measured and calculated values for the data comparison.
- Measure and calculate the area of the coating (sq. meters).
- Accurately weigh each bowl (grams).
- Coat and dry the same quantity and similar coatweights of both the impregnated and non-impregnated bowls.
- Conduct the tests at the same operating parameters for impregnated (marked as C) and non-impregnated bowls (marked as NC). That means coatweight, hot-air temperature, ultrasonics, line speed, etc., are the same and are provided by the Spectra HE Ultra ultrasonic dryer.
- Dry several impregnated and non-impregnated bowls (marked as CC and CNC) in the standard hot-air convective laboratory oven at similar operating conditions. These are the control samples (see Figure 2, described later).
- Compare control samples with samples dried by the Spectra HE Ultra dryer.
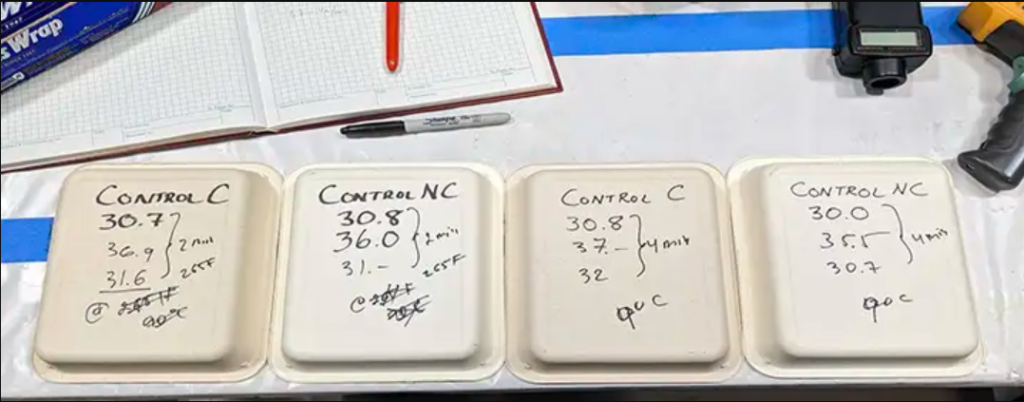
I. Measured Parameters of the Bowls
- Coated area of a bowl (full inside surface) (sq. meters).
- Mass/weight of each bowl, initial weight before coating (base weight) (grams).
- Weight of each bowl after coating (wet weight) (grams).
- Difference between the base weight and wet weight, that is the weight of the coating (grams).
- Weight of each bowl after drying (grams).
- Temperature of the bowls after drying (not to exceed 85° C at the exit from the dryer)
Calculated Values
- Base weight of each bowl (gsm)
- Area of the inside surface of a bowl to be coated (sq. meters).
- Wet weight of each bowl after coating (gsm).
- Weight of the coating (gsm).
- Dry coatweight (gsm)
- Extra residual moisture removed / bowl is not fully dried (grams and gsm).
II. Operating Parameters of the Ultrasonic Spectra HE Ultra Dryer
- Line speed (mpm).
- Temperature of the ultrasonic air (°C).
- Dwell time (drying time).
A total of 36 bowls were provided by DTI: 18 bowls were impregnated with Curran platelets, and 18 bowls were not impregnated (see Figure 1). We selected to have 16 bowls of each type for the ultrasonic-drying tests and four bowls (two of each type) to be dried in the laboratory hot-air, high-velocity convective oven. All the bowls were coated at specific coatweights and tested (see Figure 2). The method of fine air spray for the coating was used. This method is simple and easy, and a controlled way to obtain the correct wet weight for each test.
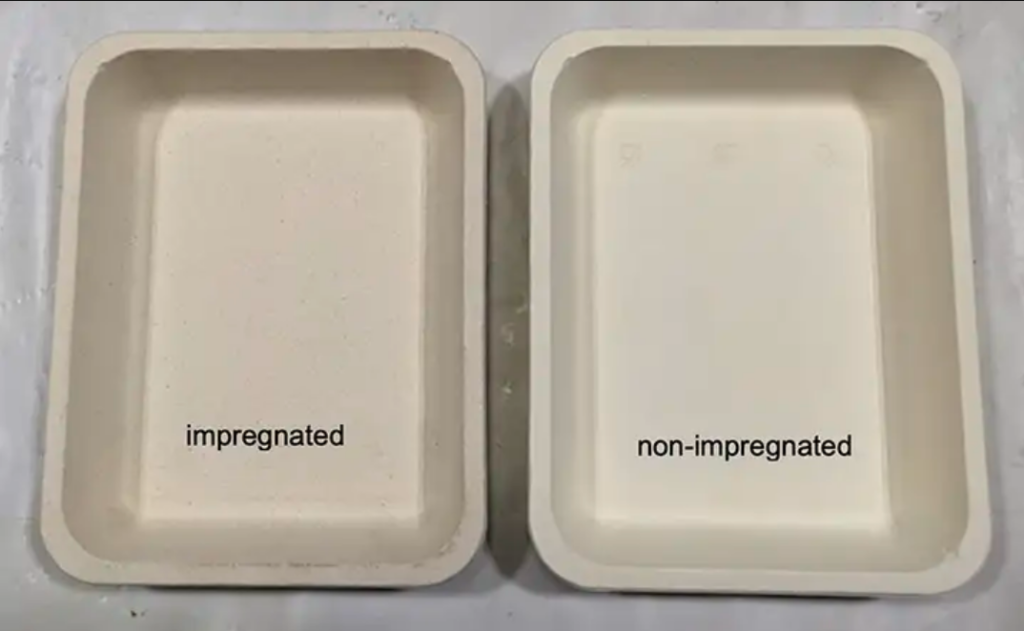
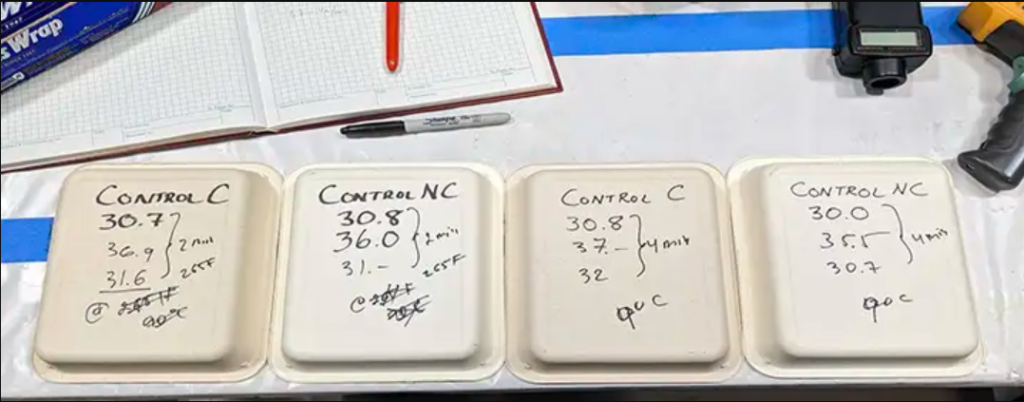
Patented, commercial-scale ultrasonic dryer
The demonstration stand consists of an adjustable line-speed conveyor from 3 to 150 mpm, with the ability to have reciprocal motion, that is to have more dwell time under the dryer chest. There are four major components in the Spectra HE Ultra drying system: 1) a three-slot-based ultrasonic dryer chest; 2) an electric heater; 3) a regenerative blower; and 4) a control panel to allow stable operation of the system. Moist air was discharged in the work zone because the relatively small amount of evaporated water will not affect the quality of drying.
Drying methodology and procedure
It was decided to divide the tests into two subgroups within each type of bowl. The first group had an average wet coatweight about 65 gsm per bowl, and the second group had an average coatweight of 120 gsm per bowl. This was done based on our practical experience with sustainable and biodegradable packaging (see Table 1).
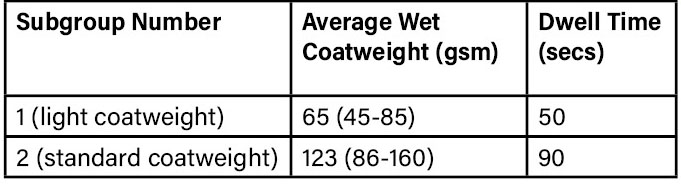
Accuracy of measurements
Following are major steps of the coating and wet/dry weight measurements: Each bowl was weighed three times – initial base weight, weight of the wet coated bowl and weight of the bowl after the drying.
- Base weight, accuracy 0.1 g
- Weight of the coated bowl after the spraying with the emulsion, and after the drying – accuracy 0.1 g
- Linear dimensions of the bowl (1 mm)
- Line speed, 0.1 mpm
- Temperature of the bowls – 0.1° C
Dry coatweight was determined as a part of percent-solids that the customer provided and laboratory-proven measurements of the percent-solids in the emulsion.
Each set of tests was conducted at identical operational conditions, such as the same amount of air, the same ultrasonic field, the same temperature of the hot air, the same distance from the jets to the product. The only difference in these ultrasonic tests was the dwell time, which represents the length of the ultrasonic dryer, based on its daily throughput. The throughput of 150,000-300,000 products in 24 hrs was taken as a target.
The dwell time was accomplished by applying the reciprocating motion of the conveyor under the dryer with the same line speed. Previous experience in design and manufacturing of drying systems for single-serve containers was taken into account to select the dwell time of the ultrasonic drying.
Both types of bowls, impregnated and non-impregnated, were coated and then dried by the Spectra HE Ultra ultrasonic-dryer module at the pre-established line speed, that was based on our practical experience. The temperature of hot air was selected based on the restriction for the coating temperature not to exceed the bowl temperature at the end of drying. Both coating and bowls should not exceed 85° C. The temperature of the ultrasonic air was installed at 95° C. High efficiency of the ultrasonically enhanced heat and mass transfer allows minimizing the difference of temperatures between the heated ultrasonic air and temperature of the bowls being dried. Based on the heavier coatweight, the dwell time for Subgroup 1 was 50 secs and for Subgroup 2 was 90 secs. All tests were conducted at the same ambient temperature and relative humidity.
As it was said in the outset of the article, there is a necessity to compare HTI’s ultrasonic-drying technology with standard high-velocity convective-drying technology (hot air). Ultrasonic drying is an advanced convective drying that is enhanced by strong ultrasonic oscillations of the heated air to disrupt the boundary layer formed on the material and provide the process with advanced mass-transfer rates. As for the convective dryer, we used a high-velocity convective oven available at this firm’s demo facility.
Originally, we set the same temperature and the same dwell time on both dryers. However, the results of the weighing show that 90 secs of dwell time at 95° C is not sufficient for complete drying of the coated bowls. That is why the dwell time was increased from 90 secs (1.50 min) to 240 secs (4 min) to obtain comparable drying.
Results of the Cobb 1800 and MTR-WVTR tests and complete data analysis
After completion of the tests, all dried bowls were vacuum-packaged and shipped to the Danish Technological Institute for further analysis on water absorbency (Cobb 1800) 1,800 secs, and moisture transmission rate (MTR – total measurement intervals – 3, time between the measurements 21.5 – 22 – 25 hrs). Bowls that successfully passed both tests were accepted as successful products. These bowls shall withstand a plurality of food applications. Results of the drying tests as well as Cobb 1800 and MTR/WVTR tests were tabulated and are presented in Table 3.
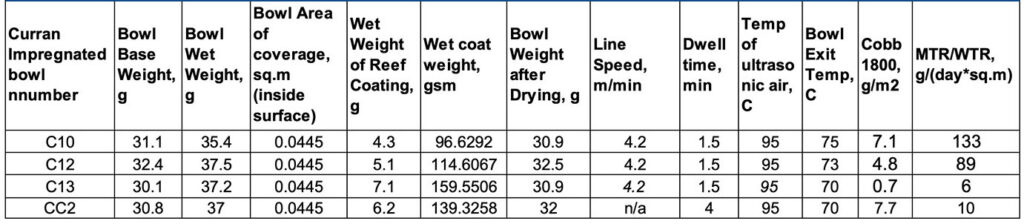
Operating parameters of the ultrasonic Spectra HE Ultra drying system to pass both tests are:
- Dryer footprint – 5.25 meters long by 2.1 meter wide at projected throughput 150,000 products per 24 hrs.
- Projected installed power 700 kW, operating power – 420 kW.
- Operating temperature – 95° C.
- Line speed – 4.2 mpm.
Conclusions
- If an end user plans to implement production of biodegradable packaging and use coatings and or pulp additives (e.g. Curran, Reef), particular tests on the permeability of the packaging material need to be considered. Furthermore, a specific application may require different coating needs. Therefore, a combination of pulp additives and coatings may need to be taken into consideration.
- The wet coatweight of the barrier coating needs to be in the range of 100-160 gsm wet weight, at 30-40% solids.
- Other types of additives and barrier coatings were not investigated during this program.
- Spectra HE Ultra drying system can be successfully used and can be of the footprint of 5.25 meters long and about 2.10-4.20 meters wide for a 150,000-300,000 products per 24-hrs throughput.
- Ultrasonic drying can be most beneficial for production with a limited installation area due to its advanced removal of moisture rates (2.5 to 3 times higher, when compared with standard methods).
The author would like to thank Danish Technological Institute for engineering and research services. Contact DTI at +45-72-202000, www.dti.dk. For products manufactured by Cellucomp, Ltd., contact +44-1592-870335, www.cellucomp.com.
Gene Plavnik, president of Heat Technologies, Inc. (Atlanta, GA), holds a Master of Science in Heat and Mass-Transfer Engineering. He has more than 35 years of experience in the development, manufacturing and commercialization of industrial and commercial heating and drying equipment. Gene can be reached at 770-804-9309, email: GPlavnik@heattechnologiesinc.com, www.heattechnologiesinc.com.
Captions:
Figure 1. Examples of the provided bowls; note the difference in color of impregnated and non-impregnated bowls.
Figure 2. The bowls impregnated (marked as C) and non-impregnated (marked as NC)
TABLE 1. Wet coatweights and dwell time, both impregnated and non-impregnated bowls for the ultrasonic-drying tests
TABLE 2. Major operating parameters of the Spectra HE Ultra dryer and wet coatweights of the bowls
TABLE 3. Cobb 1800 and MTR-WVTR test results