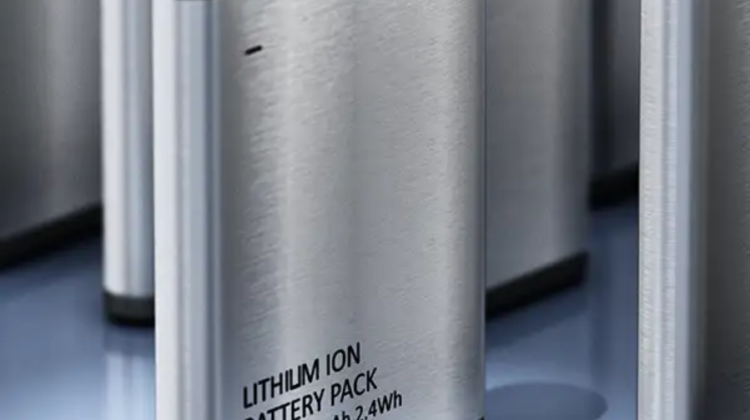
US Depts. of Energy, Labor debut new efforts to expand America’s battery-making workforce; research into recycling of lithium a key development.
By Mark Spaulding, Editor-in-Chief
Let’s face it. The dollar value of the global lithium-ion battery market – or the overall battery market, for that matter – now and into the coming decades is anybody’s guess. What may be much more important is the future demand in battery capacity and how that demand will be satisfied.
It didn’t take long for the industry to go from talking about gigawatt-hours (GWh) in 2020 to terawatt-hours (TWh) today. By some estimates, the world needs to increase battery production 30X from 2022 levels to reach a forecasted 300 TWhs of demand (see Figure 1). Production of lithium-ion batteries, in particular, will have to rise from 0.6 TWh a year to 20 TWh by 2050 for global transportation and energy systems to transition away from fossil fuels, says Benchmark Mineral Intelligence (BMI). The London, UK-based researcher regularly reports raw-material prices and other data for the Li-ion battery-to-EV supply chain.
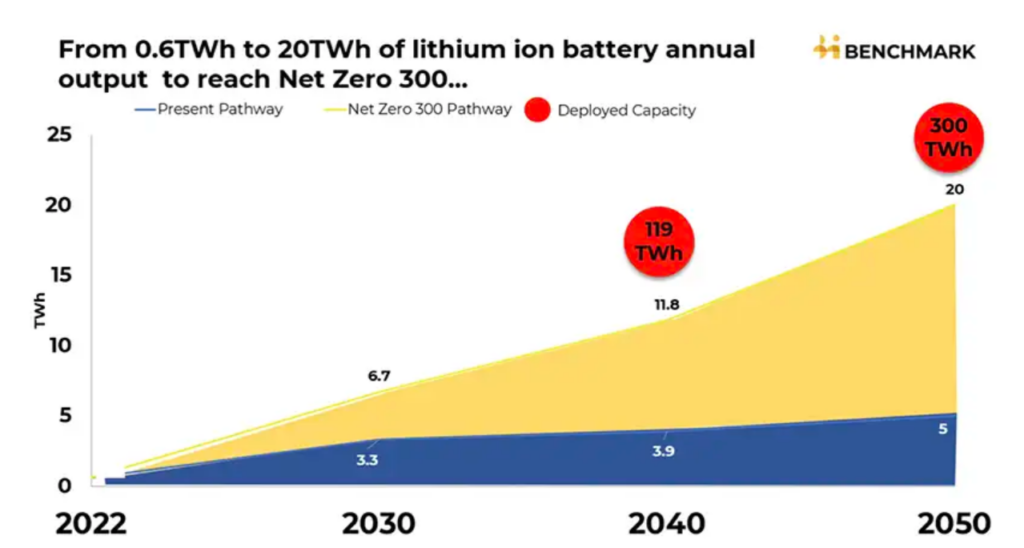
Machines still need people
So, how do we achieve this 20-TWh future? To paraphrase the joke about getting to Carnegie Hall, one answer for web-processors, coaters, laminators and full-on R2R battery manufacturers is “training, training, training.” As much as the multi-million-dollar, automated-production lines are intended to run all by themselves, it still will take people to solve problems, confirm adjustments and work to expand tomorrow’s production even further (see Figure 2).
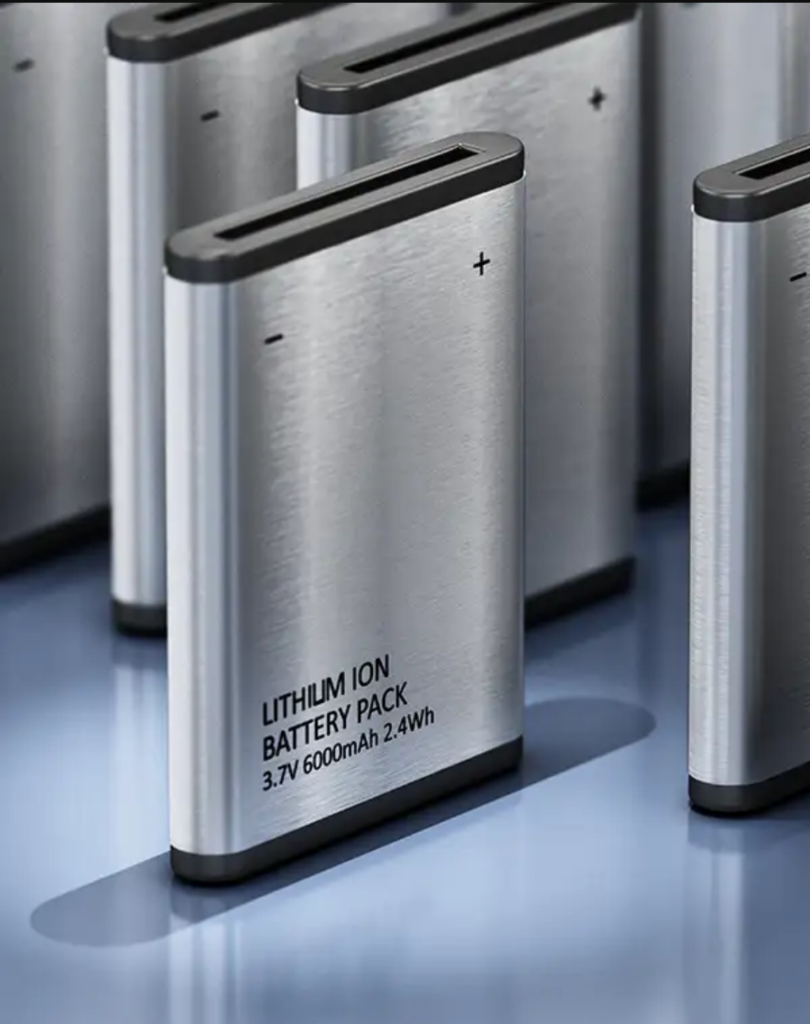
That, in part, is called “scale-up” – probably the hottest topic in the battery field today – moving from laboratory to pilot line to high-speed commercial production. Multiple presentations at the recent 2024 ARC Summit on Renewable Energy & Sustainability helped attendees get a better grasp of “scale-up,” and three papers in this supplement address the subject, all with an eye toward the long-established slot-die coating method. The extensive roster of live classroom and online ARC Converting Schools also is available, offering training in solution web coating, laminating, web handling and troubleshooting, among other topics.
Battery Workforce Initiative debuts
One specific solution to the battery-making training dilemma comes via the recently announced Battery Workforce Initiative (BWI)’s National Guideline Standards for registered apprenticeships for battery-machine operators. The US Department of Energy (DOE), in coordination with the US Department of Labor (DOL), released the guidelines that were created in partnership with battery manufacturers, community colleges and unions. The standards, which cover safety, mixing, electrode preparation, cell assembly and formation & testing, lay out rigorous training requirements to support the skilled workforce needed to staff the nearly 300 new or expanded battery facilities since 2021.
The new standards are intended to inform BWI training materials for companies and training providers. Curricula currently is under development to support DOE’s broader efforts to deploy workforce-education activities for battery manufacturing. As of press time, the National Energy Technology Lab was to launch BWI Pilot Training and the Argonne National Laboratory plans to launch regional workforce training hubs this summer.
Representing a milestone for national workforce strategy, the new standards seek to provide a rapid expansion of high-quality training and education programs in advanced battery manufacturing. By facilitating upfront industry engagement, the DOE-DOL collaboration speeds up DOL’s approval process for new battery-training programs and provides the foundation for national credentials. The BWI materials create a clear pathway for training sponsors to leverage public funds for workforce development, meet the needs of battery manufacturers and provide career-track pathways for workers to succeed and advance in the battery manufacturing industry.
Battery-making is only half the story
So, that 20 TWh of annual Li-ion battery production would require about 50 million to 60 million tonnes/yr of raw materials, BMI estimates. This would require a 20X increase in the lithium supply alone to 12 million tonnes/yr, not to mention significant increases in the supply of other raw materials such as nickel, cobalt and manganese.
Where will that all come from? While mining could account for half, battery recycling could make up another 40%, the consultancy says.
Recycling electrical and electronic waste such as Li-ion batteries and computer motherboards is problematic and particularly complex when the elements this waste consists of are critical raw materials (CRM) that also are scarce and non-renewable. The RECRITIC Project, developed by Spain’s AIMPLAS, the Plastics Technology Centre (Valencia), now is highlighting the importance of recovering and recycling the CRMs identified by the European Commission for their economic importance, scarcity and strategic relevance, given that these materials are essential to produce technological products and applications (see Figure 3).
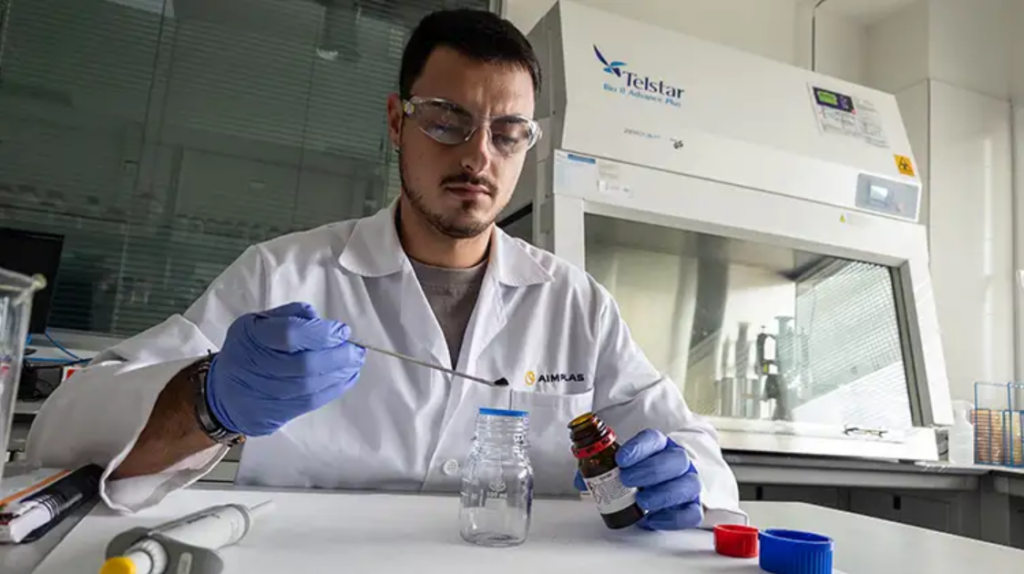
CRMs just about everywhere
“Critical raw materials such as lithium, gold and silicon can be found in everyday electrical devices like mobile phones and computers,” explains Eva Verdejo, lead researcher of the Chemical Recycling Group at AIMPLAS, “but they help build infrastructure for alternative energy sources such as wind, solar photovoltaic and solar thermoelectric energy. Therefore, these materials are critically important in the transition to cleaner, more sustainable energy sources.” The RECRITIC Project would “allow us to move toward complete recycling and zero landfill, a transformation aligned with European, national and autonomous community legislation in terms of a circular-economy model,” she adds.
To achieve this ambitious goal, the project is identifying different processes and technologies for mechanical, chemical and biological recycling, not only of all batteries and electronics but also the plastic elements that tie components together. Besides collaborating with the recycling companies involved, RECRITIC will work with Spain’s Universitat Jaume I to assess the environmental impact of CRM chemical and biological recovery processes.
A generation from now, whether global battery demand matches today’s forecasts or not, the R2R web-processing industry and its professional scientists, engineers and operators will be on the forefront of new product development and efficient, cost-effective production.
Resources
- Benchmark Mineral Intelligence, Ltd.: https://source.benchmarkminerals.com
- ARC Converting Schools: www.rolltoroll.org/education
- Battery Workforce Initiative: https://netl.doe.gov/bwi
- AIMPLAS, the Plastics Technology Centre: www.aimplas.net
- Universitat Jaume 1: https://www.uji.es