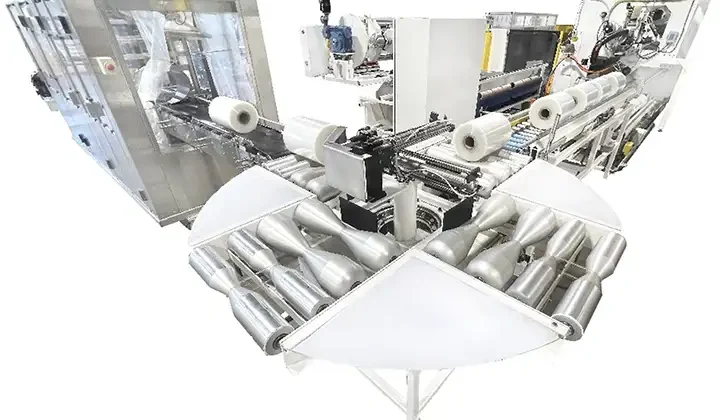
By Tom Kepper, P.Eng., general manager, Pinnacle Converting Equipment & Services
Introduction
The long-term demographics of the US labor force are not favoring the domestic manufacturing environment. Additionally, many of the educational opportunities point new entrants into segments of the labor market outside of the factory. Automation is one of the trends that may help ameliorate this trend and its impacts on domestic manufacturing, but there are initial and ongoing cost implications. These changes also require some different methodologies beyond the traditional 18-month payback to invest in new equipment.
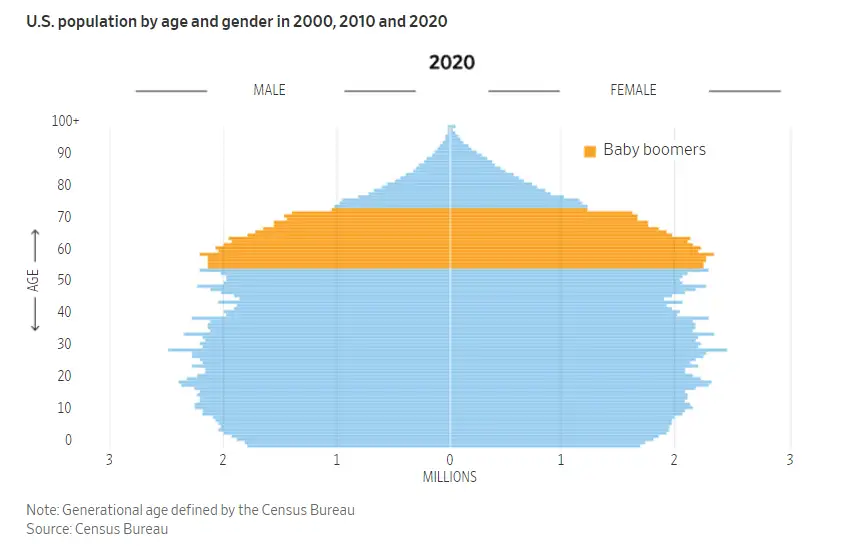
Let’s first explore the long-term demographics of the US population. The “Baby Boomers,” who were born after World War II, were the largest generation of Americans. Born between 1946 and 1964, there were a total of 76 million births during this time frame. The youngest Baby Boomer will turn 65 by 2029, five years from now. Unfortunately, the replacement generation of 5- to 24-year-olds constitutes a much smaller block of individuals at 43.8 million births (see Figure 1) (Source: US Census Bureau).
Workforce participation rates also have been in steady decline since 2000 (see Figure 2). In March of that year, the workforce participation rate was 67.3%. In February of 2020, immediately prior to the COVID-19 shutdown, that rate had dropped to 63.3%. After a precipitous, short-term drop in March of that year, the participation rate mostly has recovered, but it continues to trend lower and reached 62.8% by August 2023.
Additionally, compare the overall US civilian labor-force growth vs. the changes in the manufacturing labor force (see Figure 3). As far back as 1939, the overall US civilian labor force was 60 million people, and the manufacturing labor force was 9 million (or 15% of the overall workforce). By January 2024, the overall workforce had grown to 167 million individuals, while the manufacturing workforce grew to 13 million (or only 7.8% of the overall workforce).
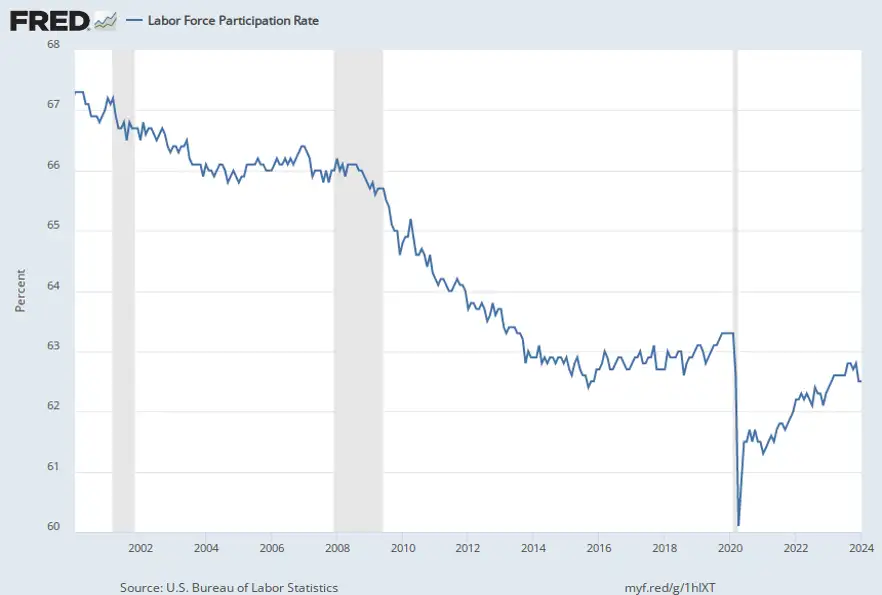
Meanwhile, the recently passed Infrastructure Act and Chips Act have estimates that these laws will produce an estimated 871,000 and 277,000 jobs, respectively (Source: Moody’s, Semiconductor Industry Assn.). It is safe to assume that in geographic locations that are set to benefit from this government intervention, there will be additional competition for individuals currently employed in the manufacturing sector.
Workforce and productivity go hand-in-hand
So how will existing industries that are not expected to benefit from these interventions going to compete for talent in a smaller skilled labor pool? Via innovation and automation of their own.
A general rule of growth is as follows: Economic Growth = Workforce Expansion + Productivity Gains
Between 2014 and Q2 2023, manufacturing industrial production growth has averaged 0.8% annually, while the average growth in manufacturing employment has been only 0.2% (see Figure 4) (Source: BLS, Board of Governors). Based on those numbers and the formula above, if an organization has an expected top-line growth rate of 8% a year, it would be required to add 7.2% more workers. And where will these workers come from, as we have seen downward trends in the manufacturing labor force?
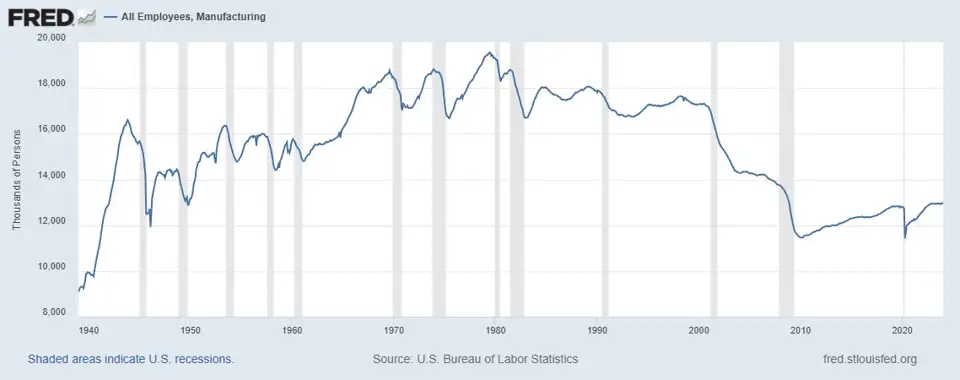
Some companies have developed their own internal training programs, but there generally is no guarantee that the graduates of these programs will remain employed by the company beyond any required commitment period. The alternative is to flip these numbers and increase manufacturing productivity while essentially maintaining the existing labor pool.
Another barometer is with the labor-force average hourly earnings rate, which has been increasing by 3.92% per year over the last 10 years (Source: US Labor Dept/Fed Reserve of St. Louis). With wage growth significantly outpacing productivity growth, the long-term profitability of most companies will require increasing manufacturing productivity.
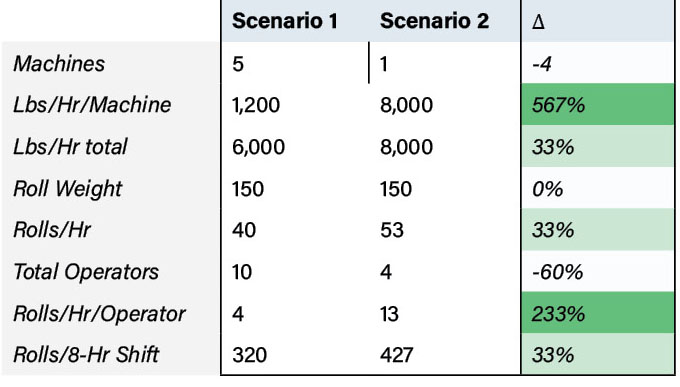
Higher manufacturing productivity is vital
Productivity gains and innovation are hard to come by and often difficult to quantify. One example of a positive breakthrough in manufacturing productivity was the widespread adoption of 3D CAD/CAM tools in the 1990s. Moving from manual milling machines to CNC machines tied to 3D-modeling tools significantly increased traditional machine-shop production and made the new generation of mills interesting to the next generation of operators, many of whom already were comfortable using computers. However, in the converting space, more specifically with slitter/rewinders, the progress of technological innovation often lacked those innovative breakthroughs. With more powerful PLCs and the continued improvements in electronics as a whole, that old paradigm is changing. Let’s look at two scenarios to examine this statement in greater detail.
Scenario 1: On a typical duplex slitter/rewinder with differential rewind shafts used to slit and rewind blown films, two operators are able to run 1,200 lbs of material/hr. This output is reasonable but certainly not enough to keep up with the slitting & rewinding requirements of multiple blown-film extrusion lines. Adding a total of five non-turreted machines would require 10 operators and result in 6,000 lbs of material running every hour or 600 lbs/hr/operator.
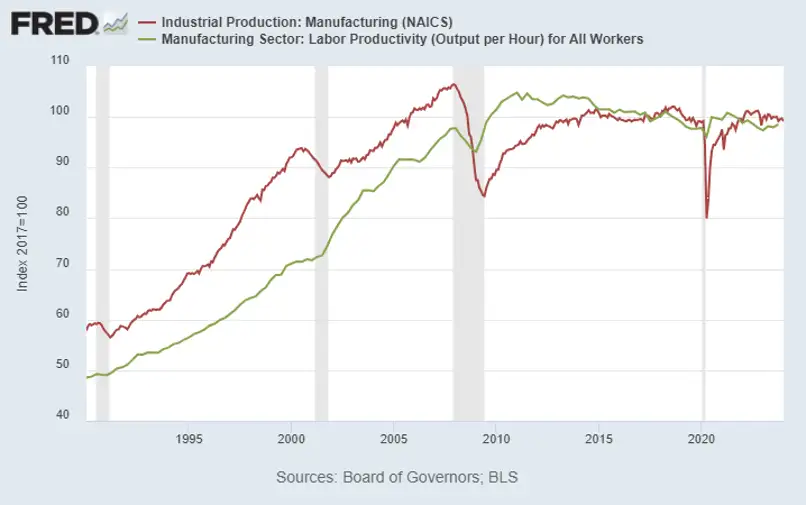
Recent machine developments are enabling significantly more throughput in the course of a typical 8-hr shift. Shaftless-unwind stations provide the ability to load rolls without operators handling a heavy shaft; splice stations allow throughput to continue without re-threading the machine; side-load blade-monitoring systems reduce blade wear; automatic core loading, leading roll edge & end-of-roll tabbing minimize operator engagement; automatic doffing to an exit conveyor and robotic finished-roll palletizing eliminate intermediate roll-handling requirements. At the end of a typical 8-hr shift, the increased material output from automation should positively impact the economic growth and profitability of a company actively engaged in slitting & rewinding (see Table 1).
Scenario 2: The fully automated machine described above (see Figure 5) produces 8,000 lbs of finished material/hr with four operators. The operators are required to provide master rolls on one of the two unwinds, provide pre-cut cores for the automatic core loader and remove finished pallets after the robotic cell has palletized the finished rolls. Automatic bagging, labeling and other features may further enhance the output of the project.
It is this type of breakthrough performance that will mitigate the reduced manufacturing labor force while providing significantly greater output to provide the corporation with a greater return on investment.
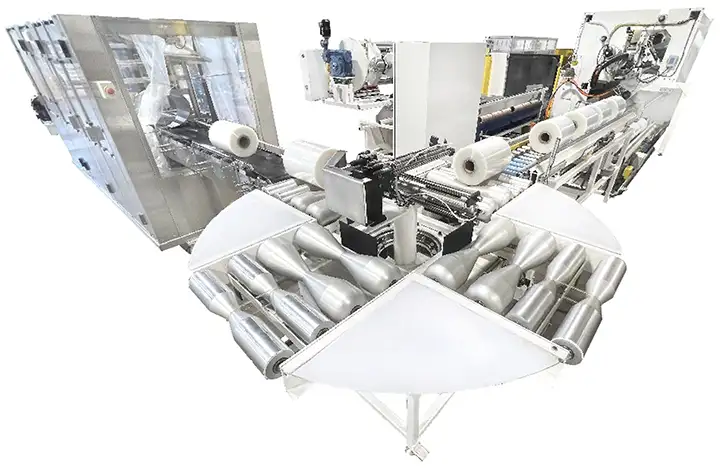
When justifying the additional cost for this type of machine, consider the following factors:
- Increased output to reduce the order-to-fulfillment cycle
- Reduced labor cost per pound of finished material over a multi-year machine life expectancy
- Improved safety with automatic core loading, web transfer and doffing
- Higher residual value of automated machinery
While comparing the following hurdles:
- Higher skill level of primary operator required
- Sales levels must be consistent with or exceed machine-output levels
- Higher initial costs
- Requirement for a skilled maintenance department
Conclusion
Innovation and automation have been the primary drivers of increased manufacturing productivity for multiple decades, not the addition of labor. Similarly, new automation opportunities have the ability to increase the output of slitting/rewinding machines. They do so by reducing operator touchpoints during the slitting process, allowing the operators to focus on finished material handling and overall machine throughput, as opposed to manual tasks such as core placement and material doffing. The initial costs for these machines may be well justified by the significant improvement in material output over the multi-decade life expectancy of the machine.
Tom Kepper, P.Eng., has been general manager of Pinnacle Converting Equipment & Services (Charlotte, NC) for the last 10 years. He holds a Bachelor’s in Mechanical Engineering from Vanderbilt University and an MBA from The College of William & Mary. Tom is a Licensed Professional Engineer and has previous manufacturing experience in both the nuclear-power and semiconductor industries. He can be reached at 704-376-3855, email: tom.kepper@pinnacleconverting.com, https://pinnacleconverting.com/.