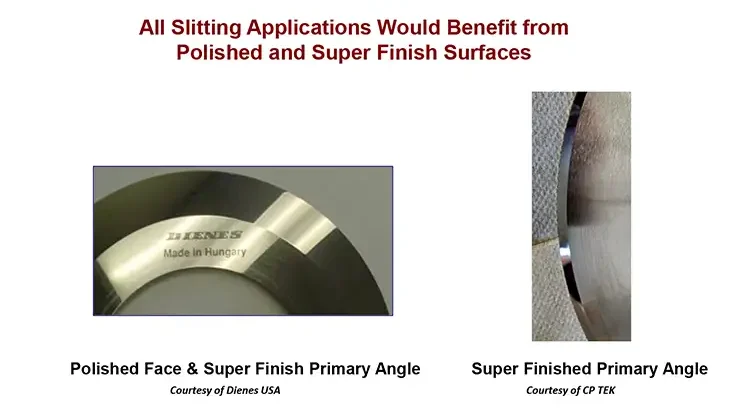
By Dave Rumson, slitting educator and consultant
Production process personnel new to the converting industry may be shocked to find out that the slitting and roll-making processes can be hair-raising experiences, both production quality-wise and physically dangerous. The reality of web slitting and roll winding is the potential for static electricity to occur that can cause excessive slitting dust to develop, along with other finished roll defects (see Figure 1).
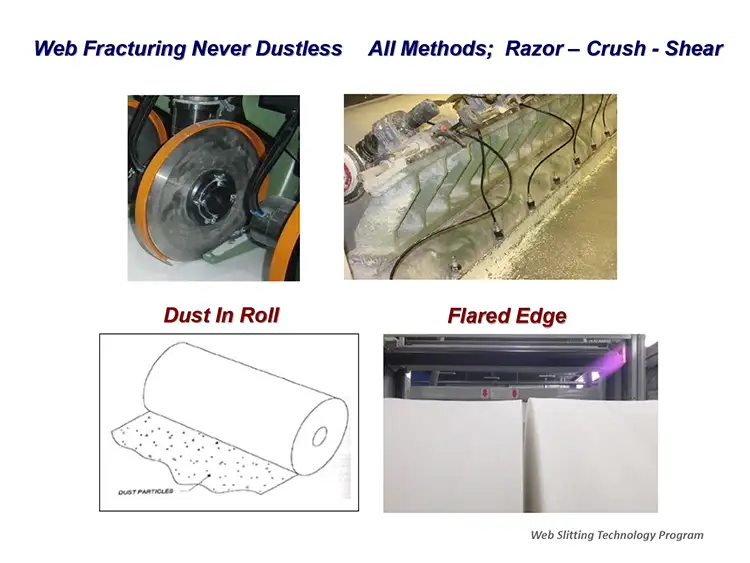
On the other hand, there are some ways the proper control of static electricity can benefit the slitting and roll-making processes. More to follow on this.
Generating static electricity
Static electricity relates to the Atomic Level Balance between two materials. If there are equal positive (+) protons and negative (-) electrons, there is no static electricity. When there’s an unequal number of positive protons and negative electrons, static electricity develops with a strong likelihood it will transfer a potential roll defect by creating an electric charge from one material to another.
Slitting can generate static electricity three different ways. These are: Piezoelectric, resulting from a mechanical strain/stress; Pyroelectric, formed by a change in temperature; and Triboelectric, developed from strong web-to-knife rubbing and idler roll contact.
Piezoelectric charges
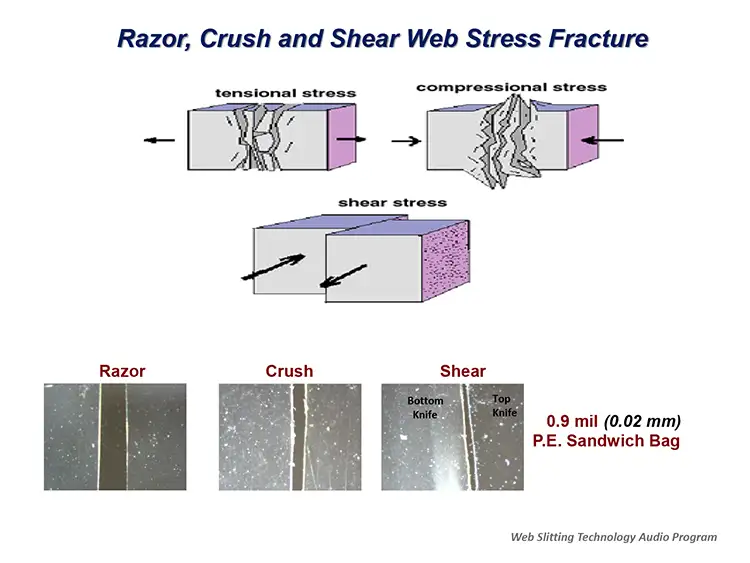
A Piezoelectric charge develops from the mechanical stresses that occur when the web is fractured and separates. Razor-blade slitting creates a tensile stress web fracture. Crush Cutting knives create a compressive stress web fracture, and Shear knives make a shear-stress fracture. The web-fracture quality varies with each of these slitting methods, and each method works better with certain web materials (see Figure 2).
Web materials should be razor slit with the smoothest, thinnest and sharpest blades possible. Ceramic and ceramic-coated razor blades offer low Coefficient of Friction surfaces. Razor blades are available in various thicknesses from 0.004 in. (0.102 mm) to 0.125 in. (3.175 mm). Thin polymer webs respond best when razor blade cut. There’s always dust development but minimum amounts when compared to Crush and Shear Slitting.
Find the narrowest blade that successfully can sever your web material. However, be sure it can handle the required cutting forces over acceptable operating time and any possible cross-machine (CD) web movement that might break the blades. If feasible, use the lower and smoother honed edge of a standard blade.
The web Compressive Fracturing Crush Cutting process creates the largest amounts of slitting dust. The moving web contacts a rounded Anvil Roll surface. A blunt and angled knife tip is pushed forcefully through it. Crush Cutting can cut a fairly wide range of materials but is most effective for fracturing tough and thick materials. Crush Cutting has a variety of knife diameters and thicknesses.
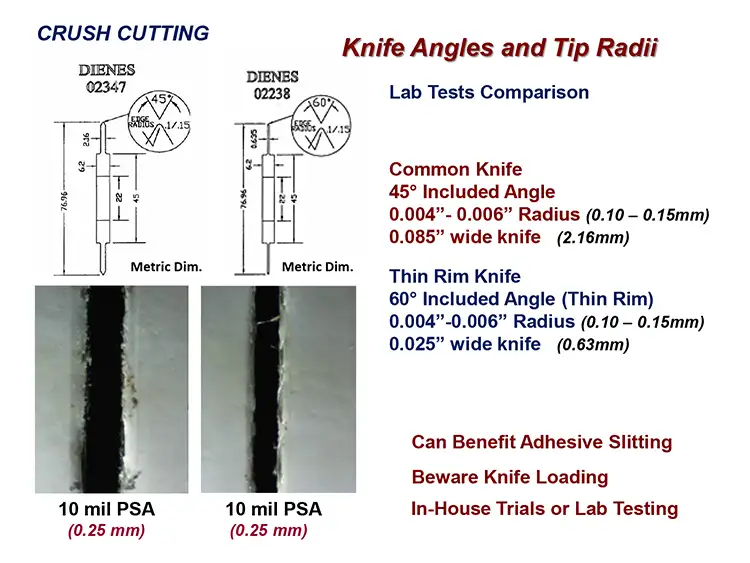
Figure 3 presents some lab test data I took years ago showing the web fracture quality difference between a more commonly used Crush Knife and a thinner special design for lessening dust levels during fracture.
Crush Cutting uses very high contact forces to fracture a web. If you do Crush Cut and this gives you the idea to look into using a thinner knife, make sure you do some in-house trials or supplier lab testing first to test for load capability and acceptable running time.
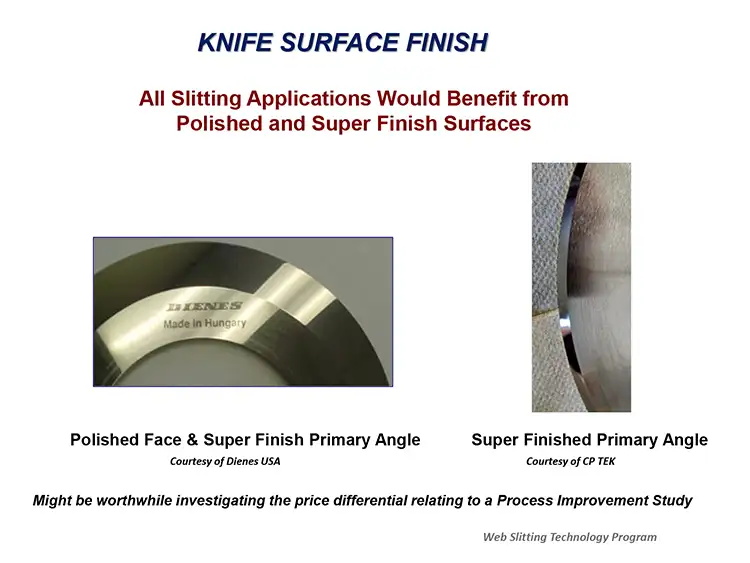
Shear knives also are available in various diameters, thicknesses and shapes. They can be highly polished or coated to reduce surface roughness that obstructs web travel after fracture separation. Super-finished Shear Top Knife cutting surfaces provide a <2 rms smoothness compared to a more standard, less-costly knife’s 8-12 rms smoothness. This shiny surface finish provides a less dust-generating web fracture (see Figure 4).
Shear Knives fracture a web by cutting both web faces at the same time with two sharp knives in contact, top and bottom, that pinch and slice the web from two directions. Shear Slitting, by far, can successfully slit the widest range of web material compositions, web thicknesses and web toughness and at the highest web speeds; to more than 9,000 fpm (2,743 mpm). And Shear Slitting, by far, is the most complex slitting method. My Web Slitting Technology Program covers over 18 Geometric and Dynamic factors of the process that can affect the finished roll quality, if not managed properly.
Pyroelectric charges
Both Pyroelectric and Triboelectric static electricity charging develop from the moving web contacting and friction-rubbing against the Razor blades and both the Crush and Shear knives. Adding to the generated heat is the metal-to-metal contact of the Crush Knife to Anvil Roll and the Top Shear Knife cutting edge in contact with the Bottom Shear Knife cutting edge.
Triboelectric charges
Kelly Robinson, Ph.D., static electricity expert and owner of Electrostatic Answers, believes that when slitting, the Triboelectric distress of two materials friction-rubbing together is by far the major reason for static electricity developing. Web to blade or knife contact is never-ending. Web speeds, web pull tension and knife surface roughness levels compound this Triboelectric effect.
Two Shear Slitting knife set-up procedures, among others, can help reduce slitting dust and roll defects. Top and Bottom Knife Overlap and Side Load Force can be set to minimum levels to reduce kinetic friction contact and heat generation. Minimized Overlap settings lessen web-traversing knife contact rubbing distance. Setting the minimum amount of top knifeholder air pressure required to fracture the web, instead of just applying the maximum shop air pressure, could extend knife life and lengthen acceptable run time. A separate air manifold might be needed for this process improvement step. I also would recommend pneumatic flow control valves to lessen unneeded high knife-to-knife impact.
These settings, of course, are web-material composition dependent, but empirical in-house testing or supplier lab testing may be worth the effort.
Note: In most Shear Slitting applications, the motor-driven Bottom Knife is in side-to-side contact with the non-driven Top Knife to rotate it during the web fracturing process. The Shear Slitting Bottom Knife circumference also is in contact with the pull-tension-driven web to slightly lift it above the web path to prevent web bunching at the Cut Point during fracture. It is rotating faster than the web speed to make sure the friction-driven Top Knife also is rotating faster than the web speed. The amount of “faster” is commonly set at 10% or more than the web speed. But the exact proper “faster” amount of knife overspeed varies based on the web-material properties and knife designs. These friction contact points and speed differences also add to the static charge levels developed.
Note, Note: The winding machine’s Idler Rolls similarly can contribute to creating static electricity, but opposite to how the Shear Bottom Knife’s circumference does it. When the somewhat-wrapped web moves over non-driven Idler Rolls under a pull tension, the rolls rotate as they support the web. But, as I have seen at a slitting facility, older winding machine Idler Roll bearings can wear down and cause a staggered resistance to rotation with web surface slippages. The winding pull tension level and varying web contact rubbing forces can intensify generated static electricity and create a Cambered web edge that negatively affects the finished roll face.
Note, Note, Note: If you have an older slitting machine, you can check non-driven Idler Roll rotation by hand for possible rotation resistance with the web out and the
power off.
Static electricity is most likely to develop when converting synthetic polymer web materials. Some of the more common polymer web materials in converting are polyethylene, polypropylene, polystyrene and polyvinyl. But as some of you know firsthand, static electricity does develop in non-polymer web materials as well. And the causes of static electricity development in the slitting and rewinding processes are the same.
Another factor to consider relating to the Triboelectric-generated electricity is that the amount of ion voltage transferred will vary based upon the two elements affected.
Figure 5has a Triboelectric Materials Chart that shows us that the more common winding and slitting machines’ component hardware, steel and aluminum, will transfer a larger percentage of voltage than gold or silver. The reality of machinery cost is that steel and aluminum idler rolls are a lot less expensive than gold or silver … duh. So static electricity-controlling steps are very important.
Also, note the extremely large ion transfer distance from polyethylene material to the human hair and skin. This caught my attention immediately because this was a near reality for me when visiting a polymer-slitting plant years ago. The closer I got to the machine the more the hair on my arms and neck tingled. I quickly stepped away.
This is a major bad caused by static electricity for its harmful potential.
Another bad static electricity effect is the potential for a strong discharge to disrupt the performance of winding machine electronic-controlling devices. This could include measurement devices to track performance, setting mechanical forces or rotating speeds on the winder.
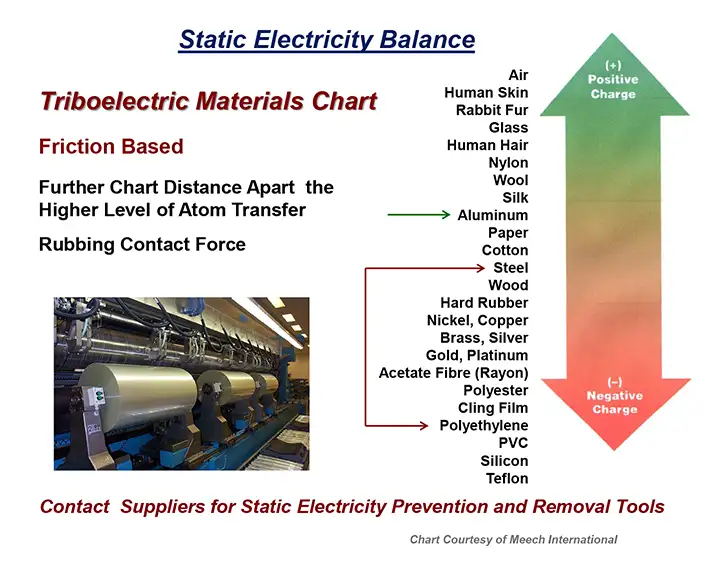
When is static electricity good?
These are some of, but not all of, the potentially bad effects from static electricity. But there are two major good aspects of static electricity in the roll-making and slitting processes.
First of all, it can be controlled and/or eliminated from negatively affecting the finished rolls. Secondly, it can be implemented into the process to provide a specific value to the finished product.
Some of the tools available to control or eliminate static electricity are anti-static agents, like amines or amides, that are added to the polymer mix during plastic making or applied to the plastic surface after manufacturing. Some of these can reduce the level of static charge that develops.
Then we have Ionizing bars used within inches of the moving web at the extruder’s output, further along the web idler roll travel to the winder and just before entering the knife-slitting zone. They remove static electricity from moving webs and are considered very helpful. It’s important not to have them mounted close to the metal idler rolls though because the bar’s effectiveness can be reduced.
Ionizing curtains also deliver static-neutralizing ions effectively from a moving web up to 3 feet (0.9m) further away. They tend to reduce dust contamination and lessen operator shock potential.
Strings of copper tinsel placed directly in contact with the moving web deliver any web static charges to ground. They are low cost compared to ionizing bars and ionizing curtains. But the obvious concern would seem to be for their copper strands to potentially being pulled from the string and ruin the finished roll.
Another effective way to reduce static electricity charges on moving webs is to maintain a high humidity level around the machine. A humidity level of 55% RH is supposed to have enough moisture content to ground static charges.
Consideration for use of any of these or other static eliminators typically requires consultation with a static consultant or related suppliers.
Now, what is so good about static electricity? The major good is that it can be eliminated and controlled. But it also can be used to benefit the sheeting and roll making processes. Here are two examples:
Sheet Stacking: After the sheet material has been made and cut, it requires stacking for shipping purposes. During this process, jamming of the sheets is possible. A static eliminator neutralizes the sheets to reducing the jamming effect and reduce machine downtime.
Non-Stop Roll-to-Roll Winding: Transferring a winding web on the fly from a finished roll surface to a non-adhesive waiting core can be accomplished with static electricity, working with specially designed and manufactured mechanical web nipping and cutting devices.
As with all the other articles I’ve written, I hope you and your company will find some benefit for your slitting and roll-making processes.
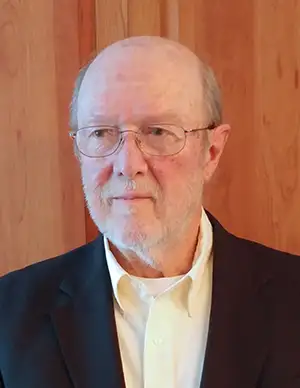
Dave Rumson has 15 years of experience as a slitting educator/consultant and 35+ years of roll /shaft handling, unwind/rewind equipment and web-slitting experience. The past 22 years include 10 years with Dienes USA and Sigmala, Ltd., the latter having developed a computer/servomotor-controlled shear knife holder. For almost 30 years, Dave has developed and conducted technical presentations for CEMA, ARC (formerly AIMCAL) and TAPPI. He currently serves on the ARC Technical Advisory Panel and its Web Handling Committee, and he writes the “Cut Points” Q&A column for Converting Quarterly. Dave also manages the 1,500-member Slitting Community Group on LinkedIn. He can be reached at 860-256-5658, email: drumson@maine.rr.com, www.drumson.wordpress.com.