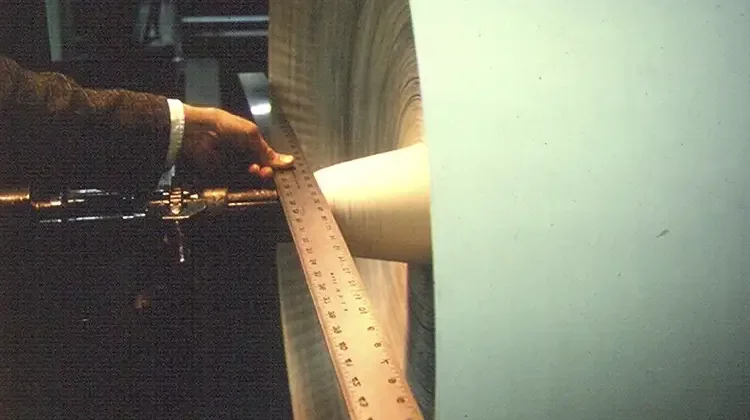
By David R. Roisum, Ph.D., principal, Finishing Technologies, Inc.
“If names are not correct, language will not be in accordance with the truth of things.”
—Confucius
Introduction
We had a big problem in web handling. That was that some words, such as telescoping, had many aliases including scoping, coning, shooting and so on. Worse yet, the same word could be used for two totally different defects. An example here is the wound-roll defect corrugations often was improperly called tin-canning (a different defect) by many in the film industry.
That big problem was almost totally solved nearly a decade ago with the latest publication of the Ultimate Roll and Defect Troubleshooting Guide [1]. This “encyclopedia” of some 500 defects codified the proper names of most things and listed common aliases for completeness. I say almost solved because, even a decade later, many people are not aware of this standard language or continue to stick with the confusing lexicon peculiar to their own plant, which may be quite different than their sister plant, competitors and customers.
Taxonomy
As useful as consistent naming might be, it does show the underlying structure among defects. This was the situation in biology some 250 years ago before Swedish botanist Carolus Linnaeus gave structure to the names of plants (and later animals), which largely replaced the common and confusing names that had been in everyday use. He introduced taxonomy to a haphazard set of information. However, this was and is no easy task. Taxonomy is both an art and a science, in equal measures, and is necessarily a work in progress.
Web handlers already have given a taxonomy to many defects [2]. A good taxonomy can be used to quickly and surely separate one defect from another, without resorting to “DNA sequencing.” This is essential so that operators, QA and customers all can use it with ease. This taxonomy usually has two parts. The major class is the outcome, usually recognizable at a glance. A subcase is what often is referred to as the root cause. However, it would be more carefully termed root-cause mechanics because, while there is a single physics, there seldom is a single predictive factor.
Core Crush
Let us begin with a simple teaching example – core crush. The major case is easy to recognize at a glance because the core loses its cylindrical geometry (For more on cores, see Vacuum Verbiage, page 20). However, and this is a big however, each of the subcases has a totally different set of symptoms and remedies. Type I core crush is a tight defect common with winding of low modulus materials. The load that crushed the core came from the interlayer pressures of winding. The failure happened during or very soon after winding. Type III is a totally different defect. First, it is a loose defect common with winding of high modulus materials. Second, the load that crushed the core did not come from the winder but rather from roll handling. Third, the core fails not during winding but rather during handling. Type II is a more rare defect where the load that crushed the core is neither winding nor handing, but rather chemical and/or thermal shrinkage of the web. BOPP plastic film is the poster child for this failure mode.
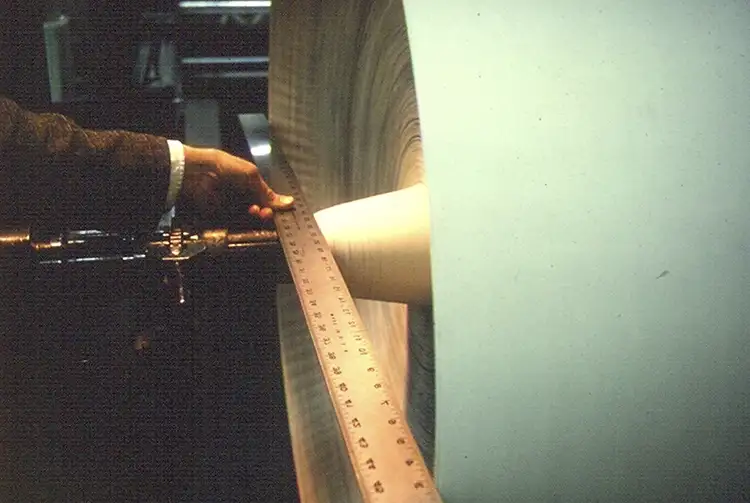
So, step one is to diagnose the major case; in this instance, core crush. This is where many people stop and make wrong guesses about remedies. Common sense would tell you to reduce winding tightness if the core crushes, but you would be correct in only one of the three subcases. Step two is to diagnose the subcase. That tells you whether to increase or decrease winding tightness via any or all of the TNTs. Step three is to redesign the product if winder tightness does not have the authority to fix the problem to everyone’s satisfaction. The easiest redesign for this defect is to change the core, such as increasing core-wall thickness.
Telescoping
Telescoping is different than rough roll edges, even though both result in roll ends that are not flat. Telescoping is when the layers of the wound roll slide upon each other in the machine direction (MD) and/or the cross direction (CD). We will not cover the 10 or so subcases here [3], because this article is about taxonomy, not defect troubleshooting, which is covered in great detail elsewhere [4]. Instead, we will just take the first two.
Telescoping Type Ia, shown in Figure 1, is by far the most common. It occurs on core-supported winders (or unwinds Type Ib). In this subcase, the layers slide near the core first in the MD, which is demonstrated with the J-line test. MD slippage then enables sliding in the CD, which is seen at a glance. Telescoping Type II, on the other hand, can occur on any winder type. Here, sliding is only in the CD. The poster child here are adhesives that do not cure, such as PSAs, or are not yet cured and thus have low “green tack.”
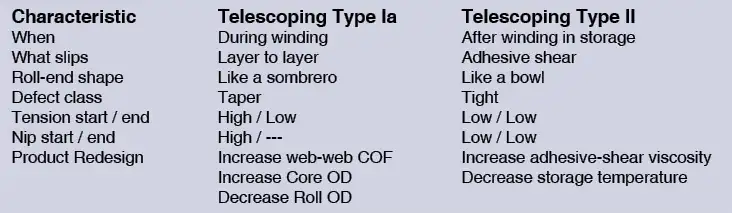
While Type I happens during winding (or unwinding), Type II happens in storage. It is like a ticking time bomb, just waiting to go off in the next few minutes to next few months. Table 1 shows just how different the symptoms and remedies are and why the troubleshooter absolutely must take the second step to correctly diagnose the subcase to get the correct remedy list.
Wrinkle
More so than telescoping, we cannot cover wrinkles in any detail, nor is there any need. It is covered in chapter-length detail elsewhere [5], and we even have a free Internet troubleshooting app to help you through the troubleshooting tree [6]. I will just show in Table 2 a list of the 20 or so most common wrinkle types that would comprise 99% of anything you would ever run into.
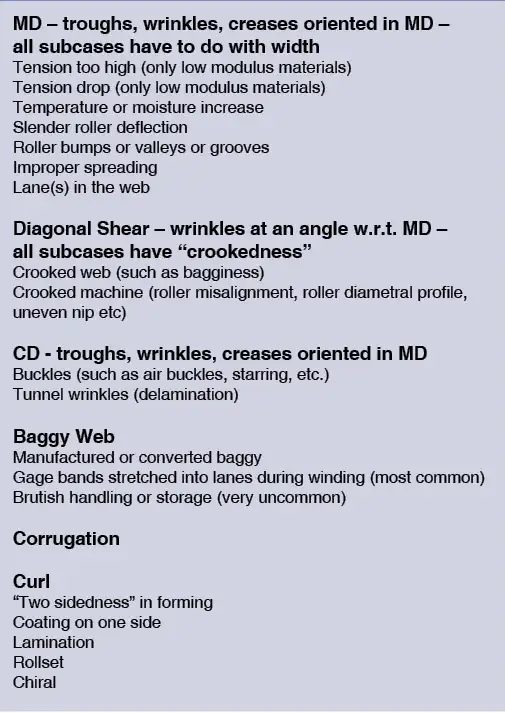
There are several things to observe with this list. The first is that the major case can be seen at a glance – sign of a good taxonomy. No Ph.D. or DNA sequencing is needed. The second is that the subcase, i.e., “root cause,” often can be found by mere process of elimination from readily known information. The third is a bit more subtle. That is that while almost all wrinkle types are “tension-sensitive,” only two of the 20 are “caused” by tension, and they are seen only on ultra-low modulus (stretchy) materials.
Why is getting the subcase so very important?
If you stand back and look at the defects presented thus far, you will notice that some defects are tight defects, some are loose defects and some are not affected by tightness much or even at all, and this is true even within a single major case of defects. This is why common tropes such as “It is best to wind loose or with maximum taper,” are hopelessly naïve. Applying the correct remedy for the wrong defect type is, well, wrong. It will just waste time and money and further risk the ire of the customer. Furthermore, after the tension/tightness knobs have been played in the correct direction for a specific defect, you will then need to redesign the product to reduce defect rates and severity any further. Some products, no matter how desirable for other reasons, might not be economically transported or wound.
Another aspect of diagnosing subtypes is important if you want to do trials and want useful measures of severity. Science and taxonomy both inform us on which measures are more likely to be sensitive to a specific defect. Measuring pounds of internal rejected waste or counting customer returns seldom will work well for many reasons. First, rejection is subjective and thus adds noise to the already noisy process. Second, and most importantly, it is likely that several different defects are lumped together in the same bin. Bad-looking wound rolls and wrinkled webs could be a catchall for one, two or perhaps 10 totally different winding and flatness issues seen by a customer, on a product or in the plant.
Do you need to classify everything?
Absolutely, otherwise you would not know for sure what a customer is complaining about or an operator is referring to. Thus, each trouble must be uniquely named with no gaps or overlaps. There are many resources to help you here [1,5,7]. However, that does not necessarily mean that taxonomies need to be generated. Recall that the primary utility of taxonomy is to help make diagnostics quicker and surer so that we can proceed to remedy lists, decision-making and implementation.
If you have a slip pimple, for example, the problem can be diagnosed at a glance because there is nothing that looks like it. Also, while a slip pimple is a tight defect, grouping it with other tight defects does not improve the understanding of the winding and defect mechanics very much at all. While slip pimples begin with a seed of contamination, sometimes slitter debris, no insight would seem to be gained if slip pimples were grouped with other debris complaints, such as fouling of printing equipment from paper slitting dust.
In a similar way, I suspect that cutting/slitting defects also might not benefit much from taxonomy. If you have bottom band axial wobble, you may see “slitter” rings on the ends of very flat rolls. Would you benefit in understanding by grouping it with radial wobble, which also can cause slitter jumps? Probably not. In either case, you would up your band grinding and mounting and motor-shaft runout game. Perhaps someone more knowledgeable or clever than I might come up with a slitter-defect organization that is widely applicable beyond merely listing defects or listing best practices.
While not web handling, several attempts have been made to name and classify coater defects [8]. I sense that this effort has not been as successful because there are a lot more coater types than winder types, for example. There also are many more coating and web chemistries which matter, while web handling is almost totally agnostic to chemistry and just concerns itself with a handful of material properties to do the bulk of its work. Nonetheless, separating coating streaks from coating bubbles, for example, will help speed up finding the specific defect you are working on, even if a useable taxonomy has yet to be devised as far as I know.
Bibliography
- Smith, Duane. Ultimate Roll and Web Troubleshooting Guide. TAPPI Press, 2013.
- Roisum, David R. A Taxonomy of Web and Winding Defects. 15th Int’l. Conf. on Web Handling. Web Handling Research Center, Stillwater, OK. June 2019.
- Roisum, David R. Diagnosing the Wound Roll Telescope. AIMCAL Coating/Handling Conf., October 2014.
- Roisum, David R. Web101SM short courses.
- Roisum, Walker and Jones. The Web Handling Handbook. Destech 2020.
- Abbott, Steven. Wrinkle Troubleshooter. AbbottApps.
- Roisum, David R. Dave’s Defect Series. Web201.68a-z, AllWebHandling channel on YouTube.
- Gutoff, Edgar B. and Cohen, Edward D. Coating and Drying Defect Problems – Troubleshooting Operating Problems. John Wiley & Sons, Inc., 1995.
Dr. David R. Roisum, principal of Finishing Technologies, Inc. (Neenah, WI), is an authority in the area of web-handling and converting. He worked for Beloit Corp. as a designer of winding machinery and later as a research manager, and for Kimberly-Clark as a converting expert. David has accumulated much practical experience working in 1,000+ plants over the course of nearly four decades. He also writes the “Web Wise” Q&A technical column and moderates the Web Handling & Converting Technical Topics Channel for this publication. David can be reached at 920-312-8466, email: drroisum@aol.com, www.roisum.com.