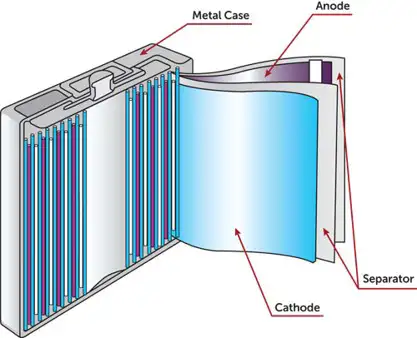
By Scott Zwierlein, coating process engineer, FRONTIER, a Delta Modtech Co.
In an era when battery technology is advancing at a record pace, it is important to ensure that battery manufacturing is capable of keeping up. In many cases, the accuracy and precision of the coated electrode are what can make or break a new technology. For example, it may be imperative to control the mass of anode or cathode loading to within +/-2% or better. Also, with the introduction of new, exotic and expensive raw materials, it will be important to minimize waste from excess coating or exposure to contaminants. Different types of current collectors used as substrates for electrodes may present difficulties in the coating process. All coating methods are not alike. The electrode-coating method should be evaluated to determine whether it can produce electrodes that conform to these high standards. This technical paper will address the advantages and disadvantages of a number of coating methods to provide the tools to evaluate which process will best suit your technology.
Editor’s Note: This technical paper is based on the author’s presentation at the AIMCAL R2R USA Conference, held in Orlando, FL, in October 2021.
Introduction
With the increase in electric-vehicle (EV) sales and portable electronic-device usage, battery manufacturing is booming. The seismic shift is spawning new innovative approaches to improving battery performance – and a golden opportunity for the converting industry. According to research firm Reports and Data, the global battery market is projected to grow from $119 billion in 2020 to $328 billion in 2028.
The use of batteries in products such as EVs and wearable devices continues to push the innovation envelope, but it likely will adhere to the following criteria:
- Make batteries smaller.
- Make batteries deliver more power.
- Make batteries safer.
- A combination of 1-3.
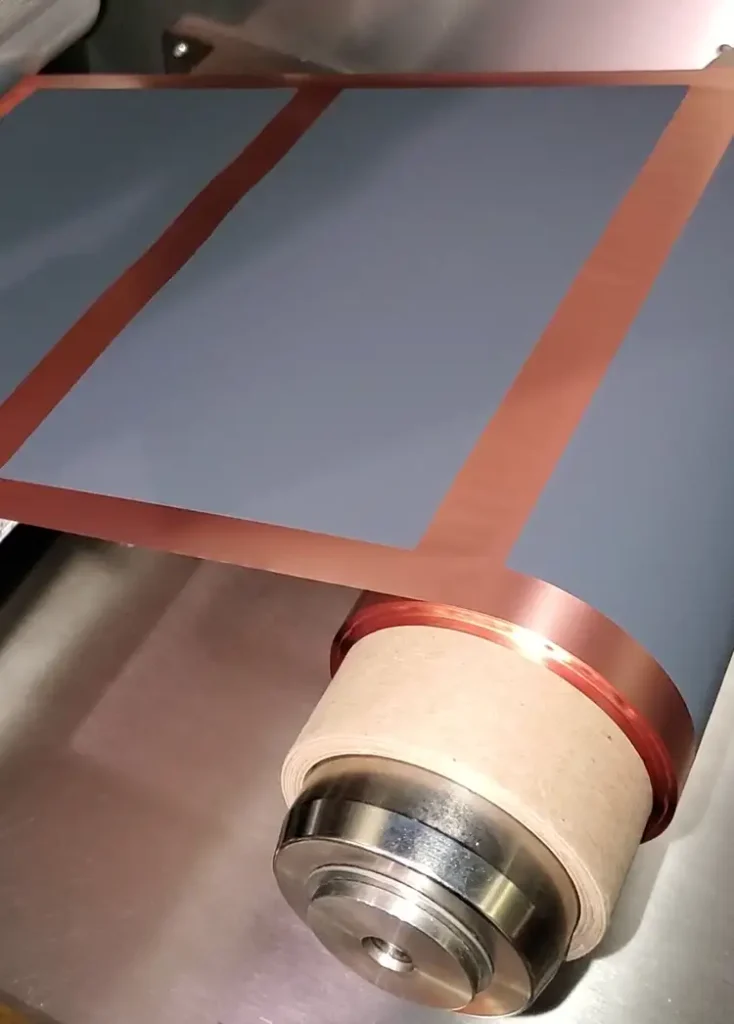
The converting industry can influence innovation particularly in the realm of battery-electrode coating (see Figure 1). In broad strokes, the higher the quality of the coating on those electrodes, the higher the quality of the battery (We’ll break down what defines quality below.).
This is a great opportunity, but also a formidable challenge, as the shrinking size of batteries necessitates thinner coating layers that must be just as accurate and preciseas their thicker counterparts. As it refers to the coating process, accuracy is the ability to coat at your target thickness from one coating run to the next. Precision, on the other hand, is producing on-target coating thickness continuously throughout a coating run. Let’s take a closer look at the role of coating within battery manufacturing.
Technologies may change, but methodology not so much
The majority of today’s battery-electrode coating slurries are composed of a carbon, graphite and binder, coated in a thin film onto a current collector (typically, an aluminum foil is used with the cathode, and a copper foil for the anode). These thin films then are layered upon each other with a separator in between. The films can be stacked in a rectangular shape or wound together (see Figure 2). The current collectors at the edges or tips of these films are bonded together by tabs in a welding process, thus allowing like electrodes to be combined.
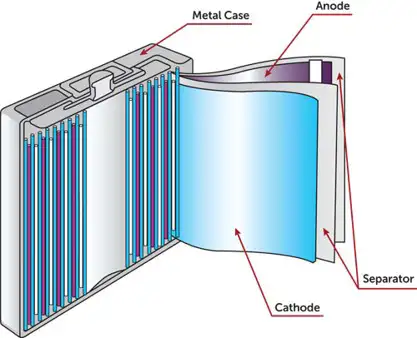
This methodology likely will not change with the advent of new battery technologies, no matter what new materials are used in the slurry; thus, the need to improve the coating process, and ultimately improve the quality of the layers, is paramount. Improving coating quality can be broken down into five areas:
- Thinner coating
- Better uniformity
- Defect reduction
- Less waste
- Safety
Understanding the two coating methodologies
Now that we’ve defined quality parameters, let’s take a closer look at two differing coating methodologies: Mechanical metering and volumetric metering.
Mechanical metering is when two mechanical surfaces create a gap that is equal to the desired coating thickness. The fluid then is distributed onto the substrate as it moves through the gap. To change the thickness, you need to mechanically adjust the spacing between the two rollers. Three types of mechanical metering include Knife-over-Roll, Comma-Roll and Roll Coating.
Volumetric metering is where a specific volume of fluid is dispensed onto the substrate surface. Instead of a mechanical metering of a gap, we have a pump that delivers a fixed volume, equal to the desired coating thickness. You simply adjust the pump to change the thickness. The lone volumetric pre-metered system is Slot-Die Coating.
Now let’s consider the performance of those methodologies in relation to both today’s and future battery-electrode coating requirements, and which one is optimal.
Quality Goal #1: Thinner coating
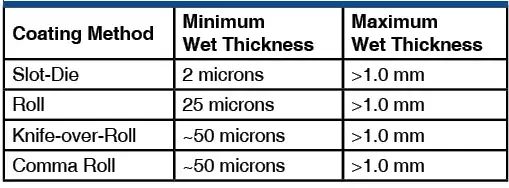
In comparing the coating methods, slot-die allows for the lowest minimum, achieving as low as 2 microns of minimum wet thickness (see Table 1). It’s important to note that most battery manufacturing requires minimum coating levels only near 25 microns, which means roll coating may be acceptable. However, if we follow the marketplace trend, thinner coating will require smaller wet-thickness minimums. It should be noted that all the methods allow for a maximum wet thickness over 1.0 mm.
Quality #2: Better uniformity
Uniformity is another critical factor. It’s a measurement of the highest point of variation in the thickness of material at any point on the film. The lower the variation, the better.
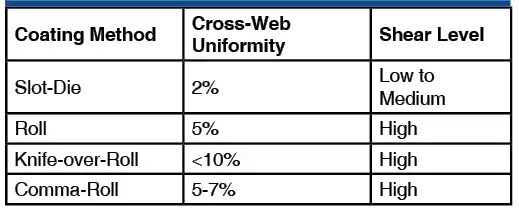
Precision plays a role here, and because the material is volumetrically pre-metered, slot-die coating leads in this category as well, with a cross-web uniformity of +/-2%. It also boasts a machine-direction uniformity of +/-1%.
Shear has a tremendous impact on electrode-coating uniformity, especially considering how the composition of slurry continues to evolve, and different materials are integrated into the mix. Shear is the grinding or sliding of the fluid upon itself. Because all battery slurries are not true ionic solutions, but a mixture of carbon and graphite, they will have tiny, jagged materials. The abrasiveness of the slurry will slowly wear out the mechanical metering surfaces of the coating device. With the slot-die method, the slurry is dispensed directly through the slot-die head onto the substrate, and you don’t have the mechanical grinding action. The wear issue is decreased significantly.
Quality Goal #3: Defect reduction
Defect management plays a big part in keeping costs down, but it’s always been a challenge due to the coarseness of the coating materials. For example, if a slurry particle gets stuck between a roller, it can leave streaks or lines in the coating.
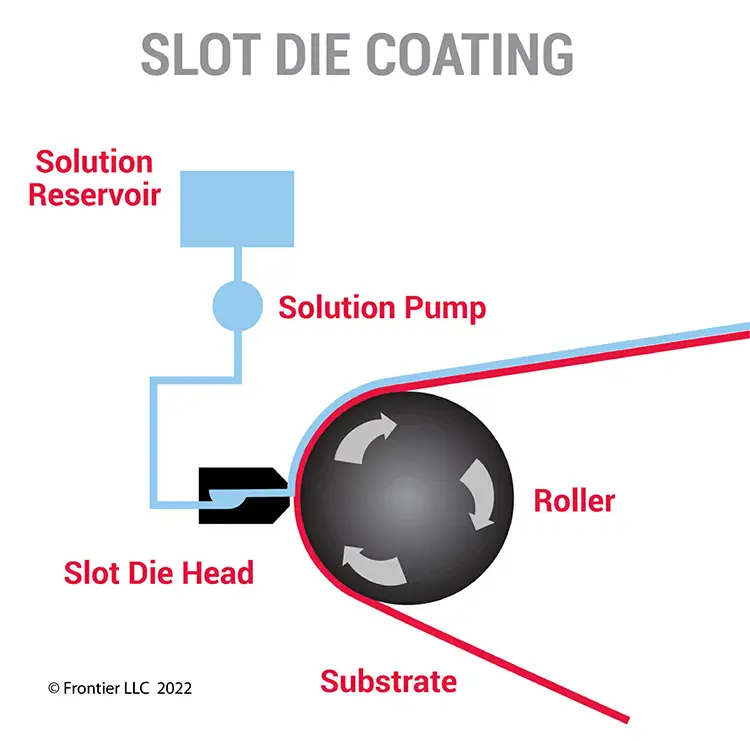
It’s important to note that with slot-die, you also are further away from the roller than the other processes – usually 2X to 5X the wet-coating thickness (see Figure 3). This dramatically reduces the chance of streaks or long-term defects. With a slot-die head, the most you’ll get is a spot defect.
Because materials are stored in a supply vessel with slot-die, there are other benefits (see Figure 4).
- The supply vessel mixer reduces the chance of agglomeration.
- The headspace in the vessel can be inerted by pumping in CO2, Argon or other gasses.
- The material can be vacuum de-gassed to remove air bubbles.
Quality Goal #4: Less waste
An ongoing issue with mechanically metered coating is the waste component. If you have a full material hopper but you’ve produced the quantity required, you can’t stop. You have to coat it out and use the entire supply whether you want to or not.
Slot-die coating offers clear advantages:
- No waste. With slot-die coating, the materials are in a closed system, and you can stop or start whenever you want. There is no cleanup, and you don’t throw any unused materials away.
- No evaporation. Because the materials are in a closed system, evaporation is reduced, and the chance your mixture could mix with other airborne chemicals or particulates is eliminated.
- No need to cut or clean connectors. You don’t need to create a continuously coated film with slot-die. Because the slot-die allows you to stop and start material distribution – both in the machine-direction and cross-web – you can produce strip and patch coating. This can be beneficial if you are producing rectangular films that need to be stacked on top of each other. You avoid the time and expense of removing dried slurry to expose connector tabs.
Quality Goal #5: Safety

While there’s no guarantee what types of materials will be used in the future, presently, operator exposure to hazardous materials is an ongoing concern. Slot-die coating’s closed system can yield significant safety benefits. Operator exposure to hazardous solvents and vapors, such as N-Methyl pyrrolidinone and sulfuric acid, is minimal, as all materials are stored within the slot-die head and slurry supply vessel (see Figure 4).
Future-proof your coating choice
Converters must balance short-term costs with long-term needs. Short-term, with battery manufacturers requiring standards such as only 25 microns for minimum wet thickness, coating methods such as reverse-roll coating still may be applied.
But long-term, the push toward more battery energy output in smaller form factors will be relentless and more aggressive. Future-proofing your converting capabilities requires moving toward equipment best-suited to deliver on more challenging standards for the battery industry.
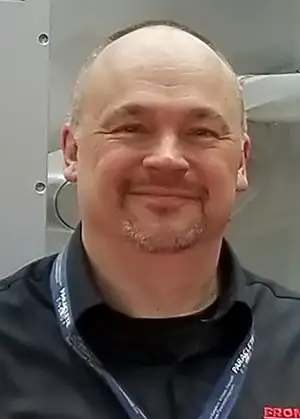
Scott Zwierlein, coating process engineer, FRONTIER, a Delta Modtech Co. (Towanda, PA), works directly with customers to develop solution-based coating and drying equipment. Solutions span a variety of industries, including batteries and capacitors, fuel cells and medical parts. Scott has extensive problem-solving experience in the coating industry. He has been with Frontier for the past 20 years. His background includes both engineering and R&D. Scott attended the University of Pittsburgh. He can be reached at 844-432-9254, email: szwierlein@frontiercoating.com, https://frontiercoating.com, www.deltamodtech.com.