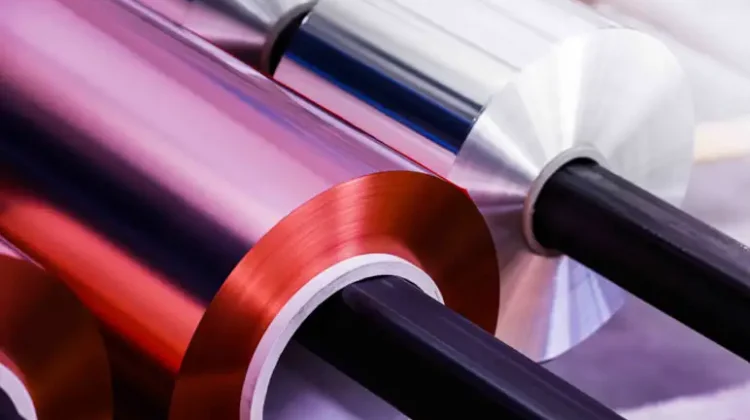
By Andree Nöh, sales mgr., Kampf Schneid- und Wickeltechnik GmbH & Co. KG
The world is facing a major transformation in the energy and mobility sector, and batteries play a central role. The increasing demand for high-performance, long-life batteries for electric vehicles (EVs) and sustainable energy storage will further challenge battery-materials production. Manufacturers need to meet increasing customer demand, expand their throughput capacities and implement efficient, automated-production processes for the flexible components of batteries.
Introduction
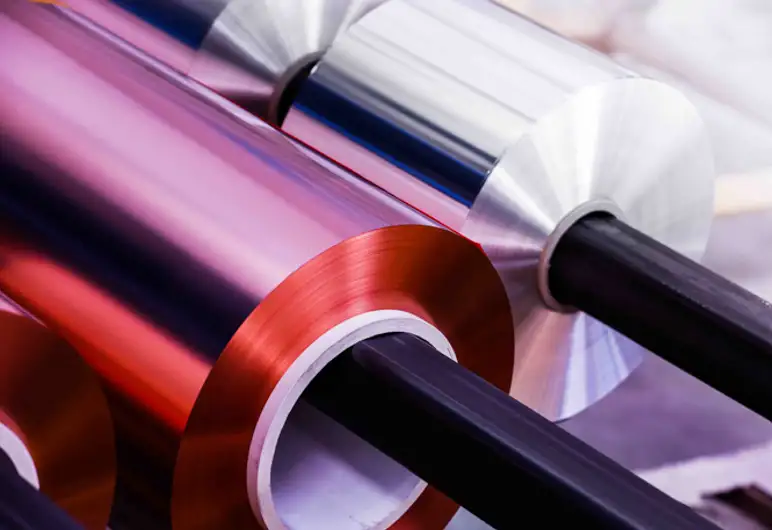
A key factor that will drive the development of new roll-to-roll (R2R) battery production is the continuous improvement of the battery technology itself. Specialists are working on the development of new flexible materials and processes to increase energy density, shorten charging times and increase battery life.
Especially when processing anode and cathode materials, cleanliness, precise cutting edges and the avoidance of particles play an important role. The cutting edges must be smooth, clean and completely free of damage to ensure optimum performance and reliable connections between the flexible materials and electrical conductors. It also must be ensured that the anode-cathode material is wound stiffly and uniformly to guarantee a stable structure of the battery cell later on. Losses of material due to damage is a cost factor in the production step that should not be underestimated.
Quality, quantity and safety are key
Here, particularly reliable slitting and winding machines must be used in the R2R-processing procedure, whose slitting technology, in conjunction with the right drive concepts, realizes this high level of quality, quantity and safety.
Copper and aluminum flexible foils are used as cathode and anode materials, and their processing is equally demanding (see Figure 1). Both materials are used in battery technology because of their specific properties. However, both materials already have undergone a long refinement process and are, therefore, cost-intensive components of a battery, which must be treated with the appropriate care.
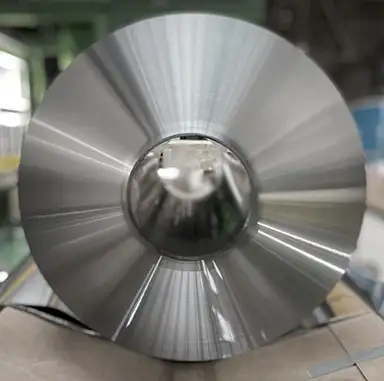
Slitting-method pros and cons
The slitting machines that are used in the converting process of these demanding and high-value materials must incorporate sophisticated and experienced slitting technology (see Figure 2). Let’s compare shear-slitting (scissors-cut) and driven burst-cut methods (see Figure 3).
Shear-cut: The conventional method for slitting foils in the common thickness range for cathode and anode is the shear-cut. Here, as with household scissors, two cutting edges directed against each other separate the material. If the cutting edges are positioned unfavorably to each other or are blunt, a burr forms on the edge. This quickly can build up unnoticed during cutting, and the edge geometry can become undefined to the technical disadvantage, which can lead to faults in the battery itself. Or the burr breaks off or is torn off and settles as a micrometer-sized particle of material in another place, which also can lead to defects in the battery.
Burst-cut is a popular process in the plastic film industry for slitting thicker plastic films. This system has been adapted and integrated into the flexible battery-material world. It is based on the fact that, unlike the scissors-cut described above, the cutting tool is free in a groove and thus has contact only with the material to be slit. During the slitting process, the material flows past the cutting edge, and no burr can form. The edge of the material remains defined, and there is virtually no particle formation due to the slitting process. As a result, possible defect-influencing variables in battery production can be greatly reduced, and the risk of defects in the downstream battery production is significantly lowered.
To further minimize the residual risk of unwanted particles on the finished battery foil after slitting, a slitting-dust suction system can be implemented in the process.
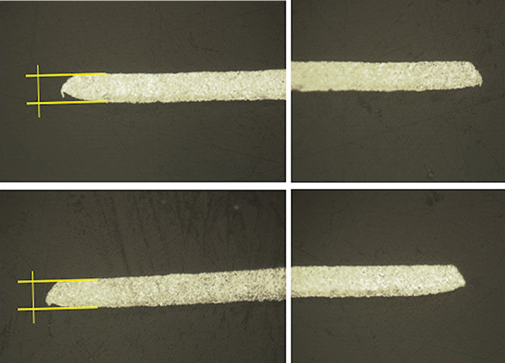
Scissor-Cut (left images): Trials were done with perfectly ground and aligned knife blades; small burrs, which are not possible to feel as they are not higher than the material thickness (see yellow lines).
Driven Burst-Cut (right images): Trials were done with standard knife blades; no burrs; a V-shaped slit is seen as of the geometry of the rotary knife.
Conclusion
Slitting is a vital process in the production of flexible battery-component materials. It adds further converted value to foils that already have undergone long refinement processes and that also are cost-intensive themselves.
The most appropriate slitting method to use may primarily depend on foil parameters – whether for conventional anodes and cathodes or new high-tech thin-gauge materials.
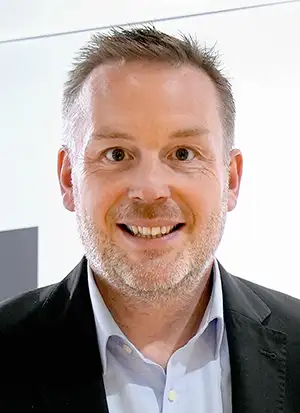
Andree Nöh, sales mgr. for Kampf Schneid- und Wickeltechnik, Jagenberg Converting Group (Wiehl, Germany), studied to become a certifed engineer. He has more than 10 years of experience as a project manager and sales engineer in the plastics industry and more than eight years in the aluminum, copper and steel industries. For the past five years, Andree has been applying his experience to the slitting and winding technologies of battery films/foils and other technical materials. He can be reached at Andree.Noh@kampf.de, www.kampf.de.