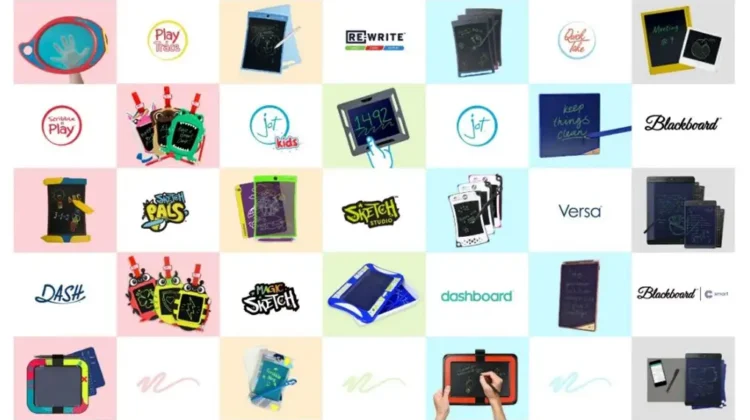
By Donald J. Davis, Global Business Development Director, Kent Displays
Kent Displays, Inc. has been commercializing cholesteric liquid crystal (ChLC) technologies for over three decades, growing from solely a technology company to a consumer-packaged goods company and beyond through a five-phase plan. This growth strategy now is being applied to switchable, liquid-crystal-based light-control films for the advanced mobility market consisting of yachts and recreational vehicles.
Founded 30 years ago to commercialize cholesteric liquid crystal (ChLC) technology, the focus at Kent Displays, Inc. (KDI) was on liquid crystal devices requiring simple electrode patterns of conducting polymer or metal oxides. This led to plastic substrates, which in turn led to early interest in roll-to-roll processing. KDI applied roll-to-roll manufacturing techniques [1,2,3] to the production of consumer electronics, which reduced manufacturing costs and enabled new products, such as reusable writing surfaces. KDI further has advanced the state of the art by introducing a roll-to-part process where a near-finished consumer device is made by a roll-to-roll converting line. The following describes the story of applying KDI’s growth strategy to a new product family, namely a liquid-crystal-based switchable light-control film.
Growth strategy

The company’s five-phase plan has followed these key stages: 1) advance a base technology, 2) introduce a minimal viable product (MVP), 3) expand a product portfolio to fill gaps in the marketplace, 4) introduce a second-generation product, and 5) offer a service-based model where product expertise and technology are scaled to new industries and use cases [4]. This framework has been applied to a new product offering called SwitchVue™ light-control films (featuring a liquid crystal-based functionality). Figure 1 compares the development status of the writing tablet to the light-control film.
Basic tech of light-control films
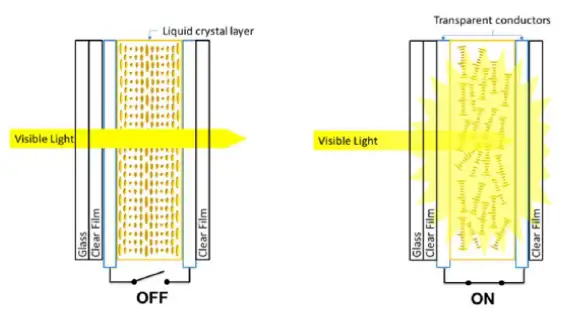
A light-control film provides privacy on demand using a liquid crystal layer that switches between a clear state and a scattering state; the latter appears translucent when a voltage is applied (as shown in Figure 2). In the OFF or clear state, light passes through the layers without scattering. When a voltage is applied in the ON state, the liquid crystals respond to the voltage and scatter the incoming light, making the film appear translucent. The switching speed between the clear and translucent states is less than one second. The optical transmission through the clear state is greater than 99% over all viewing angles. The power consumption is about 10 W to maintain the scattering state for an 18 in. x 24 in. film.
Minimal viable product
Minimal viable product (MVP) samples of light-control films were produced to show at tradeshows and customer visits to collect feedback and gauge interest. Light-control films are made in a similar fashion as writing tablets, using both narrow and wide roll-to-part manufacturing lines – covering economies of scale and, ultimately, large-format films. Light-control films have various application spaces, including architecture, automotive and aerospace. The author’s company is exploring the advanced mobility markets, consisting of windows for yachts and luxury recreational vehicles (RV), due to low volume and high product value. Figure 3 shows an early MVP light-control film in the clear and scattering states.
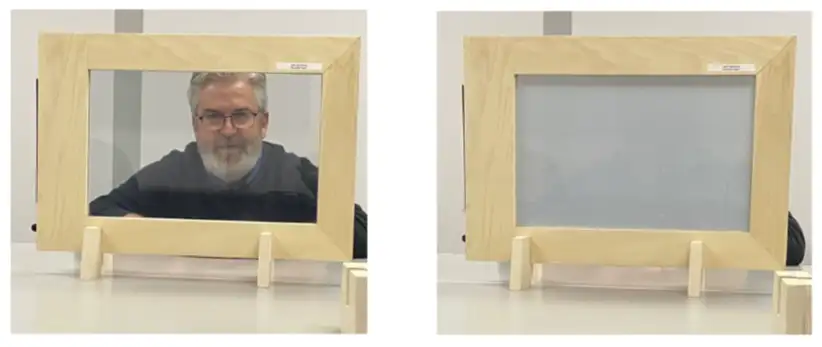
Listening to market feedback
Boogie Board® launched the world’s first reusable writing tablet (using patented cholesteric LCD tech) in 2009 and since has evolved the brand into a portfolio offering of reusable writing products for home, work and play (see Figure 4). A similar trajectory is anticipated for SwitchVue light-control films, with the intention to adapt the offering for various functionalities and specific applications.
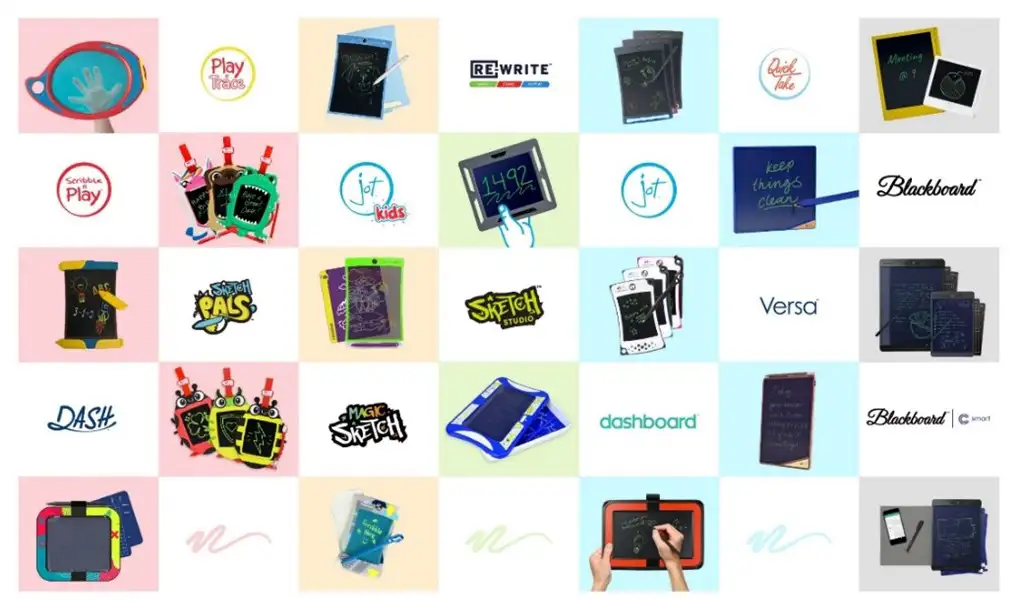
Early market research has indicated three desired use cases and applications for light-control films in advanced mobility – privacy, sustainability and switchable spaces (flipping from private to public). Privacy is the key issue for yacht users due to modesty concerns, but also for protection against obtrusive drones which unexpectedly can invade privacy.
Sustainability is another key concern. A light-control film that blocks UV light and reflects infrared (IR) light offers the potential to reduce energy consumption of HVAC units by lowering heat loads on cabins and cockpits, which especially is important for hybrid and all electric vehicles. This will be achieved using UV blocking coatings, metal oxide coatings – which are good reflectors in the IR – and specialized base plastic films.
Finally, excitement has been seen in the architecture and interior design communities for on-demand switchable spaces that instantly can toggle between private and public. Large windows and partitions can be “frosted over” for use as entertainment screens – enhancing interior design – before being switched to a clear state to be enjoyed as windows and partitions on demand.
Summary
The author’s company is applying its five-phase growth strategy to a new product offering of light-control films for advanced mobility applications. Work continues in providing a customized user experience in privacy, sustainability, projection screens and other areas using films produced on advanced roll-to-part manufacturing lines.
References
- D. Davis, “Roll-to-Roll Manufacturing of Boogie Board Writing Tablets,” Converting Quarterly, 2022, Q1.
- E. Montbach and D. Davis, “Roll-to-Roll Manufacturing of Flexible Displays,” in Jehuda Greener, Glen Pearson, and Miko Cakmak (Ed.), Roll-to-Roll Manufacturing: Process Elements and Recent Advances, (pgs. 285-324), New York: John Wiley & Sons, (2018).
- Green, E. Montbach, N. Miller, D. Davis, A. Khan, T. Schneider, J. W. Doane, “Energy Efficient Flexible Reflex™ Displays,” Proc. Intl. Disp. Research Conf., 28, 55 (2008).
- D. Davis, “Lessons Learned in Advanced Roll-to-Part Manufacturing of Consumer Electronics,” Converting Quarterly, 2023, Q4.
Don Davis has 35 years’ experience in advanced manufacturing, including liquid crystal displays, military laser systems, MEMS and nano-embossed plastic films. He is the business unit leader of KDI Technical Services, a division within Kent Displays, Inc., which focuses on clean room-based contract manufacturing. Under Don’s leadership over the past 17 years, KDI has implemented three roll-to-roll manufacturing lines for flexible liquid crystal displays for the manufacture of the Boogie Board® electronic writing tablet and other devices. Prior to joining KDI, Don held technical positions at Avery Dennison and Hana Technologies. He is the 2015 recipient of the Visionary Manufacturing Leadership Award and has spoken at conferences such as FLEX, Association for Roll-to-Roll Converters Business Summit, ESTECH, LOPEC and Prinse’22. Don can be reached at 814-573-8896, email: ddavis@kentdisplays.com or www.kentdisplays.com.