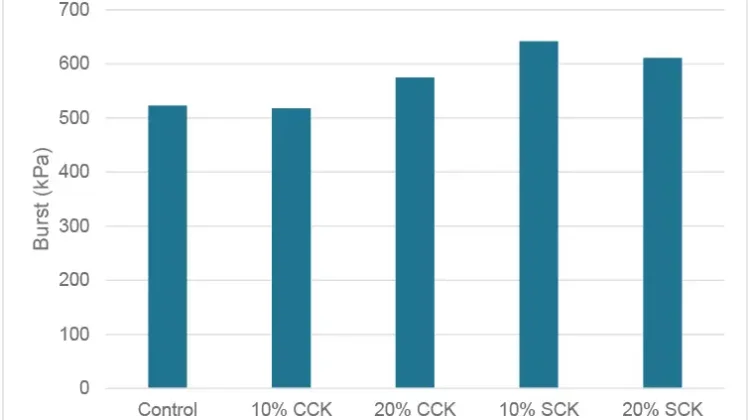
By Tim Rummel, technical mgr., Wacker Chemical Corp.
Siliconized release liner generally is perceived as unrecyclable due to the thin layer of silicone on the paper. As interest in recycling more grades of paper grows, niche grades such as liner now are of interest. This study looks at taking two common types of liner and recycling them with old corrugated containers (OCC) to make recycled-containerboard face stock. The mixture of OCC and premium fiber from the silicone-coated release liner produced an equal or better sheet than OCC alone, despite the presumed reduction in strength loss due to the presence of residual silicone.
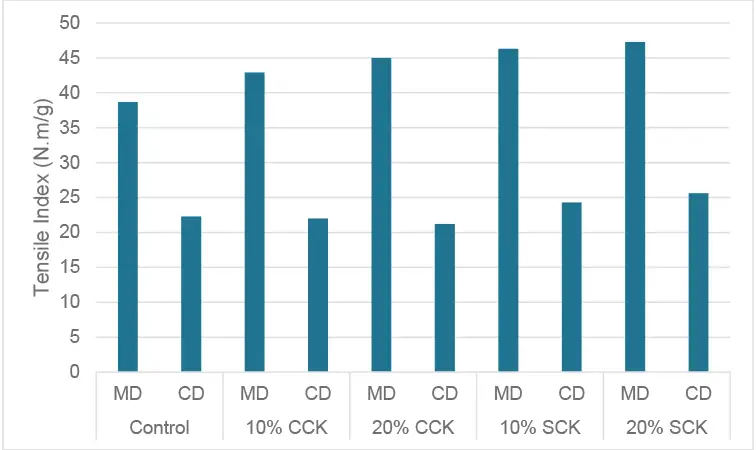
Introduction
As the world increasingly recognizes the benefits of renewable raw-material streams, interest has grown in industries such as the paper industry. Being that the forest-products industry is the largest in the world whose stock in trade is perennial plants, it is without equal in terms of sequestered carbon. Even in the case of landfilled paper and wood products, the associated carbon is out of the atmosphere for half a century or more. No other industry comes close to this. Add on the fact that the North American forest-products industry has planted far more trees than it has harvested for several decades, and the benefits become even more compelling. In fact, in the past two decades, US landowners have increased the area of forest land by almost a million acres per year, which is about 1,200 NFL football fields per day. [1]
The circularity of paper fiber also is exemplary. Recycled in large quantities for over a century [2], paper fiber is well known as a lucrative, easily recycled commodity. With the growing desire on the part of industries to be more sustainable, we find attention being given to smaller niche grades that have long been ignored. The label industry has formalized this with the establishment of CELAB (Circular Economy for LABels), an industry coalition dedicated to recycling waste products of the label industry. Having been initially formed in 2020, CELAB is a global organization of over 60 member companies whose primary objective is to promote release liner and matrix recycling. This study was conducted by Wacker Silicones in collaboration with CELAB.
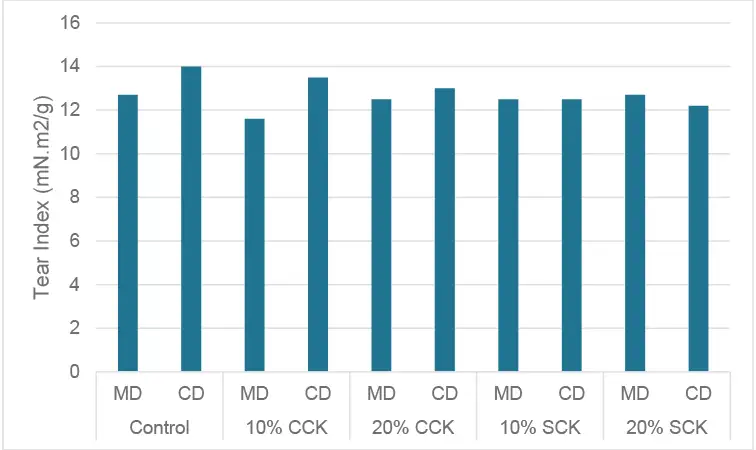
Silicone-coated release liner historically has been prohibited in recycled-paper mills due to fear of silicone contamination. While silicone granules in paper aren’t ideal, they also are not the problem they’ve long been thought to be. For example, a previous study by Venditti, et al. demonstrated that printing clarity drops due to silicone granules being present in a recycled, uncoated sheet with 25% liner and label and 75% pre-consumer copy paper [3]. This study showed a loss in strength, but label stock (which is adhesive-coated) was used, so the fiber content was quite a bit lower than what would be typical of liner waste. Additional investigation may be warranted to determine the separate impacts of silicone interaction vs. adhesive interactions. Indeed, a different study by Körkkö, et al. showed a large increase in strength when liner was added to an ONP/OMG furnish [4].
The approach of this study, as well as potential future liner-waste recycling studies, is to target more likely real-world recycling scenarios. Corrugated paperboard, which is by far the largest recycled-paper fiber stream, was chosen for this purpose. No special screening or extended processing times were to be used, and deinking (which can remove silicone granules) was not used. Siliconized C1S SCK (supercalendered kraft) and CCK (clay-coated kraft) were recycled at 10% and 20% with standard OCC (old corrugated container) cuttings.
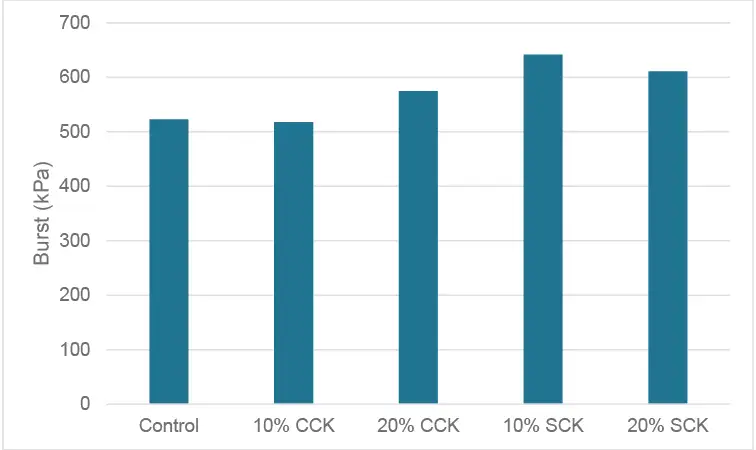
So, what IS liner waste?
Before we get further into the study, let’s look at what liner waste is and isn’t. Typical liner grades range from 60 to 120 gsm, with 1.0 to 1.50 gsm of silicone on them. By comparison, flexographic ink usually is applied at 5 to 10 gsm. Silicone-release coating is applied in a liquid form onto the liner paper, but it undergoes a chemical reaction that converts it into a solid layer on the paper. The silicone is very stable, chemically, and any solvents, acids or caustic solutions used in the paper mill will not cause it to revert into its liquid state. It is unreactive for the purpose of paper recycling, and it is never anything but a solid in the recycler’s paper mill.
That means that silicone is not a chemical contaminant, but rather a physical one. It also isn’t a strong one, so any re-pulping operation will tear the ultra-thin silicone film into countless pieces. Larger pieces will be flake-shaped and generally are removed by the screen. The smaller ones will become part of the finished paper. If we assume that the stock is 10% liner that was 2% silicone, we’re down to 0.20% of total mass. Assume that the screen and cleaners take out 90% of that [3], and the resulting amount is 0.020%. But, in a square meter of paper, that still might be 5,000 granules or more (roughly 500 granules per ft2) [5]. So, we should not ignore it, despite the low volume.
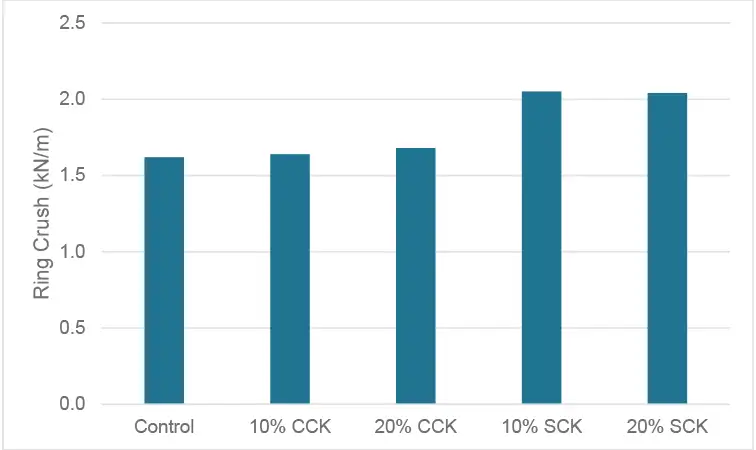
Enough about silicone for now. Liner paper has a few common classes. In general, they feature nearly equal amounts of premium bleached softwood and hardwood kraft fiber. What is unique is the high level of refining energy put into these fibers. Liner fiber generally receives substantially more refining energy than any common grades, typically using high consistency refining to minimize fiber cutting. So, liner uses strong, more expensive fiber. It is almost entirely virgin fiber as well. SCK is always, of course, supercalendered, but CCK also is either supercalendered or heavily calendered. In addition, CCK uses a coating of ultrafine clay and enough binder to have excellent pick resistance. Filler levels range from about 3% to 10%. Glassine, another grade that is common globally, has similar characteristics; however, it may be unbleached. Glassine is not common in North America, so it wasn’t included in this study.
Basic study parameters and results
In this study, 10% and 20% SCK and CCK were incorporated into a 250-gsm-sized and starch-coated corrugating face stock, 0.43 to 0.45 mm caliper. Repulping and papermaking took place on Western Michigan University’s (WMU) pilot coater. Repulping was done in a hydrapulper for 40 min at 55° C /130° F and 6% consistency. The required testing to pass WMU’s OCC-E Recyclability Protocol was completed, and all blends passed. The primary interest in paperboard is strength, so many strength properties were evaluated. We will look at four strength properties here, plus slide angle and porosity.
Tensile Index: The most basic strength property – tensile index – shows a trend that will be apparent in the rest of the strength studies (see Figure 1). Overall, CCK shows a slight increase, with cross-direction (CD) down vs. machine-direction (MD) going up. SCK is stronger on both fronts. This particular CCK grade, which is an older design no longer on the market, had an especially heavy coating, with an ash content of about 16%. Even with a non-fiber content that probably was near 20%, the strength still increased. Strength benefits of liner fiber were more apparent with SCK, as strength increased 15% to 20%. This is exemplary, considering that corrugated-fiber streams are engineered for strength above all else. They typically are strong softwood fiber, with only enough hardwood for good formation and smoothness. Despite that, liner fiber easily outperforms this blend.
Tear Index: Where tensile strength prevails, any papermaker can tell you that tear strength should suffer. It does here, but not as much as one might expect (see Figure 2). The massive increase in refining overpowers the typical refining-based effects of fiber shortening because of the incoming fiber’s high quality. Despite the massive tensile increases, tear showed only 5% to 7% declines (combining MD and CD).
Burst Resistance: Often the partner of tensile, burst provides an excellent non-directional read on strength performance of a sheet. That is true here, with bursting strength gains evident (see Figure 3). CCK is deficient compared to SCK, but reading the trend from the 20% CCK sheet, we see that it still shows a gain on strength despite the ~20% in non-fiber and residual silicone content.
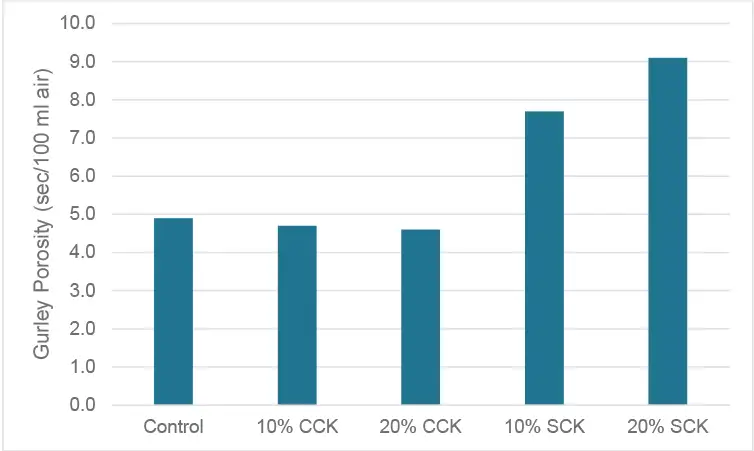
Ring Crush: Now we see the last of the strength properties. Ring crush isn’t in the same class of universal strength tests that the first three are. However, it generally is a test unique to packaging, and therefore a “must-have” of corrugated-container producers. In this instance, we see more differentiation between SCK and CCK results (see Figure 4). CCK still is holding its own, and certainly no loss in strength is seen. However, a significant increase cannot be claimed. SCK, on the other hand, repeats its performance from before, marking a 15% to 20% improvement. The strength benefit of liner fiber still is clearly evident in this test.
Liner fiber has a more profound, though not necessarily problematic, effect on non-strength tests. Certainly, the smoothness and strength targeted by liner design does not match with corrugating materials. At a minimum, liner fiber generally is considered an outthrow from OCC because it is most often bleached, but it still matches up well because of its high quality. Indeed, one might predict a substantial loss in caliper because of the very high refining level of liner fiber. That wasn’t seen, with only a 2% drop seen on CCK grades and none on SCK.
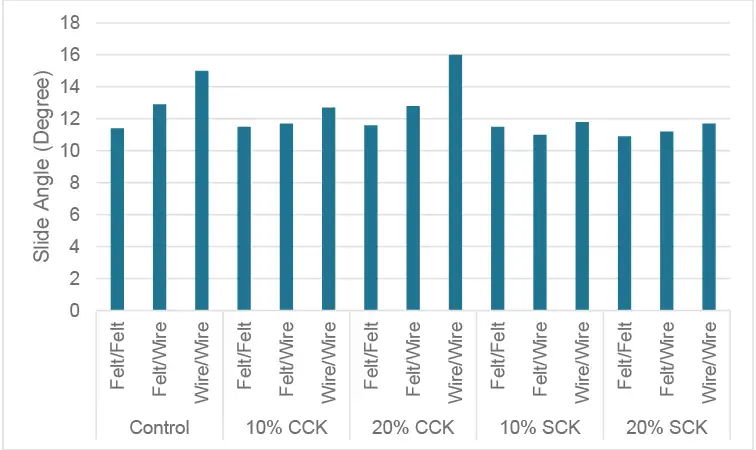
Porosity and slide angle: In any case, we now will examine porosity and slide angle. Porosity is up first (see Figure 5). One would expect the introduction of highly refined fiber to close the sheet up a bit. We see that here with the SCK, as 10% closes the sheet up by about 50%. Broken-coating granules of the CCK sheet, which inhibited strength development earlier, may now be helping to keep the sheet open. Even still, the reduction in SCK porosity isn’t massive, but notable, nonetheless.
The final test presented here is slide angle (see Figure 6). Smoothness and low coefficient of friction (CoF) of materials should be expected to make a difference in this test. Automated carton dispensers can be quite sensitive to changes in CoF. More often than not, the rougher wire side is the side being glued to the corrugating medium, and the smoother felt side is the one printed and presented to the consumer. Therefore, felt/felt is the most important test here. CCK is invisible here. Highly refined SCK fiber, with no coating granules to offset it, does drop CoF (via slide angle) by 5% to 10%. While likely not a major problem, such a decrease could require adjustment of automatic box-dispensing equipment. However, such a minor decrease likely is within the tolerance of most product-packaging operations.
Conclusions
While there is yet work to be done, liner fiber clearly is an overlooked, high-value source of recycled fiber. Harnessing the value of what currently is trash has a tremendous upside for label applicators in every corner of our industry, as well as the paper industry overall. Projects targeting SOP (sorted office paper) and other select grades already are in the planning phases. It is time to stop throwing this great fiber source into the trash.
References
- https://twosidesna.org/US/are-north-american-forests-really-shrinking-what-the-data-tell-us/
- https://www.bbvaopenmind.com/en/science/environment/history-of-recycling-from-living-scarcity-to-coping-excess/
- Venditti, R., Gilbert, R., Zhang, A., Abubakr, S., “The Effect of Release Liner Materials on Adhesive Contaminants, Paper Recycling, and Recycled Paper Properties,” Proceedings from the 2000 TAPPI Recycling Symposium, pp. 579-591, Washington, DC.
- Körkkö, M., Laitinen, O., Saari, J., Ämmälä, A., and Niinimäki, J., 2008, “Recyclability of Release Liner,” International Paperworld IPW, (9), pp. 54-58
- Rummel, T., “What Recyclers Think of Silicone Coated Paper,” Proceedings from the 2019 AWA Global Release Liner Industry Conference and Exhibition, Charlotte, NC.
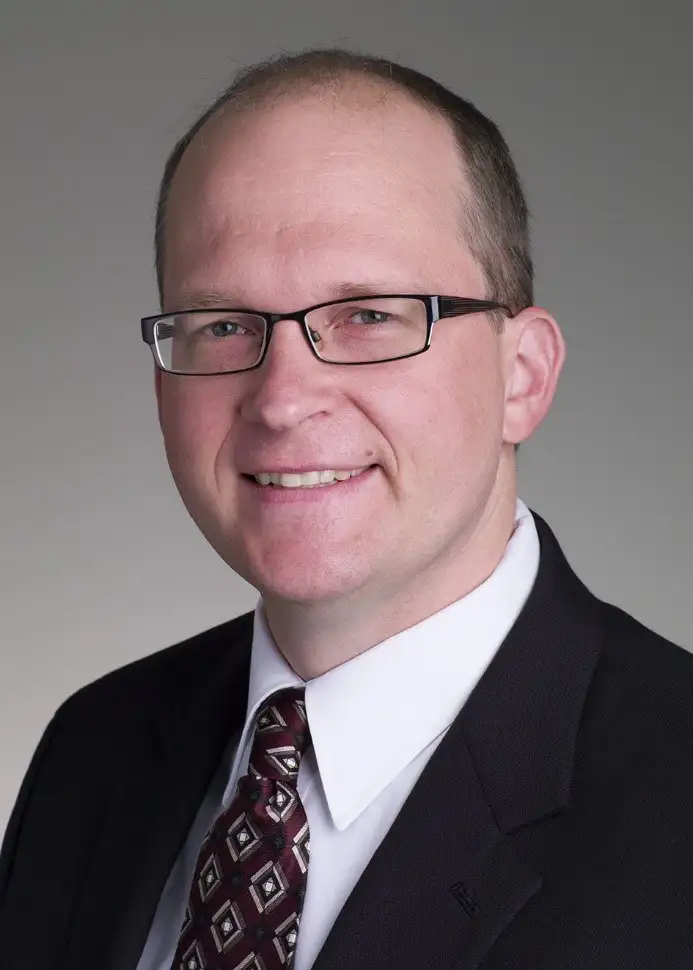
Tim Rummel, technical mgr. for Wacker Chemical Corp., holds Bachelor of Science degrees in Paper Science and in Chemistry from Western Michigan University, as well as an MBA from Wayne State University. He joined Wacker Chemical in 2012 and serves the North and Central American region for the release-coatings business. His experience includes two decades of formulating release coatings for the pressure-sensitive tape and label industries, including a great deal of process development and optimization. Tim can be reached at 734-489-8360, timothy.rummel@wacker.com, www.wacker.com.