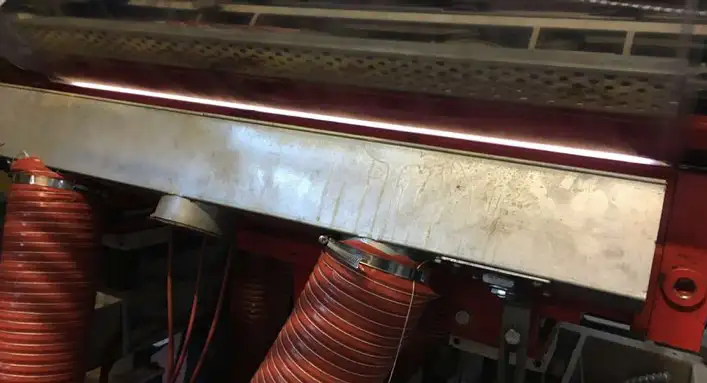
By Stefano Mancinelli, sales & process mgr. EsseCI s.r.l.
Some substrates, such as plastics, have inert and non-porous chemical surfaces that make them non-receptive to the affixing of various materials, such as printing inks, adhesives and coatings. Surface treatment increases the surface tension (wettability) of the material to prepare it for subsequent applications, like printing, painting, dyeing, gluing, coating, lacquering, adhesive tapes, vacuum-metallization, lamination, etc. The flame-treatment process mainly consists in passing flame over the surface of the material to be treated. Flame treatment can be used to improve adhesion capacity of all plastics, as well as some non-plastic materials, including aluminum, paper or metallized products. Nitro-Hydro-Flame Treatment (NH-FT) technology focuses on an upgraded, surface flame-treatment process on polyolefin (PP, PE) and PET substrates, among others.
Flame treatment can be used to improve the adhesion capacity of plastic material, preparing the surface for the application of inks, adhesives and coatings. Generally, the flame-treatment process consists of passing a flame over the surface of the material to be treated. The Nitro-Hydro-Flame Treatment (NH-FT) process from the author’s company is an upgraded process in the field of polymer surface treatment, resulting in improved surface energy on treated webs said to be previously unknown to standard surface-treatment methods, such as corona, plasma and standard flame. Let’s begin by considering the most common treatment methods to better understand the benefits introduced by NH-FT.
Comparison of surface-treatment types
According to literature and applications, Standard Flame (Std-FT) allows for a higher surface energy when compared to corona and corona-derived (plasma) treatment methods. Std-FT flame from this firm is, in appearance, very similar to a corona discharge, except for the color, which is a light blue in flame treatment and violet with corona treatment (see Figure 1).
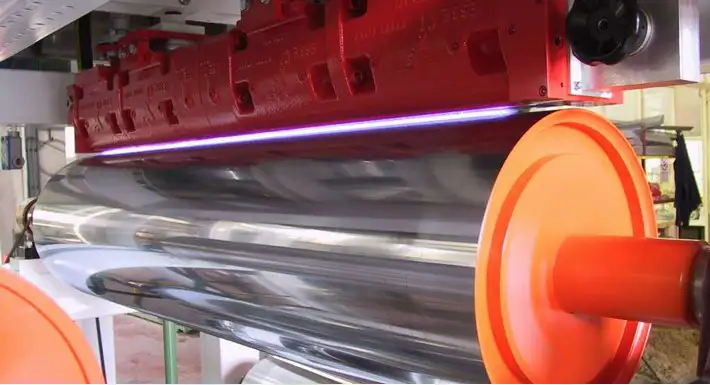
The difference between Corona and Std-FT is not just a question of color. While they are both oxidizing processes, adding oxygen and oxygen groups to the surfaces they treat, there are two main features differentiating these surface-treatment methods.
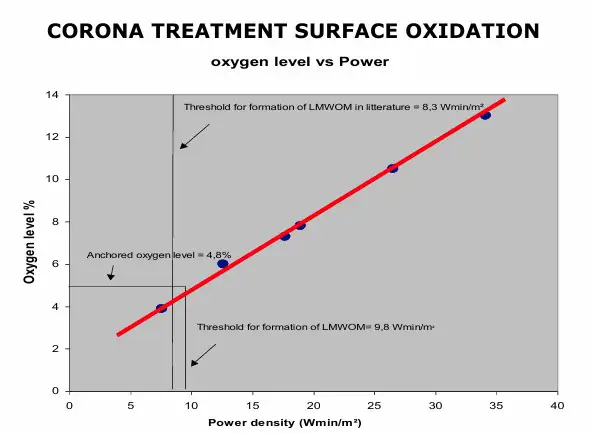
Depth of oxygen incorporation: In treated film (as with PP), Std-FT achieves a depth of oxygen incorporation between 5 and 10 nanometers vs. a depth of about 50 nanometers in the case of corona treatment. As a result, flame treatment achieves a more extensive oxidation, concentrated in a shallower surface region, which results in higher wettability and surface energy.
Quality of incorporated oxygen: Corona-treated PP (and, in general, with polymers such as PET, PE and others) is characterized by the presence, on its surface, of Low Molecular-Weight Oxidized Materials (LMWOM). This presence is much higher when increasing corona watt density is applied to the material, referred to as overtreatment (see Figure 2).
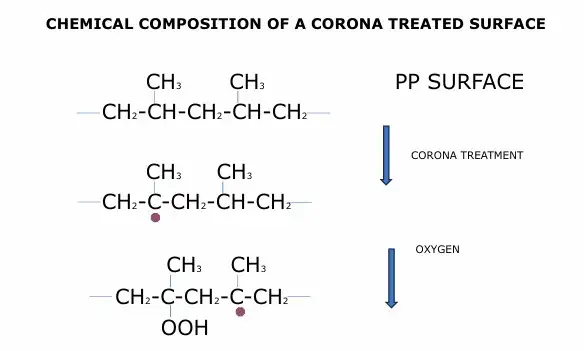
Both corona and Std-FT, when treating a polyolefin surface, begin with radicals’ attack on tertiary carbon of polymer macromolecular backbone. The initial step in the oxidation of polymers by a flame is passing through polymer-radical formation by hydrogen abstraction and formation of free sites along the macromolecular chains. In these free sites, oxygen-based groups then are inserted, polarizing the chains (represented by the purple dots in Figure 3).
Corona treatment, despite flame treatment, also breaks C-C links along the macromolecular chain (see Figure 4). This reaction is known in literature as a β-scission reaction and produces, as a consequence, weight lowering of these oxidized chains, so named LMWOM or Low Molecular Weight Fragments (LMWF). LMWOM are water-soluble or other solvent (such as acetone or methanol) -soluble and generally are more weakly anchored to the PP surface. Atomic oxygen radical is the precursor of LMWOM formation, passing through the alcoxy radicals (RO) formation. Literature states that when a hot flame impinges on the cold (at about 400° K) PP surface, many radicals present in the flame (produced by a radical reaction) are destroyed. This destruction doesn’t affect OH radical concentration – because they are by far the more present radicals in the flame – but there is a big impact on atomic oxygen radicals, strongly diminishing their concentration.
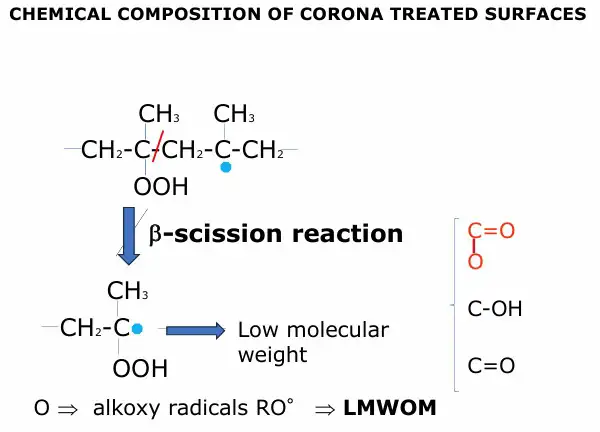
The following formation of alcoxy radicals – from which LMWOM develop – is negligible in the case of flame treatment. With flame, LMWOM eventually could form (as an alternative way in respect to the one represented by RO radicals) starting from carboxilate/peroxy groups (COO), but these groups scission to form alkoxy groups too slowly to account for a significant formation amount of LMWOM. Moreover, formation of COO groups can be kept under control with flame, working with an air/gas ratio not too gas-lean (so, not too oxygen-rich). The same phenomenon doesn’t occur with corona treatment, where alcoxy radicals, which are present in a large extent, are involved up to 50% in the β-scission reaction types, so forming LMWOM.
When treating a polymer surface, there are two main processes competing with this surface oxidation (see Figure 5), in the sense that both of them tend to reduce the amount of oxygen induced by treatment as time passes:
- LMWOM Formation: Due to their low molecular weight, these oxidized chains tend to be removed from the surface, especially if, between film rolls, humidity also is rewound. This phenomenon is typical of corona treatment.
- Hydrophobic Recovery: Due to chains remixing over time, oxidized chains tend to move from the surface to the film core, thereby again reducing the surface oxygen level. This phenomenon is typical of both corona and Std-Flame methods. NH-FT allows the inhibition of any hydrophobic recovery.
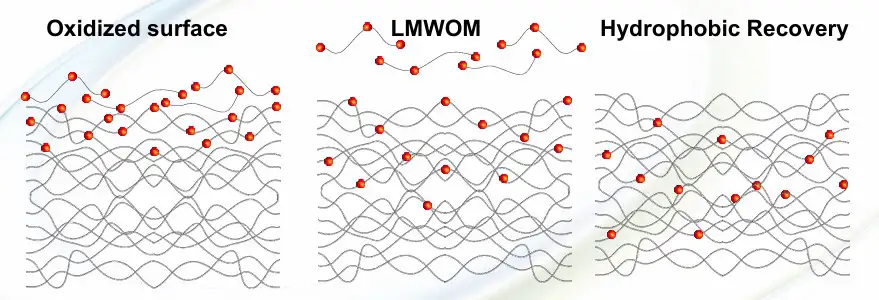
“Nitrous-Hydro Flame” treatment process
One differentiator with NH-FT is its flame appearance; its color turns to white, rather than the classic light blue of Std-FT (see Figure 6). This change is due to a higher flame temperature, 120° C to 150° C higher on the burner head. Higher temperature is the first distinctive NH-FT feature.
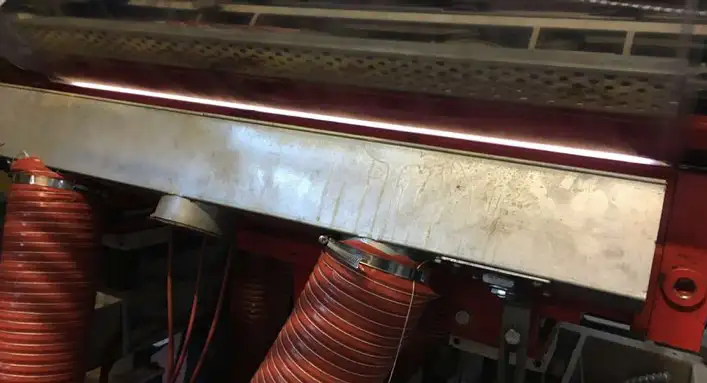
Starting from Std-FT, NH-FT is obtained by the addition of two main gases (or, better said, one gas and one mixture) to a standard combustion system (the one formed by combustion air and a hydrocarbon gas, such as natural gas, methane, propane or LPG):
Nitrous Oxide (CAS no. 10024-97-2): Nitrous Oxide (N2O) is an oxidizer substitute in the combustion system, generally used nowadays in several applications, including as an anesthetic in hospitals or dentist offices, in the food industry for whipped cream cans or for improving engine performance. When added to a combustion system, N2O undergoes a scission reaction at temperatures higher than 565° C, forming nitrogen and oxygen and producing heat. It is this heat that increases the combustion system – and so, the NH-FT – flame temperature. This increase in flame temperature makes NH-FT more efficient in breaking C-H links along polymers’ macromolecular chains, so producing a higher (vs. Std-FT) number of free sites and higher amounts of functionalities linked, after treatment, to polymer chains themselves.
A second effect of the addition of N2O to a combustion system is the formation, along with oxygen-based groups, of nitrogen-based ones, both oxidized (as organic nitrates and or nitrites) and reduced (amine, imine, amide, nitrile). These nitrogen-based groups, in effect, form a tridimensional net between different functionalities on the polymer surface, stabilizing them and inhibiting any hydrophobic recovery process.
Methane Hydrogen Mixtures: Methane Hydrogen Mixtures (MHM), formed by natural gas and hydrogen in content up to 30% in volume, are a combustible substitute in combustion systems where they are added. Nowadays, it is possible to find MHM used in public transportation to increase engine performance and reduce the engine’s carbon footprint. The effect of adding MHM in a combustion system is to increase its temperature thanks to a higher release of heat coming from hydrogen with respect to other hydrocarbons, so using MHM also increases flame temperature.
In summary, NH-FT, with respect to Std-FT, produces a higher amount and a wider range of functionalities on polymer-treated surfaces. Let’s see what this means in terms of applications.
NH-FT applications
NH-FT has been used by the author’s company in a variety of applications, starting from a lab pilot line up to industrial-scale (coaters and laminators), on the following types of substrates:
- Biaxially oriented polypropylene (BOPP), both homopolymer and coextruded skins;
- Polypropylene white opaque, solid and cavitated;
- Cast polypropylene (CPP);
- Oriented polyethylene (MOPE);
- Biaxially oritented polyester (BOPET); and
- Bio-based and biodegradable films.
Once these substrates were treated using the new process, the following types of coatings were applied:
- Liquid varnishes and inks
- nitrocellulose/PUR
- pure PUR
- nitroacrylic-based
- in ethyl acetate or ethyl acetate/alcohol, such as the ones via Sun Chemical for lamination and surface printing (gravure and flexo), including SolipropTM, Duratort PM, SolvafilmTM, Duratort PF, Solimax P, Soliprop V. series
- UV inks for labels applications, such as SICURA Nutriflex 10, Zeller + Gmelin UVAFlex® FCM Y81 (LM) and Flint Flexocure Force™
- Acrylic lacquers, such as DSM NeoCryl FL-715, FL-721, BT-36 (water emulsions) and B-871 (in solvent)
- Polyvinylidene chloride (PVDC) lacquers, such as Solvay’s Diofan family (A050, A297, B203)
- PVOH/EVOH lacquers, such as by Kuraray: Exceval™ (AQ4104) and Poval™ (2598-R)
- PET and oxygen-barrier varnishes, such as the SunBar® series by Sun Chemical;
- AlOx and aluminum
Results
After industrial-scale tests, results showed immediate (t = 0) adhesion of lacquers, inks and varnishes on polymer substrates, without the need to use a primer, adhesion promoters or hardener, including the following:
- PUR primer (such as DSM NeoRez R-600 and NeoRez R-610 for acrylic coatings);
- PUR primer (such as DSM NeoRez R-610 or PUR/PET BASF Epotal for PVDC coatings);
- PEI primer (such as BASF Lupasol WF for PVOH/EVOH coatings);
- Ti-chelated adhesion promoter (such as NT 9013000165 Sun Chemical for nitro inks).
In addition, t = 0 adhesion was achieved even in overlay printing and coating (two coatings or topcoat plus ink layer put on nitrous flame-treated surface). There was no need to prime / coat the web surface prior to UV-ink application, and excellent coating adhesion and sealability (acrylic/acrylic, acrylic/nitro and acrylic/PET) were seen, even with BOPP-coated homopolymer, after 18 months. Also noted was high metal adhesion on BOPP-homopolymer metallized substrates, without any need of a primer layer or a tie-layer (EVOH). The metal surface energy had high retention for 18 months after treatment, and nitro inks showed excellent adhesion on aluminum without the use of an adhesion promoter. These results cannot be achieved by std. flame, corona or plasma treatment.
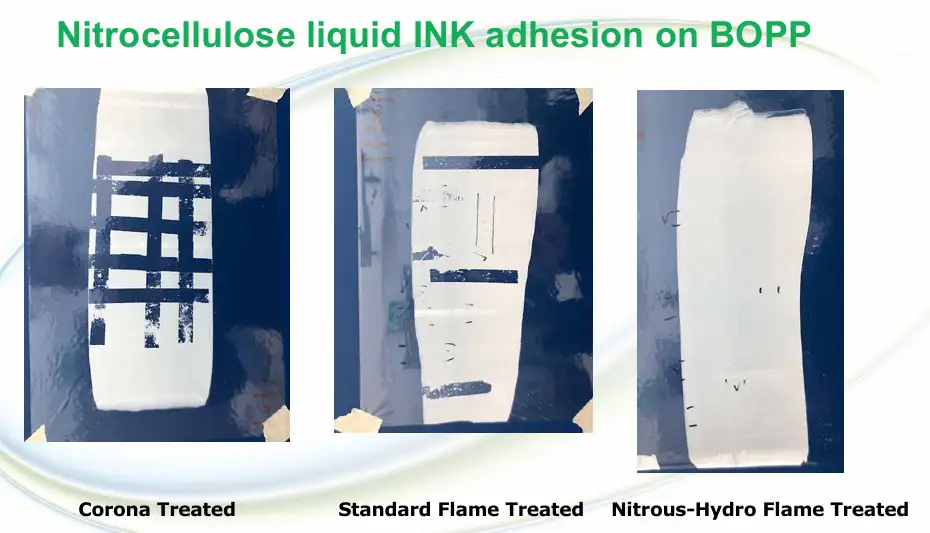
The difference in surface energy between corona, Std.-FT and NH-FT is clear when testing adhesion on a nitrocellulose-based ink, such as Sun Chemical’s SolipropTM, applied on a homopolymer BOPP skin. Figure 7 illustrates BOPP ink adhesion without the use of an adhesion promoter when treated by corona, Std-FT and NH-FT. Test method used is a standard peel test with Tesa Tape 4104.
Conclusions
Some substrates, such as plastics, have inert and non-porous chemical surfaces that make them non-receptive to the affixing of printing inks, adhesives and coatings. Surface treatment increases the surface tension (wettability) of the material so as to prepare it for subsequent applications, like printing, painting, dyeing, gluing, coating, lacquering, adhesive tapes, vacuum-metallization, lamination, etc. This firm’s new Nitro-Hydro-Flame Treatment (NH-FT) technology focuses on an upgraded, flame surface-treatment process on polyolefin (PP, PE) and PET substrates, among others. This has been shown to improve adhesion capacity.
Other benefits include a simplified process and flexibility, such as the following:
- Immediate ink adhesion, with no need to wait up to 24 hrs for cross-linking;
- Extended ink pot-life, because no cross-linker is present; and no waste of material due to ink hardening produced by an adhesion promoter prior to its application; and
- Possibility of using one ink for different substrates (such as PP, PE, PET), with no waste of time (increased press uptimes) and materials for cleaning rollers and pans.
Savings in the order of magnitude of 1M€/year in printing and coating can be realized due to primer/adhesion-promoter elimination, avoiding the need for daily disposal. A reduction of eco-toxicological risk due to adhesion promoters and primers can be found. In addition, there are no issues with adhesion in high-humidity conditions, as happens when using adhesion promoters and primers. Finally, the new treatment method advances recyclability, with no need to use tie layers of different chemistry in mono-material laminations.
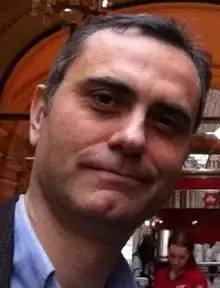
Stefano Mancinelli is sales & process manager for EsseCI s.r.l. (Narni, Italy), a provider of flame-treatment solutions for the converting industry. Stefano earned his M.S. in Material Engineering at the University of Perugia in 1998. In his over 25 years of employment at esseCI srl, he has acquired a deep experience in the field of flame treatment, first as Process Engineer and then as Process Manager, involved in plants commissioning and post-sale customer service all over the world. Since 2011, he has served as Sales Manager, Process Manager and is responsible for the pilot-plant unit. He also has served as a member of the company board of directors since 2007. Stefano can be reached at +39-0744-72641. email: s.mancinelli@essecinet.net, www.flametreaters.com.