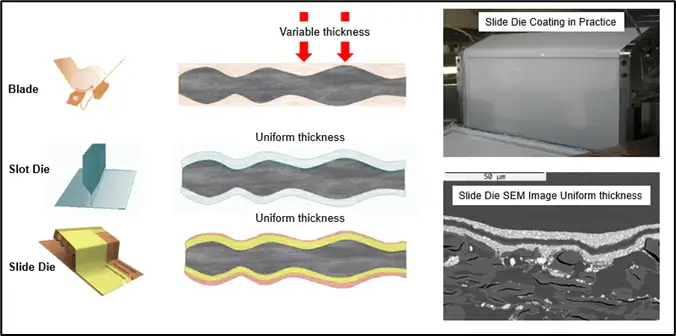
By Donato Ventresca (recently retired TS&D specialist) and Greg Welsch, global innovation and TS&D leader, Trinseo LLC
Functional coatings are applied to paper and paperboard substrates to provide resistance, or a barrier, against media such as oil and grease (OGR), water, water vapor (MVTR) and oxygen, for applications such as food packaging, foodservice and other non-food packaging. Typical functional-barrier coatings can be created by applying a solid coating or extruded film, a solvent-based coating or a water-based coating to the paper substrate using various coating methods. Today, there is increasing interest in developing recyclable and more sustainable approaches to producing these types of packages. This article focuses on water-based barrier coatings (WBBC) for OGR, water, MVTR and oxygen barrier performance, with the emphasis on creating coated systems that can achieve more than one barrier property, using multilayer curtain coating (MLCC), in one application step. Curtain coating has emerged as the premier low-impact, contour-coating application method for coated paper and paperboard. Significant research work to date and production experience on specialty papers and paperboard has focused on conventional coating techniques or single-layer curtain coating. More recent work has shown that multilayer curtain coating has many advantages over these other methods. One advantage of lower material cost is accomplished with the use of functional chemistry in confined layers where performance is optimized within the layered coating structure. This allows applying consecutive layers of different polymer types, in one step, to achieve the appropriate performance.
Editor’s Note: This technical paper is based primarily on the authors’ presentation at the Specialty Papers USA conference, held in Milwaukee (WI) in October 2023. More info: www.specialtypaperconference.com/specialty-papers-us
Introduction
There are different types of barrier coatings that can be applied as either solid coating or as dispersion coatings. This paper focuses on water-based barrier coatings (WBBC) for oil and grease resistance (OGR), water resistance and water-vapor transmission resistance (MVTR). The main goal of this article is to show how you can create coated systems that can achieve more than one barrier property using multilayer curtain coating (MLCC). The strategy is to use one or more layers that are optimized for specific barrier performance and then capped with a non-blocking barrier layer.
Multilayers of different barrier polymers is a strategy that the plastics industry has employed for over 30 years, making the finished article more effective for barrier performance. When the plastic ketchup bottle came out in the early 1980s, it consisted of five to seven layers of different polymers to achieve all the barriers required to protect the contents. This same principle can be applied using stacks of barrier layers. To do this efficiently, multilayer curtain coating has emerged as the premier low-impact application method for coated paper and paperboard, as well as other substrates. MLCC has many advantages over conventional coaters and single-layer curtain coaters [2-4].
Multilayer Curtain Coating (MLCC)
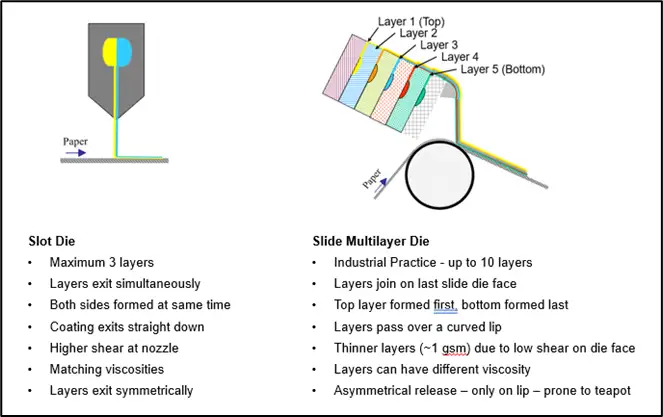
There are two types of curtain applicators (see Figure 1): the slot-die and slide-die configurations. The slot die usually is used for single-layer coating and theoretically is limited to a maximum of three simultaneously applied layers. In practice, the slot die is generally limited to no more than two layers as illustrated. In the slide-die configuration, the coatings are pumped through parallel slots on the angled slide with each layer pushing up the previous layers until the multilayer structure is assembled. The combined fluid passes over a curved die lip before falling as a free-falling curtain. It can be used to apply from one to more than 10 layers simultaneously. For barrier-grade development, it provides more flexibility in designing multilayer and multi-functional, paper-barrier grades. The slide die has an advantage in its ability to apply very thin layers as well as allowing adjacent layers to have different viscosities because the shear conditions along the face of the die are very low compared to those in the nozzle of the slot die, where coating rheology must be matched for each layer.
The basic principles of curtain coating are the same for single-layer and multilayer coating, but there are some significant differences between using the slot and slide dies. For the slide die, the top and bottom sides of the curtain are formed at different times with the top layer surface forming earlier at the top of the slide, and the bottom layer is formed at a lower slide. In the slot die, both sides of the curtain are formed at the same time. The curtain on the slide die typically travels over a curved surface with only one fixed contact line while the slot die has two fixed contact lines. The asymmetrical arrangement for the slide die makes the curtain more prone to deflection at the point of release, known as a “teapot effect,” It is a critical operational issue for slide-die applicators, particularly at the high flow rates needed for high-speed coating. If the deflection is not balanced and minimized, then the curtain may land on part of the coating equipment rather than on the paper substrate.
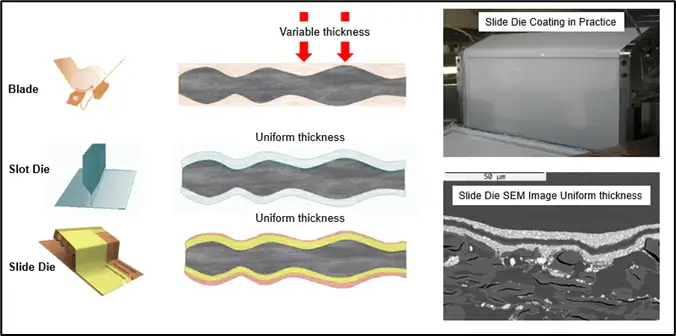
Regardless of curtain-coater type, the benefit of the method is the formation of a contour coating of uniform thickness (see Figure 2). In contrast, a blade-metered coating will give you a very smooth top surface, but the consistency of the coating thickness is dependent on the substrate smoothness, leading to areas where coating is very thin at the high spots in the substrate and very thick in the substrate valleys. This varying thickness affects barrier performance. The barrier layer itself will have to be applied with sufficient thickness to achieve appropriate performance at the thinnest spots, leading to higher costs. With curtain coating, the coating that is applied follows the contour of the substrate – as shown in the coating cross-section SEM photo. All the layers follow this contour and do not intermingle or mix [5].
Technical challenges with MLCC
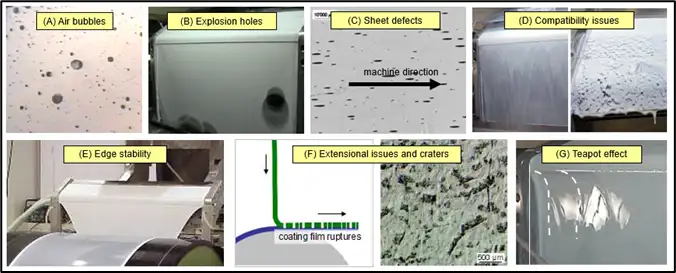
The reliability of curtain-coating equipment comes down to coating color design and proper preparation. For WBBCs, most coating defects will result in a corresponding barrier defect. A variety of defects are possible as shown in Figure 3. All coatings contain air when coatings are compounded (A), so the coating must be degassed to eliminate most air bubbles and especially those greater than one micron in size. Typically, vacuum-de-aeration methods are used. If the coating is not degassed properly, you may get explosion holes (B) in the curtain and/or possibly elongated voids (C) that you cannot see in the moving curtain but which will be visible once applied to the paper. Another problem can be coating-layer compatibility (D). Incompatible layers can be visible as coating separating in the wet state and later causing “mudcracking” defects in the dried coating and usually can be observed on the lip after stopping flow. Another runnability defect happens when the continuous curtain does not hold at the edge guides (E). This usually is an indication that the surface tension of the coating has not been optimized. Edge stability can be improved with surfactants or formulation adjustments.
The coating formulation needs to be designed to have sufficient extensional viscosity (F) for two reasons. As it extends from the die lip, it will thin out as it falls due to gravity, and insufficient extension can result in curtain retreating or splitting. Extensional properties are required to prevent the curtain film from rupturing as it is further stretched when contacting the moving substrate. Insufficient extension can result in crater formation on the coated substrate.
The teapot effect described earlier can create problems. Instead of falling straight down, curtain instability causes the curtain to bend inwards toward the coater body (G). Normally, coatings are designed so that each layer has similar surface tension. A difference in surface tension could cause this imbalance. Adjustments in flow rate and line speed may fix the issue but can be limited depending on coatweight constraints. A falling curtain is very sensitive to external air currents, so shielding in and around the curtain is important and often is provided by the equipment supplier. Another source of air is at the coating interface with the surface of the substrate, where entrapped air could prevent coating application leading to uncoated spots. Vacuum systems remove this air and are placed close to the point of the impingement of coating onto the substrate.
As described, several things can go wrong, but with good planning and experimentation, most problems can be managed by good formulation practices and by matching technology requirements to the application. Unfortunately, standard lab rheology tests that normally are used for shear-induced behavior often don’t predict many of these runnability issues; therefore, best practice often is to run trials on either a small lab-sized curtain coater or at a pilot-coater facility with proper capabilities.
MLLC in practice
Coatings are premetered and all coating goes with the paper – therefore, no recirculation loop is required – where coatings typically would cross each other or consume higher volumes of coating to fill systems. Coating-pump flow rate, coating solids and line speed are used to adjust the coatweight. The coatings are applied without downstream metering or pressure pulse, giving more freedom to substrate composition, including enabling weaker substrates.
There is reduced coating penetration into the sheets, and there are pros and cons with that. One negative is that if you are applying the curtain directly onto an uncoated board, you may need more binder to get the appropriate coating strength. We have seen that curtain coating gives us a perfectly contoured coating, so this is very important for barrier grades because we can improve the coverage. Curtain coaters, especially slide dies, can apply coating layers as low as 1 gsm, which can provide significant material savings for expensive barrier-coating materials.
Barrier-coating studies
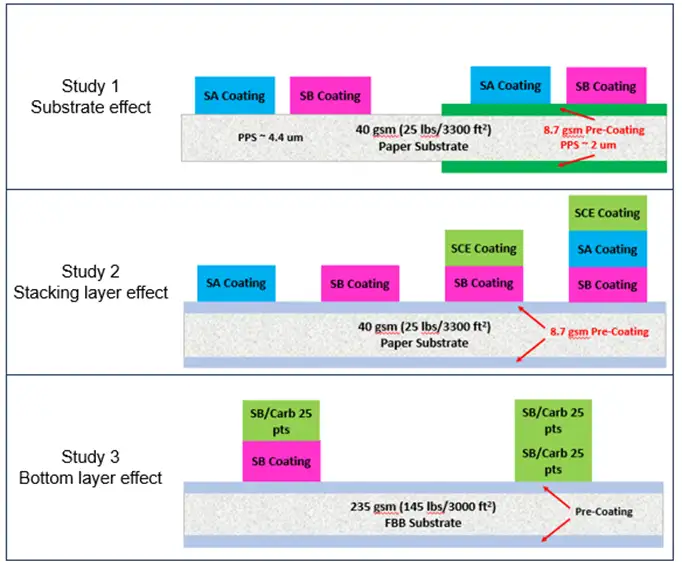
In this article, we will focus on three MLCC barrier studies as shown in Figure 4. The coatings used were based on binder systems from this firm, consisting of styrene-butadiene (SB), styrene-acrylate (SA) and a starch-containing emulsion-based (SCE) barrier chemistries. These studies were conducted on a lab slide-die curtain coater in our lab in Rheinmünster, Germany. Coatings were degassed prior to each run and were applied at speeds of 500-600 mpm. Each barrier layer was applied at a coatweight of 5 gsm.
Study 1 – Effect of Substrate Surface: Study 1 evaluated the effect of uncoated substrate vs. a smoother, blade-precoated base sheet prepared using the same substrate. This precoat provided a more consistent barrier-layer thickness in all directions, as contour coatings have to stretch to fill valleys. The pre-coat consisted of non-barrier-forming coating materials and was applied by blade coater to cover up any high fibers that could cause pinholes and also to fill in the valleys in the base sheet. The uncoated sheet had a PPS roughness of 4.4, whereas the precoated substrate had a PPS of 2. The SA and SB coatings were applied with the slide-die curtain coater.
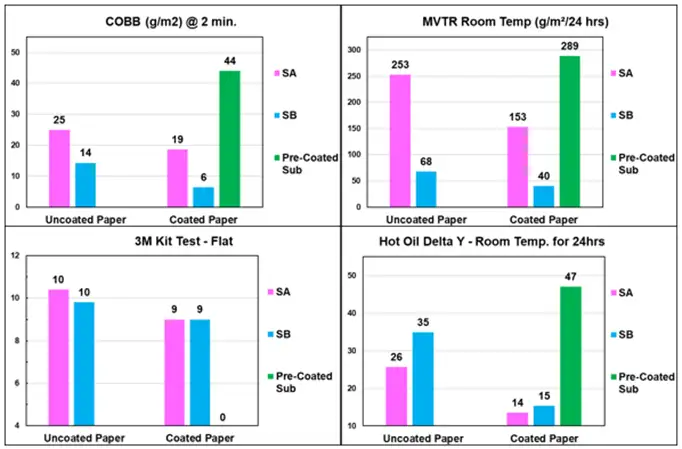
Figure 5 shows barrier test values of the four coated systems. The values for the barrier tests on the uncoated sheet are on the left side and the values for the same barriers on the precoated sheet are on the right side for each property graph. The precoated base sheet also was tested to see its own effect on barrier performance. Cobb data show that there is an improvement in water resistance for both the SA and SB when applied onto the precoated paper. The precoated substrate had very poor water resistance on its own, so the improvement we see mainly is due to the improved quality of the barrier layer on the smoother base. MVTR data also show a significant improvement in MVTR for both the SA and SB when applied onto the precoated paper. Again, the precoated paper is providing no moisture barrier on its own. For the Kit test flat, we do not see any improvement for the barriers on precoated vs. uncoated paper, but we know that Kit is not the best indicator of OGR performance. The substrate gave a zero Kit value as expected. Hot-oil resistance after 24 hrs is shown where lower values are better. We see a significant improvement in oil resistance for both the SA and SB coatings on the precoated paper. The precoated paper had very poor hot-oil resistance on its own, so not a contributor. In summary, barrier coatings applied onto a precoated substrate show better OGR-barrier performance due to a more consistent barrier-layer thickness and fewer pinholes.
Study 2 – Multilayering – Stacking-Layer Effect: The most effective water-based barrier coatings are those formulated at or below the Critical Pigment Volume Concentration (CPVC). Above the CPVC, air voids exist between the pigment and binder particles, which are a source of easy transport for water, oil, etc. At the CPVC, there is just enough binder to fill all the voids in the coating structure. The coating system becomes binder-rich at this point. Below the CPVC, the binder or polymer is the continuous phase in the matrix, and the pigment is dispersed in the polymer. Most water-based polymers when film-formed typically produce a tacky surface so, with higher concentrations of binder, blocking is a problem with these barrier systems. Generally, it is recommended to increase the pigment volume to reduce blocking, but then barrier performance is sacrificed. This issue can be overcome with multilayer coatings where it is possible to bury a polymer-rich coating under a non-blocking top layer. One or two layers that are rich with latex polymer to maximize barrier performance can be assembled under a non-blocking topcoat.
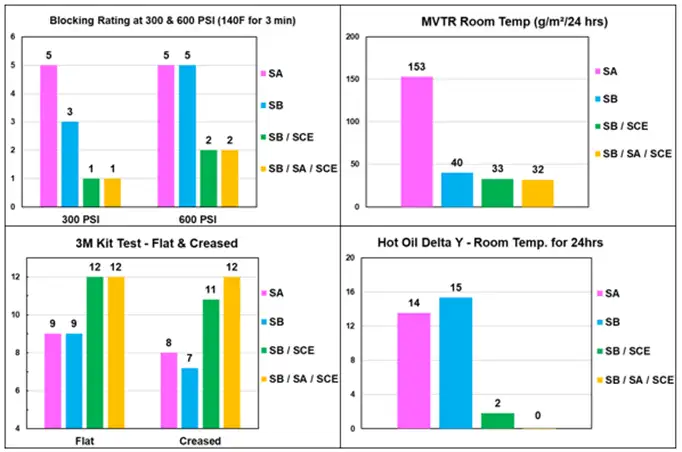
In this second study, we compared one-layer systems based on SA and SB latex-rich coatings compared toa two-layer system with SB and non-blocking SCE top layer, and then a three-layer system with SB, SA and SCE layers. Each layer was applied at 5 gsm onto a precoated paper substrate. Figure 6 shows data for this study, starting with the lab blocking test. In this test, we press two sheets, coated side to uncoated side, for 3 mins at 60o C at different pressures, then peel them apart to observe the blocking. A rating of 0 to 5 is given, where 0 is when the sheets fall apart with no resistance, and a 5 is totally blocked or stuck together. In this set, we have the data at 300 psi and 600 psi. We can see the conditions with the SCE top layer, the green and yellow bars, in both the 2- and 3-layer systems have very little blocking. The MVTR results show that even with the SCE top layer, the 2- and 3-layer systems have slightly better MVTR at room temperature. Use of a starch-containing emulsion topcoat did not reduce the MVTR performance. The Kit testing, both flat and creased, indicates that the SCE top layer over the rich-polymer SB and SA layers also significantly increases Kit values.The hot-oil resistance of the 2- and 3-layer systems are significantly better than the monolayer system. This study shows that you can eliminate blocking without sacrificing barrier performance with the multilayer systems.
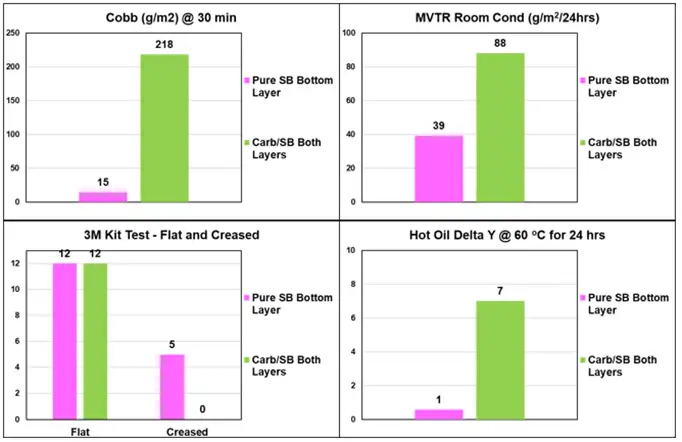
Study 3 – Multilayering – Bottom-Layer Effect with Top Layer Constant: The third study evaluated the effect of a different bottom curtain layer with the same top layer (see Figure 7). The base-layer coatings used in this study were a 100% SB vs. a coating with 75 parts calcium-carbonate pigment and 25 parts of the same SB latex binder.Both systems had the carbonate/SB coating in the top layer and were applied to a coated FBB substrate, with each layer being applied at 5 gsm.
The system with the pure SB in the base layer had significantly better MVTR performance and also significantly better Cobb value. Although the flat Kit values were both 12, it was observed for creased Kit the carbonate/SB base layer (see green bar) cracked during the creased Kit test, resulting in a total failure, but the SB base layer, being more flexible, gave creased Kit of 5. Significantly better oil resistance also was observed for the SB base-layer condition. In summary, a significant improvement in the performance of the barrier system can be made by optimizing the barrier properties of the lower layer.
Conclusion
Multilayer curtain coating (MLCC) has economic and technical advantages over single-layer curtain coating and especially conventional coaters. MLCC allows the application of multiple coatings in one operation, minimizing capital investment and machine footprint, and is today a fully developed technology for the coating industry. Laying down a contour coating provides excellent coverage with low impact. Because curtain coaters can apply precise, thin layers, one can minimize the amount of expensive barrier components or functional coatings, and optimize the composition of the lower coating layers to give the greatest barrier performance without worrying about blocking resistance or heat sealability that can be managed in the top layer. Because the layers that are applied remain intact and distinct, the possibilities to be creative and use different coatings (such as reactive coatings) or to use materials that promote certain functional behavior (like stiffness or flexibility) exists for the specialist to design. MLCC allows the greatest flexibility and options for developing barrier systems with multiple barrier properties.
References
- Ventresca, Donato, “Multi-Functional Barrier Coating Systems Created By Multilayer Curtain Coating,” October 2023, Specialty Papers US, Milwaukee (WI) USA.
- Ventresca, D., Welsch, G.W., “Multi-Functional Barrier Coating Systems Created by Multilayer Curtain Coater,” PAPERCON 2021.
- Ventresca, D., Welsch, G., Eisenhauer, D., Benz, B., Burton, D., “Multi-Functional Barrier Coating Systems Created by Multilayer Curtain Coating,” April 2023, TAPPICon 2023, Atlanta (GA) USA.
- Urscheler R., Roper J., Dobler F., et al. 2006, “Multilayer Curtain Coating – an enabling technology for increased efficiency and new paper grades,” 22. PTS-Streicherei-Symposium, September 2005, Baden-Baden, Germany.
- Kilcher, G., Dahlvik, P., “Multilayer Curtain Coating – Back to the Future!,” PTS, 2019.
Greg Welsch, global innovation and TS&D leader for Trinseo LLC (Midland, MI), can be reached at 989-495-4804, email: gwwelsch@trinseo.com, www.trinseo.com.