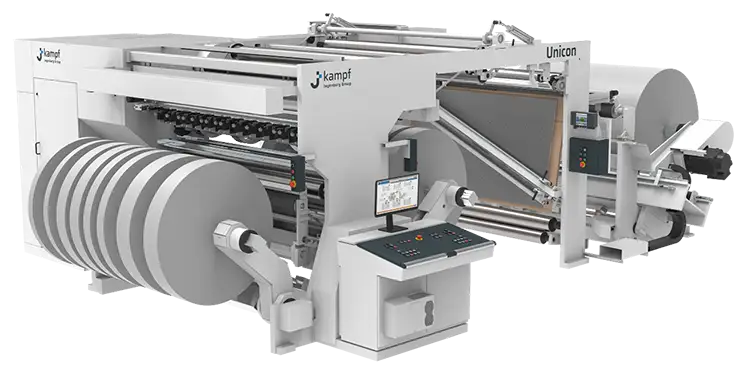
By Martin v. Pawelsz, Head of Sales, Rigids & Tech App, Kampf GmbH
The challenge in producing perfect rolls lies in the non-uniformity of material formation processes, coatings and printed surfaces. The following article looks at the intricacies of the winding process, the importance of roll hardness and the ultimate goal of producing high-quality label stock material with a high degree of automation.
Market experts and observers still forecast a growth rate for print labels until 2027. Various factors are fueling growth during the forecast period, such as increasing demand for more attractive brands from print-label customers and rising demand for industrial goods.
In recent years, label converters have felt the need for automation at various stages of the product life cycle. Skilled labor shortages in this industry sector can lead to bottlenecks in the production chain, and the demand for quality is increasing. The challenge in producing perfect rolls lies in the non-uniformity of material formation processes, coatings and printed surfaces. The following article looks at the intricacies of the winding process, the importance of roll hardness and the ultimate goal of producing high-quality label stock material with a high degree of automation.
Material challenges
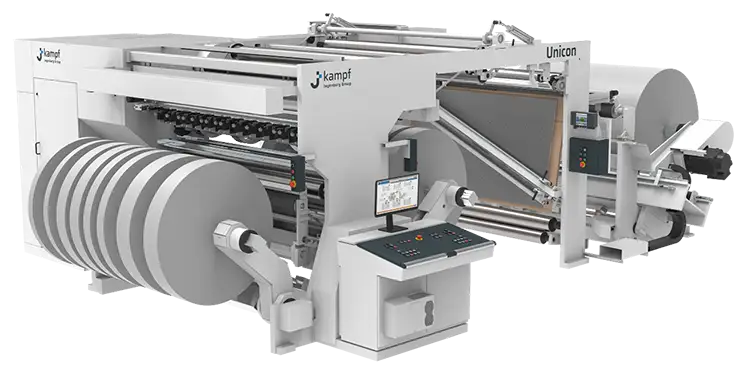
When it comes to slitting and winding of labels and specialty paper, the material determines the appropriate slitting machine concept.
If the full web width would be of equal thickness, producing perfect rolls would not be much of a challenge. However, due to the non-uniformities in material formation processes, coatings and printed surfaces, there is no such thing as a perfect material. Given this reality, the challenge of the winding operation is to ensure that these imperfections do not stand out in appearance and are not amplified during the winding process.
The slitter operator also must ensure that the slitting and winding process does not introduce additional variations in product quality. The ultimate challenge is to wind material that will run on a customer’s process without problems and produce high-quality products for customers.
In the processing of label materials, it is crucial to maintain a consistent web tension to achieve the best winding quality. This ensures that no winding errors, such as telescoped rolls or layer misalignment, occur.
The importance of roll hardness cannot be overstated. Roll density, or in-wound tension, is the most critical factor in determining the difference between good- and poor-quality rolls. Rolls that are wound too softly will go “out-of-round” while winding or during handling or storage. The roundness of rolls is crucial in a customer’s operation to enable processing these rolls at maximum production speeds with minimal tension variations.
Tightly wound rolls present their own set of problems. They can create blocking-defect issues, where the layers fuse or adhere. When winding extensible material on thin-wall cores, winding hard rolls can cause the cores to collapse or elongate, leading to problems with shaft removal or with inserting the shaft or chucks during the subsequent unwinding operation.
Machine selection
The author’s company provides the appropriate machine types for different materials, such as label stock combinations like film-adhesive-paper, paper-adhesive-release liner and film-adhesive-film.
Two examples are as follows:
- Unicon: This machine is suitable for processing label materials without significant thickness differences, up to working widths of 2,050 mm and even narrow widths. The finished rolls are wound on a continuous winding shaft and swiveled radially as the diameter increases. The winding concept is a center drive and surface drive with a driven contact roller.
- Unislit II c/s: If larger thickness differences are expected in the materials, the Unislit II c/s offers the right concept. It is equipped with individual horizontal moving winding stations with center drive and surface drive with a driven contact roller.
Summary
High roll-quality and high speeds are important, but output primarily is determined by the logistics around the machine. If the machine is modular, a kit with automation modules can increase throughput. When these components are ordered from a single source, they complement each other and can be installed, adjusted, programmed, controlled and maintained together. Available systems include mother- and finished-roll handling, mother-roll handling with automatic splice, finished-roll unloading, automatic web cross-cutting and automatic knife positioning, to mention a few.
Martin v. Pawelsz is head of Sales, Rigids & Tech App for Germany-based Kampf GmbH. He has 30 years of experience in the slitting and winding business at Jagenberg, Voith, Andritz and Kampf, beginning as a mechanical fitter at Jagenberg and obtaining further education as a mechanical engineer. Martin can be reached at +49 2262 81-0 or www.kampf.de.