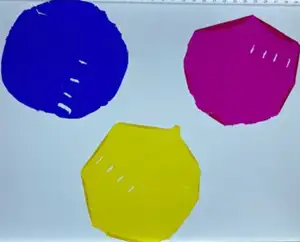
By John Park, Chad Roberts, Chris Milasincic and Kevin DeMartini, HD MicroSystems LLC
Polyimide, a high-performance polymer, offers unique advantages in various fields, including semiconductor chip packaging, the flexible PCB board industry (known as Pyralux® laminate) and high-dielectric-strength wire wrap (known as Kapton® film and Oasis®). Here, polyimide layers are prized for their exceptional properties. This study introduces a novel liquid-polyimide formulation designed for roll-to-roll processing. Unlike traditional polyamic acid-based liquid precursors, the formulation is a ready-to-use polyimide solution, offers broader solvent compatibility and requires only very low curing/drying temperatures (and short time under temperature) to use. The authoring company’s novel liquid polyimides deliver comparable cured-film properties to Kapton® while enabling high-throughput coating production where a polyimide layer can be much thinner using a liquid rather than a traditional standalone polyimide film, polyimide film laminate or film shrink wrap. This liquid polyimide product has been applied successfully at industrial scaling, with its full market potential and wider application adoption continuing to be explored.
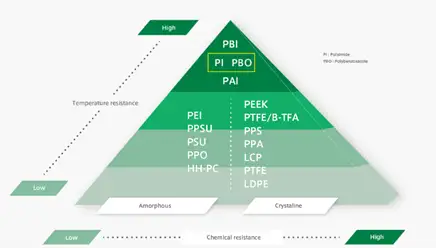
Polyimide (PI) is a versatile polymer widely used in roll-to-roll (R2R) manufacturing, particularly in the form of DuPont’s Kapton® film. Known for its exceptional mechanical, thermal and electrical properties, PI is suitable for a broad range of industries (see Figure 1). Its high heat resistance (up to 500° C) and resistance to chemicals, shocks, friction, bending and torsion make it a valuable material. Additionally, PI’s low permittivity (Dk) and thermal expansion (CTE) are advantageous in many applications.
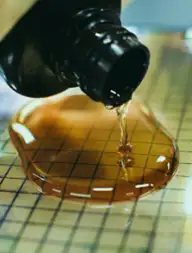
In the converting industries, PI film has found diverse uses, including heat-resistance tape, flexible printed circuit boards, foldable panels and wires for motor and aerospace applications. While solid-form PI films are well-known to scientists and engineers in this field, liquid-form PI, often sold as polyamic acid (PAA), also is commercially available (see Figure 2) [1].
PAA solutions in R2R manufacturing
PAA, a precursor to polyimide, has found broad application in semiconductor packaging. Its uses include interlayer dielectric coatings, stress buffers atop integrated circuits, redistribution layers in advanced packaging (flip chip, chip-scale packages and wire-bonding) and temporary adhesives for packages and power devices. Beyond semiconductor packaging, PAA has been applied in printed and flexible electronics for dielectric coatings in wearable devices, additive manufacturing and other areas [2-5]. PAA is a polymeric material formed by the reaction of a diamine with a dianhydride. It contains a repeating unit with an amic acid group and can form a polyimide by cyclization, which is promoted by elimination of water molecules from the amic acid group.
Applying PAA solutions in R2R manufacturing and flexible/printed electronics presents several challenges. Firstly, the conversion of PAA to polyimide requires prolonged exposure to high temperatures (over 300° C for an extended period), making it an energy-intensive process. Secondly, many PAA formulations contain per- and polyfluoroalkyl substances (PFAS), raising environmental and regulatory concerns. Thirdly, PAA solutions require strict storage at approximately -20° C, which can be challenging for handling and logistics. Repeated thawing and refreezing, as well as poor shelf-life at room temperature, further complicate their use. Fourthly, PAA is relatively expensive compared to other polymer solutions. Finally, the backbone polymers of PAA solutions have a limited range of compatible carrier solvents, often requiring high-temperature drying after coating, increasing processing complexity.
Here, the authors’ company has developed a novel liquid polyimide formulation that addresses the limitations of traditional PAA-based polyimides. Unlike precursors, the formulation is ready-to-use and offers a broader range of solvent compatibility, including cyclopentanone, PGMEA, MEK, gamma-butyrolactone, NMP and more. This versatility enables its application through various coating methods such as spin coating, spray coating, inkjet printing and R2R-based techniques.
Liquid polyimide for R2R processing
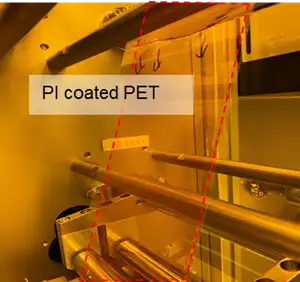
The liquid polyimide developed by the authors’ company is said to be cured at significantly lower temperatures (~200° C) and require shorter curing times (~15 min), making it suitable for high-throughput R2R processing. Despite these advantages, it delivers comparable cured-film properties, including high glass-transition temperature, high decomposition temperature, good elongation, tensile strength, modulus and dielectric properties. Furthermore, its room-temperature storage eliminates handling and logistic challenges.
Toward R2R manufacturing, the liquid polyimide has been demonstrated successfully in both lab-scale and large-scale environments. In lab-scale experiments (see Figure 3), the liquid polyimide was formulated in cyclopentanone with solid contents ranging from 20% to 30%. The viscosity of these formulations varied from 200 cP to 2,500 cP at 25° C. Using an 80R-size Microgravure roll, coatings were applied with a wet thickness of 12-20 µm onto heat-stabilized PET substrates. The coating process was conducted at speeds of 0.5 and 1 m/min, with a kiss-roll coating speed set at a 1:1.5 ratio. The coated films were dried in a hot-air oven at 90° C and 130° C, resulting in final coating thicknesses ranging from 1 to 8 µm with the different formulation and coating conditions. The liquid polyimide solution is compatible with various additives, including SiO2, TiO2 and pigments. Tests have successfully demonstrated the application of pigmented liquid polyimide to impart color (see Figure 4) and enhance dielectric properties on PET and PEN films with widths ranging from 1.0 to 1.5 meters and lengths of 100 to 500 linear meters.
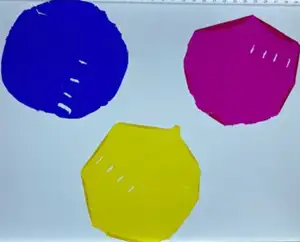
The company’s developed polyimide demonstrates potential across various industries and applications. Its exceptional cured-film properties and versatility make it well-suited for a range of optical coatings, including clear, colored and those with enhanced dielectric performance. Furthermore, the polyimide is compatible with diverse coating methods, such as slot-die, gravure, spin coating, inkjet printing, aerosol jet printing and spray coating, ensuring its adaptability to different manufacturing processes.
The authors anticipate substantial demand for this advanced polyimide in the field of integrated circuits, particularly for both rigid and flexible substrates. Additionally, its promising characteristics position it as a valuable material for electrochemical devices, such as batteries.
Conclusion
The developed liquid polyimide formulation offers a promising solution for various applications in R2R manufacturing and flexible/printed electronics. Its unique properties, including lower curing temperature, broader solvent compatibility and room temperature storage, make it a viable alternative to traditional PAA-based polyimide precursors. The successful demonstration of its application in both lab-scale and large-scale environments highlights its potential for commercialization and integration into various industrial processes.
References
- Biswas, Shantonu, et al. “Integrated multilayer stretchable printed circuit boards paving the way for deformable active matrix.” Nature communications 10.1 (2019): 4909.
- https://www.hdmicrosystems.com/rad/polyimide
- Kwon, Young-Tae, et al. “All-printed nanomembrane wireless bioelectronics using a biocompatible solderable graphene for multimodal human-machine interfaces.” Nature communications 11.1 (2020): 3450.
- So, Changrok, et al. “Epidermal piezoresistive structure with deep learning-assisted data translation.” npj Flexible Electronics 6.1 (2022): 70.
- Wang, Binghao, et al. “Flexible and stretchable metal oxide nanofiber networks for multimodal and monolithically integrated wearable electronics.” Nature communications 11.1 (2020): 2405.
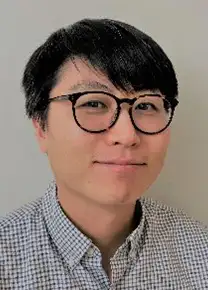
Janghoon (John) Park is a principal investigator at HD MicroSystems (HDM). HDM is a 50-50 joint venture of DuPont and Resonac and is the leading supplier of polyimide and PBO precursor chemistries specifically engineered for microelectronic applications. John has expertise in formulations, R2R coating and printing processes for semiconductor packaging, flexible/printed electronics and electrochemical devices. He received his Ph.D. in Mechanical Design and Production Engineering from Konkuk University in South Korea. Prior to joining HDM, he worked at the Chemistry and Nanoscience Center, National Renewable Energy Laboratory in Colorado. John can be reached at 302-295-1869, email: john.park-1@dupont.com, www.hdmicrosystems.com.