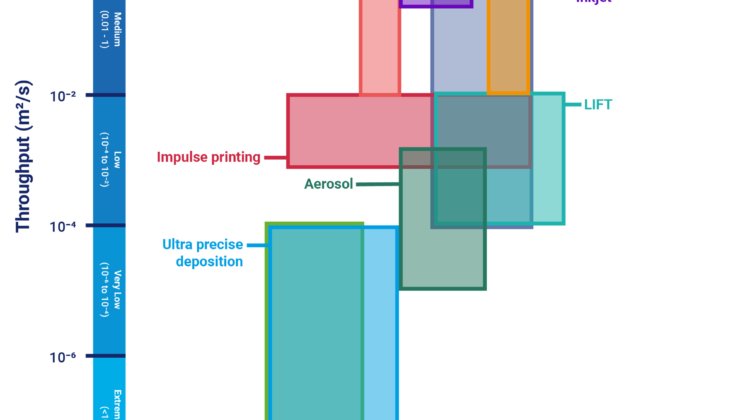
By Matthew Dyson, Ph.D., principal technology analyst, IDTechEx
Printed & flexible electronics represent a great opportunity for the converting industry to use existing capabilities to produce higher-value functional products. This article reviews developments across compatible applications that require large areas or very high volumes. Those that don’t require pick-and-place, such as thin-film heaters and parts of electronic skin patches, typically will have lower adoption barriers. Combining pick-and-place with a roll-to-roll (R2R) line broadens the application space to include large-area LED lighting and, ultimately, smart packaging. Finally, emerging deposition techniques, such as laser-induced forward transfer (LIFT), offer the promise of high-speed digital printing, enabling R2R equipment to be used for high-mix, low-volume manufacturing.
Introduction
Printed & flexible electronics represent an alternative to the conventional, printed circuit board (PCB) production method of etching laminated copper layers on rigid substrates. These types of electronics offer two main value propositions: form factor, which can be large-area, flexible or even stretchable, and compatibility with digital and/or continuous-manufacturing methods that change production economics.
Despite being viewed by many as an “emerging technology,” printed & flexible electronics already are used commercially, including for car-seat occupancy sensors and blood-glucose test strips. The potential application space is extremely broad, ranging from building integrated photovoltaic panels to automotive touch sensors and from electronic skin patches to smart packaging on a long list of consumer goods.
Purely printed applications
The most straightforward approach to adopting printed electronics is to simply print conductive functionality – without mounting any components. The power supply, along with data readout and processing, typically is provided by a conventional PCB linked by a component, such as a zero insert force (ZIF) connector. The lack of mounted components greatly simplifies manufacturing, especially if done R2R, thus reducing costs. Established examples of printed functionality without mounted components include automotive-seat occupancy sensors and glucose test strips.
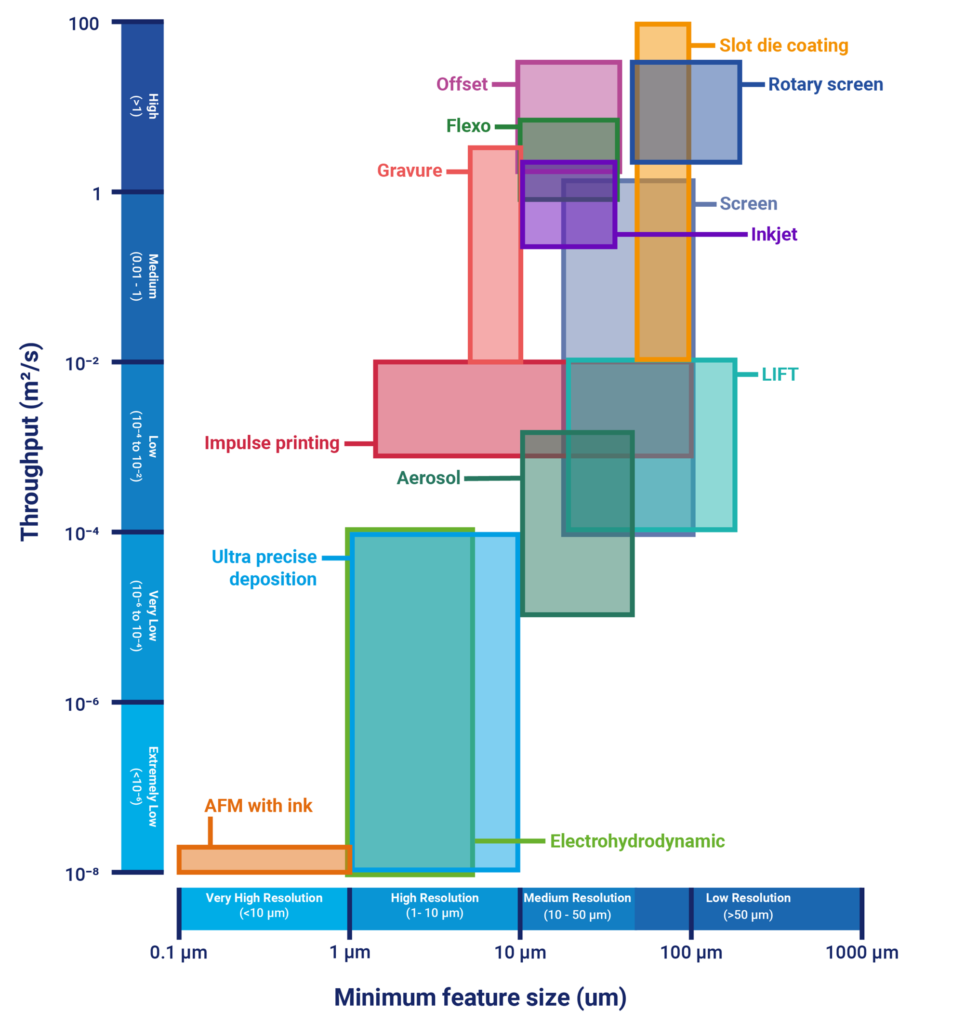
Screen printing is by far the most common deposition technique across printed electronics, primarily due to its compatibility with viscous inks that enable thick traces with the desired conductance to be deposited in a single pass (see Figure 1). Furthermore, the same technique can be used from small- (small-area, sheet-to-sheet) to high-volume (rotary) manufacturing, reducing the technical challenges in scaling up. Notably, many companies are looking to transition from traditional graphical-screen printing or membrane switches to printed electronics, with the motivation of leveraging their existing expertise to a new industry that produces higher-value items. Of course, there is a wide range of both digital and analog printing techniques, some of which can produce features as small as 1 µm.
Flexible hybrid electronics
The next step up in manufacturing complexity is to mount some of the functionality directly onto the same flexible substrate, rather than connecting to a separate PCB – this approach of “print what you can, place what you can’t” is known as flexible hybrid electronics (FHE). Mounted components typically include an integrated circuit but can extend to MEMS (microelectromechanical systems) sensors, batteries, LEDs and more. The motivation is to capture the benefits of a flexible form factor, digital/additive manufacturing with the functionality of mounted components, because printed logic/memory has proven very difficult to commercialize.
The main commercial challenge for FHE is finding applications that add sufficient value relative to the incumbent approach (typically rigid or flexible PCBs with etched copper) to merit the additional costs associated with transitioning to a new technology. Arguably, the most straightforward opportunities are those that use FHE’s compatibility with digital manufacturing methods, such as rapid prototyping and small-volume manufacturing. Smart packaging/smart tags is a potentially huge addressable market, but displacing low-cost, stamped-aluminum antennae with printed conductive will be tricky unless circuits can be printed directly onto packaging using existing infrastructure. Wearable healthcare devices are a compelling use case where flexibility/stretchability adds considerable value, supported by the macro drivers of a transition toward “digital healthcare” and an aging population. Again, a considerable challenge here is adding sufficient value relative to the incumbent solution of housing conventional electronics in a reusable rigid box.
Technical challenges for FHE include developing sufficiently durable products that can withstand mechanical stress and thermal cycling – this can be difficult due to the disparity in material properties between polymeric substrates and inorganic components. Consumer-facing applications (smart packaging and disposable electronic skin patches) also likely will require improvements in sustainability.
Toward high-volume digital manufacturing
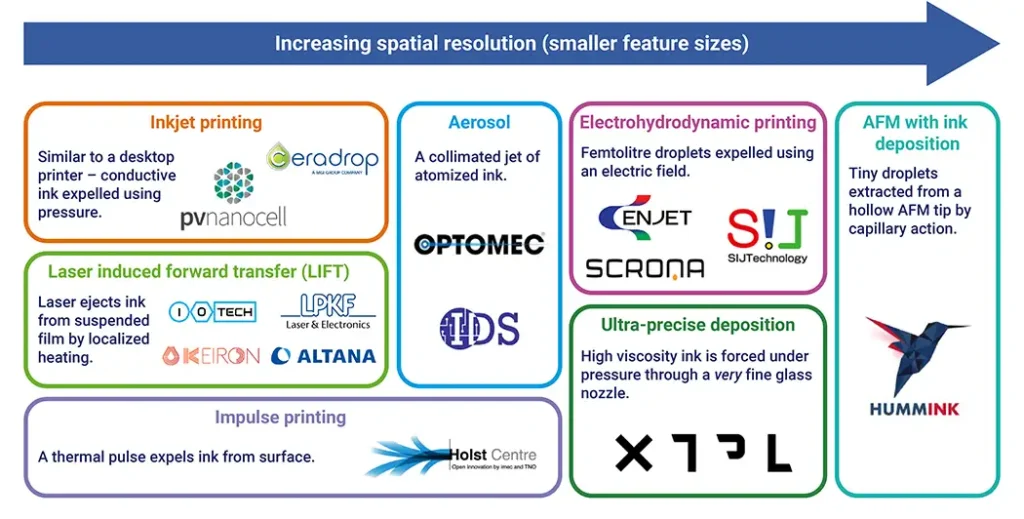
Continuous roll-to-roll manufacturing generally is associated with low-mix, high-volume (LMHV) orders – for example, rapid production of thousands of newspapers every evening. A single design is imparted to the cliché and then printed many times. Even if the print pattern can be changed efficiently, with conventional analog-printing techniques such as gravure or flexography, the minimum volume for a single print pattern typically is a roll of substrate, usually 10s of meters long. However, there are few applications of printed electronics, particularly given the relatively early stage of commercial adoption, that require sufficiently high volumes to justify the capital expense (see Figure 2).
Digital printing offers a solution. If inkjet or laser-induced forward transfer (LIFT) is combined with R2R printing, then the minimum order volume is no longer determined by the length of the substrate roll. Instead, every circuit printed can, in principle, be different (although they would need to be separated afterward).
More likely, different circuit designs could be printed onto different sections of the roll. For example, a contract manufacturer could use the first 10 meters of a substrate roll to produce circuits for one customer, and the rest of the roll for another – all in the same print run. This would significantly reduce costs relative to S2S (sheet-to-sheet) as the individual sheets wouldn’t need to be handled.
Despite this benefit of digital-printing techniques in enabling high-throughput, R2R circuit manufacturing to be used for high-mix, low-volume (HMLV) production, analog rotary screen printing remains the most common choice for new lines – for example, it will be used by new printed-electronics contract manufacturer TracXon. This is because it allows high volumes of viscous ink to be swiftly deposited. However, if contract manufacturers want to use R2R for smaller lot sizes, then digital printing methods, such as LIFT, that also are compatible with highly viscous inks are highly compelling.
Conclusion
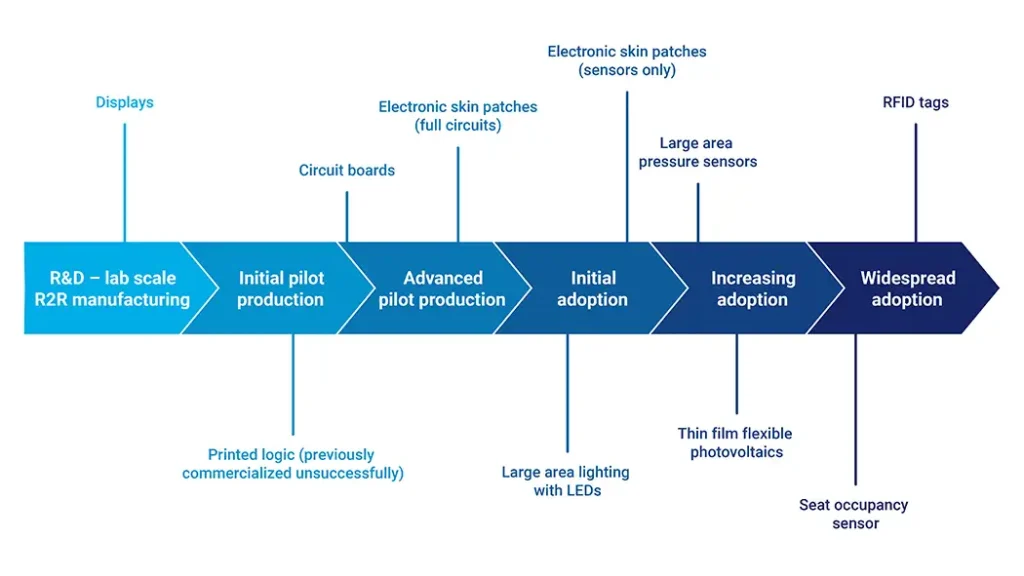
In summary, there is a great opportunity for companies with existing converting or screen-printing capabilities to produce printed electronics. Initial targets are likely to be purely printed, but over time investment in pick-and-place capabilities will enable production of more sophisticated FHE circuits with mounted components (see Figure 3).
Dr. Matthew Dyson, principal technology analyst at IDTechEx (London, UK), holds an MRes and Ph.D. in Physics from Imperial College London, in which he investigated organic semiconductors, followed by post-doctoral research at Eindhoven Technical University in The Netherlands. At IDTechEx, Matthew uses this background to assess technical developments and commercial opportunities across the printed/flexible/hybrid electronics space. He can be reached at +44-1223-827-631, email: m.dyson@idtechex.com, www.idtechex.com.