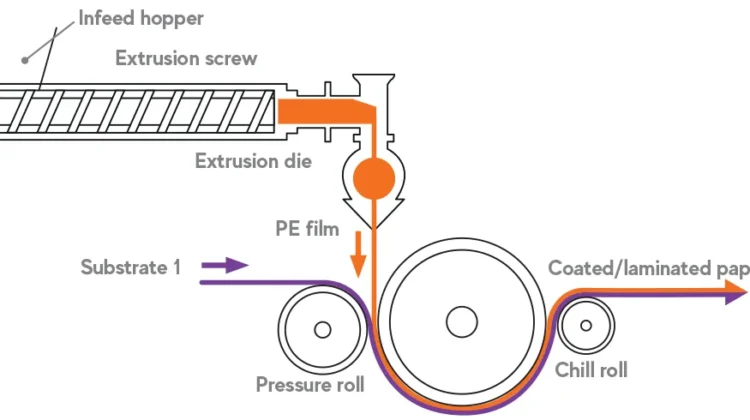
By Dr. Tobias Nienke, technical account mgr.-Pressure-Sensitive Applications, Mondi Functional Paper & Films
Structured release liners combine air egress, slideability and repositionability to enable easier installation of pressure-sensitive products, such as tapes, graphics and labels. A canal structure is applied to the surface of the liner during the extrusion process; this structure then is transferred to the adhesive layer and enables the described features. After installation, the structure remains invisible, allowing for a perfect surface finish. This article provides insight into the underlying manufacturing technology, explains the different structure types and illustrates their application. Furthermore, it highlights this firm’s approach to a sustainable, plastic-free solution based on clay-coated paper.
Introduction
Release liners are used across a range of industries due to their versatile and reliable performance levels. Particularly suitable for pressure-sensitive adhesive (PSA) applications, combined with adjustable degrees of rigidity and release values, they can be tailored to suit different, specific requirements. Already performing at a high standard, release liners are continuing to evolve and improve, particularly for high-end applications, without compromising on performance. And along with these characteristics, release liners also are helping to ensure sustainability remains at the forefront of development.
There are several different liner types, based on film or paper substrates, which are equipped with customized silicone-coated systems that allow precise specification of release forces. For excellent surface properties and dimensional stability, two-sided polymer extrusion coatings are applied on various substrates [1]. Polymer-coated (kraft) papers (PCK) often are used as substrates for graphic products, such as car-wrapping films. Through the extrusion process, it is possible to give the surface of the PCK liner a structure that enables additional, useful performance properties.
- The extrusion process of a PCK liner
Extrusion-coating and extrusion-lamination processes are quite similar. They differ through the presence of a second or auxiliary web that sandwiches the melt in the lamination process. In the 1940s, extrusion coating replaced wax-dipped paperboard and was introduced to the market by a major supplier of gabletop cartons for milk and other beverages [2].
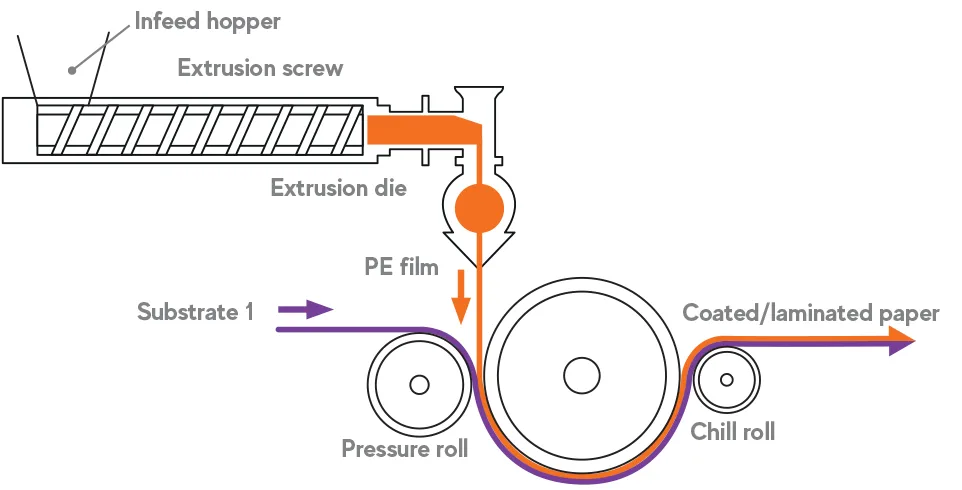
The process consists of three fundamental steps, which are shown in Figure 1. Polymer granules are melted in an extruder. The molten polymer stream is transferred to a die, where it is exposed to the open atmosphere. The melt curtain leaving the die then falls by its own gravity onto a paper or film substrate and into a nip between a pressure roll and a water-cooled chill roll. During this process, the molten material is elongated by a factor of 30-40X. The chill roll usually is copper- or chrome-plated and accelerates the curing process of the hot curtain.
Parameters influencing adhesion between polymer and substrate are: [3]
- Melt temperature
- Distance and time between die lip and nip
- Nip pressure
- Web pretreatment
- Polymer type
The two-sided extrusion process at this firm is done using a tandem line that combines two separate extrusion units, siliconization and backside printing in one machine pass. The extrusion process allows creation of a surface structure on the PCK liner, enhancing its performance with additional beneficial properties.
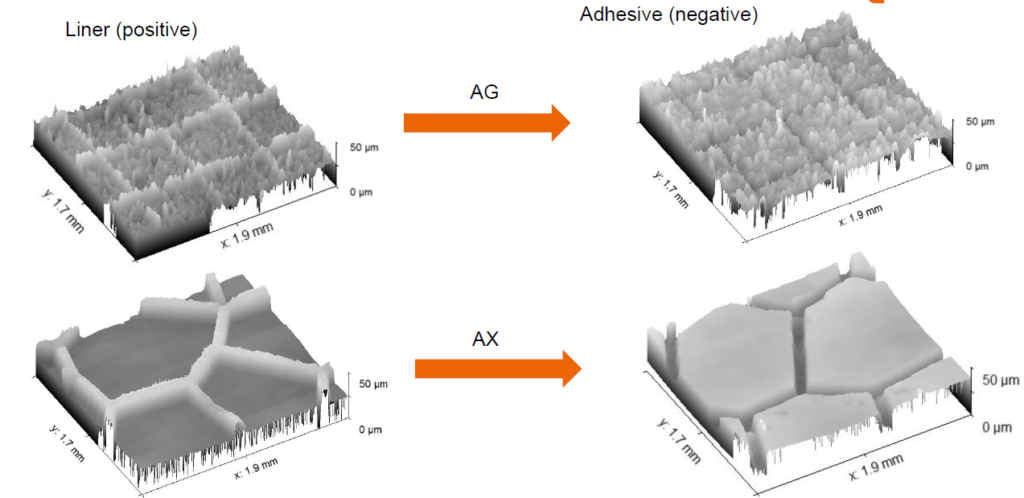
We have implemented a technique in which fine structures are transferred from the chill roll onto the extruded liner surface. When adhesives for pressure-sensitive products, such as car-wrapping films or tapes, are applied onto the liner, this structure is transferred into the adhesive. The result is an adhesive layer with a small canal structure. Figure 2 shows how the liner structure is the template for the structured-adhesive surface. The main benefit of this canal system is an air-egress functionality, when the PSA material is applied to a surface. By allowing the air to escape through the canal structure, it is possible to apply large films without bubbles. Car-wrapping can be done much easier using these kinds of films. After application, the canal structure disappears within a few hours, ensuring a high-quality result.
This firm has been working to improve structured liners for almost two decades, developing new structures to enhance the functionality of the liner and PSA product. Slideability and repositionability are additional features that make the liners much more user-friendly. The film now can be laid out onto its surface and perfectly positioned without it immediately adhering, meaning a truly flat finish can be achieved as the film will start to stick only once pressure is applied. There still is room for error; however, if the wrapping is not positioned correctly or needs an adjustment, it can be removed and reapplied to the surface without compromise to its performance or its finish. This reduces waste, saves money and means the quality and performance of the finished product is guaranteed. Table 1 gives a detailed overview of the different structure types and their main features.
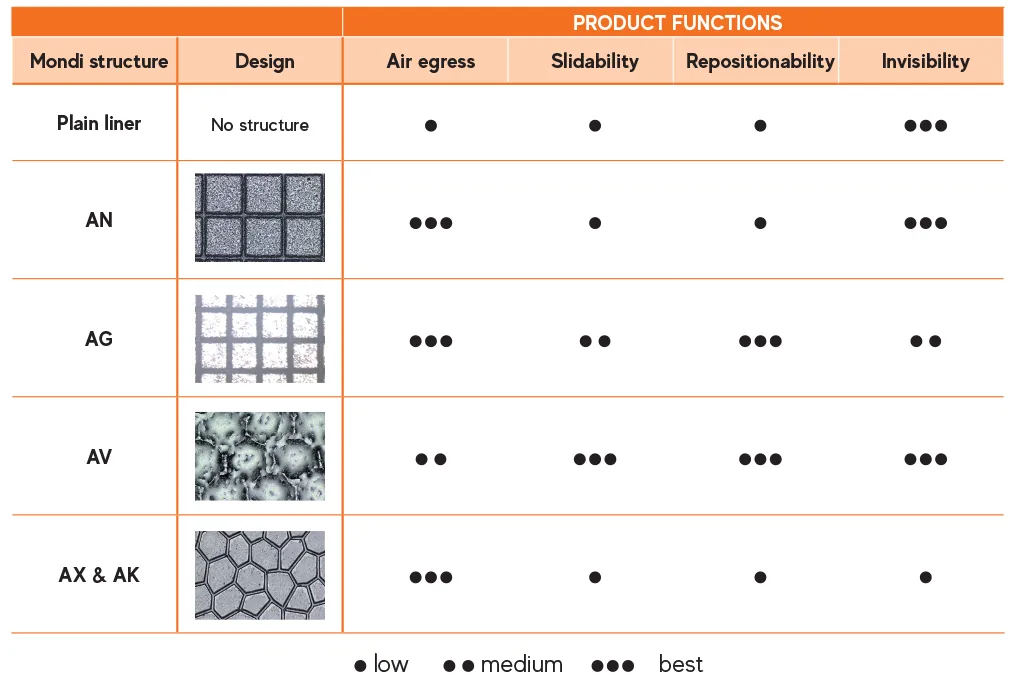
1.1 Structured release liners as key for the car-wrapping and printing industries
The author’s company’s portfolio of structured liners includes different products for a variety of applications. Two of these are car-wrapping and platemounting tapes for the printing industry.
Car-wrapping is a constantly growing market. The demand for individual brand advertising, paint-protection films and complete color changes is increasing. In the past, air entrainment on large film pieces was a major issue that required highly skilled staff. The air-egress feature of the AG-structure is a significant solution as the additional repositionability allows a precise application. For this industry, the invisibility of the structure after wrapping the car also is very important.
Platemounting tapes help the printing industry achieve excellent results. Print layouts and, therefore, also flexographic sleeves need to be changed constantly. Bubble-free mounting of the sleeves with the help of foam tapes is key. The AK-structure reportedly provides a convincing performance for this application.
- Making it sustainable
While the performance of release liners is vital, it also is imperative that they help customers on their sustainability journeys. The automotive industry has been going through huge (and necessary) upheavals to become more sustainable, and this drills down into every component of the vehicle, even the release liners. It means that the industry must work to develop sustainable products and introduce innovative ideas that contribute to a circular economy. For example, recent developments in this firm’s release-liner portfolio include a range of sustainable PCK liners and a clay-coated structured liner.
Sustainable PCK liners: Produced with 100% recycled base papers and delivered with a coating made from up to 100% renewable resources, this firm’s sustainable PCK liners have 60% lower CO2 emissions in materials and manufacturing than traditional liners. They are available in plain and with structured surfaces.
Clay-coated structured liners: There is a growing demand for plastic-free liners that still offer advanced features such as those introduced with structured PCK liner. For less-demanding applications, a more sustainable product range of structured liners is available. Clay-coated paper (CCK) is used as base paper for this product range, and an embossing station is used to give the liner a structured surface.
Embossing process for CCK structured liners
The embossing process for structured-CCK liners takes place without any polymer layer onto the substrate, ensuring no plastic is used compared to PCK-based liners. Embossing units apply specific surface topographies onto the substrates. The technology is well known in tissue-paper production but also can be implemented in other areas of paper converting. Embossing can change absorption behavior, softness and tensile strength of a fiber material. Two different methods have been established in the industry:
- Force-locked embossing using steel/rubber or polymer/rubber-roller combinations
- Form-locked embossing using steel/steel-roller combination
Because a pair of steel and rubber rollers can be implemented at a lower cost, force-locked embossing has become the standard in the roll-to-roll (R2R) converting industry. Furthermore, the endurance of the steel roller is higher for this combination and register control is not necessary. Paper embossing usually is done as cold embossing. Operating a constantly compressed rubber roller generates heat, which needs to be controlled to avoid increased wear.
Form-locked embossing results in a more stable structure but is more susceptible to creases or dirt entrainment [4]. A male and a female die deform a paper substrate. For all embossing processes, precise control of parameters is critical. By embossing in the elastic zone of the substrate, the structure will recover over time, and the embossing will disappear. Applying too much pressure, on the other hand, can reduce the tensile strength critically and result in web breaks or winding issues [5]. Both of these embossed CCK liners are coated using a solvent-free silicone thatis platinum-cured.
- Collaboration for success
Research and development is an ongoing process, and this firm works with other industry leaders and organizations to continue driving forward. We are part of CELAB (Circular Economy for Labels), an industry-led initiative founded by companies in the pressure-sensitive label industry. This initiative facilitates partnerships with like-minded organizations all along the p-s label value chain, ensuring the recycling of release liners and encouraging universal adoption of industry best practices.
Conclusion
Release liners are a critical component of pressure-sensitive products in the graphics, tapes and label industry. By improving and optimizing product performance, customers can reduce waste and use less material. Through careful sourcing of raw materials, constant optimization of the supply chain and ongoing development of new solutions, a significant contribution toward a more sustainable industry can be achieved.
References
- LyondellBasell, “A Guide to Polyolefin Extrusion Coating,” Houston, TX.
- T. Dunn, Manufacturing Flexible Packaging, Elsevier Science, 2014.
- H.L. Moody, “Extrusion Coating Technology,” Tufted Carpet: Textile Fibers, Dyes, Finishes and Process, Manchester, TN. William Andrew, Inc., 2004, pp. 133-138.
- J. Blechschmidt, Papierverarbeitungstechnik, Munich: Carl Hanser Verlag, 213.
- J. Costa Vieira, M.L. Ribiero, A.M. Martins Salguerio Carta and P.T. Fiadeiro, “Embossing Pressure Effect on Mechanical and Softness Properties of Industrial Base Tissue Papers with Finite Element Method Validation,” Materials, 2022.
Dr. Tobias Nienke, technical account mgr.-Pressure-Sensitive Applications at Mondi (Vienna, Austria), holds a Master’s in Packaging Technology and finished his Ph.D. in the field of coating and drying of thin films. He has been in the coating industry for around eight years and has worked for a coating-line manufacturer and a technical certification company before joining Mondi in May 2023. Nienke can be reached at email: tobias.nienke@mondigroup.com, www.mondigroup.com.