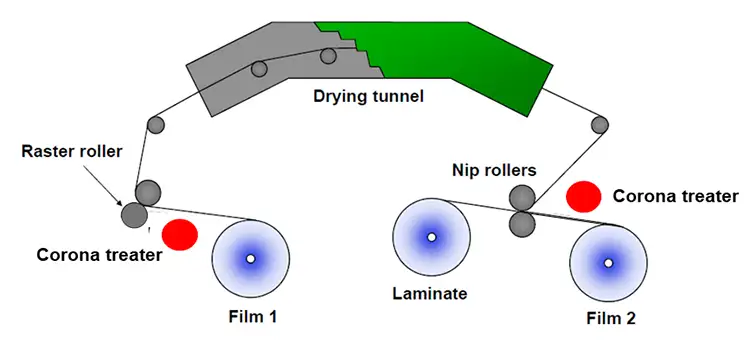
By Kirsten Lykke, consultant-Polymers & Flexible Packaging Technology for Vetaphone A/S
This article discusses the main criteria for high-quality lamination used in today’s flexible-packaging sector and the role that surface treatment plays with sophisticated substrates. Lamination requires two essentials: bond strength and zero visual defects. Fundamental to both is the need to understand the part played by surface tension in maximizing surface-treatment efficiency. Looking at solvent-based and solvent-free technology and outlining the features, advantages and benefits of each, this article highlights the signs you need to look out for to ensure successful production.
Introduction
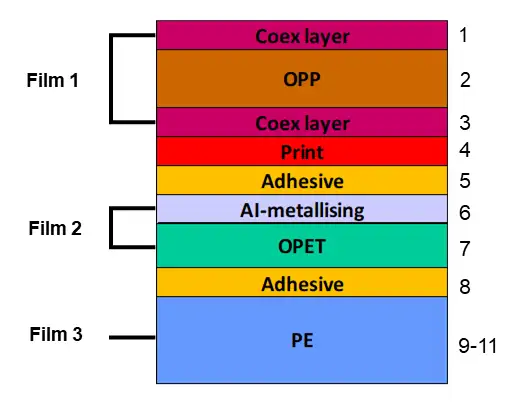
There are two fundamental principles required for high-quality lamination of flexible substrates: high bond strength and zero optical defects. To understand the implication of these and how they can best be achieved, it is important to look at the construction of a typical laminate – and for the purposes of this, I have chosen one used for coffee packaging. Figure 1 shows a construction of 11 separate layers, made up of three films each with different constituents, and “stuck” together by two layers of adhesive in Positions 5 and 8.
Each layer plays an important role, from the coextruded oriented polypropylene (OPP) layer sealing against polyethylene (PE) (lapseal) at Position 1 through the coextruded-OPP providing rigidity and stability, which is necessary to obtain high-quality when printing in register. The metallized polyethylene terephthalate/polyester (PETP) at Position 6-7 provides stiffness and very good barrier properties to keep aroma inside the pack and water vapor, oxygen and light outside the pack. The PE layer at Position 9-11 is able to lapseal to the coex-OPP and provide tight seals when sealing the top and bottom of the pack. The two layers of adhesive bond the three different films together to give the final laminate a high bond strength. Even though the laminate consists of 11 different layers, the total thickness is only 92 microns.
Solvent and solventless techniques
In today’s highly competitive market for flexible packaging, there are two means of producing the film lamination required: solvent-based and solvent-free, which can be seen in the schematics of Figure 2 and Figure 3, respectively. Each has its advantages and disadvantages in terms of end-result, cost, production efficiency and environmental implication.
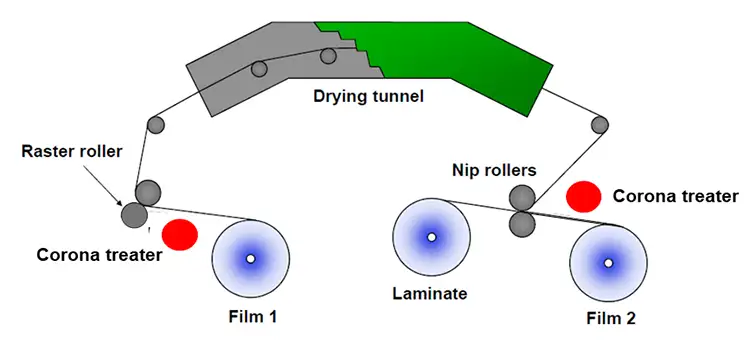
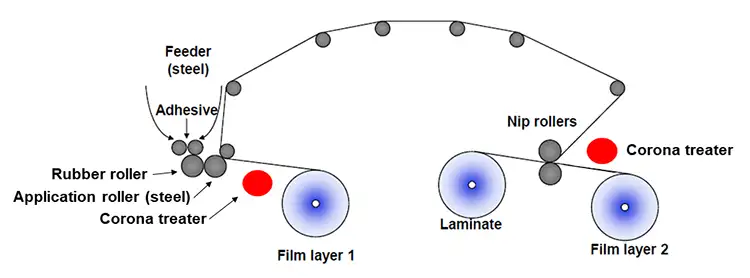
Solvent-based lamination normally is used for retort applications or for very aggressive filling goods. The higher initial tack minimizes the risk of telescoping and, therefore, it is not necessary to adjust the web tension and winding profile precisely. Solvent-based adhesive has a longer “pot life” and allows a higher weight of application that gives good performance, especially for retort applications. You can judge the final optics immediately after lamination – which is not the case with solvent-free lamination.
Against these, and in favor of the solvent-free process, are zero cost for solvents, no energy requirement for drying, an absence of solvent residuals, a lower CO2 index, and significantly, a lower investment level required for the capital equipment involved.
Key terminology
Just for the sake of clarity, one often hears the terms “adhesion” and “cohesion,” and it’s important to understand the difference. Adhesion is the attraction of different molecules, whereas cohesion is the attraction of identical molecules. A simple example is that adhesion is the attraction of the adhesive (glue) to the film – cohesion is the attraction of the adhesive to itself (inner strength).
When the bond strength gets below 1.0 N/15mm, you need to look for the failure mechanism. So, what causes lamination failure? If the adhesive or ink separates from the film, it’s an adhesive failure. The problem often is caused by poor wetting of the film surface, due to low surface tension, set-off or other impurities on the surface. If there is a cohesive failure in the adhesive, look for an incorrect mixing ratio of the adhesive and residual solvents from the ink reacting with the adhesive (only if mirror-printed). If there is a cohesive failure in the ink, it can be due to the adhesive viscosity being too high, which means the adhesive will not penetrate the ink properly.
Know your films
All polymer films have a natural surface tension. Typically, this ranges from 29 dyne/cm for cast polypropylene (CPP) to 30 dyne/cm for low-density polyethylene (LDPE), up to 43 dyne/cm for PETP. But, with surface treatment, usually corona, these values can be increased to 40, 40 and 54 dyne/cm, respectively, which are levels that offer better wetting capabilities.
The surface tension of the films can be influenced negatively by impurities on the surface. These vary from film to film (printed and unprinted) and relate to the migration of slip additives and processing aids, as well as set-off from inks and coatings. To counteract these, corona treatment is required to clean the surface or modify the chemical composition of the film’s surface layer. This allows more oxygen molecules to change the functionality of the film surface, which boosts its surface tension and allows better wetting/adhesion.
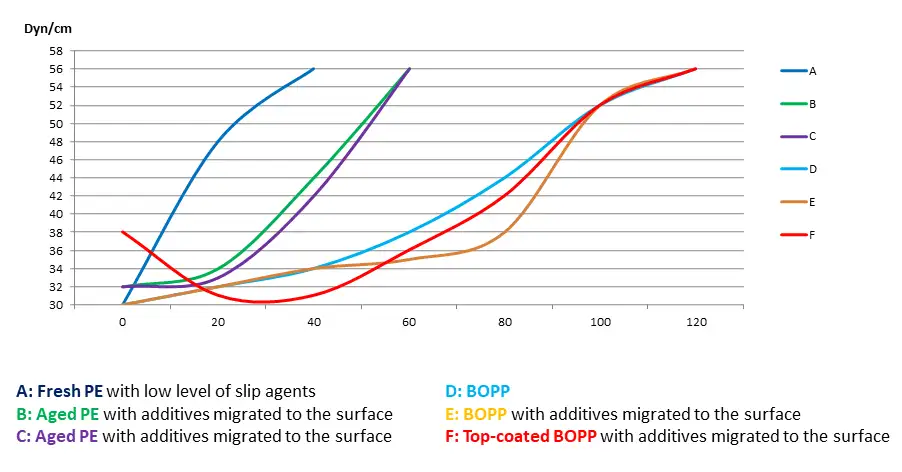
As mentioned above, different film materials have different properties and, therefore, different behavior. In Figure 4, you can see the various dyne levels achievable, and the levels of power required to reach these levels with each film.
One of the important points to grasp is the knowledge that allows you to calculate how to attain a certain dyne level with each film. Taking PE as an example in both fresh and aged form, we can apply the formula: P = W x S x M, where “P” is the power required in Watts at the corona station, “W” is the web width in meters, “S” is the running speed in mpm and “M” is the material factor.
So, for running a 1.2-meter-wide web at 250 mpm with a material factor for fresh PE of 10 W/min/m2, you will require 3,000 Watts of power. A similar calculation for aged PE would be 1.2-meters x 250 mpm x 30 W/min/m2, which needs 9,000 Watts of power.
If you do not have the data available showing which material factor to use for your specific film, this calculation will help you. For standard material, the factor is 15 W/min/m2 (1.4 W/min/ft2) – so the following would apply:
Typical web speed: 200 to 400 mpm (650 to 1,300 fpm)
Typical web tension: 20 to 500 N/m (0.10 to 2.8 pli)
Typical web width: 1,000 to 1,700 mm (40 to 66 in.)
Typical web thickness: 10 to 500 microns (0.40 to 20.0 mil)
Production issues
When corona-treating films that are used as a sealing medium (normally PE or PP), it is very important to avoid reverse-side treatment. If there is a small air pocket between the film and the roller, corona can be formed in the air pocket, which leads to reverse-side treatment. If the film is reverse-treated, it will not be able to seal. The air pocket can be formed by wrinkles in the film caused by insufficient web tension or contact between the roller and film. The result is stripes appearing in the machine direction (MD) of the material where the surface tension is higher and, in the case of PE and PP, polar groups will appear at the film surface that prohibit good sealing properties.
This is the reason wetting plays a significant part in good quality lamination. Optimum wetting is dependent on the correct level of corona-discharge treatment; the viscosity of the adhesives used, both in solvent and solventless applications; and the nip temperature and pressure. Wetting failures are the result of one or a combination of these factors: a contaminated application or nip roller, an application weight that is too low, the adhesive having too high a viscosity (in solvent-free, it’s too low a temperature; in solvent-based, it’s too low a content of solvents), low roller pressure, nip roller temperature too low.
Lamination issues also occur when nip rollers are not parallel or if they are hollow. The rubber cylinder in the nip may be too soft; it can retain contaminants because it is not cleaned properly; and switching from a narrow to a wider web, or vice versa, can pose problems owing to the convex profile of the rollers. Regular cleaning and monitoring to assess the need for adjustment are critical to lamination quality.
What goes around comes around
All of which brings me to my final section of this paper – sustainability. I showed the example earlier of a typical, laminated coffee pack that consisted of three different films and multiple layers. Today, there is a pressing need to develop mono-materials that offer the same properties but also can be part of the circular economy.
This circular concept is based on recyclability and to achieve this there is a paramount need to collect flexible-packaging waste. According to the industry body CEFLEX, there are five basic steps to take: collection of all waste for sorting and recycling; sorting and recycling the mono-materials; redesigning packaging to use mono-materials where possible; identifying opportunities to sort and recycle the remaining waste; and identifying/developing end markets for the recycled material.
I mentioned mono-materials; for these, it is essential to apply the correct corona surface treatment as they often are made of PE or PP with natural low surface tension. This group of materials includes OPE/PE, OPE-print/PE, OPE barrier layer-print/PE, OPE-print/PE-EVOH-PE OPP/PP, OPP-print/PP, OPP barrier layer-print/PP and OPP-print/PP-EVOH-PP. Looking ahead, mono structures might include Print-OPE-plasma-coated barrier/PE and Print-OPP-plasma-coated barrier/PP.
Conclusion
Corona surface treatment plays a fundamental part in the processing of film substrates. For this reason, commonly used materials such as OPE, PE, OPP and PP should be treated in-line at the point of extrusion, and in the case of oriented films, given a corona refresh in-line with lamination. If you are using chemically treated, oriented films, a light corona refresh may be useful if the material has become contaminated but be very careful not to burn off the chemical coating. With unoriented films, like PE and PP, be careful to avoid reverse-side corona treatment.
Finally, as substrates become more complex and market demand changes, it is more important than ever to work closely with experts at all stages of production to ensure a top-quality end product. There is a wealth of knowledge and data available for you to tap into – why not use it?
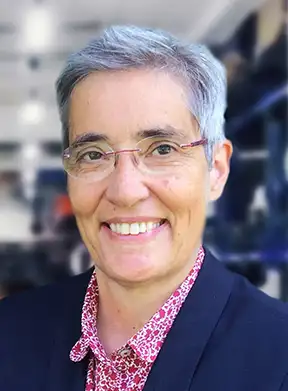
Kirsten Lykke, an independent consultant in polymers and flexible-packaging technology, holds a Master of Science in Chemical Engineering and has previously worked as a development manager for Amcor Flexibles. She also has been a technical account manager for Dow Chemical, where she was responsible for lamination adhesives, and worked as a senior manager for polymer technology at the LEGO Group. Kirsten established her own company in 2018 and provides converters and brand owners with services in developing sustainable packaging solutions, constructing optimum laminates for the packaging of a specific product; finding the root cause for a packaging failure; optimizing specific production processes and minimizing waste; specifying correct adhesive strategy for individual projects to gain cost savings; and setting up test programs and interpretating the results of physical and chemical analyses. She can be reached at +45-20-604051, email: kl@kirstenlykke.com or www.linkedin.com/in/kirstenlykke/.
More info: 312-803-3691, www.vetaphone.com