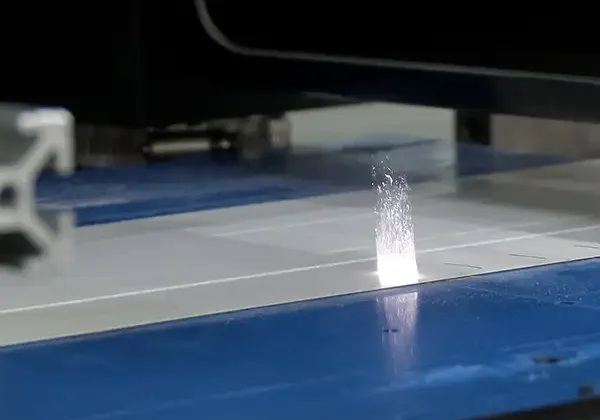
By Zach Haddock, regional sales mgr., Preco LLC
Few will argue the magnitude of the energy-storage gold rush that is happening right now. We are in a time where demand is pushing innovation harder than ever. The pressure to scale up from proof-of-concept to full-blown commercial production is immense and unyielding. In this article, we will look at some of the hurdles for taking these new battery technologies from proof-of-principal to mass production, and how old methods of material handling and device construction have been rethought or replaced to adapt for the demand, unique construction challenges and volume, without compromising precision.
Introduction
You would literally have to be living under a rock to be unaware of the electric-vehicle (EV) boom that is happening right now. Just 10 short years ago, seeing an electric vehicle on the road was a rarity, almost a spectacle. Now seeing a Tesla on the road is commonplace, and it’s not just Teslas. All the big players have launched EVs. Ford has the F150 Lightning and Mach E Mustang, Chevy is rolling out EV versions of its flagship models this year, and then there are newcomers like Rivian and Lucid Motors. As part of the US Infrastructure Investment and Job Act, $2.8 billion is being made available through grants to foster additional manufacturing capacity. It’s apparent that electric vehicles are here to stay.
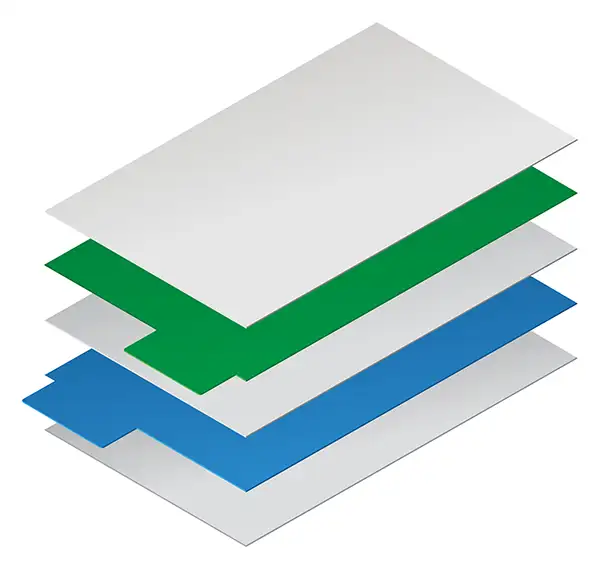
Initially, the biggest hurdle for general converting of EV-battery components is the sheer volume that is in demand. A typical mono cell consists of a cathode, an anode and a separator. A prismatic battery may contain 50 or more mono-cell sub-assemblies (see Figure 1). Additionally, that one mono cell is only a small fraction of the total battery assembly, as these vehicles need multiple batteries connected in series and parallel for the voltage and capacity required. The volumes of discrete components add up fast. Back to the Future’s Doc Brown and his 1.21 gigawatts seem almost laughable in these modern times.
The R2R battery-converting process
What does it take to convert these new materials and turn them into functional battery components? At the basic level, there are three components of a battery that need to be converted: a cathode, an anode and a separator. There are some very interesting, emerging designs that diverge from the traditional media but, for the most part, the cathode and anode components typically are coated, thin metal foils. Some of the coatings on these foils can be quite delicate and susceptible to moisture. They need to be processed in a dry environment. The separator materials usually are very thin polymer films or nonwovens. Cut geometries usually are simple but can require tight tolerances. The cathode and anode often will have a coating edge that needs to be registered to a tab profile that will be used to make the internal connections once the battery is assembled. The separators sometimes can require heat-staking or folding and sealing.
Because of the very thin and delicate nature of these materials, it’s often best to assemble them into a mono cell during the conversion process as handling them once singulated would prove difficult. Also to be considered are the efficiencies afforded of overlapping operations. While there are a multitude of cutting methods capable of converting most battery materials, some are simply too slow or non-compatible, such as plotter-knives and water-jet. Flatbed, rotary and laser, however, offer excellent throughput and tolerance capabilities. Each has its own advantages and challenges when it comes to converting for the energy-storage market.
Flatbed diecutting options
Flatbed diecutting typically offers the best dimensional-cut tolerances and can use a wider gamut of tooling options. Most common is the steel-rule die, but it’s also popular to run chem-etched dies, or Class A male/female dies. Dimensional tolerancing varies based on the type of tooling used, with steel-rule dies being the least expensive/lowest tolerance and matched metal dies being the most costly/highest tolerance. While chem-etch dies are relatively inexpensive and offer excellent dimensional tolerancing, they are limited by material thickness and have fewer options when it comes to blade profiles. Iron contamination can be a concern when converting for hydrogen fuel-cell applications. And with the limited ferrous contact area of a steel-rule die, this can be advantageous.
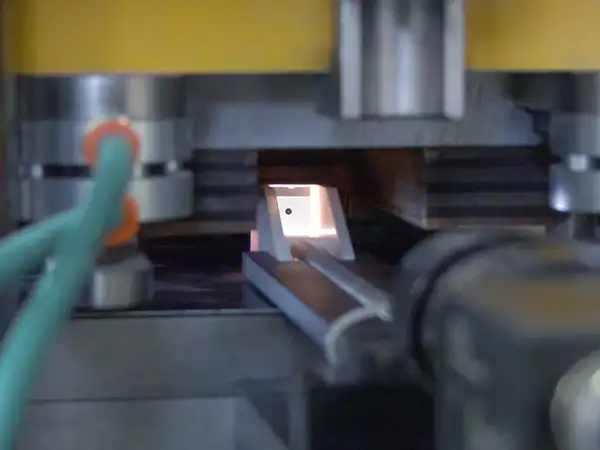
Most all electrodes will have a tab, which typically is an uncoated section or a welded addition where the internal contacts are made. This often means there is a need to register the die to either the coating or the welded tab. Because the material is stationary during cutting, the vision registration and registration verification on flatbed systems will offer the tightest tolerances when compared to rotary processing (see Figure 2). Typically, the foil and tab material and/or thickness will dictate the type of tooling used. If there is a welded tab, it’s not uncommon to use a matched metal die to ensure a burr-free edge.
Along with diecutting, flatbed presses also lend themselves well to heat-sealing and embossing or forming. As the entirety of the rule is in contact with the material during the downstroke, the active dwell time to seal is much higher than in a rotary application where the moment of contact is constrained by the tangent of the blade to the anvil. With some battery technologies requiring the mono cells to be pouched and sealed, this offers an advantage. Flatbed presses also can accommodate sheeted materials or roll-to-roll, which offers some versatility but, because they operate with intermittent motion, tend to have lower throughput than other methods of diecutting.
Benefits of rotary diecutting
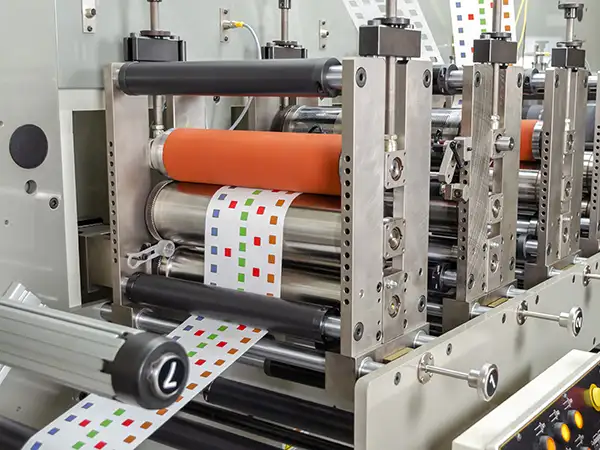
Rotary diecutting, on the other hand, typically is much faster than flatbed as it is designed for continuous motion and high throughput. It’s very easy to achieve cutting speeds that produce more singulated parts than can be collected. However, dimensional tolerances on the cut geometry tend to be lower, especially in the feed axis. This is, in part, due to the inconsistency in the feed rate of the material compared to the rotational speed of the die. Imagine the die is profiled with a perfectly round circle. Should the die be rotating slightly faster than the rate of the material, the circle becomes a short oval in the direction of feed. The inverse is true should the die be turning slightly slower. It’s nearly impossible to ensure a true one-to-one ratio between the die and the material feed, and if the die is making a registration move, this can compound the issue.
The continuous motion of a rotary system by nature means that it also is well suited for overlapping operations, such as lamination, slitting and island placements (see Figure 3). One of the drawbacks to flatbed cutting is that some amount of waste matrix often is needed to move the cut pieces out of the platen area, which leads to added waste and material cost.
With island placement, the parts can be cut very close together or with geometry allowing a cut with common rule and then spaced out onto a carrier material. This greatly reduces or even can eliminate waste. When looking at methods to construct mono cells in-line while converting, island placement becomes an asset. Cathodes and anodes can be cut and then island-placed into mono-cell stacks as part of a holistic operation. Opportunities for in-line coating processes also are a reality. Rotary processing, however, typically is limited to roll-to-roll processing and not usually well suited to sheetfed applications.
Versatile, accurate laser cutting
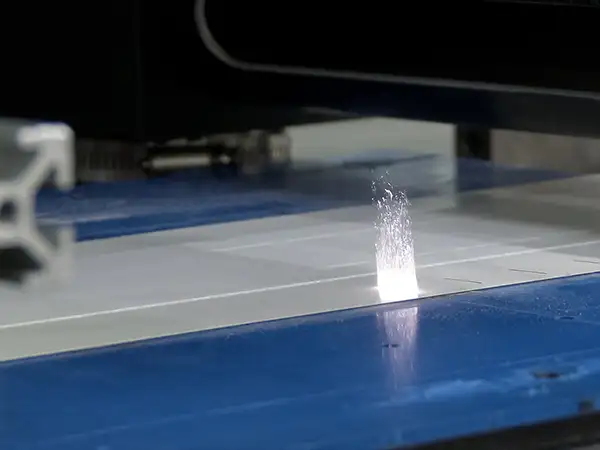
Laser cutting can offer extremely accurate dimensions and is capable of processing either sheets or roll-to-roll. Along with cutting, the laser is capable of sealing, ablating, welding or heat-treating. Lasers are unrivaled in their ability to create extremely small and complex cuts, as they are not bound by the physical constraints of a machined tool. The impossibly small features found in medical devices, such as heart stents and microfluidic devices, are all possible due to amplified and focused light.
However, there is a unique set of challenges with laser cutting that isn’t a consideration for hard-tool cutting. Because the laser is a single-point cut, the beam essentially must trace the cut pattern on the material. Therefore, speed can be slower, depending on the total linear inches needing to be cut – although, in some cases, it can be considerably faster. For example, long lineal with short cross-web patterns can be achieved with minimal beam direction. It should be noted though that one of the biggest determining factors for the cut speed of the laser is the material itself and the power of the laser. There can be heat-affected zones near the cut with a chance of contamination from debris caused by the vaporization of the material being cut by the laser (see Figure 4).
R2R, sheet or hybrid material handling
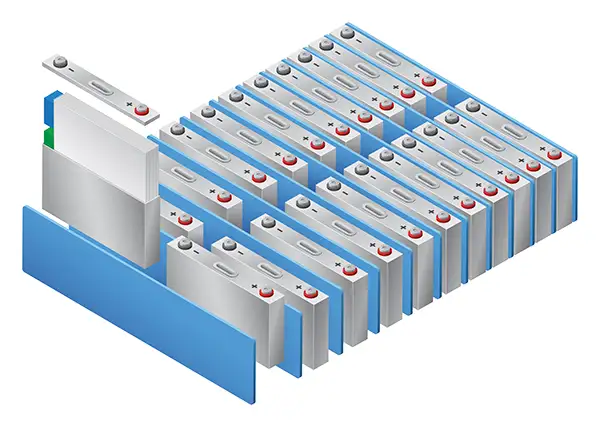
All things considered, roll-to-roll almost always is the preferred method of material handling for battery-component manufacturing. Roll-to-roll offers multiple advantages over sheet handling, such as easier placement, overall control and minimal handling labor. However, some designs simply cannot facilitate roll processing because of substrate availability. Physical limitations due to rigidity and/or coating integrity can be an issue.
To maximize capacity and maintain the often-stringent dimensional tolerance and processing requirements, we often have had to look toward hybrid systems. It’s becoming more and more common to incorporate flatbed diecutting into rotary and laser processing systems. This especially is true when heat-sealing is needed, as the dwell time necessary would slow down rotary sealing far too much. Laser processing is integrated easily into just about any core system and often is the only option available when features become very small or non-contact cutting is required for open-faced adhesives, for example (see Figure 5).
To summarize, Table 1 presents laser, rotary and flatbed diecutting methods and their preferences across various applications.
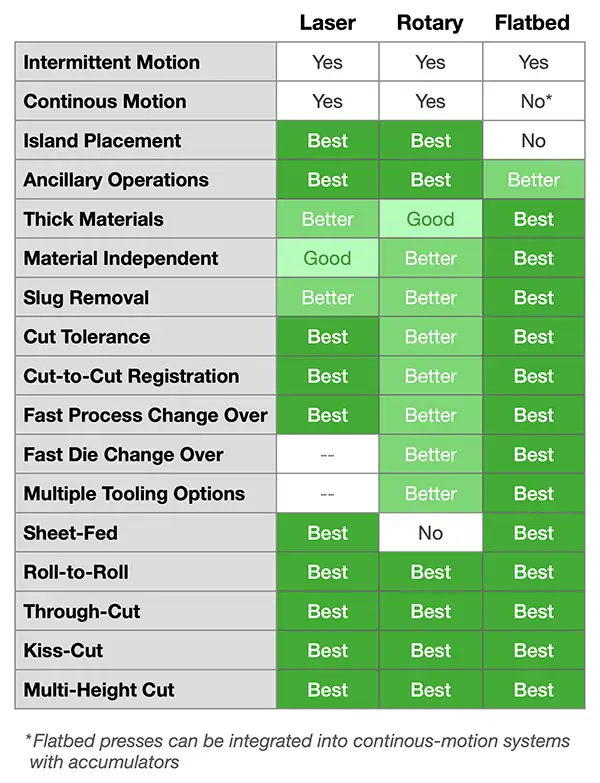
Conclusion
Is the gold rush for just electric-vehicle energy storage? The answer to that question is a resounding, “No.” The internal combustion engine is being phased out, or at least optioned out, at just about every level from homeowner lawn-care equipment to forklifts. Converting opportunities don’t stop at just the battery-components level, either. Hydrogen fuel cells have some unique but manageable converting challenges. Thermal-management and fire-mitigation components can offer some low-hanging fruit as well.
Energy storage and creation is an industry expanding at a rate not often seen for any business or technology. There’s enormous potential, and everyone from startups to the goliaths of industry are looking to take a piece of the pie.
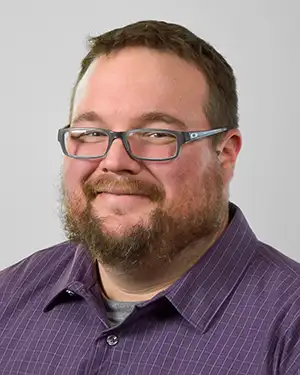
Zach Haddock, regional sales mgr. for Preco LLC (Lenexa, KS), holds a Bachelor’s degree from Pittsburg State University. Since 2007, he has worked on custom process solutions for Preco customers in the aerospace, medical, electronics and general converting industries. Zach regularly presents at tradeshows on topics such as diecutting and automation to reduce labor. He also shares his vast industry knowledge in his YouTube video series, “Tech Tips.” The lifelong Kansas native is a member of the International Assn. of Die Cutters and Die Makers tech team and serves as a subject-matter expert for diecutting plastics, metals and specialty materials. Zach can be reached at 913-541-0066, email: zhaddock@precollc.com, linkedin.com/in/zach-haddock/, youtube.com/user/precoinc, www.precollc.com.