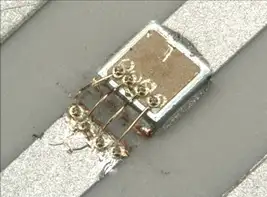
By Heidi Hoffman, senior dir.-SEMI Technology Communities Marketing, SEMI FlexTech
SEMI FlexTech has been championing business and technology development of the flexible, hybrid, printed and organic electronics sector for 20+ years as the industry expanded to more than US$50 billion, with significant growth on the way. Driven by demands in mobile phones, automotive, flexible power, IOT devices, e-textiles, displays, sensors and many niche applications, the small-size, lightweight, low-power attributes of these devices have been popular with electronics-system designers. SEMI FlexTech continues to provide technical education, networking events and marketing opportunities for its members, including its flagship FLEX Conference & Exhibition.
Introduction
For more than 20 years, SEMI FlexTech has been organizing the industry to advance the state-of-the-art in flexible, hybrid and printed electronics, a technology that promises to bring electronics out of their boxes and enable low-power, low-weight and more environmentally friendly products.
Environmentally friendly can mean many things. The products can reduce the electronics wastestream with more organic components, or they can be manufactured in a way that creates less waste or uses fewer chemicals that contribute to greenhouse-gas emissions. Flexible electronics has the potential to do both of these, with smaller packaging, organic earth-friendly components and most requiring much less electrical current to operate (Molex [1], SunRay Scientific [2]), thus enabling less caustic battery technology (Imprint Energy [3], Arieca [4], UCLA [5]). The research into novel materials, such as graphene, have led to its use in less caustic but stronger cement mixtures for large and small building projects (CHASM [6]).
Flexible electronics driving medtech innovation
The ability to have conformal electronics shines for the medical technology (MedTech) sector. SEMI FlexTech spun out the SEMI Nano-Bio Materials Consortium (NBMC) in 2013 [7], for identifying the gaps in medical monitoring and augmentation. SEMI NBMC focuses on innovation challenges and opportunities during research and development (R&D) to increase the technology and manufacturing readiness levels (TRL/MRL) of nanotechnologies and biotechnologies.
Over the past two years, SEMI NBMC has funded projects in wireless, interstitial (under the skin) fluid-monitoring devices (GE Research [8] and Binghamton [9]), multi-sensor systems for physio-cognitive states (Georgia Tech [10]) and many other medical-sensor projects [11].
SEMI FlexTech funded-projects focus
Technically, SEMI FlexTech continues to fund the following technology-development projects in the Technology Readiness Levels (TRLs) 2-5 areas:
- FHE power and power integration
- Reliability as it applies to FHE
- Electronics environmental sustainability for FHE
- Heterogeneous packaging for FHE
- Advanced materials for encapsulation, printing and conductors
Projects currently underway include one on additively manufactured, flexible smart packaging for antenna arrays for 5G system-on-package designs with Georgia Tech. Soft robotics are areas of keen interest, including the development of a haptic-response glove to augment human activity with Worcester Polytechnic Institute [12]. Hewlett Packard Labs [13] is leading a project on 3D printing with a multi-jet fusion process. GE Global Research is creating a soft, electronic robotic worm for remote maintenance of difficult-to-reach spaces.
Low-temperature processes are very attractive to use the best flexible materials, and SEMI FlexTech is working with ACI Materials to create inks and pastes sinterable at high film thickness and low temperature.
The SEMI NBMC and SEMI FlexTech rely on teams of members and industry experts to identify the technical gaps and project proposals that stand the best chance of filling them. Both groups will be holding “Gap Analysis” workshops in January 2023 for anticipated requests for new proposals shortly thereafter. Industry attendees are welcome to contribute to the workshops and invitations will be sent to the mailing lists [14] (see Figure 1).
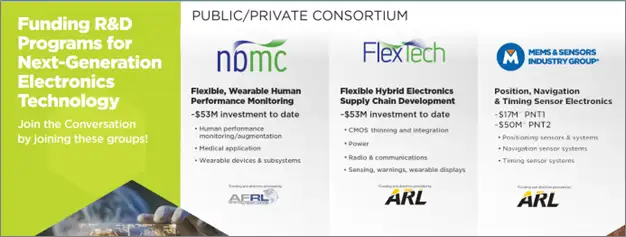
Network to collaborate
SEMI FlexTech believes key to technology advancement is collaboration, especially in the multi-faceted space of heterogeneous integration of flexible-electronics packaging. Many of the pieces’ fundamental building blocks of the technology are available, and the challenge lies in solving the integration and reliability questions. That expertise lies in many adjacent, and some completely disparate and unfamiliar, sectors which speak a different technical language. FlexTech provides a platform for them to gather and create a common understanding of capabilities.
Printing accuracy and interconnect of printed electronics with a semiconductor continue to provide the greatest challenges to flexible-electronics manufacturers. Thin, flexible substrates, bare die, and combinations of printed and small-format packaged components require the use of additive processes for circuitization, mechanical attach and encapsulation.
Additive techniques, such as printing with a master (e.g., screen, gravure) or direct-write (e.g., inkjet, aerosol jet, extrusion), are used to deposit conductors, insulators, adhesives and other materials precisely to connect and attach electronic components onto flexible substrates, and the materials can be cured (e.g., thermal, IR, UV, photonic) without the need for extended exposure to high temperatures.
Industry participants have been working to apply these novel interconnect-and-attach techniques to advanced packaging applications, in which the ability to precisely apply specific materials under controlled conditions enables more compact, lightweight and higher-performance microelectronic systems. While these techniques are not yet in volume production, presentations at FLEX 2022 indicated intriguing possibilities.
For example, Binghamton University reported on direct-write for selective deposition and patterning of both dielectric and conductive materials in a multilayer fashion to create high-resolution, 3D circuit elements for millimeter-wave electronics. An Optomec [15] aerosol-jet system was used in conjunction with conventional low-k substrates and etched copper-foil circuitry. Compared to wire bonds, the use of printed connections showed similar RF and electrical performance in a simpler and more compact package (see Figure 2). In addition, the use of aerosol-jet deposition allowed for the fabrication of 3D-antenna structures.
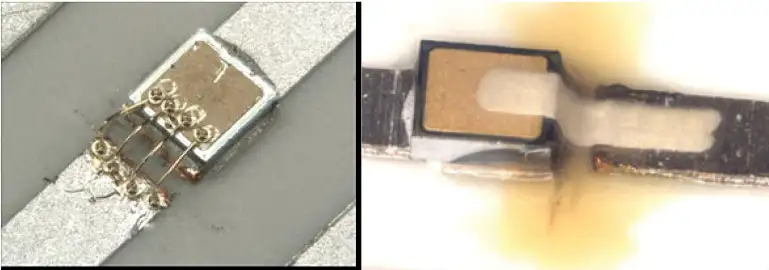
Materials & processing challenges
SEMI FlexTech funds projects at the discretion of the US Army Research Laboratories (ARL). At FLEX 2022, Eric Forsythe, program manager at ARL and NextFlex, the Flexible Hybrid Electronics Manufacturing Institute, categorized the challenges for materials for 3D hybrid electronics as ensuring a domestic supply chain, reduction in the space and weight of the package and account for the unique Dept. of Defense environments which call for high-forces and thermal stresses. Building the material science for these environments is key, particularly in molding high-temperature polymers and creating reliable interconnects with stable overmolding compounds. Forsythe notes that all of these applications have important commercial counterparts.
Convergence of FHE techniques and advanced packaging
Another SEMI FlexTech spin off, NextFlex [16], discussed the relationship between FHE and packaging, pointing out ways in which FHE can lead to integration and elimination of the distinction between package, PCB and system (see Figure 3). While hybrid-electronics approaches enable things including additive printing of circuits and multichip modules, structural electronics enable circuits on and within parts, non-planar surfaces and 3D structures.
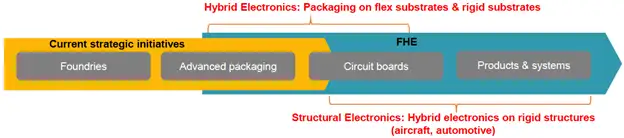
Hybrid packaging includes the combination of additive-deposition techniques, chips and substrates/board materials. NextFlex presented application examples for these novel packaging approaches, including wearables and textiles, conformal monitors and active shipping labels. Future component technologies used in hybrid packaging could include embedded fluidics, MEMS integration and photonics/optoelectronics.
FHE is a hybrid technology and much of the requisite material and manufacturing expertise and capability exist or relatively easily could be adapted to the needs of the manufacturers. IDTechEx notes that “from a business perspective, one of the largest challenges for FHE is the low-cost functionality – such as RFID sensors for smart packaging and industrial monitoring – is possible only with large-volume production, which necessarily requires a substantial upfront investment. Another challenge is that creating a complete product that adds value to the end user requires collaboration between many different suppliers, all with complementary technologies and expertise.” (See related article on page 36).
As demand grows, we believe this is another hurdle that will fall – and it could fall very quietly, benefiting only those already aware of the opportunities available.
References
- www.molex.com/molex/home
- https://sunrayscientific.com
- www.imprintenergy.com
- https://arieca.com
- https://chips.ucla.edu
- www.chasmtek.com
- www.semi.org/en/communities/nbmc/projects
- www.ge.com/research/
- www.binghamton.edu
- https://coe.gatech.edu
- www.semi.org/en/communities/nbmc/projects
- www.wpi.edu
- www.hp.com/us-en/hp-labs/research/overview.html
- https://discover.semi.org/technology-communities-subscription-registration.html
- https://optomec.com
- www.nextflex.us
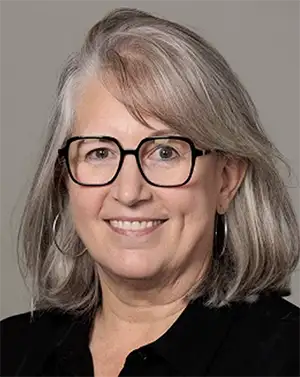
Heidi Hoffman, senior dir.-SEMI Technology Communities Marketing at SEMI FlexTech (Milpitas, CA), has been following the flexible, printed, hybrid and organic industry for more than 20 years. She provides market research and communications strategies for all SEMI TCs, including MEMS & Sensors (MSIG), Electronic Materials Group (EMG), SOI Industry Consortium (SOIIC) and more. Heidi can be reached at email: hhoffman@semi.org or www.semi.org.
More info: flextech@semi.org, www.flextech.org