
By Eldridge Mount, consulting technical editor
This article will discuss film treatment and the many mysteries that can be found in film-surface treatment production, testing and end uses. In this article, “treatment” will be an oxidative process applied to the film surface by a corona, flame or atmospheric plasma. “Wet” oxidative processes will be ignored for the purposes of this article.
Introduction
For the first nine to 11 years of my work in industry, film surface treatment was no mystery to me, because I had no direct exposure to it. At first, I was a synthetic organic chemist (which ultimately helped me understand surface treatment), followed by four years in graduate school studying polymer extrusion melting. Even when I went to ICI Americas to make oriented polyester films (OPET), it was no mystery, because we did not “treat” the OPET film surface at that time. Rather, an in-line adhesion primer was added by coating the film in-line, i.e. between the machine direction orienter (MDO) and the transverse direction orienter (TDO). Even when I started at Mobil Films developing oriented polypropylene (OPP) films, my first product was an untreated shrink film.
I started to be aware of the OPP surface treatment mysteries from my Mobil coworkers who always were complaining about, and working around, treatment and treater problems. It wasn’t until I began work on more traditional and metallized OPP products that the mysteries presented themselves directly to me. In the ensuing years, I came to the conclusion that, regardless of the OPP surface-treatment method employed, many of the mysteries were due to the basic treatment process mechanisms acting on various polymer surfaces and poor process control.
What is OPP surface treatment?
From here on, I will focus on OPP surface treatment as I know it. So, what does OPP surface treatment do and how many ways are there to do “treatment”?
In general terms, treatment adds oxygen to a film surface to improve wettability and, hopefully, adhesion, to inks, coatings, adhesives, evaporated aluminum and other chemical treatments applied to the film surface. The oxidation can be carried out by an electric corona, a flame (thermal corona) or an atmospheric plasma treater. In particular, flame and corona treatment generally rely on a plasma of ionized atmospheric oxygen in atmospheric nitrogen gas. Atmospheric plasma treatment can use helium [1] or nitrogen or a nitrogen/carbon dioxide blend [2] as the ionizing gas to activate the polymer surface, which then reacts with atmospheric oxygen to attack and oxidize the film surface. In the end, the result is a treated polymer surface containing oxygen.
An alternative to surface treatment would be to directly coextrude a film surface containing various oxygen containing polymers, such as EVOH [3], EVA, PVA, PET [4], Nylon [5] or other oxygen-containing polymers to replace the reactive film surface modification. Coextrusion of these various polymers could be more expensive than coex OPP and more difficult than the “simple” in-line corona, flame or atmospheric plasma treatment processes.
The “right” treatment level
This is where the mysteries begin. Each of the treatment processes give different surface energy outcomes, because the oxidation mechanisms are different. OPP treatment results also depend strongly on the polymer of the film surface, such as homopolymer PP, copolymer PP or HDPE. Corona treatment is widely believed to oxidize the surface with ozone generated in the corona. Flame treatment is believed to use excited oxygen atoms to oxidize the surface. Plasma treatment is thought to ionize the film surface directly, using excited nitrogen or helium atoms, which then react with atmospheric oxygen molecules, diffusing to the film surface to oxidize the film surface.
So… three surface oxidation mechanisms, which yield similar, but different surface chemical outcomes, i.e., different film surface chemistries. The actual chemistry of the film surface can be determined by Electron Spectroscopy for Chemical Analysis (ESCA), now generally called XPS (X-ray photoelectron spectroscopy). This technology goes a long way to help clear up some of the mysteries as we will see.
One of the big mysteries is: What is the “right” treatment level? Treatment level is measured in surface-energy units of dynes/cm (often shortened to “dynes”) by testing the wetting of a series of formamide/ethyl cellosolve solutions. This is used to determine the “wettability” of the film surface between 30 and 56 dynes/cm, using ASTM D 2578-04a “Wetting tension of polyethylene and polypropylene films.” Of course, the first mystery is determining the right treatment level that is needed. The ASTM standard simply says 35 dynes/cm or higher generally is okay for flexographic printing of type 1 blown PE films, but that other film types, processes and end uses may have their own “acceptable” dyne level for acceptable film wetting performance. Not much help there.
Treatment level in production must be correlated with actual film performance in the application, which keeps the engineers busy. Also, wettability does not guarantee ink, coating, adhesive or metal adhesion, i.e., higher dyne levels do not necessarily translate to improved adhesion of the treated surface. Indeed, higher treatment levels may lead to degraded polymer surfaces and lower adhesion.
Surface treatment loss
Once the proper treatment level in production is identified, we’re all set. But wait! Mysteriously, it seems that treatment can “disappear” with time. What is that about, and how does it happen? There are two, maybe three, main mechanisms for treatment loss with time.
- First is that the high energy surface in air can rearrange such that the oxygen groups existing on the surface diffuse, or rotate, into the film surface to lower the surface free energy of the film. This can be reversed by soaking the film in water where, with time, they diffuse back to the surface to minimize the free energy difference of the water and film surface.
- The treated film surface is covered by low-molecular-weight polymer or additives in the film, covering the surface, while wound in a roll.
- The treatment may have degraded the film surface such that highly oxygenated, low-molecular-weight polymer is rubbed off onto process rolls. This generally is found in highly or “overtreated” films.
Point 1 always will lead to an apparent loss in measured dyne level with time, but usually to a limiting value. Point 2 is well demonstrated by treated films containing silicon oils, used to lubricate the film surfaces for high-speed packaging applications [6]. In this instance, it is not possible to treat a film surface containing silicon oils without destroying the lubricity of the silicon oil, so only one side is formulated to contain the oil. Then the surface free of oil is treated in-line and wound into rolls on the orienter. Treatment conformation and level are measured by taking a sample directly from the film line before winding into a roll. But, on taking a sample from a wound or slit roll, the film surface will show no treatment until washed with a solvent, i.e., the treated surface has been “contaminated” by transfer of the oil from the untreated surface. This surface “contamination” also can occur in roll form with films containing migratory additives or low-molecular-weight polymer species formed during film processing or originating in the polymers of the core or surface polymers.
In my experience, surface contamination by film additives or polymer degradation is the main source of apparent treatment loss. The silicon-additive films’ silicon oil transfer is the clearest demonstration of this cross-surface contamination to cover, or hide, surface treatment. So, in general, treatment loss in films with migrating additives or degraded polymer (high levels or poor-quality reclaim) will show a treatment loss by treated surface contamination.
With highly treated films (Point 3), there sometimes is a deposit that forms on rollers downstream from the treater. This can be called treater dust. When it is collected and analyzed, it is found to be highly oxidized polypropylene oligomers, i.e., degraded surface polymer. Here, treatment is lost by the mechanical loss of oxidized surface polymer. This oftentimes is associated with poor adhesion due to a weak surface layer on the film.
Backside treatment
Another treatment mystery is how patches of treatment can appear on the untreated surface. This is called “backside treatment,” and it typically is found on corona-treated films. In general, it causes pinpoint blocking and web tears in slitting. It oftentimes is associated with a “hissing” sound during unwinding. In printed or metallized products, it can cause ink and metal pickoff, making the converted product unusable. If severe in heat-sealable films, it can raise the minimum heat-sealing temperature (MST). In our Connecticut plant, I watched Frank argue with customers, sales and the plant about this film defect while he was developing new films and, in particular, a metallized film. Many times, it was about the only thing wrong with the film.
Backside treatment is formed when there is air trapped behind the film during corona treatment. Corona treaters create a high-voltage electric field between the treater bar and the treater-roll surface, which ionizes the air and creates ozone and electrons, which then causes the film surface to oxidize. If there is air trapped behind the film on the treater roll surface, it also is ionized in the electric field and treats the back of the film. It can be difficult to prevent air behind the film – especially if the film is not nipped on the treater roll, if the nip pressure is too low, if the nip pressure is too high (bows the roll) or if the nip or roll surfaces are damaged.
Backside treatment is not found with flame treatment because the air in the treater gap is ionized by high flame temperatures, which don’t exist behind the film. That is why, after watching poor Frank, I installed flame treaters on the lines I was developing metallized films on. Atmospheric plasma treaters using helium also don’t cause backside treatment because the helium is ionized for treating the film at a lower voltage than is required to ionize atmospheric gasses. With no source of helium behind the film, there can be no backside treatment.
Identifying surface chemistry
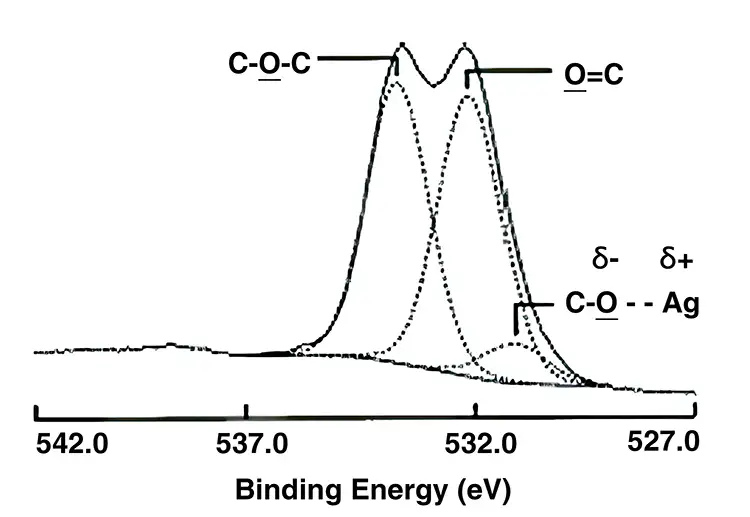
Another big treatment mystery can be found in determining the surface chemistry of a treated surface. We know it has added oxygen on the surface of the film, but what is the chemistry of the added oxygen? How does the oxygen level and surface chemistry affect the treatment level?
Here is where X-ray photoelectron spectroscopy (XPS) is important. XPS allows the identification of the amount of surface atoms, as well as giving information about their bonding to the carbon of the polymer chains. Figure 1 shows a high-resolution XPS spectra of a film surface in the area of the oxygen-carbon bond energy. From these measurements, the percentage of oxygen on the surface can be calculated. With the high-resolution scan shown, the functionality of the C-O bonds also can be quantified. This data is important in correlating film performance with treatment level and type. Figure 2 shows a comparison graph of treatment level and percentage surface oxygen for flame and corona treatment of homopolymer polypropylene. The slope of the treatment vs. surface oxygen is notably different for flame vs. corona treatment. It is notable that flame treatment gives higher treatment levels for lower percentages of surface oxygen.
Armed with the knowledge from literature searches and the many experimental treatment studies of my coworkers and myself, I believe the difference in wettability vs. oxygen level is due to differences in the surface chemistry. Specifically, flame treatment results in a higher surface concentration of hydroxyl (alcohol) functional groups than corona treatments, predominantly ketone, aldehyde and carboxylic acid end chains; i.e., better wettability primarily is due to a higher percentage of C-OH groups (water-like) for flame treatment vs. a higher percentage of C=O, -HC=O and C-OOH groups for corona treatment, as determined by XPS.
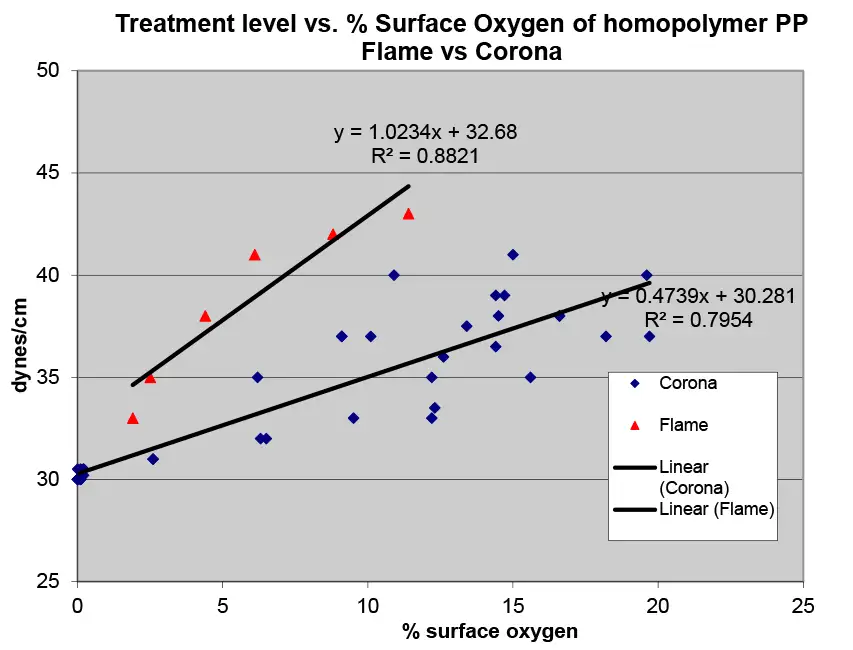
Knowing that a coextruded EVOH skin is expensive to produce but gives superior metallized barrier properties [3], and understanding flame treatment’s predominant HC-OH functionalization, we suddenly arrive at the invention of flame-treated HDPE metallizing skin [7]. Flame-treated HDPE, like metallized OPP films, produce a film with the moisture barrier of a metallized EVOH skin and an oxygen barrier between those of metallized OPP and metallized PET [8]. This is a perfect barrier profile for many snack packaging applications as it extends shelf life and is economical to manufacture, and it’s all due to understanding one of the many treatment mysteries.
It was found that the disparity in slope of flame vs. corona of the treatment level vs. surface oxygen are different for a wide range of common coextruded OPP surface polymers, except for the notable exception of coex films containing a propylene butylene copolymer (PB copolymer) skin. With PB copolymer, the slopes of flame and corona treatment vs. surface-oxygen level were found to be identical. This solved a mystery for me – that corona-treated PB coex metallized surfaces gave oxygen-barrier values comparable to flame-treated HDPE metallized films.
I left Mobil before I could complete my treatment studies of the surface chemistry of flame- and corona-treated surfaces, so I can only hypothesize that the ethyl side groups (CH2-CH3) of the PB copolymer were converted to CH2-CH2OH groups, giving comparable performance of the CHOH groups of flame-treated HDPE. It is my hypothesis that it is the alcohol (OH) groups that are the source of the high moisture- and oxygen-barrier [9] of flame-treated metallized HDPE. This is borne out by the superior barrier performance of metallized EVOH coextruded films. EVOH essentially is a highly hydroxylated HDPE. The higher the OH concentration along the HDPE chain, the better the moisture and oxygen barrier of the metallized film. Flame-treated HDPE surfaces are, in essence, producing a low vinyl alcohol copolymer surface. A lot of this is discussed in my 2023 Q1 Converting Quarterly article, “Metallized film barrier: Where does it come from?”
Conclusion
Recognizing the difference of treatment process mechanism, between flame, corona or atmospheric plasma, is the first step to understanding the mystery of surface functionalization of polymer films. While not discussed here in much detail, atmospheric plasma treatment is best understood as a “cold flame,” in my mind. Adding to that the understanding that treatment decay has several mechanisms, from surface contamination to surface diffusion of surface functional groups, should aid in demystifying treatment.
Treatment type and level must be correlated with film performance in converting and end uses. Once these correlations are discovered and developed for a film product, process control must be used to ensure the film’s Fitness for Use in the final application. This will take the form of controlling Watt Density in corona-treated films, and the Air Gas ratio and mixture flow rate for a specific treater/film gap in flame treatment, i.e., treatment power levels. Atmospheric plasma treaters have been an emerging technology over the last 20 years or so. They are a bit of a continuing mystery to me as I have not used one since 2000, but they will have key process controls somewhere between corona and flame treaters.
While I personally prefer flame treatment, it does not always give the best product performance in some film structures and applications, which still is a mystery to me.
Resources
- Chi-Ming Chan, Polymer Surface Modification and Characterization, Hanser/Gardner Publications Inc., Cincinnati, Ohio, 1994
- Rory A. Wolf, Plastic Surface Modification: Surface Treatment and Adhesion, Hanser Publications, Cincinnati Ohio, 2010
- Sina Ebnesajjad, Surface Treatment of Materials for Adhesion Bonding, Plastics Design Library, William Andrews Publishing, Norwich NY, 2006
References
- Yializis et al., U.S. Patent 6,441,553, “Electrode for Glow-Discharge Atmospheric-Pressure Plasma Treatment,” Sigma Technologies International, Aug. 27, 2002
- Deguchi, et al., U.S. Patent 4,297,187, “Surface Treatment of Plastic Material,” Toray Industries, October 27, 1981
- Migliorini, R.A., U.S. Patent 5,153,074, “Metallized Film Combination,” Mobil Oil Corporation, October 6, 1992
- Mount, E.M., Benedict, A.J.; European Patent 444340; “Metallisable Heat-Sealable, Oriented Polypropylene Film – Has Layer of Co-polyester To Improve Bonding To Metal”; (1991)
- Migliorini, R.A., Mount III, E.M., U.S. Patent 5,591,520, “Multilayer film with metallized layer,” Mobil Oil Corporation, October 25, 1991
- Balloni, R, et al., U.S. Patent 4,764,425, “Oriented, Heat Sealable Multi-Layered Film,” Mobil Oil Corporation, Aug. 16, 1988
- Migliorini, R.A., Mount III, E.M., U.S. Patent 5,1943,318, “High Barrier Film,” Mobil Oil Corporation, April 28, 1995
- Mount III, Eldridge, M., Wagner, John R., “Aroma, Oxygen and Moisture Barrier Behavior of Coated and Vacuum Coated OPP Films for Packaging,” J. Plastic Film & Sheeting, V17(July), 2001, pp 221-237.
- Mount III, Eldridge M., Wagner, John R., US Patent 5,981,079, Issued Nov 9, 1999, “Enhanced Barrier Vacuum Metallized Films”

Eldridge M. Mount III, president of EMMOUNT Technologies LLC (Canandaigua, NY), has 40+ years of industrial experience in the extrusion and orientation of polypropylene and polyester films at ExxonMobil Chemical and ICI Americas Film Divs. He holds a Ph.D. in Chemical Engineering from Rensselear Polytechnic Institute. Eldridge writes the “Substrate Secrets” Q&A column for this publication. He can be reached at 585-943-2250, email: emmount@msn.com, www.emmount-technologies.com.