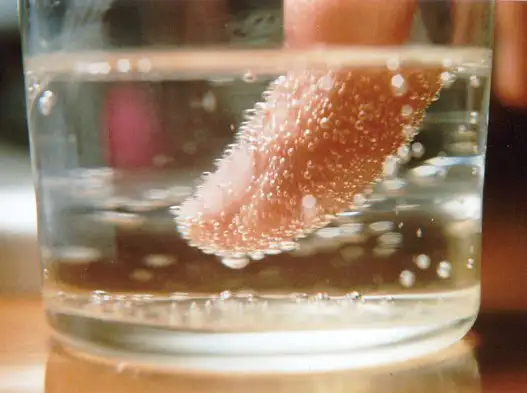
By Robert Malay, Ph,D., technical mgr., VDI LLC
With more and more devices being able to communicate to the larger environment, there is a desire for aesthetically pleasing films with a metallized look that do not block or attenuate signal from commonly used communications frequencies. This work investigates the use of various metal coatings using specific nucleation mechanics to achieve overall higher dielectric coefficients. The propagation of Volmer-Weber nucleation in sputtered coatings allows for discontinuous growth, leading to high resistance while maintaining the optical properties of the metal. The result is a purely sputtered film with a metallic look that retains high dielectric properties and allows for radio-frequency (RF) signals to pass through without attenuation. This type of coating can be used for applications such as hiding external sensors for self-driving cars, window tinting that does not interfere with cellphone signals, or packaging that is microwaveable.
Editor’s Note: This technical paper is based on the author’s presentation from the 2022 AIMCAL R2R USA Conference held Oct. 25-29 in Orlando, FL.
Introduction
The internet of things (IOT) is here. Numerous devices out in the market now are interconnected in a way that seemed like fantasy even 10 years ago. Smart home hubs allow for interconnectivity with myriad devices, and the development of smart vehicles allows for communication between people on the road. Devices connected in this way have become the norm.
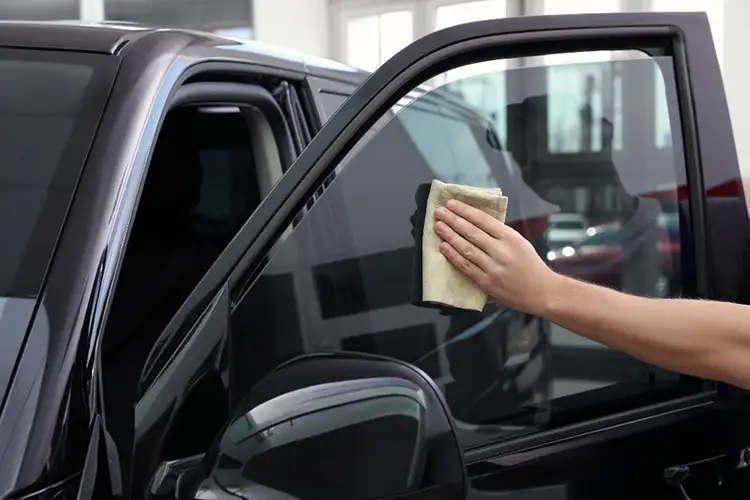
As more and more devices are integrated into the IOT, the demand for metallized film that does not attenuate signals grows. While 5G signals provide extremely fast communication, upload and download speeds, they easily are blocked (attenuated) by more common objects. Buildings, large metal structures such as bridges, and even trees with thick enough canopies can cause a reduction in signal strength. Even traditional aluminum-metallized window tint can cause a substantial reduction in transmitted signal (see Figure 1). Prior generations’ frequencies for telecommunications were at wavelengths long enough to not be affected.
Metallized films and components have become integrated into many different applications, many of which are not just limited to reflective surfaces or aesthetics. Many automakers now incorporate metallized film into vehicle bodies. These films serve as insulation, preventing a large portion of the heat generated from the engine from reaching the cabin, thus bringing the power draw of the AC down. Metallized film also is being used in self-driving cars. To effectively communicate with other vehicles, sensors must be placed on the outside of the vehicle, and hiding them with reflective, thermoformed pieces is the desired route.
Due to the higher frequency of 5G, metallized film attenuates a great deal more of the signal than previous generations of communication bands. Up to 90% of the signal can be blocked, depending on the resistance of the deposited metal. One proposed method of providing the desired products is the use of specific nucleation mechanics to control the resistance of the sputtered film.
Background on nucleation
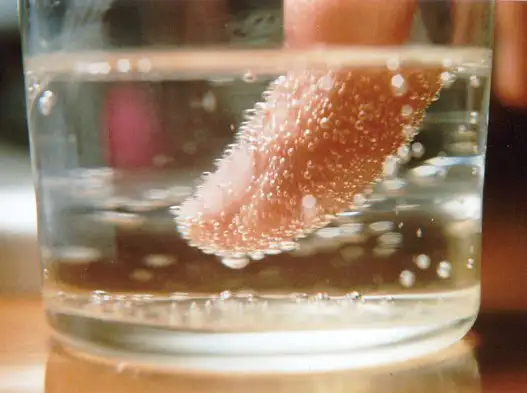
The nucleation of sputtered films dictates a number of film properties, including adhesion, crystallinity and electrical resistance (see Figure 2). There are three primary growth mechanisms for sputtered films. Frank-Van der Merwe growth refers to layer-by-layer growth and occurs when the surface energy of the substrate is much greater than that of the internal forces of the deposited material. The impinging adatoms will preferentially diffuse across the surface of the substrate to fill vacancies before adhering to other nucleating species and building thickness.
Volmer-Weber nucleation commonly is referred as island growth. It occurs when the cohesive forces of the material being deposited are greater than the surface energy of the substrate. The adatoms agglomerate into discreet segments and form a connected film only after growth causes them to come into contact.
Stranski-Krastanov growth is a hybrid between the other two mechanisms and occurs when the surface energy of the substrate and the cohesive forces of the target material are approximately equal. Pockets of island growth occur, but there also is sufficient mobility along the surface of the substrate to create thin layers between islands. Figure 3 demonstrates the three different nucleation modes.
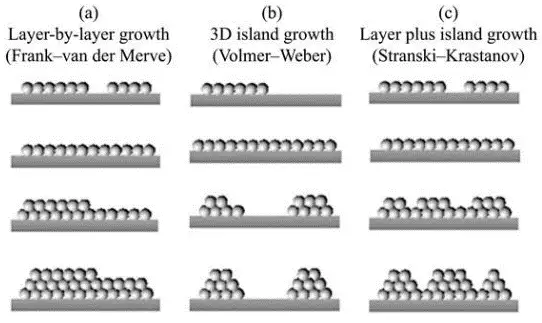
Volmer-Weber growth particularly is suited to generating thin films with a metallic appearance but yet having a high enough resistance as to prevent attenuation of radio frequency (RF) signals. The discreet islands prevent macro-scale conduction and give the film dielectric properties over longer distances (mm range and greater). By determining which variables control the island growth and preventing agglomeration of the islands, controlled depositions can be performed at significant optical densities (>1.0) that still retain RF transparency. The focus of this work was to determine the feasibility of facilitating Volmer-Weber growth in an attempt to repeatedly generate these films.
Materials
One of the primary factors in controlling the growth mechanism of the deposited thin film is the alteration of the substrate’s surface energy. This is a chief reason plasma treatment is used during vacuum-coating processes to increase the surface energy of the web. Argon and oxygen plasmas can create dangling oxide bonds which readily bond to the adhering adatoms in a plasma. This facilitates Frank-Van der Merwe nucleation and results in more uniform films with better adhesion to the substrate.
A proposed method of decreasing the surface energy of the substrate without losing adhesive properties is to use divalent zinc as an initial seed layer. It’s been shown that when deposited in-situ with other subsequent layers, zinc retains its divalency, which allows for lower surface energy. This process requires sequential depositions under vacuum, as exposure to atmosphere and oxidation of the zinc reduces effectiveness of this method. With this in mind, sequential roll-to-roll (R2R) sputtering systems with multiple deposition modules are well-suited for this.
The zinc layer discussed above would serve as the seed layer for an intermediary film that already is prone to Volmer-Weber nucleation. This intermediary film would provide a large portion of the coating thickness. In addition, this film would enable the RF-transparent behavior through the discreet islands, being non-conductive over distances greater than 1 mm (the lower end of the range for wavelengths in the radio regime).
After the intermediary layer, a third layer would be applied, which would provide the general optical properties needed for the product. Ideally, this third film will grow preferentially on the islands generated by the second layer. It is expected that at a certain deposition thickness, regardless of the island growth facilitated, agglomeration will occur, and conductivity will be realized by a uniform film.
Experimental Setup
The experiment was performed using a 500-mm-wide, R2R sputter coater built by Intellivation LLC. The system is equipped with four independent sputtering zones, as well as in-line optical-density and sheet-resistance monitoring. The experiment was set up as a multi-level factorial design using the thickness of the deposited layers as variables. Deposition thicknesses were calibrated independently, and samples were generated in random order.
Two levels of zinc were chosen to determine the effect of the zinc thickness, and five levels of aluminum-deposition thickness were used. The intermediary layer was kept constant, as the focus was on the effect of the zinc on the resistance of the sample and the optical properties obtained from the varying thicknesses of aluminum. Aluminum also was used as a control to determine behavioral change compared to the hybrid films.
Results and Discussion
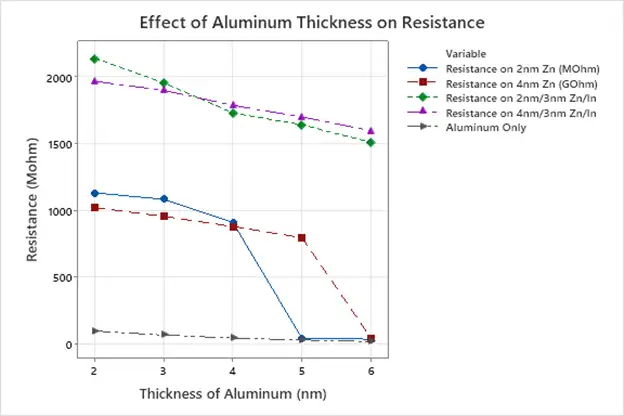
It was found that the zinc layer, regardless of the thickness, will propagate higher resistance in sputtered films. As can be seen in Figure 4, the resistance of only aluminum deposited is extremely low and remains low for each deposition level. This is indicative of a continuous film, which allows current to move through the metal as normally deposited.
This can be contrasted with the depositions done on top of 2 nm and 4 nm of zinc. The initial resistance is orders of magnitude greater than that of the single aluminum layer, despite being an overall thicker deposition. The reason for this can be attributed to facilitated Volmer-Weber growth in the aluminum film by the zinc film, preventing continuity of the coating at the thicknesses present. At 5 nm of aluminum deposition, it can be seen that the resistance drops significantly for 2 nm of zinc and drops at the 6-nm level for the 4 nm of zinc. This can be attributed to the agglomeration of the film. The islands had grown to the point where they fuse and form a continuous film.
The effect is compounded with the addition of a Volmer-Weber-prone intermediary layer. The initial resistances are even greater than that of the bilayer structure. The intermediary layer postpones the agglomeration of the films as well, which is seen by the lack of a drop-off in resistance as the aluminum thickens. It can be assumed that if thickness were to continue to increase in the aluminum layer, the structure eventually would fuse and become continuous.
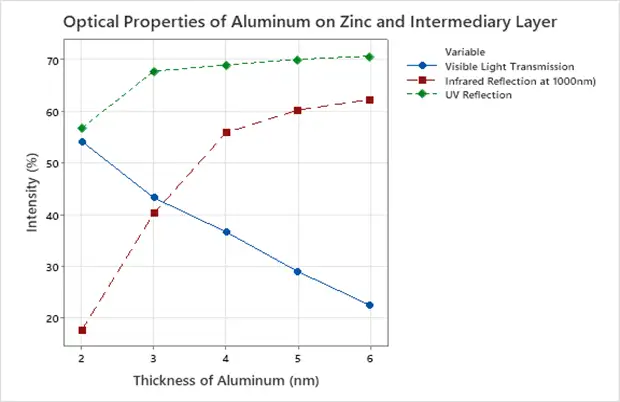
The optical properties for films generated in this manner can be seen to have similar properties to those of single-layer films. Figure 5 shows the visible light transmission, infrared reflection at 1,000 nm and ultraviolet reflection of the 4-nm zinc sample with the intermediary layer. From the figure, optical properties desirable in window films can be achieved with the proposed film stack. The decrease in visible light transmission from 55% to 25% shows a wide range of capabilities, allowing for various densities being deposited. The increasing infrared reflection also increases, which is critical to solar-control films that advertise heat reduction and rejection.
Conclusion and Future Work
The addition of a zinc seed layer and an intermediary film has a large effect on the resistance of a measured stack, which can be attributed to Volmer-Weber nucleation of the sputtered films. Continuous films eventually are achieved through the agglomeration of the film at increasing thicknesses, which can be seen in the significant decrease in resistance in the samples with a zinc seed layer. Stacks with optical properties similar to that of current window films have been achieved.
Future work includes further analysis of the nucleation mechanics and an understanding of the structures at various stages of growth. Additional material will be investigated to determine feasibility as seed layers and intermediary films. Optimization of the stacks will be done to realize opaque films that retain RF transparency for use in thermoformed and decorative applications. More robust RF testing will be performed on all samples to quantify attenuation of signals.
References
- Source: Lacivita, B. (2022, April 12).“How to tint car windows.” Family Handyman. Retrieved September 26, 2022, from www.familyhandyman.com/article/how-to-tint-car-windows
- Source: Anne Marie Helmenstine, P.D. (2018, December 6).“What does nucleation mean in chemistry?” ThoughtCo. Retrieved September 26, 2022, from www.thoughtco.com/definition-of-nucleation-605425
- Source: Mohammed, N.J. (2022, September).“Surface Energy and Nucleation Modes: Lecture 1.” Advanced Topics for Postgraduates in Materials Science.
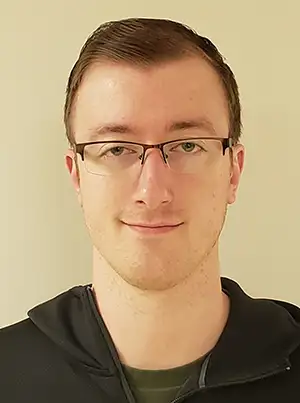
Dr. Robert Malay, technical mgr. at VDI LLC (Louisville, KY), hold a Bachelor of Science in Chemistry, as well as a Master of Science and Ph.D. in Industrial and Systems Engineering from Binghamton University. He has been with VDI since 2018, leads all research and development work, and is responsible for all process-engineering projects and initiatives. Prior to this, Robert was a doctoral researcher at Binghamton University, working on integrating flexible glass into roll-to-roll (R2R) systems, as well as fabricating and characterizing electronic devices made with R2R techniques. He is a member and regular attendee at ICEC USA, SVC TechCon and AIMCAL R2R USA Conferences. Robert serves as the Vacuum Coating Committee Chair for the Assn. for Roll-to-Roll Converters (formerly AIMCAL). He can be reached at 502-969-4227, email: rmalay@vdi-llc.com, www.vdi-llc.com.