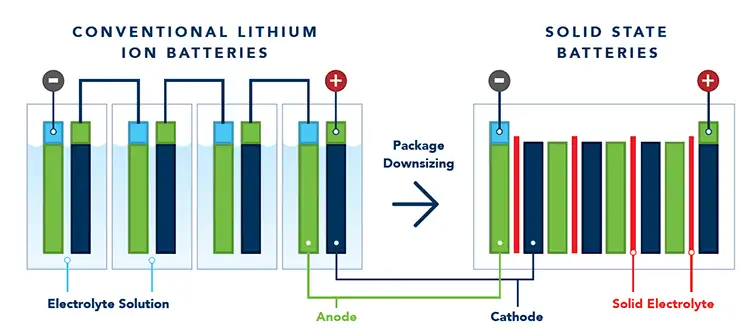
By Dan Walker, Ph.D., (formerly with Ilika Technologies, Ltd.)
Lithium-ion batteries (LiBs) are the most mature zero-emission technology for automotive applications but have limitations in cycle-life and energy density, with public concern about battery life, driving range and safety issues. Solid-state batteries (SSB) alleviate these issues with intrinsic properties of higher energy densities, reduced thermal-event failure modes (aka “thermal runaway”) and wider thermal operating range. This paper describes Ilika’s journey to scale up its SSB technology, with roll-to-roll (R2R) slot-die coating being a cornerstone enabling technology. Solid-state battery processing affords additional possibilities for tuning this established industry standard technique, resulting in a clear processing advantage for SSB.
Editor’s Note: This technical paper is based on the author’s presentation at the ARC R2R USA Conference, held in Milwaukee (WI) in October 2023.
Introduction
Solid-state battery (SSB) technology, when employed in automotive applications, will result in improved safety, lighter vehicles and higher range. To a large extent, these batteries can be produced on established lithium-ion battery (LiB) production processes, with some key differences that present an opportunity for battery manufacturers and for the production equipment fabricators alike.
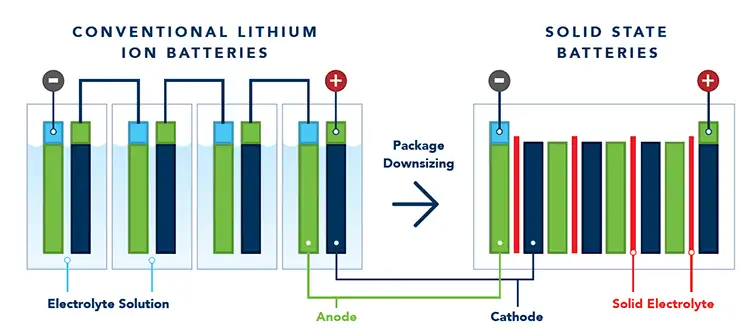
A solid-state battery is a battery in which the liquid electrolyte of a lithium-ion battery has been replaced by a solid or semi-solid material that supports ion transport (see Figure 1).
By not having liquid electrolyte, which typically is flammable and toxic, the amount of packaging required to keep users and passengers safe in case of an accident may be decreased. This reduction in weight improves the gravimetric cell-to-pack ratio, which is a measure of how much weight of the total battery pack is taken up by the batteries storing the energy. The reduced weight should result in longer range with a lighter vehicle or alternatively a greater capacity in the same-sized pack. The liquid electrolyte has further drawbacks, in that the maximum operating temperature is low as the solvents can start to volatilize. Without these solvents, the batteries can run at increased temperatures, potentially simplifying the cooling systems required on the battery pack, further increasing the cell-to-pack ratio. Finally, the SSB could be safer and easier to recycle at the end of its operating life, but that does depend on the particular solid-state chemistry being employed.
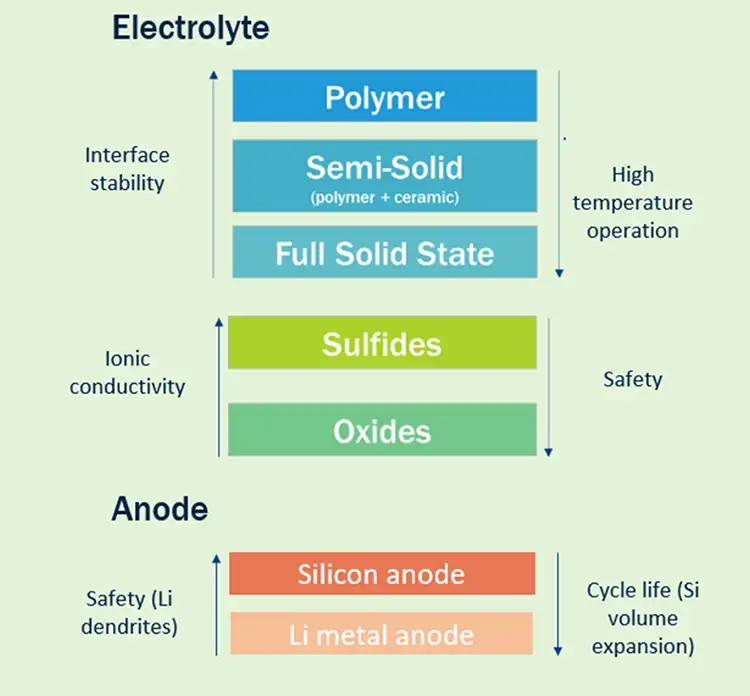
There are several types of SSB under intensive development, each with their own set of challenges to be overcome and inherent advantages (see Figure 2). The electrolyte of a SSB usually is comprised of either a polymer, a solid oxide or a sulphide material.
Sulphides have superior ionic conductivity (they can transport ions from cathode to anode and back more quickly), but these usually are toxic, especially when they come into contact with air, negating some of the packaging benefits of solid state. They also are extremely moisture-sensitive, so the production environment must be maintained at very low dew points (very dry conditions), thus increasing production cost and impacting operations.
Polymers typically are easiest to process, but do not offer the same thermal stability as oxide materials. Oxides have lower ionic conductivity but inherently are the safest and most temperature-stable. In reality, there is not a single best choice, and many of today’s SSB are a hybrid of a polymer system and an oxide system, where the oxide acts as the separator, bringing robust temperature performance and good resistance to lithium dendrites (where lithium-metal electrochemically plates through the separator), and a polymer or “gel” electrolyte in the cathode, which supports ionic conductivity.
Solid-state battery processing
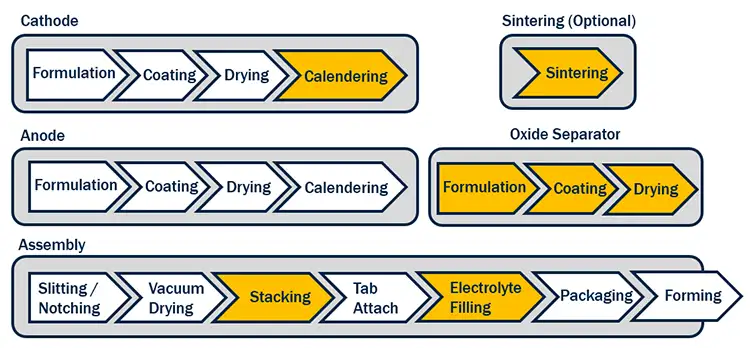
LiB manufacturing is an established and well-documented process [1], shown diagrammatically in Figure 3. This article will focus on the production differences for oxide and hybrid SSB, shown by the yellow chevrons in Figure 3.
The process used to produce the batteries is similar at any scale above fundamental research. For reference, a prototype line to produce samples for initial customer engagement might have a capacity of 1-10 MWh per year, whereas a factory can be many GWh per year. A prototype facility would output 100-1,000 completed batteries a week on an automotive format, which requires processing 100-1,000 kg of cathode slurry and coating that onto 300-3,000 meters of foil substrate. This is produced on a machine similar to the one shown in Figure 4, with a 300-mm coating width, single-sided slot-die process (shown inset) and a 3-meter-long drying oven. The gigafactory would output 70,000 batteries per week using 64 tonnes of cathode slurry, coated onto about 250 kilometers of foil every week, for each GWh produced, using either a simultaneous or sequential double-sided coating.
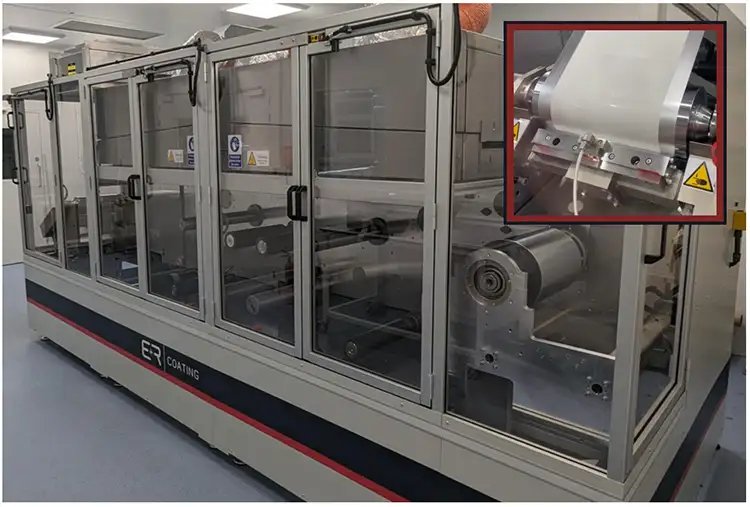
The formulation process for solid state is the same as conventional LiB, employing both low-shear and high-shear mixers to create a stable, coatable slurry, with rheological properties tuned for slot-die coating. The cathode-coating process typically is the same as LiB, employing a slot-die process for highly homogeneous layers. The anode coating also is the same as LiB, although the formulations may be different, or the anode coating skipped all together in Li-free batteries or batteries using Li-metal anodes. There is an additional coating of the solid electrolyte onto the cathode or anode, or a separate lamination process. After coating the cathode, the process may diverge, depending on the technology. For some solid-state chemistries, the calendering step can be substituted for a “sintering” step. Sintering is a process designed to “fuse” particles of electrolyte together, although in battery processes this often is performed at much lower temperatures than conventional sintering by employing additives to get the temperatures below 500° C [5,6].
In the battery-assembly process, the stacking is different; typically, not requiring a polymer separator film. This has implications for the machine tools used in the process as the separating polymer that supports the many electrode leaves through the process is no longer present. Electrolyte filling usually also is modified or removed from the process.
Future manufacturing
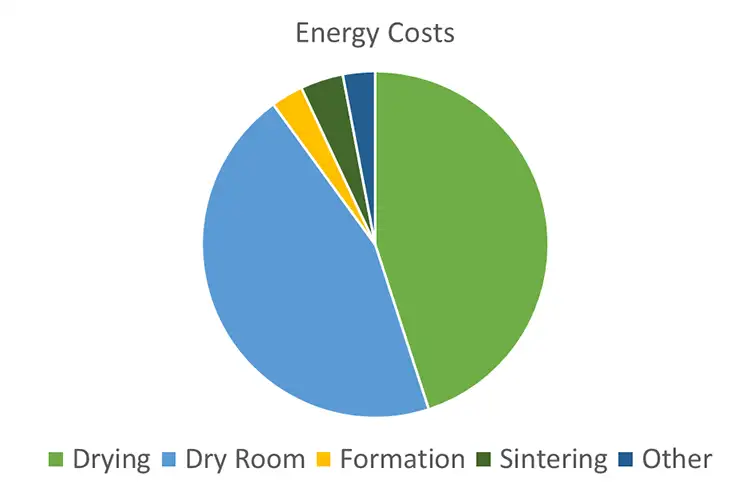
The main driver for converting from internal combustion engines (ICE) to electric motors is to reduce the environmental impact over the full lifecycle of the car. Battery manufacturing is itself an energy-intensive process, and future processes will seek to reduce this energy cost to make more cost-competitive batteries. Figure 5 shows the energy cost for different processes in battery manufacturing from an Ilika internal study based on the available literature [2,3,4]. It is evident that by far the largest costs are in the coating processes and the maintenance of dry rooms used in manufacturing. Sintering, if employed, has a low cost as the oven is maintained at temperature, with minimal exhaust air resulting in an efficient process.
Reducing the size or dryness of the dry rooms to achieve reduced operating costs is challenging as the dry atmosphere requirement is determined by chemistry and battery performance. The trend is to drier rooms, so high nickel-content cathodes can be employed; however, tuning the room dryness to the process and careful selection of which areas of the process are dry can minimize the impact of the dryrooms. The cathode-coating process is a particularly critical point due to the size of the machines at large scale. During materials dosing and mixing, they can be kept dry by controlling the headspace of the mixers. The first point of exposure is at the coating head, albeit for a short time before entering the dryer. Often pilot lines and factories accept the small exposure rather than take on the running cost of installing the coater in a dryroom. If the coating head – and the web path after coating – can be in a small, protected mini-environment, it would maintain the integrity of the coating, while costing far less than running a dryroom. The dryers typically are not installed in dryrooms at pilot-scale or above but can be fed with dehumidified air. The exit of the dryers usually is into a dry facility at a dewpoint of -40° C, where the electrodes undergo a further vacuum-drying process before final assembly.
The coating process has such a high cost, as coating solvent must be evaporated away from the slurry to form the coated-electrode layer. This is done in a warm-air convection oven, where the air transports the solvent away. This warm air must be continuously replaced, accounting for much of the energy use. Once the air containing the solvent is removed, it must be chilled so that the solvent is condensed out for recovery. This is done as the solvent usually used in lithium-ion manufacturing, N-Methyl-2-pyrrolidone (NMP), is harmful to the environment, and also for economic reasons, as even with the recovery process, recovered solvent still is around three times less expensive than solvent as purchased. (Also read “Recovery of costly solvents is critical for sustainable R2R-battery production” on page 49.)
Coating-process development is moving toward increasing the solids content of slurries, thus reducing the amount of solvent that must be removed. Dry-coat processes are being researched that can eliminate solvent all together, resulting in a vastly cheaper and “greener” manufacturing process. Solid-state chemistries may have the edge for high-solids coating or dry coating, as they can be more flexible in the binders used (LiB binders must be orthogonal to liquid electrolytes) and can use non-NMP solvents, potentially using solvents with increased evaporation rates and, therefore, lower temperatures required to evaporate
the materials.
Further research into coating processes will be targeted at coating-on-coatings – or graded-cathode coating. Today, electrode coatings are done in a single full-thickness pass, which works as the cathode thickness is not limiting battery performance. As electrodes and electrolytes improve, affording the ability to produce batteries with thicker cathodes that provide good electrochemical performance, then drying times of these thick coatings will become further limiting, requiring novel formulation, or coating and drying, techniques. In non-battery industries, coating multiple layers at once is performed routinely. Increasing coat rate also will be important, so achieving the same long-run uniformity as slot-die with alternative, faster coating methods would benefit the industry.
Conclusion
Solid-state batteries offer the potential for performance and processing advantages when compared to traditional lithium-ion batteries. The reduced need for safety protection, combined with improved thermal stability, results in lighter battery packs that give longer range. The relative freedom in solvent and binder choice means more flexibility in processing and gives the potential for reduced manufacturing costs, and “greener” manufacturing. n
References
- Lithium-Ion Cell Production Process, RWTH Aachen, https://www.pem.rwth-aachen.de/global/show_document.asp?id=aaaaaaaaabdqbtk
- A Flexible Model for Benchmarking the Energy Usage of Automotive Lithium-Ion Battery-Cell Manufacturing, MDPI, 22 Feb. 2021, https://www.mdpi.com/2313-0105/7/1/14/pdf
- Pathways to Reduce Energy Consumption in Lithium-ion Battery-Cell Manufacturing, UKBIC, https://www.ukbic.co.uk/white-paper
- Energy consumption of current and future production of lithium-ion and post lithium-ion battery cells, Nat Energy 8, 1284–1295 (2023). https://doi.org/10.1038/s41560-023-01355-z
- Low-temperature synthesis of highly ion conductive Li7La3Zr2O12–Li3BO3 composite, Electrochemistry Communications, Vol. 33, 51-55, 2013. https://doi.org/10.1016/j.elecom.2013.04.004
- The development of low-temperature sintering techniques for functional ceramic devices using chemical reactions, Journal of the Ceramic Society of Japan, 128[10], 747-755, 2020. http://doi.org/10.2109/jcersj2.20107
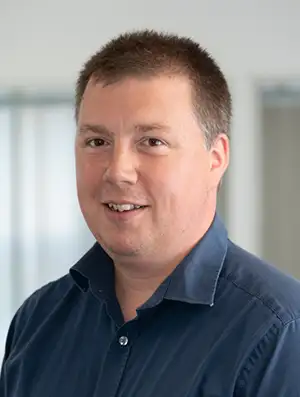
Dan Walker, formerly with Ilika Technologies, Ltd. (Southampton, UK), holds a degree in Physics and a Ph.D. in Materials Science. He started his industrial career at Merck Chemicals, Ltd., UK subsidiary of Merck KGaA. There, Dan spent 14 years on a variety of projects, from printed OLEDs to commercializing novel materials for semiconductor packaging applications – all in the field of printing and ink design for printing. In total, he has been a named author or inventor on over 25 patents and peer-reviewed publications in the field of printing inks. Over the course of his career at Merck, Dan rose through the scientist positions to project manager. At Ilika Technologies, he worked to develop next-generation, printable solid-state batteries, where he was responsible for the Goliath automotive-battery program management and Ilika’s scale-up activities to pilot and beyond.
For more information, +44-23-8011-1400, email: Denis.Pasero@ilika.com, www.ilika.com.