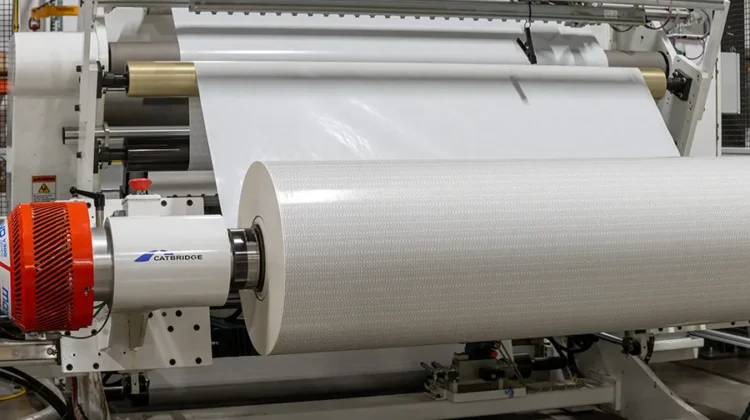
By Christopher Powell, technical sales, Channeled Resources Group (CRG)
This article delves into the variety of established release-liner products and provides a guide for selection. Vital elements such as substrate type and release levels are examined, highlighting their advantages, drawbacks and suitability for adhesive use. From thickness to peel strength, this article breaks down the complexities of release liners in an accessible manner, guiding readers through the maze of options and helping them make informed decisions.
Introduction
If you work with adhesives, chances are you have encountered the need for a release liner. But what is a release liner, and how do you select the one that is the most suitable for your needs? A release liner is a substrate coated with a release coating (most likely silicone-based) whose purpose is to protect the adhesive until its use/application. The focus of this article is to provide some general guidelines for selecting the correct release liner for the application. It will cover general release-liner use, but it is important to remember that unique applications may differ from these guidelines.
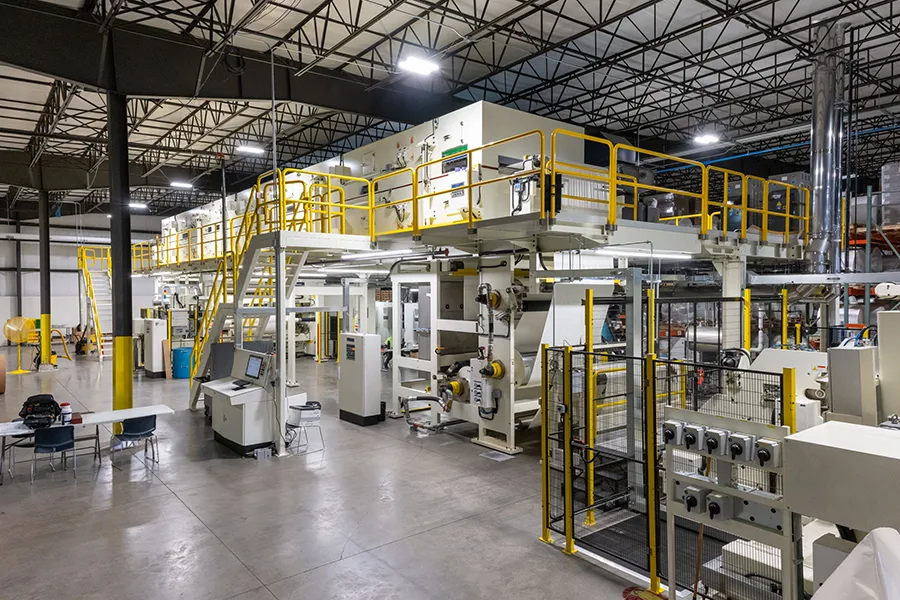
Many factors go into selecting a release liner, including the adhesive coating and subsequent processes, the product’s end use and even the market into which the product will be sold. The key characteristics of a release liner that figure into this decision-making process can be broken down into three main categories: coated one side (C1S) vs. coated two sides (C2S), the base substrate, and the release levels of the silicone (see Figure 1).
C1S vs. C2S
A product that is adhesive-coated and laminated to a face stock in the same machine pass typically needs a release liner with silicone only on the side facing the adhesive (C1S). This is the most common type of release liner and widely is used in label applications.
For an adhesive product that is unsupported or double-coated (i.e., where adhesive is exposed on both sides), a release liner with silicone on both sides most often is used (C2S). This protects both sides of the adhesive and allows the product to be unwound, exposing its application side. Once applied, the release liner then can be removed from the other side of the adhesive. An example of this would be a double-coated tape that is coated on a C2S release liner and then machine-applied to an envelope, leaving the release liner covering the exposed side of the tape for removal by the end user prior to sealing the envelope.
C2S release liners also are used when the back side of the liner may come in incidental contact with adhesive or other sticky substances. The source of incidental contact can be in your process, subsequent processes or even in how the final product is packaged or used.
Substrate
The substrate will serve as the carrier for the release coating and will be mated to your adhesive-coated product until its time of use. Consideration of the nature of the processes this laminate will encounter and how the finished product eventually will be used will allow you to identify characteristics that will be important (basis weight associated with strength property, caliper control for diecutting, thermal requirements, to name a few).
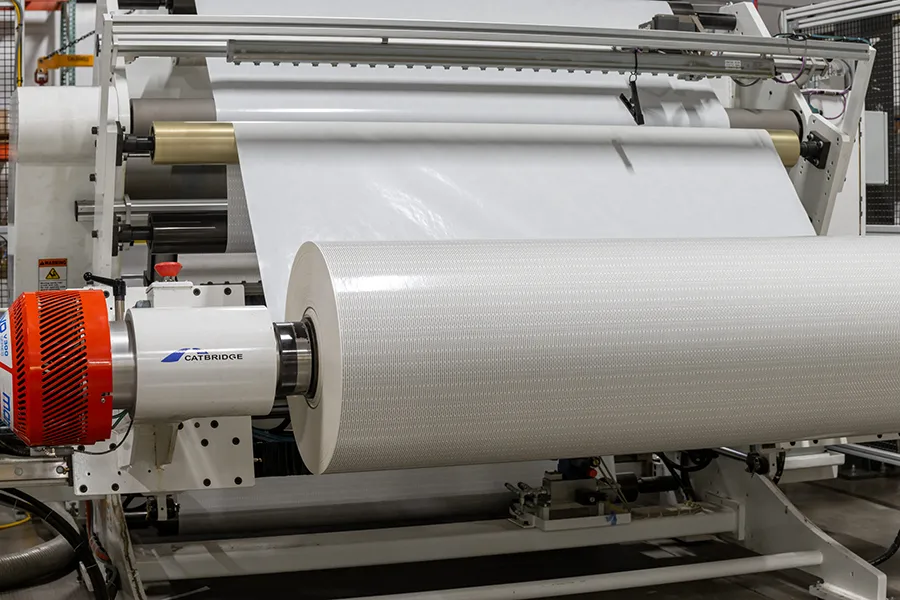
Types of substrates: Paper (super-calendered kraft [SCK], clay-coated kraft [CCK] & glassine), polycoated paper and films are the most common substrates used in release liners. Film liners are only about 10% of the market, typically are used for specialty applications and are beyond this article’s scope (see Figure 2).
Different types of paper and polycoated papers have characteristics derived from how they are made, which influences what types of applications they are best suited for. For example, SCK and glassine grades tend to have the best caliper control and hence often are selected for use in applications where diecutting is required. Table 1 highlights some of the key strengths and weaknesses of the different types of papers used in release liners.
Work currently is being done to introduce next-generation alternatives to polycoated papers, which show promise in performance and reduced cost. The construction is in the form of clay-coated sheets, with specific chemistries used in their coatings to increase moisture resistance and dimensional stability. These alternatives provide additional advantages over polycoated papers, such as recyclability/sustainability and much higher heat resistance.
Release levels of silicone
The release level of a liner is a characteristic defined by the amount of force required to remove a specific adhesive tape from the silicone surface at a given peel speed and angle. Release force can be modified via additives to the silicone formulation and generally comes in broad ranges referred to as easy, medium or tight release. Release force can be tailored to suit specific applications.
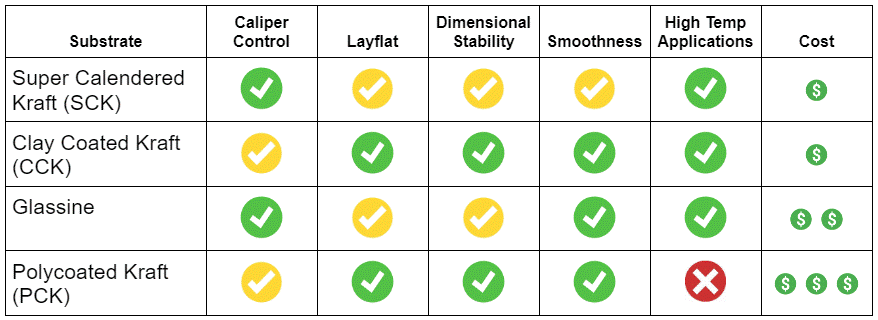
When selecting a release liner, some of the considerations for release force include:
Adhesive aggressiveness: An aggressive adhesive may require an easy release to facilitate the removal of the release liner. In contrast, a low tack/removable adhesive may require a tight release so that the adhesive does not separate from the release liner prematurely.
Subsequent processes: Machine-applied labels often require that the label comes off of the release liner easily at the time of application, while a tight release may be preferred where the liner must stay with the adhesive through multiple processes.
“Feel” of the peel: A tighter release liner can give the impression of a more aggressive adhesive if this is desirable for the end use.
C1S release liners will have one coating that can be customized to the specific application. C2S release liners often will have a differential (i.e., a different release on each side, usually referred to by the ratio of release forces, such as 2:1, 3:1, etc.). They often are used for casting liners or for double-coated tapes, where the product is wound upon itself. The tight side is where the adhesive most often is coated and where it remains through unwinding or subsequent processing.
Conclusion
This is by no means an exhaustive list of considerations or applications but should serve as general guidelines when selecting the correct release liner for your situation. It is important to partner with an experienced supplier who understands your complete process to help determine the best release-liner solution for your specific application.
Christopher Powell, technical salesperson at Channeled Resources Group (CRG) (Chicago, IL), has held Quality and Technical roles in the converting industry for close to 30 years. The majority of this time has been focused on release-liner manufacturing, but he also has worked in the related industries of extrusion polycoating and slot-die coating of hot-melt adhesives for the tape and label markets. Chris can be reached at 715-680-6326, email: cpowell@channeledresources.com, www.channeledresources.com.