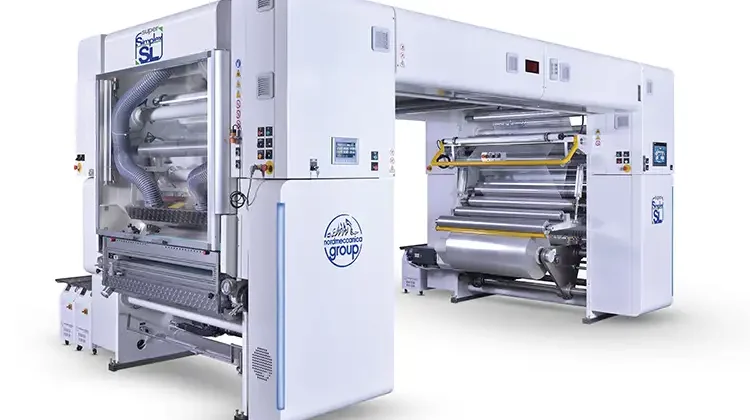
By Giancarlo Caimmi, Ph.D., commercial dir., Nordmeccanica USA Group
Historical background
My early days in an engineering department were spent in a flexographic printing-press factory. At the time, that company was one of the two largest in the world, and its products were distributed worldwide with our primary markets being North America, South America and Europe. That gave me exposure to a number of alternative cultural approaches to machine use, operator interfaces, and operator safety. In the early 1980s, when I started my career as a project engineer, safety was in fact a major concern. Nevertheless, the need to properly operate machinery back then was when most of the printing functions were manually controlled. The same applied to almost every other converting machine design back then.
In the mid-1980s, local authorities, industry associations and machinery-manufacturer organizations started looking seriously into operator interfaces and safety, offering guidelines, and not taking everything at the OEMs’ goodwill. Local authorities started implementing laws ruling on the subject. The US Occupational Safety & Health Administation was the first to release basic guidelines (surveillance of machinery with exposed rotating mechanisms and lockout/tagout during maintenance). The European Community first published its Machinery Directive in 1989, harmonizing the safety rules of all member countries.
Then, in the following years, through development of automation and an increase in electronics, most machinery controls have progressively moved from a “mechanical hands-on” approach to “remote control.” As a consequence, the number of direct mechanical controls declined while the number of process-controlling pushbuttons grew. Efficiency in machine operability and operator safety also improved. That evolution was perceived as negative by the most conservative within our industry. All of those OEMs not prepared to grow design standards to the new guidelines offered converters a solution: old-style, fully mechanical equipment that experienced quick obsolescence. Conversely, trendsetters and industry leaders adopted in real-time the new approach, investing in the improvement of both overall process efficiency and increased operator safety.
It was a sort of revolution within the industry. On one side, companies offered obsolete equipment at a lower price. On the other side, companies adapted their designs to the new guidelines and technological evolution, offering slightly more-expensive equipment but featuring higher productivity, higher output quality, lower scrap rates – and increased safety; in other words – faster ROI. The new approach, in fact, allowed the ability to implement efficient process monitoring. Operators, with the help of motorized functions and the support of remote inspection systems, have been able to not only stay safer but be more efficient in controlling the overall process and, consequently, enjoying improved output quality. The free market did the selection. The list of OEMs showing a proper ethical approach is easily determined by current market shares.
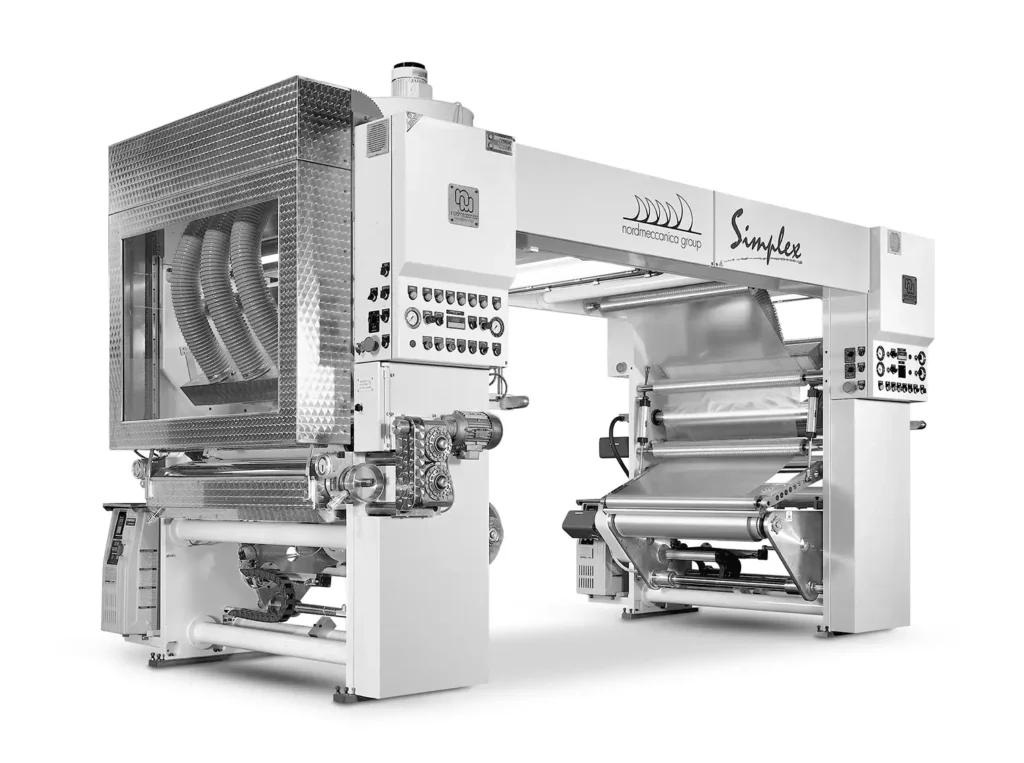
Intrinsically, every roll-to-roll (R2R) printing, coating, laminating or slitting process, being based on rotary equipment, offers potential risks to users. Printing presses have been drawing the most attention, perhaps because there are more stations, and the complexity of process control is assured by the number of controls required. So, most of the safety guidelines were originally developed around printing presses and then adapted to other processes. In most other cases, safety guidelines are protecting a single converting station, which was once considered only for the unwind and rewind safety setup as an industry standard.
Current situation
Operator-safety regulations and guidelines have been developed in a continuous evolutionary process during the past few decades. Such rules are the result of attempting to harmonize safety with the need for effective process control.
Figure 1 shows the setup of a laminator during the 1990s. The level of operator protection from hardware is definitely higher compared to the standards available in the 1980s. The number of remote controls testifies to how industry-leading machinery designers over 30 years ago had already started evolving and automating machine operations. That evolution kept elevating both operator protection and remote process handling to levels unthinkable only a few years earlier. Advances in electronics were, in fact, the most influenial factor. Confining equipment inside a glass bubble and making it perfectly safe is relatively easy; the hard part for an OEM is to also make equipment user-friendly, easy to operate – and safe.
Process know-how is at the root of OEM ability to evolve machinery design. While this may seem obvious, it’s not. A traditional engineering department, basically a mechanical shop, during the 1990s evolved into something much more complex, staffed with a comprehensive team of professionals including mechanical and electronics engineers but as well process experts, machine operators and technologists. Only those among the OEM world that have understood that need have eventually been rewarded by growing market share.
Mechatronics is born
Finally, at the turn of new millennium, even the most conservative among machinery manufacturers were forced to adopt mandatory guidelines, and regulators developed protocols to effectively monitor all new installations for compliance. Now, it’s not unusual to talk operator safety during new-project negotiations, as a key factor in supplier selection and machine-setup evaluation by converter customers. Most of the largest converters have their own set of rules tailoring the safety level of new installations not only to applicable local rules but also to a specific converting site’s environment. This avoids aligning to a unified standard for those organizations with plants in multiple locations around the world.
Figure 1 shows an early 1990s example of machine-operator interface, consisting of multiple physical pushbuttons, with each button covering a function previously operated manually. The equation, “More buttons = more safety and automation,” is easy to read. Nevertheless, even a young industry such as ours had its hard-core conservators. At the early stages of automation, there were lines such as: “If I can’t touch it, how can I be sure that it is properly set?,” “If I can’t feel the feedback and the resistance to the advance of the screw, how can I be sure I’m at the right setpoint?” and “How can I memorize the functions of all of those buttons?” All of those statements perfectly explained the setup of the vast majority of machinery installed at that time: all mechanical controls freely accessible, even ones placed in dangerous areas; and no interlocks or, in case they were provided, an everyday habit to bypass those safety devices. Operators of totally mechanical design had no need to memorize much with mechanical controls placed right at the point to be controlled. No protocols of action were enforced.
The new remote-control approach meant learning protocols because otherwise there was no way to run the machine. Compliance with safety protocols evolved to the next level through devices and components to be able to operate the machine. That generated severe allergic reactions within the industry. Safety is a culture, and culture is made of intellectual and moral evolution. People in love with basic mechanical approaches are still around our industry, selling their primordial principles and disinterested in operator safety and industry growth.
An on-board digital evolution
The digital evolution of on-board devices and components plays a big role in this story. During the era of analog technologies, the ability to handle most process variables remotely was very limited. Then electronics improved the number of remote-controlled functions, eventually bringing on-board automation to current levels. The good news was that this digital approach did not also impose a growing number of physical pushbuttons and controls. To the contrary, as technology evolved, more and more functions have been grouped and handled through algorithms, lessening the number of protocols to be learned by operators.
Again, it is an evolution with two basic requirements. First comes a massive investment at the OEM’s expense, and secondly comes flexibility required by industry players to evolve. Missing one or the other makes for failure.
Investments at the OEM level require flexibility to adapt to constantly evolving technologies. The electronics industry provides continuously new solutions targeted to simplify process control and improve safety. This is a “complication” that should affect only OEMs, not machine users. Think of the smartwatch on your wrist; there is the entire computer know-how built through the ages into it, nevertheless its use is simple and intuitive. The same level of friendliness and safety must be provided to operators of industrial machinery through design and engineering, and that is what the industry currently is able to provide. Process automation is not decisive if it’s not easy to work with. Leonardo da Vinci said, “Simplicity is the ultimate sophistication,” and it’s still true today – five centuries later.
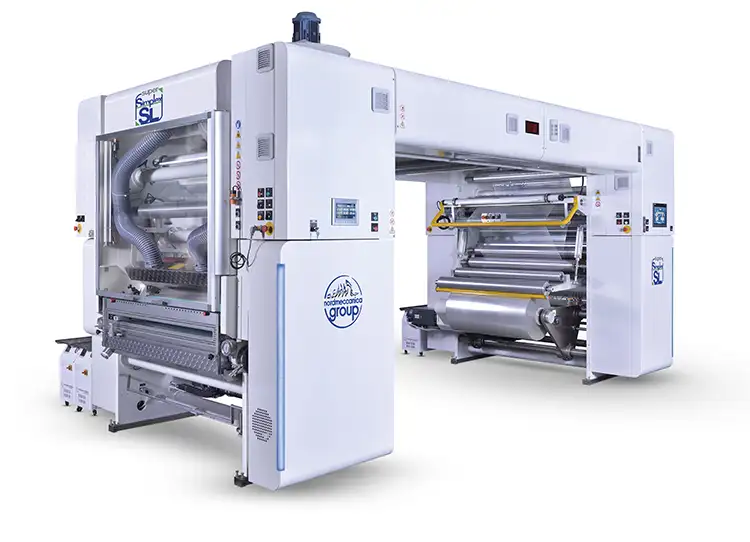
Figure 2 shows how a new generation of fully digital equipment is clear of pushbuttons, virtually none. The ones still in place are for emergencies (mandatory) and quick-reaction controls. This is the solution the firm I work for prefers to adopt: speed up, speed down; that’s it. All controls are handled digitally with some functions grouped and automatically monitored and controlled, and all actions implemented through intuitive touchscreens. Safety, it’s understood, goes hand-in-hand with efficiency and ergonomics.
The “Zero-Touch” Target
It is not the end of the story. The most advanced machinery evolution is now targeting a “Zero-Touch” production approach. It all started with consumer electronics but soon interested the manufacturing environment and machinery industry as well. The race to “zero-touch” involves a lot of activities at the OEM level and requires the contribution of partners covering several technologies, the most important being electronics. Developments are achieved through process know-how and the use of some of the most advanced technologies, such as Machine Learning (ML) and Artificial Intelligence (AI) and, again, a team of innovators contributing from its field of competence. This complex activity has for the time being led to machinery featuring the highest levels of simplicity of use and safety for operators.
A zero-touch production environment is closer than we may think. The concept is for processes where operator influence is very limited, where developments involve standardization of job recipes and the ability to set up operation through algorithms expressly developed for repeat jobs but eventually for all runs involving similar recipes. Solutions to serve a zero-touch environment are technologies that will soon be ready to cover an entire production process, including predictive maintenance.
Conclusions
Aligning with innovation is the basis of success in every industry, and so it is for ours. Converting-process and machinery-design innovation has very many faces as we discussed, and current trends have a serious impact on the ability of OEMs to always be on the cutting edge.
Flexibility, simplicity of operation and worker safety are key drivers for the machine supplier. Investing in fully digital equipment doesn’t offer just the benefit of installing machines with fewer buttons; fully digital configurations offer immediate advantages in productivity and output quality that also are in full compliance with applicable safety rules. A fully digital machine can offer the ability to upgrade with ease, as well as help limit the negative effects of scarce manpower and speed up operator training.
Stopping evolution means the end of a species. Our species, the converting industry, is relatively young and has experienced innumerable revolutions. My generation, the Baby Boomers, has witnessed almost the entire story. If it was not for those individuals that shaped our industry inspired by ingenuity, determination and creativity, we may have not evolved to these levels. Let’s keep being inspired by them and think innovation and evolution versus conservatism and satisfaction with the status quo.
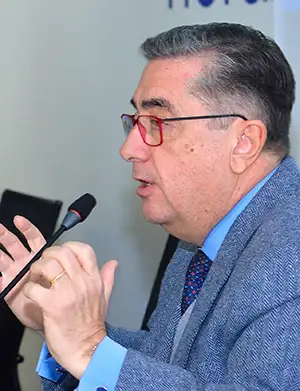
Giancarlo Caimmi, commercial dir. for Nordmeccanica USA Group (Hauppauge, NY), holds a Ph.D., in Mechanical Engineering from University Federico Secondo (Italy). He has almost 40 years of experience in the converting-machinery manufacturing field. Giancarlo can be reached at 631-242-9898, email: caimmi@nordmeccanica.com, www.nordmeccanica.com.