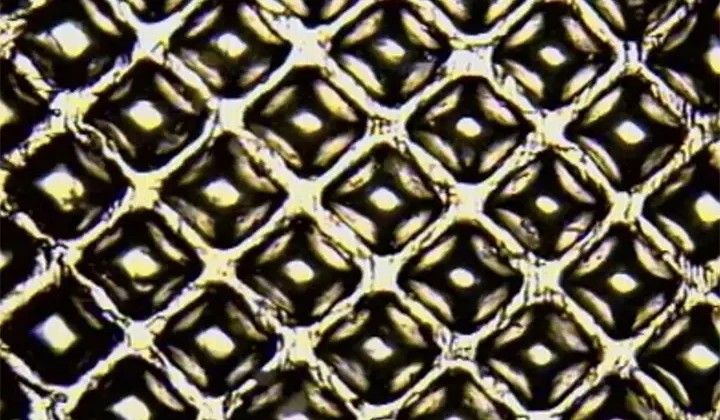
By Bill Poulson, global technical solutions mgr., Harper Corp. of America
This article will discuss the pros and cons of the chrome anilox to ceramic anilox rollers conversion. While there are times when converting to ceramic may not be a good fit, the wear resistance of ceramic is many times more than chrome. The geometry and volume capabilities of both technologies, as well as the transfer efficiencies will be compared. Volume correlation is not 1:1, so experience is needed to know how to adjust volume on certain coating applications. Many successful applications using ceramic anilox rollers are possible. Silicone is a low-volume use in many cases. Release-coat variations can be controlled easily simply by adding or reducing volume for the application. Other topics covered include how to test to compare what selection is optimal when shifting to ceramic; volume/transfer efficiency matters more with a ceramic roller for gravure than a chrome surface; and the finish of ceramic is critical at the initial polish before going to the laser-engraving process.
Introduction
For many years, mechanically engraved and chrome-anilox rollers have been the standard in the gravure printing and coating industries. At one time, these technologies were the only option converters had, whether they ran the flexographic or the gravure method. These rollers ran with rubber meter rollers or a doctor-bladed metering system.
Many improvements and innovations over the years have provided new opportunities that should be considered by the coating industry. Most of these improvements in ink metering came after the implementation of ceramic, laser-engraved anilox rollers. Continued innovations in ceramic rollers provide a new level of efficiency for the gravure method.
Converting to ceramic anilox engraving continues to be a trend that many converters have accepted, and those who haven’t should consider. Ceramic rollers have proven to outlast chrome by more than 20 times and, depending on the specific application, have lasted even longer than that.
Our intention in this article is to show the advantages of converting to ceramic anilox rollers. Although chrome still provides value in specific applications, the vast majority of uses can convert to ceramic with improved operational efficiencies. Identifying the controlling variables will allow printers and converters to make this transition an easy one. Chemistry of the coating, substrate and final product are all crucial elements. Pick and choose where it will make sense to convert based on production efficiency, roller life cycle as well as product requirements.
Chrome engraved anilox rollers
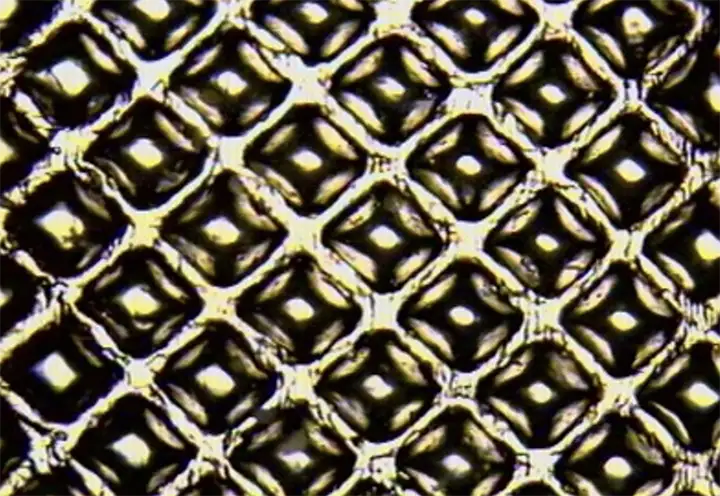
Chrome rollers are the original anilox technology. They are constructed of a steel base that is electroplated with copper and chrome. The roller surface can be milled or engraved with a variety of tooling practices. Many chrome rollers are engraved using a diamond-stylus method. Whatever method yields the same surface and wear characteristics (see Figure 1).
Advantages of chrome anilox rolls:
- Consistent ink transfer
- Repeatable cell definition
- Ease of cleaning
- Can achieve higher billion-cubic-micron (bcm) ranges over ceramic
Disadvantages of chrome anilox rollers:
- Rapid wear; coatweights can drop quickly
- Wider cell walls
- Some geometries have less efficiency than ceramic
- Limited line-screen selection
- Limited geometry selection
- Easily damaged
- Environmentally hazardous to produce due to chrome-electroplating process
- Limitations in reproducibility
- Susceptible to corrosion
Laser-engraved ceramic anilox rollers
A ceramic anilox roller is constructed of the same steel base as chrome rollers. The finished diameter then is accomplished with a build-up process using various base materials or barrier coatings prior to chromium-oxide ceramic powder being plasma-sprayed onto the roller surface. The base materials provide a barrier coat that prolongs roller life by preventing corrosive chemistries from reaching the steel base. The chromium oxide then is polished to a mirror finish and laser-engraved to the desired geometry (see Figures 2a-d)
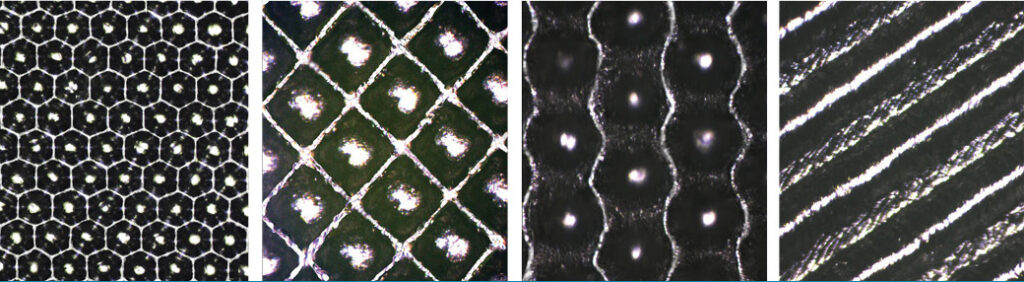
The build-up on a ceramic roller can be achieved by arc-welding, an alloy-spray build or HVOF – a high-velocity, oxygen-fueled spray-coating method. Spray build-ups primarily are used for sleeve technology. HVOF is an excellent alternative for a corrosion barrier if the base material is thick enough to defend against the heat transfer of the build-up process. This provides a higher-density sublayer to prevent corrosion. Build-up materials can be various grades of steel or alloys.
Advantages of laser-engraved ceramic anilox rollers
- Excellent wear characteristics
- Increased deposit efficiency
- Higher consistency of coatweight over time
- Maintains coatweight at high speeds
- Thinner cell walls
- Minimal post areas
- Precision cell shapes
- Variety of geometries
- Higher line screens
- Increased press speeds for flexo and/or gravure
- Saturation specifications achieved with improved transfer efficiencies
Disadvantages of ceramic-surfaced rolls
- More care is required in cleaning the roller
- May not transfer as efficiently as chrome on certain coating chemistries
- Higher initial investment than chrome
Inks and specialty coatings
In most cases, the ceramic roll will convert over from chrome at a lower volume. There are many variables within the coating realm. Coatweight, percentage of solids, viscosity and lb/gal are critical specifications that need to be known before an anilox can be specified for a coatweight. You need to take into consideration the type of ink, whether the ink or coating is solvent-based, water-borne, energy-curable (electron beam or ultraviolet) or any other specialty types. Adhesives would be considered a specialty type of coating. Metallic and scratch-&-sniff both have larger particle sizes than standard inks. This also needs to be considered before specifying the anilox’s line screen.
Volume critical
Volume is the critical factor when specifying a ceramic anilox roller. Too often, we get caught up in what line screen is used and overlook volume. Volume is what delivers the desired coatweight, while line screen and cell geometry will provide the most efficient transfer. Every anilox manufacturer has its own line-screen and volume recommendations charted and published. It is highly recommended to work with your supplier to determine the proper volume and geometry to meet your specific coating needs.
Line screen
As mentioned above, volume is critical. Once the volume is determined for your application, it can be optimized to the proper cell geometry for transfer efficiency. Take into consideration the particle size of pigments when specifying line screen and cell openings. Ceramic does not yield the same surface tension as chrome and requires cell configurations to have efficient, internal-cell cavities. When heavy-viscosity coatings are being applied, a shallow free-flowing cell configuration is the appropriate cell profile, such as channeled engravings like a trihelical geometry. Thinner, less-viscous coatings should have an enclosed-cell configuration (60º hexagon) to eliminate the chemistry from slinging. This may vary depending on the chemistry of inks and coatings used. Banded-roller testing and experience will help make this decision.
Banded-roller testing
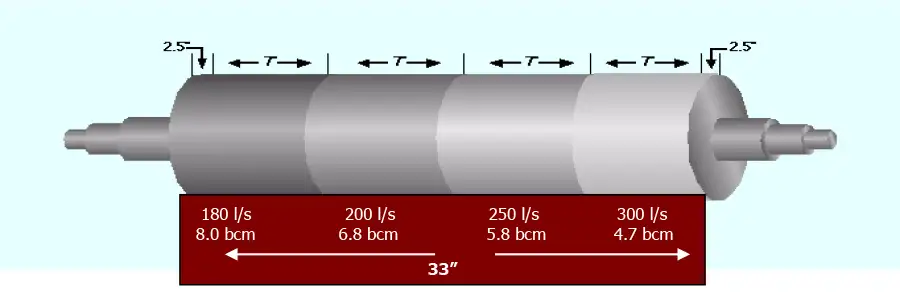
The key to making a smooth transition from mechanically engraved chrome rollers to laser-engraved ceramic rollers was derived from banded-roll testing. A banded roller is a single anilox roller with various line screens, cell geometries and cell volumes (see Figure 3). Banded rollers primarily are used in flexographic process printing to determine what line screen and volume will provide optimal print densities, dot gain and print contrast for a given application.
Although this is the most common type of testing conducted with banded rollers, it is by no means the limitation. The limits are determined by time and dedication put into the testing. To have a successful trial, the proper personnel who will be involved in the test run should define trial goals. This may include management, prepress, co-suppliers and the operators running the press. Once the objectives are determined it is time for the press trial, the mind set should be open and focused on making the banded roller perform the way it was designed, not focused on making the numbers fall in place by manipulation. A properly designed banded roller should have failing results as well as passing results. The logic behind this is to see where the limitations are.
This approach was taken before the press trials below were run. Much of the testing was with different ink formulae as well as variations in substrates. The line screens and volumes as well as geometry will vary depending on what type of coating or ink is being used. This is a well-thought-out way to approach any area where you are unsure of what is the most efficient way to lay down your ink or coating – be it flexo, gravure, adhesive or silicone.
Pressroom conversion: Chrome to ceramic
We conducted press trials to show the efficiency of deposit rates of ceramic anilox rollers. The performance of the ceramic engravings surpassed all expectations and delivered many positive results. The most astonishing discovery was how efficient the ceramic roller was in transferring the coating. This allowed increased press speeds with noticeable improvement in print smoothness. Another eye-opener was exposed when the test results were measured; not only did we have an improvement in press speeds and print quality, but we also achieved the same opacity values, capitalizing on improved transfer efficiencies that equated to about a 20% reduction in ink costs.
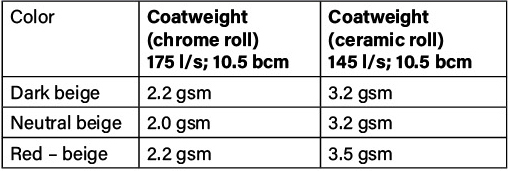
The application that was converted used a 175-line-screen, chrome roll with a volume of 10.5 bcm. The target coatweight was 2.1 gsm on paper. The ceramic anilox roller that was recommended was a 145-line-screen, 10.5-bcm volume. Water-based beige ink with a pH of 8.9 was used; viscosity was 17 secs on a #4 din cup. The initial job ran on the chrome roller. The goal was to match the coatweight of 2.1 gsm delivered by the chrome roller. Once again, the results achieved by the ceramic roller exceeded all expectations on all three shades of beige (see Table 1). We purposely matched volumes on the conversion to show that ceramic delivered its coating more efficiently. In many cases, when matching a chrome volume, we need to increase volumes by 15%, but this all depends on viscosity. The higher the viscosity, the higher the increase of volume is needed. Due to reduced transfer efficiencies of chrome, we needed to have more volume to equal the transfer efficiency of ceramic.
The advantage chrome has is that maximum volumes can be obtained into the 100-bcm range.
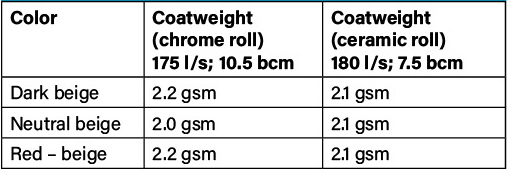
The increased deposit efficiency of the ceramic roller allowed for a reduction in cell volume and justification for more testing to be conducted. The new specifications for the anilox were 180-line-screen with a 7.5-bcm volume. This was a 39% reduction in cell volume with our goal remaining the same (to achieve 2.1 gsm). All other variables were constant except for the running conditions. The new comparisons were to be done in a live production environment. At the end of the second press run, the chrome roller was switched out and the ceramic roll was installed. Samples were taken, and coatweight and spectroscopic readings were done. The coatweight matched the chrome roller exactly at 2.1 gsm (see Table 2).
The improved performance of the ceramic roll over the chrome roll allowed for an increase in press speeds by as much as 50 mpm (150 fpm). In the past, increasing press speed on the chrome roller lowered the coatweight to unacceptable levels. This was not the case with the ceramic engravings. Press speeds increased, and coatweight remained stable. Other notable improvements worth mentioning were the visual smoothness of the coating. This allowed us to reformulate the ink with less opaque white, which also equated to further cost savings that we were not expecting.
The base colors that were printed were overprinted with three additional colors. The overprint colors showed improvement in laydown because the base coat has improved. The dot quality of what is printed above these base coats also improved considerably. The conclusion from the trials conducted has not only justified the cost associated with a ceramic roller over a chrome roller but provided significant savings in press time and ink cost. Color matching is another cost-saving area through reduced time matching ink on press. The ceramic anilox roller has provided improved consistency when press speeds vary in direct-gravure mode.
Summary

Important points to keep in mind. Choosing the correct line screen determines the depth-to-opening (D/O) ratio of the cell. In gravure, we want what is illustrated on the left in Figure 4. Flexography can push the limits of the laser-engraving process, but to get efficient ink or coating release with gravure, optimal D/O is critical.
Why do we choose specific volume ranges within line screens? What happens when the D/O ratio is too high? When should I use a lower line screen? These all are great questions asked by converters when doing a variety of printing and coating applications. Illustrated in this article are the results when the D/O ratio is too high and what happens to cell integrity when pushing limitations of line screen to volume. Also shown was how line screen can affect the ability of how well inks and coatings transfer from the cell, and how specifications for line screen to volume may change depending on the ink chemistry being used.
There have been many advantages experienced through the conversion from chrome to ceramic anilox rollers. All improvements are cost-effective and will be noticed in reduced downtime and increased throughput on-press. Advantages from this conversion include:
- Increased stability of coatweight over life of the roll
- Increased deposit efficiency with ceramic anilox
- Improved laydown at lower volumes
- Higher opacity on the substrate
- Ceramic exhibits better control of ink transfer compared to chrome rollers.
- Ceramic rollers manufactured with a 60º hexagon has 15% more transfer efficiency than a 45º quad cell.
- The coatweight remains the same at higher speeds rather than dropping off as it did with the chrome roller. This resulted in an ink savings of 0.35 to 0.51 cents per pound of paper due to the 39% reduction in cell volume.
- Ceramic anilox will have an increased working life.
- Major increase of runtime on ceramic rollers on press
- Less time needed to match color with ceramic roller during make-ready compared to chrome roll
Conclusion
This conversion from chrome to ceramic anilox rollers has yielded many cost savings to the converter. Consider this conversion to ceramic engravings if you are a gravure or flexo coating facility and still using chrome rollers across your product mix. In the applications tested above, printing on a paper substrate was performed. Ceramic rollers can print on a variety of substrates from films, styrenes, papers, nonwovens, tissue and any substrate that will attract inks or coatings. Overall, ceramic has a more controlled deposit rate, which will allow for an increase in efficiency and quality.
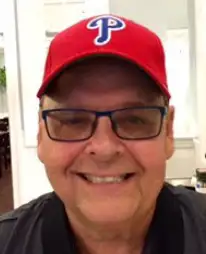
Bill Poulson, global technical solutions mgr. at Harper Corp. of America (Charlotte, NC), has been with the company for 23 years. He has experience in the flexographic and gravure printing and coating industries since 1971. Much of what Bill has written here is from his hands-on experience, and he believes in education and supporting organizations such as The Phoenix Challenge, which annually conducts high-school and college-level flexo-printing skills competitions. Bill can be reached at 704-588-3371, ext. 4335, email: bill.poulson@harpercorporation.com, www.harpercorporation.com.