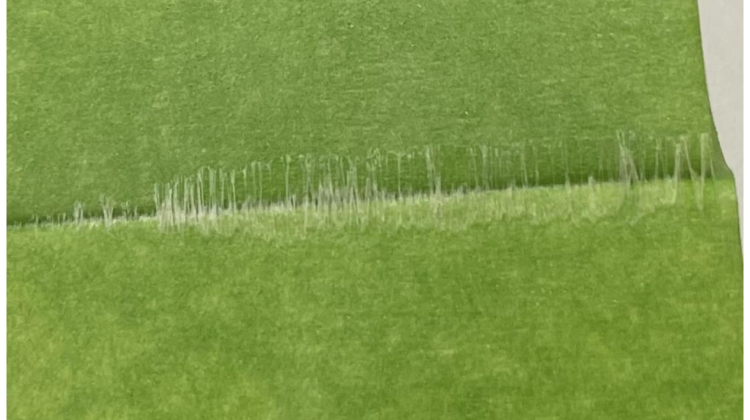
By Tim Rummel, technical mgr.-North and Central America, Wacker Chemical Corp.
Linerless labels provide unusual challenges for silicone release coatings, as the thermal-imaging paper contains unique chemistries and is very temperature-sensitive. For this reason, the majority of linerless labels are made with UV-curable silicone. While UV-curable silicones have some clear advantages in this application, low-temperature curable silicones can offer specific advantages as well, such as lower rates of inkjet-printhead fouling. This article explores the pros and cons of the two different platforms.
Editor’s Note: This technical paper is based on the author’s presentation at the 2024 AWA Global Release Liner Industry Conference & Exhibition held in Amsterdam, Netherlands, in March 2024. More info: www.awa-bv.com
Introduction
The linerless revolution for labels is inevitable, though it will come slowly. In case the reader is unfamiliar, linerless labels are ones where there is no paper or film release liner to protect the adhesive, just a label that can release from the image side with the usual adhesive on the other side. Really, a linerless label is not much different than a roll of masking tape. The trick, though, is that a label has an image of some sort, and it must be under whatever release coating is present. In most cases, the release material is silicone, which is notoriously hard to stick to (which also is the point, actually). Even if we could print well on silicone, ink would bury it and prevent it from releasing the adhesive.
Linerless labels are far from a new concept. They’ve been in development for decades now, and it will be decades more before they are the primary solution in the pressure-sensitive label market. The advantages of one substrate instead of two, and the environmental and cost benefits that this can provide, are buried behind an array of challenges. Some are more obvious than others. A solution for prime labels is far off. Silicone can be applied over printed images, but then the adhesive and silicone would need to be coated after printing. This would require a complete reversal of that part of the value chain. Never mind the fact that the belt that feeds a high-speed labeling machine currently is the label’s liner.
Progress with variable-information labels
Variable information (VI) labels, on the other hand, are making good progress. These labels are preprinted with a flood-coat of colorless chemicals that react and turn black when exposed to heat. They are used in applications such as address labels, luggage tags and deli-counter labels where each printed label is different. So, if pre-coated with silicone, imaging still is accomplished easily by firing energy in the form of heat through the silicone coating to render an image. VI labels that are linerless differ from most two-ply labels in that their corners are square. Two-ply labels are diecut, almost always with rounded corners. This is done for aesthetic reasons but also for greater converting efficiency. Linerless VI labels must be cut by the printer and are, therefore, largely limited to straight cuts.
Still, however, there are challenges for VI labels. Most labels are made with silicone that’s cured at 140-170° C. Most VI labels activate between 70° and 90° C and will turn black at higher temperatures. Therefore, the predominant solution to date has been UV-curable silicones. With no specific curing temperature, UV silicones can be run as on any other substrate. Thermal silicones, however, have some advantages of their own. Versions are becoming available that can be cured at 80° C with reasonable line speeds by using different silicone polymers and better-suited inhibition systems. Each platform has its advantages and disadvantages, which we will now explore.
Comparison of UV vs. thermal silicone coating
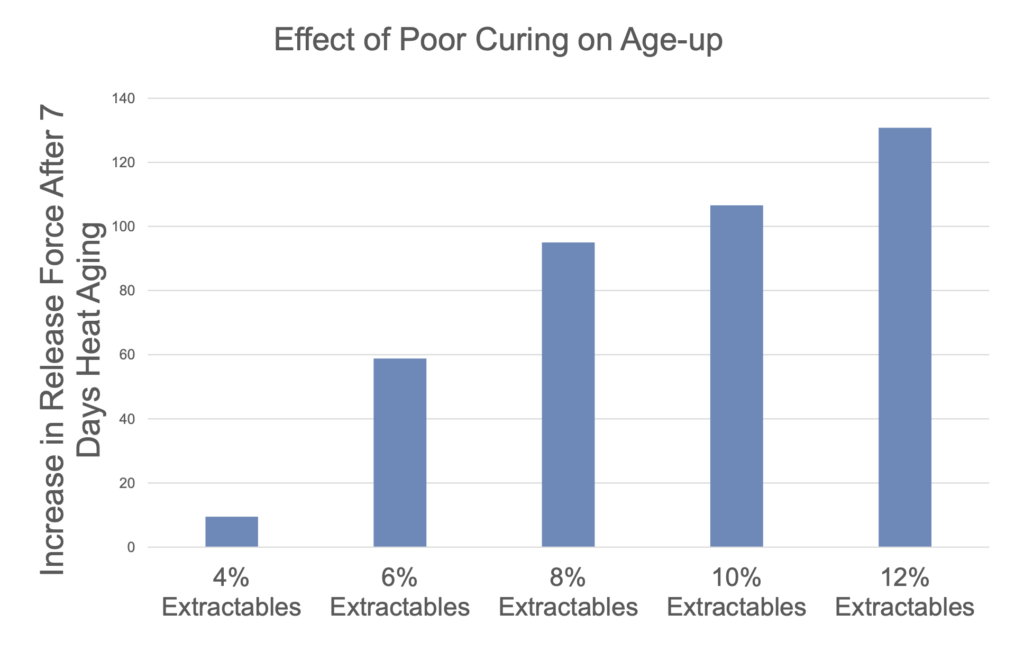
Completeness of silicone curing is arguably the most important aspect of coating silicone release. Incomplete cure typically causes high release force, poor aging (climbing release force over time) of the label stock and even poor adhesion of the label to a container (see Figure 1). In this case, UV has an advantage, as it can be cured under ambient conditions, provided the lamps don’t give off too much heat. Thermal systems are cured in short ovens built to run high temperatures, so even the fastest curing systems out there might result in decreased line speed or higher than normal catalyst dosing. That being said, UV systems are more prone to aging and stability if under-cured, so care must be taken to get complete cure regardless of which platform is used.
Silicone coatweight is another aspect that needs consideration. In this case, there is no advantage for UV vs. thermal, but there is an unusual aspect to consider. Image clarity and color density may be impacted by silicone coatweight. Typical silicone coaters apply just enough silicone to get good release performance. While good release still is a requirement of linerless labels, optimum image clarity also is an issue that must be evaluated on a case-by-case basis. Barcodes and QR codes have little room for error, so clarity is vital.
Food-contact rules apply to many labels, so a thorough review of the system being used is required. The biggest issue for thermal silicones is platinum concentration in the coating. Platinum concentration must be under 150 ppm for 21 C.F.R. § 175.300, 100 ppm for some sections of 21 C.F.R. § 176.170, and 120 ppm for BfR XV – Silicones. UV systems, on the other hand, use photoinitiators, which must be fully consumed, as they are not rated for food contact. This is an advantage for thermally curing systems, as compliance is determined simply by the formulation used when applied. UV systems, however, rely on continuous analysis after production to ensure that they are “safe for use.”

Substrate inhibition, in general, is a bigger problem for thermal-curing silicones than for UV systems. This is because platinum catalyst is highly reactive, so there are a number of chemicals that can interfere with it. Amines, mercaptans, phosphites and melamines are some common examples of chemical types that can interfere with platinum catalysts. This issue is growing even more complex, as thermal-paper manufacturers reformulate their coatings to remove phenols, such as bisphenol A and bisphenol S. Phenols, despite their issues, don’t inhibit platinum, while many of the replacement materials do. It is possible to get great thermal cure on one sheet and absolutely no cure on a different sheet. So, with thermal silicones, converters must work with their paper suppliers to make sure they have a good sheet for thermal silicones. This is less of a concern with UV systems.
Substrate anchorage is more critical than for most labeling applications – whether UV or thermal (see Figure 2). This is because the silicone will rub across the surface of a heated printhead. Anchorage is achieved via formulating properly with either silicone platform, and the same rules apply for linerless as for other substrates. The surface coating of thermal papers often is polyvinyl alcohol (PVOH), which typically is quite receptive to silicones. However, the surface will consist of very little, if any, paper fiber, because of the multiple polymeric coatings needed to make good thermal VI-label paper.
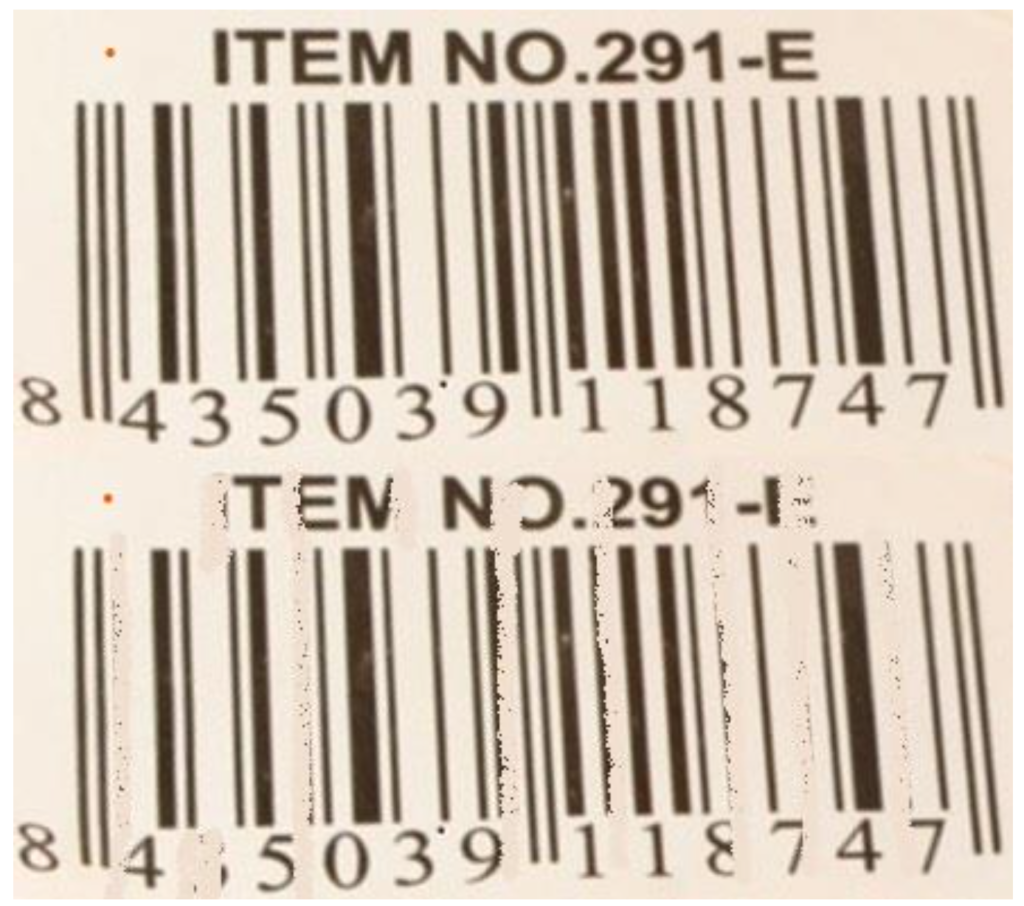
So, there is no advantage with one system vs. another for substrate anchorage, but that doesn’t translate into equal performance of build-up on printheads. This is one of the biggest drawbacks of linerless-VI labels, as build-up will prevent proper imaging (see Figure 3). Thermal systems can offer a big advantage in some cases, because there are more formulating options available and a lot less functional chemistry overall compared to UV-curable silicones. Thermal systems typically are compatible with acrylic adhesives as well, but UV systems often are not, which opens up new markets and options. Linerless printhead build-up can occur because of adhesive that transferred to the silicone as well, so good performance by both silicone and adhesive is necessary. Clean printhead performance is vital, especially in high-speed labeling applications, and thermal-curing silicone offers a way to get that performance.
Conclusions
UV- and thermal-curing silicones each have advantages relative to one another for linerless-label applications. UV systems require only minor adjustments to chemistry and work on most substrates. Thermal systems often are more challenging to apply, but they offer advantages for food-contact compliance and better performance related to printhead build-up of silicone. Each individual case would benefit from an analysis to ensure that the best system is selected.
Tim Rummel, technical mgr.-North and Central America for Wacker Chemical Corp. (Ann Arbor, MI) for the release-coatings business since 2012, holds Bachelor of Science degrees in Paper Science and in Chemistry from Western Michigan University, as well as a Master of Business Administration from Wayne State University. His experience includes two decades of formulating release coatings for the pressure-sensitive tape and label industries, including a great deal of process development and optimization. Tim can be reached at 734-489-8360, email: timothy.rummel@wacker.com, www.wacker.com.