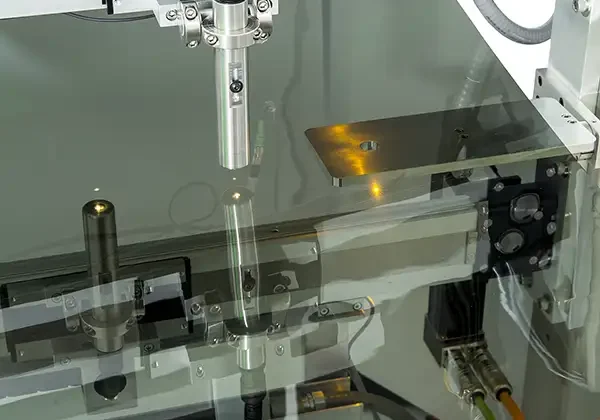
By Vivek Komaragiri, chief technology officer, Sensory Analytics
This article discusses some of the coating-process digitization opportunities created by real-time measurement of coating-thickness measurement data, especially by using a precise and absolute thickness-measurement technology known as ruggedized optical interference (ROI) technology. To remain competitive in a rapidly changing and evolving coated-product manufacturing industry, organizations must explore ways to digitalize and transform their processes to be more efficient and more automated. The retirement of an aging workforce creates a significant void for an inexperienced workforce to fill, and as such there is an increasing need to automate entire manufacturing processes. Availability of real-time, high-speed data is critical for automating various manufacturing methods and steps.
Introduction
For coated-product manufacturers, coating application and control is one of the primary areas of concern, and accurate, immediate feedback of coating application with real-time measurement is critical to proper optimization and control of the coating-application process. Manufacturers constantly are looking for ways to improve coat quality by measuring the coating thickness and coatweight while reducing coating cost. With coatings becoming increasingly thin and applied within tight tolerance limits, the ability to measure accurate and precise uniform thickness during production allows manufacturers to capture in-process defects much earlier, and thus eliminate product waste.
Real-time measurement of adhesives and other coatings on tape products, laminations and flexible packaging is critical to improving the overall quality of the end-product and process efficiency. Conventional off-line and in-line measurement tools either are environmentally unfriendly or fall short as an accurate measurement option as thickness of adhesives and applied coatings become thinner. As a result, manufacturers face significant challenges in applying and verifying the correct amount of applied coatings. The availability of new high-speed, non-contact measurement alternatives that accurately measure the absolute thickness or coatweight of applied coatings immediately following application improves accuracy, minimizes process-control issues and reduces costs by minimizing overapplication.
Ruggedized Optical Interference (ROI) technology
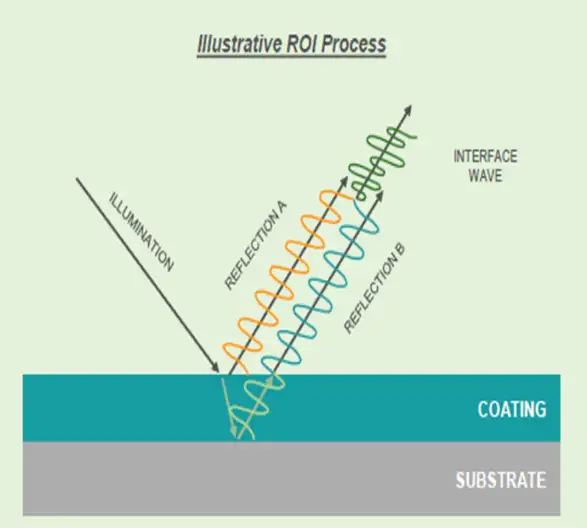
One such technology that can be used to obtain high-speed, reliable and precise thickness measurement is patented Ruggedized Optical Interference (ROI) technology (see Figure 1). The abundance of precise and accurate data available through this real-time measurement technique greatly helps facilitate coating-process digitalization opportunities.
This technique analyzes a light signal comprised of rays that are reflected from the surface of the coating, as well as rays that transmit through the coating to reflect from the adjacent layer. The interference of these waves produces a discrete optical interference pattern with a frequency that directly correlates to the absolute thickness of that coating.
The ROI-measurement technique can be used to precisely measure real-time thickness of wet and dry applied adhesives and other coatings down to sub-micron levels for measuring coatings on polypropylene (PP), polyethylene terephthalate (PET), Kapton® film, biaxially oriented polypropylene (BOPP) and many other substrates. The technology generally is substrate-independent (see Figure 2).
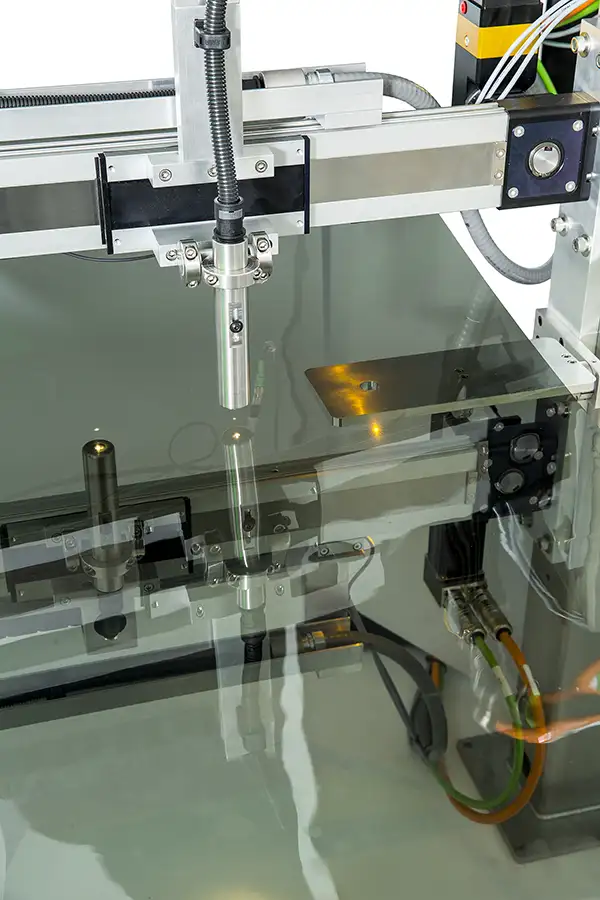
It is based on the well-known science of optical interference, but unlike most legacy thickness-measurement tools based on optical interference, ROI technology is an enhanced and optimized version of the technique that can be used to measure in a real-time production environment with a production speed of up to 600 mpm. It also effectively counters additional production-related variables, such as material flutter, temperature and humidity changes, and so on. The broad wavelength of light used in this technology will help measure not only transparent coatings, as with most optical tools, but also pigmented and other non-transparent coatings.
Process digitalization
Process digitalization generally means that some digital technologies will be used in the processes to manage data digitally to, in turn, improve existing processes and make them more efficient and more productive, resulting in greater customer satisfaction. Therefore, a key benefit of digitalization by use of digital information is to optimize business results, improve profitability and cost-optimization and achieve a better customer experience when applying digital technologies.
One of the key additional advantages of process digitalization is that it allows companies to enable a fully automated process with closed-loop feedback, which increasingly is an end goal for most coated-product manufacturers to minimize the dependency on skilled and aging operators. With up to 150 measurements/sec, ROI technology delivers an abundance of valuable data to help digitalize the coating-application process (see Figure 3)
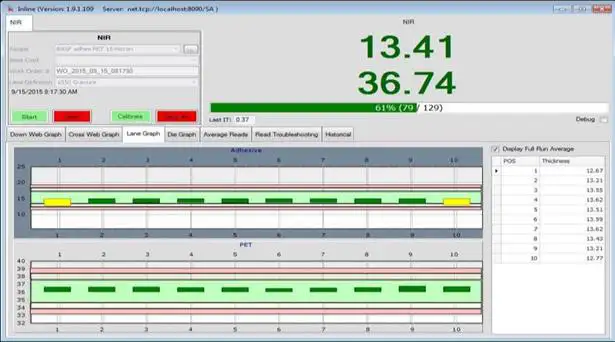
Coating-process optimization
For most coating applications, there is a target specification for coating thickness and coatweight. Historically, due to the lack of precise and accurate in-line-measurement tools, coated-product manufacturers usually err on the side of caution and tend to apply the coating toward the higher end of specification ranges, thus increasing costs where it is unnecessary. It is important to have a precise and accurate measurement tool, along with excellent R&R (repeatability and reproducibility), to effectively optimize coating-application processes as a gauge.
With an R&R of usually less than 5% and an accuracy of +/-1% of the applied-coating thickness, Ruggedized Optical Interference technology can be used effectively to optimize the coating process and apply materials toward the lower end of the specification. As a result, this not only saves on coating costs but also improves quality and consistency of the measurement at the same time. As shown in Figure 4, the key benefit is to reduce process variations with a more accurate tool and minimize the standard deviation of the coating-application process. Once a better process control is established, the mean value can be shifted left to witness significant coating cost reductions while improving quality.
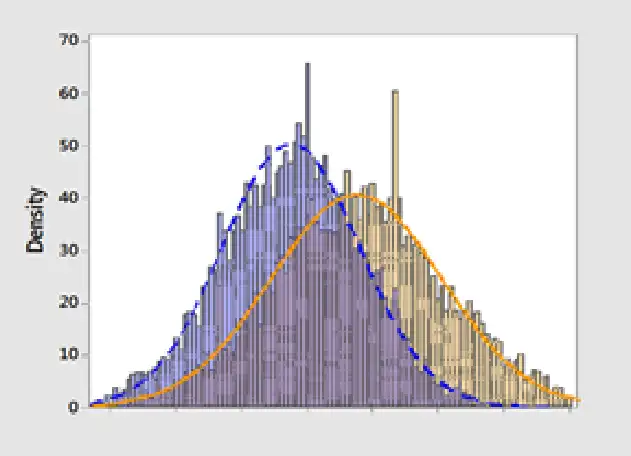
ROI technology can be used to measure and optimize a wide range of coatings, starting from sub-micron thickness to about 350 microns thick. Coating types also include adhesives, thin hard coats, barrier coatings, base films (polyethylene [PE], PP, BOPP, PET to name a few), pigmented coatings, and many others. The ROI technology measurement is not dependent on specific chemicals in the coating or coating chemistry and, hence, is applicable to a much broader range of uses than other legacy measurement technologies.
Conclusion
With the increasing desire of coated-product manufacturers to digitalize, automate and optimize manufacturing, ROI technology is ideally suited to accomplish the goals of high-speed measurement, generating an abundance of valuable data and a much higher level of coating accuracy and precision. Process automation is valuable only if the automation is done correctly, which is where the accuracy and precision of in-line coating-measurement technology is critically important. Hundreds of global coated-product manufacturers have successfully used ROI technology. It has the added benefits of being non-contact, non-destructive, non-radioactive and intrinsically safe, as well as possessing the ability to measure applied coatings in both wet and dry forms.
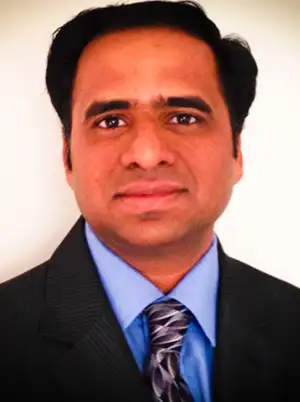
Vivek Komaragiri, chief technology officer at Sensory Analytics (Greensboro, NC), holds a Master’s degree in Physics from North Carolina A&T State University and a second Master’s degree in Electrical & Computer Engineering from Mississippi State University. He has led the technology and IP development efforts for SpecMetrix Systems for more than 15 years. Vivek has broad educational background in optical physics, spectroscopy, software and electronic instrumentation and extensive experience with advanced optical-coating and thickness-measurement technologies, and holds numerous patents. He can be reached at 336-315-6090, email: vivek@specmetrix.com, www.specmetrix.com.