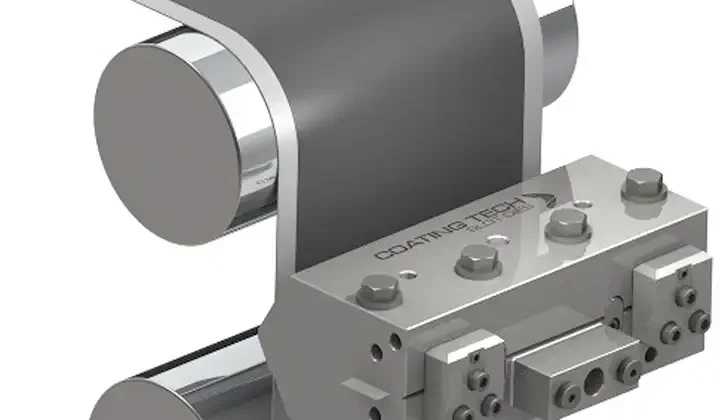
By Mark Miller, CEO, Coating Tech Slot Dies LLC
Something so simple shouldn’t be complex. When you think about water, it seems abundant and clean; readily available; and simple, clear and overlooked. But take notice of this complex industry. As viable drinking water has become more necessary at larger volumes, purifying the existing supply has developed a higher demand for water-filtration membrane technology. As membrane technology advances, so too does the need for precision casting and coating technology for the roll-to-roll (R2R) -manufactured membranes. This multi-step process provides ample development into thin-film coating technology and rheological understanding.
Introduction
One of the most interesting end-use categories for roll-to-roll processing is membrane production. Well known for water filtration, the process applies to liquids, gases, biological applications, pharmaceutical products, energy-storage solutions and carbon-capture products. Where else can you combine fluid coating onto a substrate, water-bath reactive chemistry and tensioned-web-over-slot-die (TWOSD) coating? By reviewing this process, we can understand many features of coating technology. Let’s look at the overall process and then dig a little deeper.
In the world of isotropic (uniform cross-sectional area) membranes, there are a few methods of construction, but the most common is phase-inversion, microporous manufacturing. In this process, a polymer film is cast with a slot die while the polymer is in solution with a solvent. The hydrophobic film then is immersed in a non-solvent (water), which causes the polymer to precipitate to form the porous membrane.
The best way to ensure a uniform cross-sectional area of the membrane is a uniform cross-web profile from the casting equipment. Cross-web profile control is a function of the pump precision and the slot-die manifold’s fluid-flow design. Because most membrane-polymer solutions are low-percent solids, the fluid flow typically is based on Power Law mathematics. However, as polymer and process development improve to develop better economies of scale, the polymer functionality will take over the fluid-flow considerations, and more complex mathematical models will be needed to understand flow. Anisotropic membranes also can benefit from uniform cross-web profiles from the casting equipment, with the main difference being that the pore sizes are not uniform within the membrane itself.
In addition to the isotropic and anisotropic formation, membranes can be considered organic or inorganic based on the polymers used in the dissolution process. Typical organic membranes are made with synthetic polymers – polysulfone (PS), polyethersulfone (PES) and polyvinylidene fluoride (PVDF) – while inorganic membranes include ceramics and other non-polymeric materials. Typical solvents are organic in nature – dimethylformamide (DMF), N-methyl-2-pyrrolidone (NMP) and dimethylacetamide (DMAc).
The same scientific principles apply
It doesn’t matter if we are looking at RO-Reverse Osmosis, FO-Forward Osmosis, NF-NanoFiltration, UF-UltraFiltration or MF-MicroFiltration, the same scientific principles apply. Regardless of the nominal pore size required, proper coating and casting parameters can provide a quality pinhole-free membrane. The main difference between the different pore sizes developed are the polymers used that precipitate at different rates. Of course, the different polymers lead to different rheological behavior. These viscosity vs. shear-rate data are critical in designing and manufacturing the slot-die equipment for membrane production, not only for cross-web caliper control but also morphology (surface roughness) of the final polymer membrane. The internal manifold design needs to control the fluid flow of the polymer to develop a precise cross-web profile, which will lead to a uniform cross-sectional area membrane.
While membranes have an overall unusual process, the unit operations follow a similar path to other roll-coated products – membranes perform better the thinner they are coated. In water-filtration membranes, this optimally thin cast thickness allows for higher water flow (or flux), reducing the energy required to push water through the filtration process. However, as the membrane is cast-thin, more imperfections are recognized.
Imperfections rise to the top
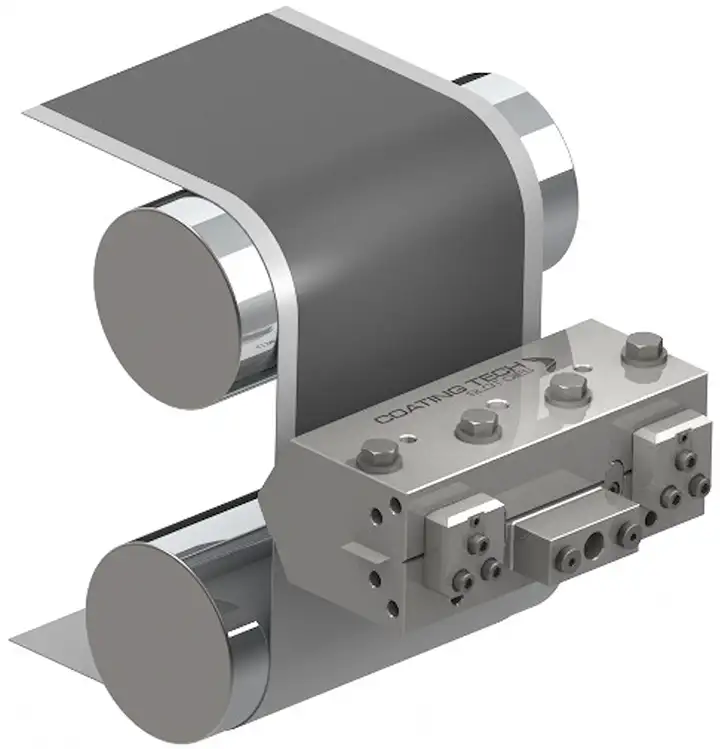
Just imagine a gel within a bathtub. Like a thick casting or coating, the gel is buried at the bottom when the tub is full. As you drain the tub, you start to recognize the gel, and it eventually peeks up above the water line. So it is when you coat or cast thinner. Imperfections will rise to the top.
With water-filtration membranes, thicknesses can approach the molecular level, so variation in the molecular weight of the developed polymer can be recognized. These imperfections develop pinholes, which definitely are an issue when you are trying to control flux.
TWOSD method as a solution
So, what do you do when you need a thin casting, but the flaws stick out and cause problems? You can’t just let these holes persist, or the membrane will fail. The goal needs to be thin casting with zero holes. This is accomplished by tensioned-web-over-slot-die (TWOSD) coating to control flow evenly across the substrate (see Figure 1).
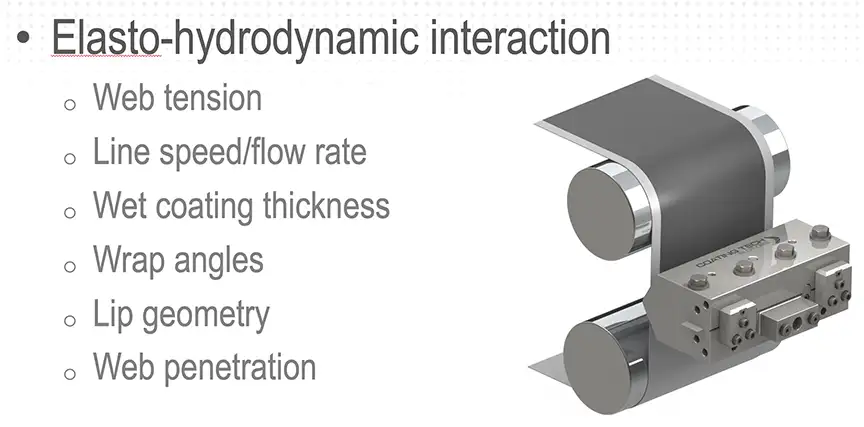
As you can imagine, casting a membrane in a free state, thinner and thinner, becomes tricky and complicated. What is done in practice is a carrier substrate (a base layer of woven or nonwoven fabric) carries the membrane through the process. This secondary, porous substrate then supports the strength of the cast membrane. For standard roll coating in a proximity arrangement, the coatweight is limited to 12 microns wet coating or thicker. The TWOSD technique uses the fluid pressure to push the substrate away to whatever wet-coating thickness the pressure can support. This elastohydrodynamic interaction (see Figure 2) allows for thinner coatings than typical proximity coating (see Figure 3), leading to the thinner-coating capability that membranes require with the precision that slot-die coating technology provides.
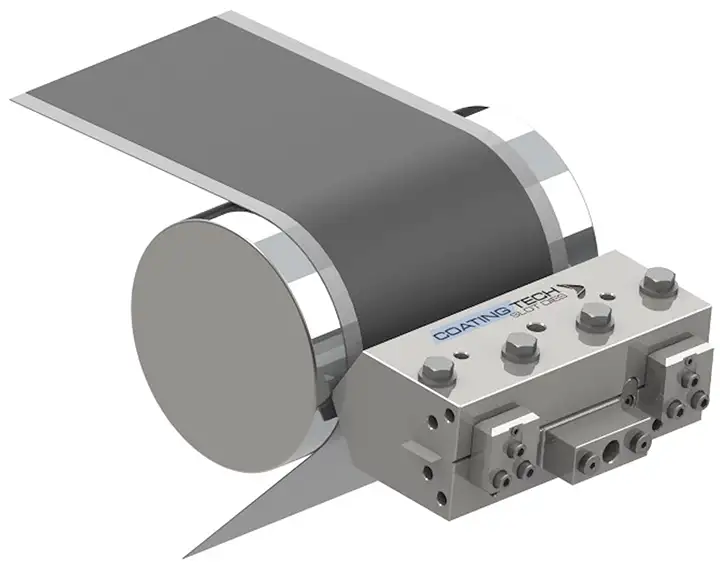
What’s unique and fascinating about membrane casting is that the cure typically is not the same as curing of fluids in most roll-to-roll coating systems. Like other curing methods, the phase-inversion process is the rate-limiting step in the casting process. However, it has the additional consideration of roll processing within a water bath. In membrane manufacturing, the cast fluid forms a thin film by reaction with another fluid in a tank. The resulting polymer matrix thus is the complex sheet that is a membrane.
But the fun doesn’t end there!
Besides needing a thin membrane for increased fluid flow and reduced flaws for pinhole-free operation, membranes need to stay clean longer. Fouling, or the clogging of the membrane over time, can be reduced by adding functional coatings to the water-filtration membrane. These functional coatings repel the items that would stick and cause the membrane to clog through hydrophilicity, roughness reduction and static charge, allowing water to pass through the membrane. In both the casting and coating steps, polymeric formation in-process is presented and shows how reactive chemistry can occur before, during and after the coating process.
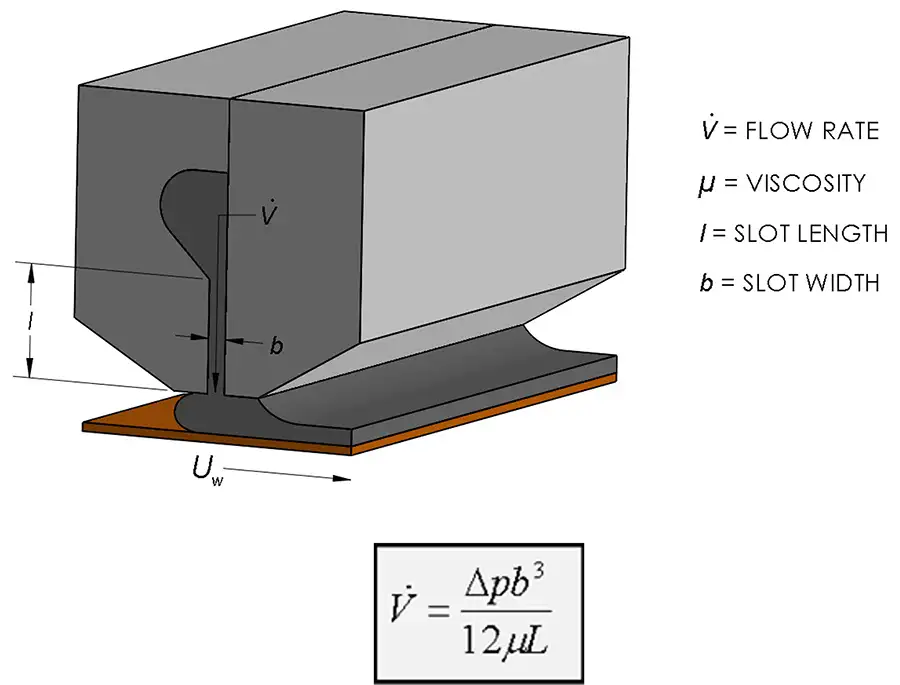
After the wound material has been cast and developed through reactive chemistry in the water bath, we need to unwind the roll to further provide functionality with direct slot-die coating in a proximity arrangement (see Figure 4). These additional coatings typically are coated thicker than the casting steps, allowing for the proximity coating technique (see Equation 1). The process engineer and operator need to be aware of potential issues associated with wet-on-wet coating, including corrosion, liquid/liquid surface-tension issues and tension control of the substrate in wet conditions. This includes process controls and material of construction decisions for the equipment.
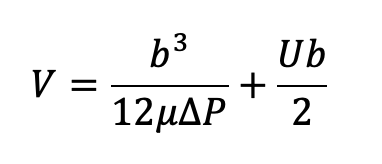
Conclusion
Ultimately, coating technology provides the science behind improved membrane filtration results, including higher water flux, excellent resistance to damaging media and even rejection of salt in desalinization treatment. Membrane-process technology also can provide insights into other coating techniques and systems. As purified water standards have become more stringent, we need to continue to work on improving the precision of the equipment, the robustness of the processes, and understanding of slot-die coating and casting for improved product performance.
Mark Miller, CEO of Coating Tech Slot Dies LLC (Eau Claire, WI), holds a Bachelor’s degree in Chemical Engineering from the University of Wisconsin-Madison, a Master’s degree in Polymer Science and Technology from Lehigh University, and a J.D. from Hamline Mitchell School of Law. He has worked at 3M Co., and Coating Tech Slot Dies, and is a frequent presenter at AIMCAL R2R Conferences. Mark can be reached at 715-456-9545, mark.miller@slotdies.com, www.slotdies.com.