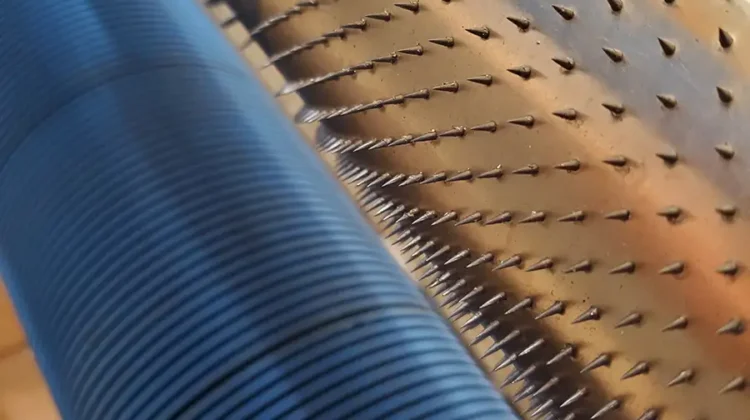
By Craig S. Jackson, Vice President, Stewarts of America
Rubber rollers, anvil rolls and pin-perforating rolls are all round, spin and have one purpose in certain web-processing and converting applications, and that is to – colloquially speaking – “poke holes in stuff.” The advantages of quick-change tooling systems for these various rollers can be very significant. Production setup and throughput productivity are maximized, while the chance of damage to the machine, tooling and personnel is minimized dramatically. Quick-change tooling removes guesswork and increases accuracy, while procedural documentation is minimized. Systems can range from tooling that is simple to remove and replace, all the way to fully automated setups that change out with a touch of a button via stored recipes that the machinery remembers for future use. This article will cover how to incorporate such quick-change rolls and rollers into a process.
Introduction
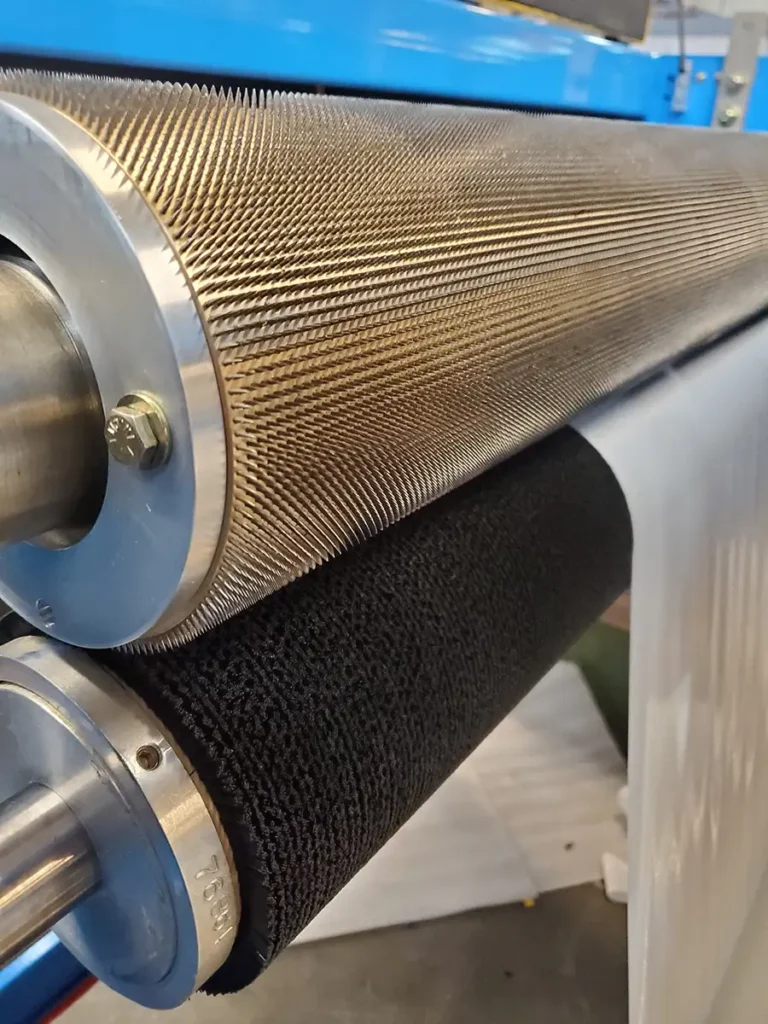
The standard method of perforating typically involves a pinned / needle roller or other tool that pushes against an anvil roll. The web is sandwiched between these rollers, and the pins are forced through the substrate, creating the perforations (see Figure 1). A wide variety of pin sizes and pin patterns are available to create a broad array of hole sizes and pattern specifications based on customer or product requirements. The perforation size and pattern affect the transfer of air, water vapor or liquid through the material. These perforations can be controlled accurately to create a great value-add to the in-process or finished material. Perforations also can be designed to have multiple benefits, such as an easy-tear line that doubles as steam ventilation in microwave-heating applications, or an air-escape hole with perforations laid out in the pattern of a product logo, removing the requirement and cost of printing the logo. The holes created can be nano, micro or macro perforations and can be round apertures, slits or impressions.
To exchange tooling, the roller must be removed by hand or with heavy material-handling equipment, serviced and manipulated on a workbench and then replaced into the machinery. It is a similar process for removal and replacement of the anvil roll. The spare and replacement tooling must be stored securely to prevent damage to the pins and hardware. The tooling also needs to be labeled and categorized if multiple tools are used to make sure that the operator knows where to select the correct tooling for the job. Instructions are needed to set up the tooling for each job-particular specification. Typically, this whole process is performed manually with operators who are experienced with the handling of the delicate tooling.
Applying automation into the process
How to incorporate automation into the process has been answered in multiple ways for perforating technologies, with graduations of options to meet varied budget and operational requirements. There are basic (manual), intermediate (semi-automatic) and advanced automated (fully automatic) options available. These quick-change technologies also may be combined with other automation methods to make the process truly hands-free for the machine operators.
Typically, perforating-tooling changeouts at room temperature can take 30 mins to an hour. Heated perforating systems can take up to 12 hours to cool, and then must go through the “30-mins to 1-hour” changeout. The solution? A multi-roller quick-change system, specially engineered so that it can be used with both room-temperature and heated systems. The quick-change tooling even can be used with applications that are independently driven and matched to the system speed. The tooling changeover time drops to less than 30 secs, even with heated applications.
The quick-change can be varied in size and number of tools mounted to the unit. Many of these systems also can be engineered to allow removal of the inactive tooling while the active tooling is running, saving even more downtime. For the manual option, a hand crank with a low-ratio gearbox helps keep things simple, easy and economical. For the semi-automatic option, an electric motor is included so that tooling can be changed out with the press of a button. Sensors are mounted to the unit to detect which position of the quick-change system is active. For the fully automated option, the unit comes with a touchscreen that has an animation to show which tooling set currently is selected and what tooling sets are available. A barcode reader may be integrated into the HMI. The operator simply scans the barcode on the product to be perforated, and the correct tool set automatically is activated into place. The HMI can monitor tooling use and wear, and an alarm can be set to alert the operator when the tooling requires cycling or replacement.
Product and process-specific recipes
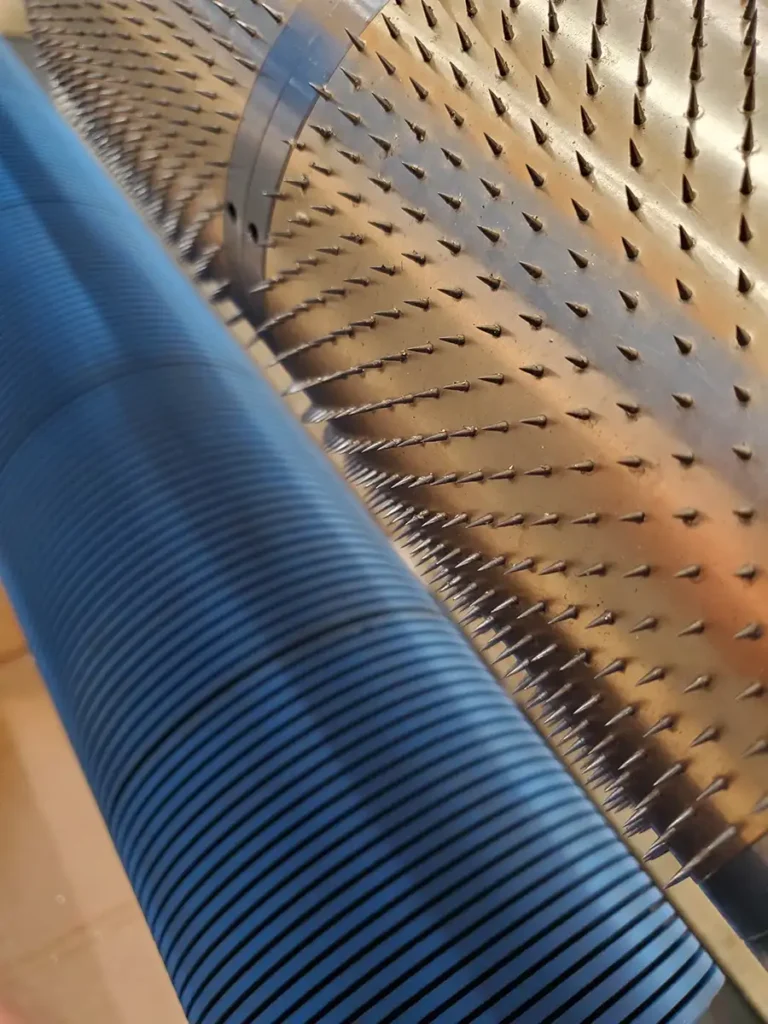
This automated selection, combined with a recipe system that automatically sets penetration depth of the pin into the material, gives the operator all the parameters he or she needs to duplicate a setup. A servo-drive system is optional to accurately control penetration depth of the pins. If a heated system is used, the operational temperature may be one of many remembered parameters and, to move the automation even further, vision systems are available to interact with the perforating unit’s servo-motor system to monitor and adjust on-the-fly the size of the perforations being made.
Nano, micro and macro perforating often requires different anvil rollers to be used with the perforating tooling (see Figure 2). These can consist of brush rollers, felt-covered rollers, rubber rollers, silicone-covered rollers or grooved rollers. These too can be placed on a quick-change system for fast changeouts. Often, because anvil rollers will wear in spots, the quick-change option allows the unit’s components to be rotated out on a timed basis so that a fresh area of a roller can be used against the tooling, ensuring optimum and repetitively accurate hole sizes. Such systems also may be used with vertical and hole-punching applications.
Conclusion
A rapid return-on-investment with quick-change systems is almost assured. By adding the reduction in man-hours required to change over the tooling, the storage required, the reduction of errors the system prevents, not to mention the increased quality of the in-process or finished product seen, the reduced wear and tear and damage on the tooling and machinery components, converters will see the benefits quickly outweighing the costs.
Submitted in partnership with Finzer Roller, Inc. www.finzerroller.com.
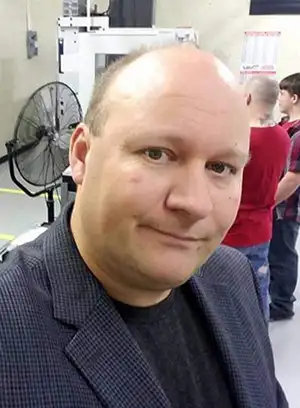
Craig S. Jackson, vice president of Stewarts of America (Simpsonville, SC), holds degrees in General Engineering, Atmospheric Physics and Computer Science. He has 22 years in the converting industry, is a US Air Force veteran and serves his local community as a South Carolina Police State Constable. Craig also serves as an advisory board member for Greenville Technical College (Greenville, SC) and the Golden Strip Career Center (Simpsonville, SC). He can be reached at 864-967-7085, email: Craig@StewartsofAmerica.com, www.stewartsofamerica.com.