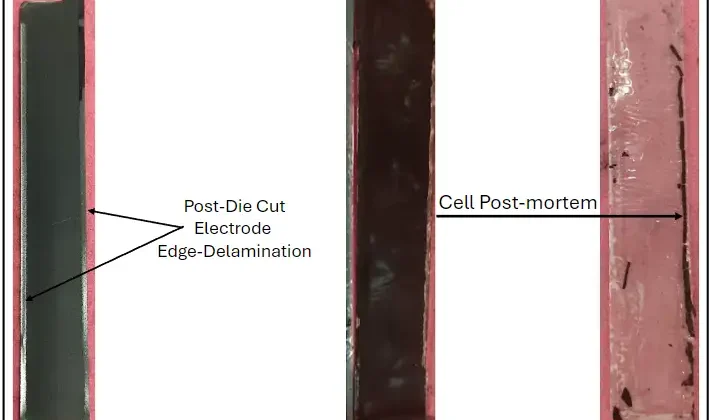
By Swapneel Kulkarni, Ateios Systems; Dr. Kevin Barry, Ateios Systems; and Joe Sampair, Mathias Die Company
Battery electrodes are made by roll-to-roll coating a composite slurry of several chemicals onto a metal foil. These films then are cured, calendered, diecut and assembled into a battery. Ateios’ RaiCure process, using PFA-free solvents and energy-based curing, is said to boost substrate adhesion by 3x compared to traditional PVDF-based electrodes. Despite the improved substrate adhesion, the diecutting process can cause delamination, reducing cell performance and causing failures. Collaborating with Mathias Die Company, an efficient diecutting protocol was established, which improved cell quality and capacity by 3.1% and eliminated edge delamination.
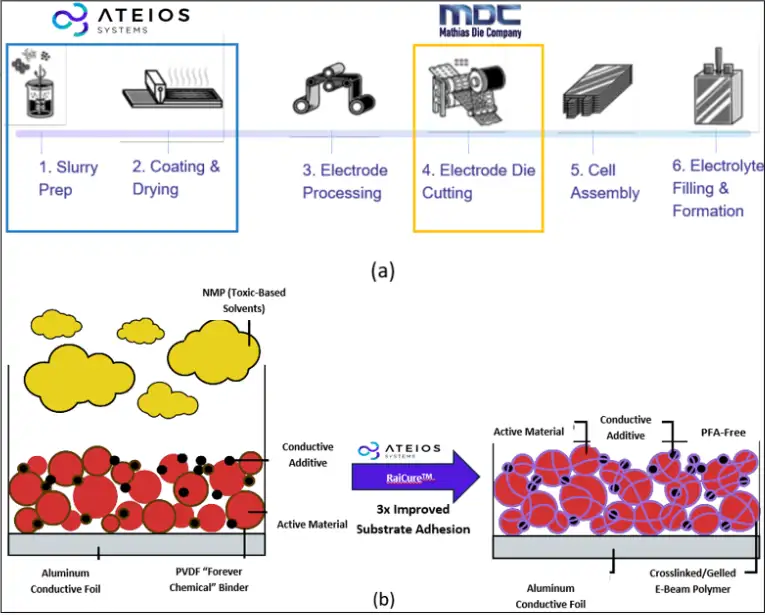
Ateios Systems has developed a scalable, PFA-free electrode manufacturing process called RaiCure for high-energy density, low-carbon footprint batteries. This novel method, hereafter referenced as RC, enables mass production of next-generation battery solutions by incorporating advanced materials. Traditional battery electrode manufacturing involves coating a metal foil substrate with a composite “ink” of active materials, conductive additives, PFAs-containing PVDF binder and toxic solvent. The wet film then is dried in long thermal runners to remove the solvent, which must be recovered due to environmental concerns [see Figure 1 (a)]. In contrast, RC eliminates toxic solvents and PFAs by using an electron beam (EB) system with EB-curable polymers to create electrodes.
The newly developed process acts as a drop-in solution to existing lines, offering material-level benefits and optimizations for scalable manufacturing. Like the traditional process, an ink is formed, but RC replaces PFAs and solvents with EB-curable polymer binders. Instead of thermal drying, the wet electrode is exposed to an EB emitter to crosslink the polymers and form a final film [see Figure 1 (b)]. This faster process reduces costs by $8 million per year, decreases the carbon footprint by 250,000 tonnes annually and maintains electrochemical performance comparable to PVDF-based electrodes [1,2].
Electrode substrate adhesion
A key advantage of battery electrodes produced using the newly developed process over those from the incumbent process is substantially improved substrate adhesion. To demonstrate this, a 180° peel test was conducted. This test is crucial in evaluating electrode quality and its impact on battery performance. By assessing the adhesion between the active material and the substrate, the peel test offers insights into battery stability. Poor adhesion may result in material delamination, reducing battery performance and lifespan. The test also helps optimize electrode thickness and composition for balancing mechanical stability and electrochemical performance [3].
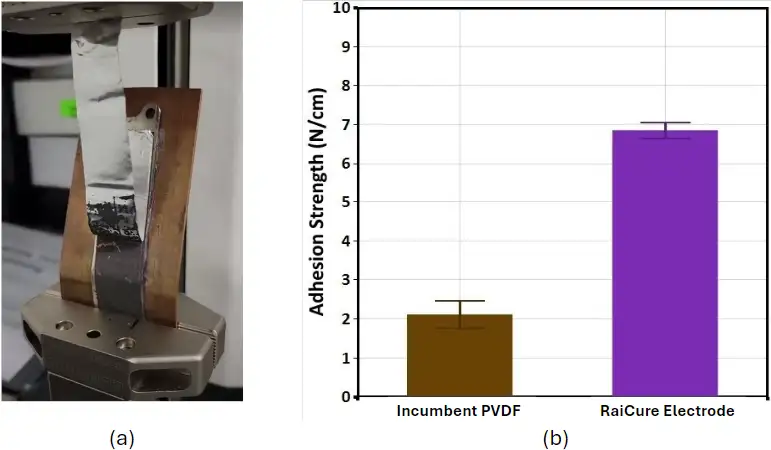
The tests were conducted using an Instron tensile testing machine equipped with a 10N load cell. A typical set-up is shown in Figure 2 (a). A 2 cm-wide-strip of coated electrode was secured to the setup by attaching the uncoated substrate side to a jig using double-sided tape. The electrode was pressed firmly to avoid air bubbles. The lower jig and part of the electrode were fixed in the lower grip of the tester, while aluminum tape was pressed onto the top of the electrode and attached to the upper grip. The upper grip was programmed to move upward at 100 µm/s, peeling the tape off the electrode while the load cell measured the force required. The average force determined the peel strength in N/cm. Tests were repeated for three samples in each category (PVDF and RC), with the results shown in Figure 2 (b). RC electrodes exhibited nearly 3x enhanced peel strength compared to the PVDF electrodes across all datasets.
Scaled battery production
Once electrodes are coated and processed, these electrode rolls are cut into precise shapes for subsequent cell assembly using electrode diecutting methods. The cut electrodes along with separators then are stacked or wound to form the final battery cell structure. Diecutting plays a critical role throughout this process, ensuring precision and consistency in the cell’s components and contributing to the overall quality and reliability of the final product.
Diecutting is vital in producing electrode sheets for lithium-ion pouch cells, recognized for its speed and efficiency. On an industrial level, electrode diecutting can process and convert up to 10 electrodes per second. Despite its efficiency, diecutting presents challenges, particularly with cutting edge-quality and edge-delamination, both of which significantly can impact the performance of the final cell.
During electrode diecutting, a sharp tool mechanically shears the layered electrode material into precise shapes. The active material tends to fracture, resulting in a rough fracture zone, while the metallic current collector deforms plastically before fracturing. The cutting process generates distinct zones, with the cutting edge’s quality being critical to the cell’s performance [4].
Edge delamination, where the active material on the boundary of the electrode separates from the current collector, is a significant concern during diecutting in the battery industry. This issue primarily is caused by the mechanical stresses introduced during the diecutting process, especially in the brittle active material. Delaminated edges can lead to exposure of the current collector and cause the delaminated electrode material to float around and get deposited onto other surfaces within the battery cell. This increases the risk of short circuits and negatively impacts the cell’s overall electrochemical performance.
Industrial challenges
One of the main challenges in industrial electrode diecutting is balancing edge quality with tool wear. Smaller cutting gaps improve the quality of the edge but significantly increases tool wear, leading to higher maintenance costs and production downtime. Research suggests that optimizing cutting parameters is essential to mitigate these issues [4].
The incumbent diecutting process is illustrated in Figure 3 (a-g). These dies have blade cavities precisely shaped to match the desired electrode configuration for battery cell assembly. They are embedded into a wooden board, with rubber foam material affixed both inside and outside the blade cavities for optimal pressure distribution. Each battery cell design requires its own specific cathode (positive electrode), anode (negative electrode) and separator die to encompass all the main components of the battery.
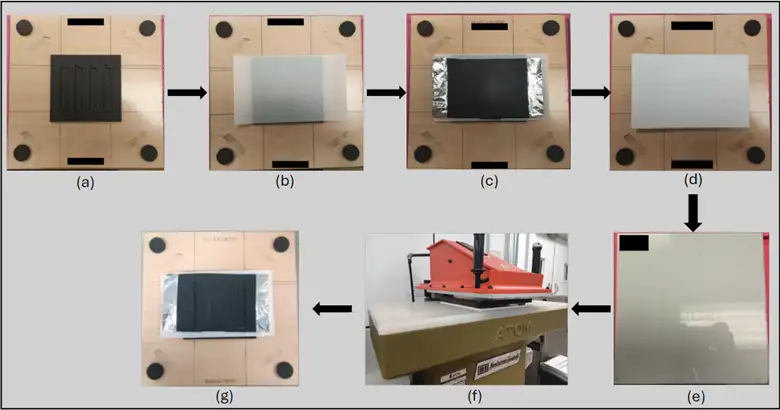
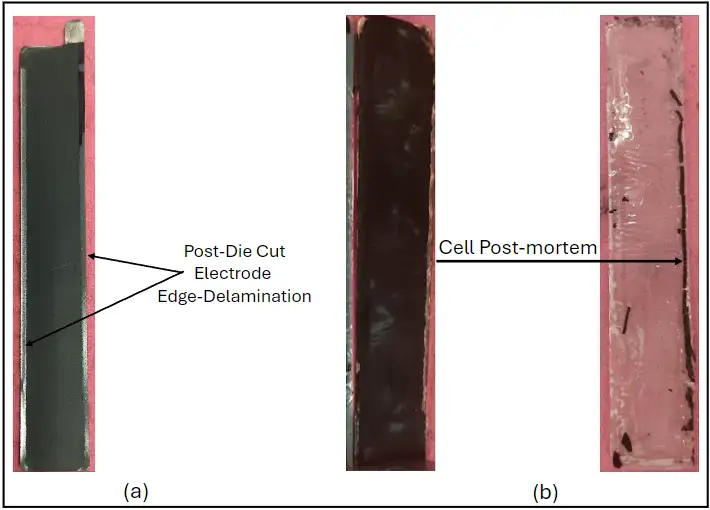
The incumbent diecutting process involves a thin sheet of paper which first is placed directly over the blades and rubber foam to protect the electrode from any impurities on these surfaces. An electrode sheet then is cut from the roll to the required length and positioned on top of this thin paper. A thicker paper subsequently is placed on top of the electrode, followed by an acrylic backing board. This layered assembly is inserted into a punch press to execute the diecutting. Given the high tonnage of the punch press, it is set to a minimal pressure setting to apply the necessary force to the assembly. The resulting cuts are displayed in Figure 3 (g).
As previously discussed, edge delamination of electrodes is a significant issue observed in the industry when using this method. Despite the strong substrate adhesion of RC-based electrodes, significant edge delamination was observed when following the incumbent diecutting process (Figure 4 (a)). Additionally, upon performing internal inspection of battery cells built using electrodes cut with this method, notable delamination of the material from the electrode edges was observed, with particles deposited onto the separator (Figure 4 (b)). As noted earlier, this can lead to several critical issues, including potential cell shorting. To counteract this issue, Mathias Die Company’s technology and diecutting protocols were implemented.
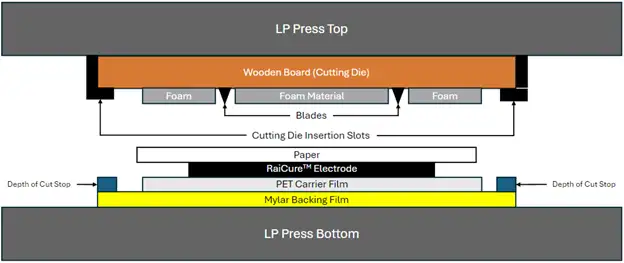
A solution via diecutting
To improve the electrode cut qualities, a pneumatically actuated 4-post press was selected – Mathias Die Company’s LP Press – which provides easy access for set-up and a clear view of the cutting process. New cutting dies specifically were manufactured for integration with the press, with the company optimizing these dies by adjusting the blade-bevel geometry and incorporating custom ejection foams. The electrode cutting protocol (see Figure 5) illustrates the precise electrode diecutting method employed.
In this cutting process, the dies were mounted on the upper section of the press. The electrode was placed on the bed, shielded by a protective paper layer to avoid contact with the die’s foam surface and a PET film carrier underneath to carry the electrode out after diecutting. A Mylar sheet was placed beneath the PET film carrier to prevent the blades from impacting the metallic surface of the press. Cut sensitivity meticulously was regulated by controlling the cut’s depth, achieved with precision metallic stops. These stops ensured the blades effectively penetrated the electrode material while performing a kisscut on the PET carrier film.
All electrode cuts were performed on the LP Press at MDC’s facility, adhering to this established protocol. The diecut electrodes were shipped to Ateios for evaluation. Pouch cells subsequently were assembled using both MDC’s diecut electrodes and those processed using Ateios’ protocol for comparative analysis. The cell assembly process was kept consistent across both builds to ensure a fair comparison.
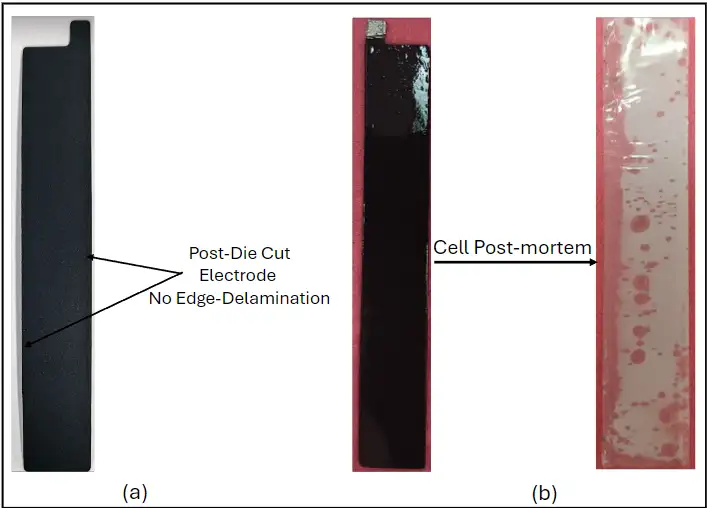
Results
Upon inspection of resulting electrodes, no edge delamination was observed in the electrodes when the new diecutting protocol was implemented (see Figure 6a).
These electrodes were assembled into pouch cells, which were subjected to electrochemical testing. Approximately 70 cells from each category were fabricated, and a series of electrochemical tests were conducted on both sets of cells. Battery cell capacities at a representative discharge rate were compared, with the results shown in Figure 7. A 3.1% increase in cell capacity was observed when comparing the two cell types from each category, with all testing variables held constant except for the diecutting protocol.
Following the electrochemical testing, the cells were disassembled for internal examination (see Figure 6b). No delamination at the electrode edges and no particle deposition on the separator were observed after cycling the cells.
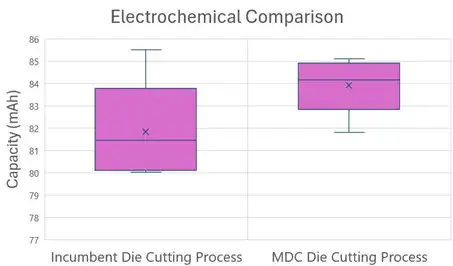
As demand for higher-capacity batteries continues to grow, electrodes will require coatings with increased material loading and thickness. Hence, edge delamination during diecutting may become more pronounced without the implementation of an effective diecutting protocol, potentially leading to larger failures. However, cells fabricated using a combination of the technologies described in this article are anticipated to demonstrate superior performance and achieve higher capacity gains to meet these growing demands.
Conclusion
The novel electrode process described herein boasts key advantages over PFA-based electrodes in manufacturing and yields a 3x higher substrate adhesion. These electrodes, in combination with the diecutting technology and protocols also described, produce electrode diecuts with no edge delamination and subsequently furnish lithium-ion batteries that show increased capacity.
References
- Zhijia Du, Christopher J. Janke, Jianlin Li and David L. Wood. High–Speed electron-beam curing of thick electrode for high energy density Li-ion batteries. Green Energy and Environment, 4(4): 375–381, 10 2019.
- Zhijia Du, C. J. Janke, Jianlin Li, C. Daniel and D. L. Wood. Electron Beam Curing of Composite Positive Electrode for Li-Ion Battery. Journal of The Electrochemical Society, 163(13): A2776–A2780, 2016.
- John Kim. Effect of Electrode Adhesion Strength on Lithium-ion Battery Performance. Technical report, 2020.
- Tobias Jansen, Maja W. Kandula, David Blass, Sven Hartwig, Wolfgang Haselrieder and Klaus Dilger. Evaluation of the Separation Process for the Production of Electrode Sheets. Energy Technology, 8(2): 1900519, 2 2020.
Swapneel Kulkarni is a Battery Engineer with extensive experience in battery manufacturing, slurry development, electrode coating, cell building and electrochemical testing. Currently, he is leading the development of Ateios System’s scaled battery manufacturing and product development through research and innovation in the field of energy storage. Swapneel holds a Master of Science in Engineering with a specialization in Aeronautical and Astronautical Engineering and Management, as well as a Bachelor of Science in Aeronautical and Astronautical Engineering from Purdue University. He can be reached at https://www.linkedin.com/in/swapneel-kulkarni/.
Dr. Kevin Barry is a materials physicist with extensive experience in thin film growth and characterization, battery slurry formulation development and scalable battery electrode manufacturing. He has more than a decade of thin film fabrication and materials characterization experience. Dr. Barry has over four years of direct battery manufacturing experience working at the Battery Innovation Center and currently leads research and development efforts for Ateios. He has received a B.S. in Astrophysics and a B.S. in Physics from Michigan State University, as well as an M.S. and Ph.D. in Physics from Florida State University. He can be reached at https://www.linkedin.com/in/kevin-barry1524/.
Joe Sampair is Business Development Manager for Mathias Die Company, with corporate headquarters in South St. Paul, MN. Employed 38 years with Mathias Die Company, Joe has in the field experience working with OEM and Contract Manufacturers developing tooling and material converting solutions for finished component and part production in the spaces of medical device, automotive, aerospace, electronics, energy, packaging, printing, gasket and manufacturing automation companies. Joe can be reached at 651-289-3461 or www.mathias_die.com.