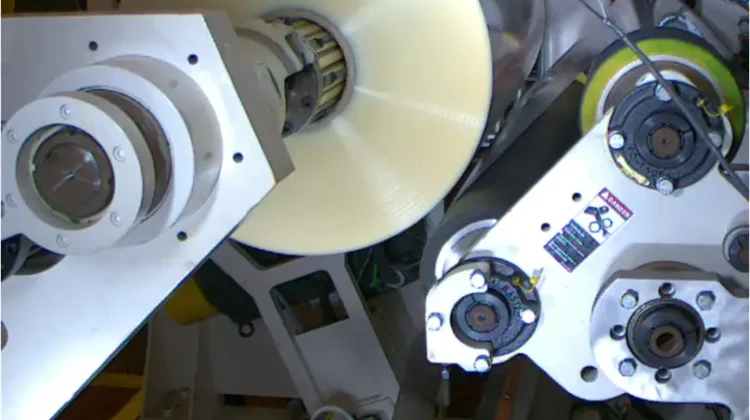
By R. Duane Smith, process mgr.-Web Handling and Specialty Winding, Davis-Standard LLC
Introduction
Consistent unwind splicing and winder transfers are paramount to high productivity on all web-substrate processing lines. This especially is true when manufacturing quality flexible-packaging materials on extrusion coating and lamination production lines. In addition, current industry trends require processing of ever-thinner web materials at ever-increasing production speeds. To meet profitability and output goals within these parameters, it’s important to apply new technology that minimizes scrap and maximizes production uptime.
The impact of a failed unwind or winder transfer on a continuous roll-to-roll (R2R) web-processing line is substantial when you consider that every time a transfer fails, the line must be stopped. Then, the web-material scrap is cleaned up and disposed of, and the line is re-threaded and restarted. Typically, the total time from the web break to viable production is more than an hour from the line’s scheduled run time. Thankfully, smart technologies can optimize the unwind splicing and winding web-transfer process. In addition, these technologies provide the tools to quickly diagnose or, better yet, predict when a critical element’s performance degrades enough to cause missed transfers.
This paper outlines the critical components of unwind splicing and winder transfers with examples of smart technology supporting best practices on a continuous extrusion coating and lamination line.
Understanding the unwind splicing operation
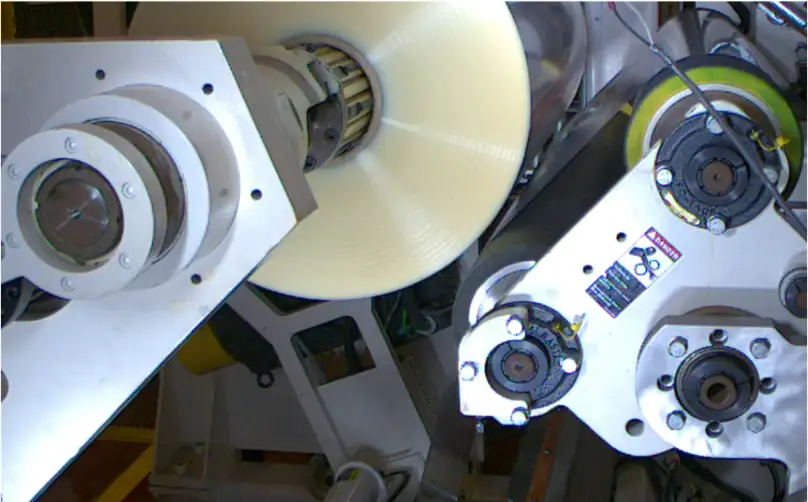
Productivity targets for continuous R2R web processing hinge on the ability to introduce new rolls of web material into the operation with splicing accuracy approaching 100% (see Figure 1). Achieving this efficiency level requires a splicing process that delivers accurate web-transfer tension, reliable pasting and cut-off operations, and precision web-tension transfer control. This makes it possible for high-quality, repeatable splicing at various speeds and roll diameters.
The five steps of a typical unwind splicing operation are as follows:
- Indexing the new incoming roll into the proper pre-paste position to ensure the web is correctly pasted;
- Accelerating the incoming roll to closely match the surface speed of the new roll to the expiring web’s speed;
- Firing the paster roll, so the expiring web makes contact with the incoming roll at 180° degrees from the leading edge of the new roll prepared with splicing adhesive;
- Firing the cut-off knife to cleanly cut the expiring web for the desired tail length; and
- Transferring the web-tension control seamlessly from the expiring roll to the new incoming roll of web material.
Figure 2a-d shows these steps of a typical unwind splicing operation.
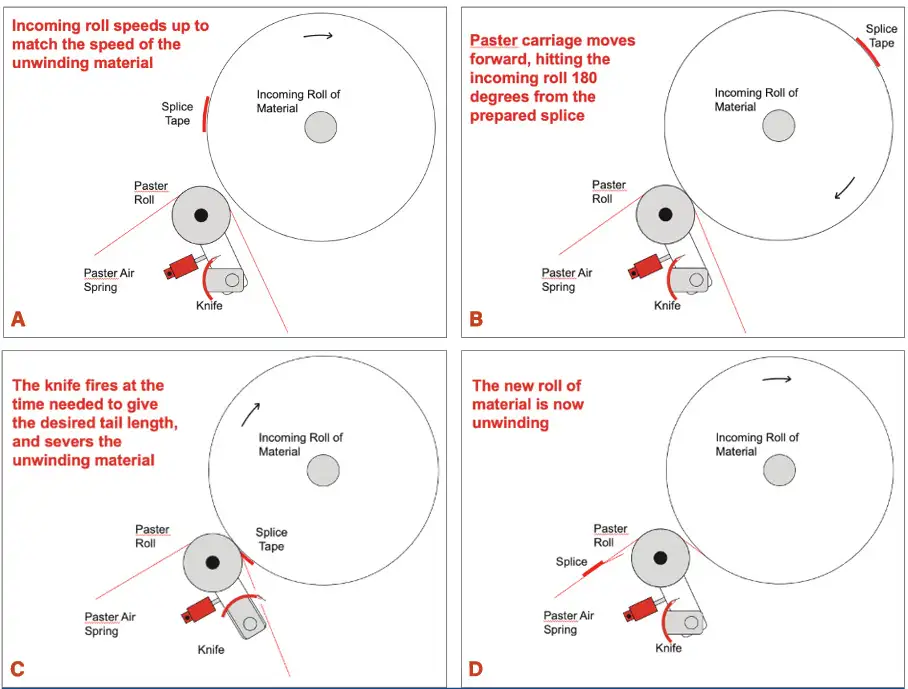
Accurate Web-Transfer Tension: Because thinner (lighter gauge) web materials are in demand, they need to be unwound at lighter tensions during the process. This requires that the roundness of the new rolls of material be monitored to be sure that high-speed unwinding of out-of-round rolls of material does not produce tension upsets that can distort the web or cause web breaks. If the incoming rolls are not concentric or round within a specific tolerance, then the line speed must be reduced to ensure that web-tension variations from these out-of-round rolls after the splice do not cause production problems.
The surface speed of the incoming roll and the speed match of the paster roll also are critical to reduce tension upsets during splicing. The incoming roll’s diameter needs to be accurately measured for best results. Just before the material is unwound from the expiring roll, the new roll must be sped up to match the expiring web’s speed within a tolerance of +/-1%. The surface speed of the paster roll must match the roll speed of the web and incoming roll for a successful splice without tension upsets.
Reliable Pasting Operation: Absolute control of the process from when the expiring web is pasted onto the surface of a new incoming roll is a necessity for consistent splicing. The pasting-roll system must provide a firm and uniform paste across the roll to ensure a good splice. The firing of the paster roll needs to be initiated, so the nip occurs at 180°, (+/-90°) from the splice adhesive on the leading edge of the new roll. Contact just before the new roll’s leading edge can cause the paster roll to bounce over the adhesive. Contact just after the leading edge can break the hold-downs, causing a missed splice. As line speeds increase, timing of the paster roll firing becomes more critical. This especially is true when introducing smaller-diameter rolls into the operation.
To enable consistent splicing for a variety of speeds and roll diameters, the firing of the paster needs to be calculated based on line speed and rotational speed of the incoming roll. This calculation uses the reaction time of the pasting system to predict when to fire the paster so the pasting nip will occur in the correct orientation to the prepared splice. This reaction time can vary greatly depending on the pressure used to fire the paster and the mechanical condition and environment of the paster-roll system.
Reliable Cut-off Operations: After the expiring roll’s web is pasted to the leading edge of the new roll, a clean and consistent web cut-off is needed. The knife cut-off system should be oriented, so the contact angle of the knife penetrates the web opposite the incoming web’s direction. A short tail length ensures the splice will pass through the operation without catching and tearing apart along the web path or causing other web-converting or finishing problems.
The cut-off operation needs to be initiated before the paste has been made. This allows the cut to coincide with the prepared tail at the paste point for a short, controlled tail length. The timing of the cut needs to be calculated based on line speed and the incoming roll’s rotational speed to predict when the webs will be joined together. This calculation uses the reaction time of the knife cut-off system to predict when to fire the knife for a short and controlled tail length. This knife-firing reaction time can vary greatly depending on the pressure used to fire the knife and the mechanical condition and environment of the knife cut-off system.
Web Tension Control Transfer: As soon as the web starts to unwind off the spliced roll, the roll is switched from speed control to automatic tension control. The required braking torque applied to the new roll of material is calculated based on the roll’s diameter and the tension setpoint. As long as the tail length is minimal, the unwind tension-measuring system should detect and provide feedback on only one tensioned web.
This post-splice web tension needs to be monitored to confirm the transfer tension is within the limits of the maximum deviation allowable for the material being introduced into the process. This typically is +/-10% of the tension setpoint. Larger tension upsets need to be flagged to identify the root cause quickly.
Understanding the winder’s roll-change operation
As with unwind splicing, web transfers during the winding process are significant contributors to scrap, downtime and lost production sources. Every time a transfer is missed, the line stops and production is delayed. The web, which now is “gift wrapping” the winder, must be cleaned up, the line re-threaded and restarted, and leveled out to produce a saleable product.
Web transfers to a new core should have little to no web foldback and be free of web-tension upsets, resulting in offsets or wrinkles at the start of the winding operation. Quality transfers also should be insensitive to the speed of the winding operation. The stationary-knife roll changer is recognized globally as one of the best transfer systems for making reliable roll changes nearly 100% of the time, regardless of speed and width. The stationary-knife roll changer provides straight-line transfers with little to no foldback and no scrap at the core. All winder-roll changers, including the stationary-knife system, must be properly installed and maintained to ensure absolute reliability when making quality web transfers onto new cores. The essential components of a winder’s roll-changing operation include proper positioning of the pressure roll and the cut-off knife systems. This is followed by indexing to the correct roll-change position for the core’s outside diameter.
During the transfer, the spindle drive must be accelerated, so the surface speed of the new core matches the incoming web within a tolerance of matched speed to a 1% maximum overspeed. The required roll-change force then is applied to the pressure-roll loading system for a successful transfer. The roll-change force must be sufficient to make a good paste but not so high as to cause a bounce when the pressure roll is fired into the new core.
After the web is cut and transferred to the incoming core, the spindle drive is switched from speed mode to the programmed web-tension control for the winding operation. Usually, the web tension will be tapered when winding at the full roll’s diameter. This is because the web’s tension at the start of the winding on a new core typically is higher than the in-wound tension profile for the winding roll. Also, pressure-roll nip loading must be altered from the transfer pressure to the programmed nip pressure or positioned for a minimum gap when winding in gap mode.
Applying smart technology to analyze performance and predict costly failures
The above summaries provide an overview of the many variables that impact performance during a continuous R2R process. Smart manufacturing solutions, such as this firm’s active-checking vision-based system, help simplify the process. This customizable cloud-based platform uses advanced sensors and control programs to supply real-time data about critical parameters and key performance indicators (KPI) using predictive analytics and alert notifications. Alarm displays are initiated when KPIs are outside the recommended operating range. Proactive monitoring can reduce downtime significantly, promote timely maintenance and improve production-line consistency.
Smart manufacturing solutions for unwind/splicing and winder/roll-change operations also should include high-speed image recording systems that automatically capture complete transfer operations. These real-time, automatic image recordings allow for a quick and thorough analysis if a missed transfer occurs. Recording sequences for quality web transfers provides an excellent tool for training new operators and process engineers. Following are some examples of how a smart manufacturing solution can improve various aspects of roll-splicing and transfer operations.
Continually monitor the roll diameter and concentricity of incoming rolls of material to the unwind. A laser or other advanced sensor can accurately measure the roll and provide feedback to ensure rolls are within the acceptable range. If the measurement is out of range, the operator is warned of this condition immediately. The process line can be automatically slowed down or stopped to make an adjustment and avoid further error.
Improve paster firing efficiency by measuring the time it takes from the command to the actual paste or web cut-off. Reaction times can vary depending on the pressure used to fire as well as the mechanical condition of the paster-roll and cut-off systems. The cumulative average from three previous transfers can be calculated to predict when to fire these components by monitoring reaction times.
Predict issues that impact roll-change performance. Sensors on the unwind and winder can highlight pressure issues beyond the acceptable variation for consistent transfers. This can include monitoring the transfer-paste nips and the programmed nip force for the pressure roll while winding. Variation of the unwinding and winding web tensions during and after a transfer can be observed and compared to setpoints. Alarm warnings are displayed if these factors are out of the acceptable range. In addition, the operator will know what preventative maintenance is needed for specific components.
Ensure the cut-off knives on both the unwind and winder are sufficiently sharp for clean cutting of the web. The timing of knife replacement will vary depending on the abrasiveness of the web material and the speed and diameter of rolls being processed. Smart technology programming tracks the number of times the knife has been fired to predict sharpness, maintenance and potential replacement to avoid transfer issues from a dull knife.
These and other alarm warnings are accessible to operators from existing displays. In addition, due to the collaborative nature of smart technology, all warnings are logged and brought to the attention of supervisors and maintenance departments. As a result, corrective action is taken before variations deteriorate to a point where they cause missed transfers or production of defective products off the line.
Conclusion
Our industry has reached a point where scrap, downtime and lost production due to missed splices during the unwinding and web-transfer process can be prevented. By applying smart manufacturing solutions to your R2R-production lines, you can significantly increase the productivity and profitability of high-quality products. Tools that help avert missed splices assure quality transfer reliability and increased running time, significantly impacting your
bottom line.
R. Duane Smith, process mgr.-Web Handling and Specialty Winding, Davis-Standard LLC (Fulton, NY), is known throughout the paper, film and nonwovens industries for his technical expertise in web handling and winding with nearly 50 years of working in this area. He holds two US patents in the winding field. Smith is the editor of the TAPPI Press ebook, “The Ultimate Roll and Web Defect Troubleshooting Guide.” He has been honored as a TAPPI Fellow and by the Society of Plastics Engineers with an SPE Certificate of Recognition for his contributions to the SPE and the plastics industry. Duane can be reached at 860-650-4992, www.davis-standard.com.