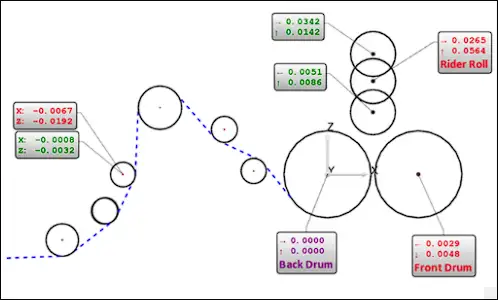
By Joe Kotwis, P.Eng., co-founder, Webineering, LLC
The job of a web-handling machine is relatively straightforward: Deliver the web from Point A to Point B at the specified quality, width and speed. Persistent web-equipment difficulties frequently center around issues with Rollers, Alignment and Tension (RAT). At this firm, we spend a lot of time preventing RAT infestations from processes. Because there are few alignment publications from a process-owner’s perspective, this three-part series will focus on the need for alignment, the precision required and the methods to achieve it.
Editor’s Note: Part 1 of this series, which appeared in the 2024 Q2 issue, focused on the need for alignment. Part 2, which appeared in the 2024 Q3 issue, focused on how and when alignment should be done.
Web-equipment misalignment can lead to web defects that negatively affect the financial metrics of a plant and business. The goal of alignment is to improve those financial metrics. Ensuring the equipment is properly specified, toleranced, designed, fabricated and aligned is the key to achieving that goal.
The third part of this series describes considerations when selecting an alignment vendor as well as the pre-alignment and alignment work that should be considered by the process owner before beginning an alignment job.
Vendor selection
Determining an appropriate vendor is not trivial. It may be the most important decision to be made on an alignment project. The selection should consider your site’s experience and capability with alignment.
Unlike many purchased services, the quality will not be obvious when the crew is complete. The quality of the alignment will become evident by running your most difficult web through the freshly aligned equipment. If the signature walking-diagonal wrinkle or other alignment-related defects appear, the alignment crew may need to return to resolve the issue, while the equipment sits idle (again). This rework can be painful and expensive and is the main reason to ensure you are working with qualified crews. It also may encourage you to be directly involved with the QA process and documentation. Regardless, the decision on which alignment company to work with should be more than just an hourly rate decision.
Vendor selection considerations
Technology: What alignment technology will be used? There are three precision alignment options: optical, laser or gyroscope. They have varying degrees of accuracy and speed.
Construction vs. Alignment Focused: Most industrial construction companies have alignment crews. Not all construction companies have the qualifications to complete precision alignment jobs with reasonable accuracy and speed.
Adjustment:Who is responsible for the adjustments or mechanical ‘moves’ – the alignment vendor or process owner? Is there an advantage to assigning a single team to make the readings and adjustments? Less finger-pointing? More efficiency?
Speed: Alignment accuracy is the most important aspect of alignment. However, the number of rollers adjusted per hour directly impacts downtime. The speed of alignment will depend on many variables. However, for reasonably sized machines, 10 to 30 rollers per 12-hr day per team is common. Large paper machines will be closer to 10.
Report: Will there be a final alignment report provided? Will a rough digital alignment report be provided at the completion of the work? Having a report in hand when alignment is complete can aid troubleshooting at start-up. An example report is included in Figure 1. Red text is ‘as found’ and green ‘as left’.
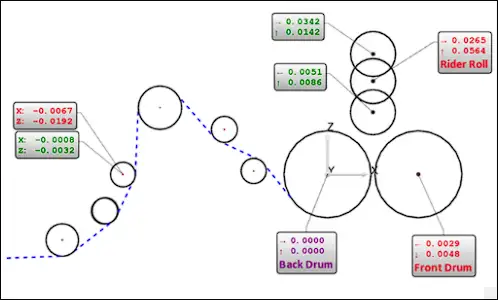
Down Time: Understanding how long the equipment can be down will dictate the size of the crew and will affect the estimate. If the allotted equipment downtime is critical (expensive), then setting up a 24-7 schedule with multiple crews is advisable. Alignment frequently is quoted at 12-hr days, since travel expenses and equipment charges are a significant part of the cost, and downtime should be minimized.
Guarantee: Will there be a guarantee of alignment after start-up? Will expenses associated with alignment mistakes be covered by the alignment vendor? Is there an option to start up the equipment while the alignment vendor still is on site?
Modification/Fabrication Capability: The process of alignment may require the modification of brackets, shim or other equipment components. It can be beneficial if the alignment company brings its own mobile fabrication equipment. Having machining capability can make the job faster and require less involvement from the site representative. If available and beneficial, it can be included as a bid requirement. The alternative may be to have a machine shop on standby to modify components as necessary.
Total Cost: What is the hourly rate of various crew functions? Alignment vendors usually prefer to bid on a ‘time and material, not-to-exceed’ basis, unless they already have surveyed the equipment. Using hourly rate as the only decision variable is ill advised. Quality and speed (total hours) may more than make up for a higher hourly rate.
As Left: If an alignment job cannot be completed in the allocated time, the ‘as left’ values should be documented in the report. It also may be necessary to temporarily leave rollers sequentially out of alignment in order to create a more gradual transitioning path for the web as it travels from an aligned section to unaligned section.
Pre-alignment work
Before beginning alignment, it is recommended to consider the following:
Previous alignment reports and information should be located and reviewed. The alignment values (as left) and difficulties from the previous alignment results/reports should be compared to problem areas of the equipment. Are there significant deviations from work that was done in past reports? What will be different or should be different on the next alignment job?
Walk down the equipment while it is running the thinnest, weakest and tackiest webs. Note any areas of diagonal wrinkles or troughing that may be attributable to alignment. Note the location even if it is not a rejected fold-over wrinkle. If areas are found, notify the alignment technician so additional focus can be applied in that area. It also can provide insight into required alignment tolerance for the equipment and product.
Review relevant information about previous work and critical components of the equipment with the alignment crew. Walk the job down and note any challenges or risks that could be mitigated ahead of time (line of sight concerns, difficult moves, obstacles, safety issues, work area conflicts, etc.). The shutdown scheduler should be included in all areas like this.
Alignment tolerances need to be provided to the alignment crew. This was covered in Part 2 of this series.
Centerline-dependent components are those that negatively can affect product performance if they significantly deviate from the centerline (dies, tenters, mounted rulers, bowed rolls/bars and spreading devices). Most rollers have enough face length that they can tolerate some amount of ‘off-center’ web without falling off the edge of the roll. However, there are many components that will not function well or will create defects if they are off-center. So, centerline-critical components need to be identified and communicated to the crew. Failure to achieve centerline for these components can lead to droop, skew, variable dimstabs and wrinkling. Higher-temperature processes increase the stakes on property variations.
Monuments typically are embedded in the floor along one side of the equipment to establish alignment baseline. If there are no monuments, new ones should be established by the alignment crew before beginning the alignment. Sometimes they are buried under decades of accumulated equipment and debris.
Equipment should not straddle floor expansion joints.
Thermal equilibrium of the alignment equipment can impact the accuracy of alignment. The equipment should be at room temperature prior to shooting. If possible, the alignment equipment should be unloaded the day before to ensure thermal equilibration (especially with extreme temperatures). Thermal stability of the room throughout the shoot also should be considered.
If the process equipment experiences thermal expansion or contraction after alignment, any side-to-side differences negatively can affect alignment.
Rubber rollers should be checked to ensure there is no significant wear or taper across the face of the roll.
Bearings should be checked for ‘feel-able’ movement (slop). If movement is found, it should be resolved prior to aligning that roller.
Identify Nip systems ahead of time and determine if they require tighter tolerances, as discussed in Part 2.
Key components requiring alignment
Alignment is more than just getting the rollers correct. The following is a list of equipment components that may require attention during an alignment job.
Sole Plates make alignment easier and the equipment less likely to shift over time.
Linear rails (or ways) need to be aligned before aligning the equipment that rides on them. Winders, unwinds and other oscillating equipment frequently are mounted on top of linear rails to ensure smooth and accurate control of side-to-side movement for oscillation and edge guidance. Alignment should not vary as it moves side to side.
Pivoting Shafts: When aligning pivoting rolls like lay-ons and dancers, the pivot point should be aligned first. The roller should be aligned only after the pivot meets the appropriate tolerance. This can be challenging if there is no machined surface exposed on the pivot. This approach ensures alignment is maintained through the entire rotation.
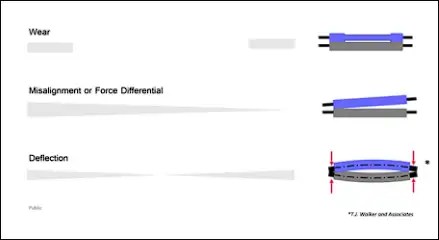
Nipping systems such as tacky roll web cleaners, tension isolation and lay-ons require nip impressions upon completion (see Figure 2). There should be no visible indication of taper across the width, and the nip impression width difference across the width should not exceed 25%.
Thickness Scanning Heads (gauge control) should be aligned to maintain the thread path halfway between the opening across the entire width of travel. This usually only requires a string pulled through the scanning heads.
Camera systems should be set up according to vendor recommendations.
Shear slitting frequently is overlooked during alignment. If you have a product with high quality requirements around slitter dust, edge integrity and width, then spending the time to ensure the dovetail bar or linear rail are properly aligned is worth the time. This especially is true if the shear slitters do not have independent depth adjustment.
Chucks should be level and parallel to each other (according to the specified tolerance). They also should be level and parallel on a given side, although given its short span it is not as critical as being aligned with respect to the opposing side.
Driven Rollers: If driven rollers are moved– CHECK the drive train alignment! The coupling is not there to take up an infinite amount of misalignment. For belted drive systems, ensure the pulleys are re-aligned or at least watch for signs of belt wear (rubber shavings).
Pinning all rollers and critical components is recommended. Some practitioners recommend pinning immediately after alignment, whereas others recommend pinning after running for one to 12 months. If possible, it would be ideal to run the most sensitive products prior to pinning. Pinning can take a lot of time and frequently gets dropped so the line can start up.
Roll pins are acceptable for most applications unless it is a ‘blind hole’, in which case, threaded tapered pins should be used to make removal easier for maintenance. Occasionally, super-precision equipment benefits from straight pins.
Gap winding rollers need to be aligned resting on the ‘stops’ they use during engagement. The ‘stops’ are what the pivoting or linear moving roll pushes against and, therefore, are the critical alignment configuration. Gap rollers frequently are designed to also run in lay-on mode. If you operate in both modes, both conditions need to be aligned.
Mounting structures that support rollers like brackets sometimes can move within the slop between fasteners and mounting holes. If they can move and affect alignment, they should be pinned. For instance, if a pillow-block bearing is mounted to a bracket, the pillow block should be pinned to the bracket and the bracket pinned to the side frame.
Summary
“Unfortunately, alignment is an expensive proposition and can be quite difficult to sell to management. However, I consider it to be the first step in solving registration, wrinkling, web breaks and many other process problems.” – Roisum
Well said. To summarize this three-part series:
- Understand your product.
- Understand your process/equipment.
- Understand your history.
- Understand alignment and the required tolerances.
- Understand the timeframe for the alignment work. How long can the equipment be down?
- Understand the capabilities and limitations of the alignment vendors.
- Understand what you are looking for on a start-up after alignment and hold the alignment crew accountable.
Delivering positive results for any alignment job will depend on the people representing the Buyer (process owner), Builder and Alignment Team.
References
“How can I align my machine?” Roisum, David, Web Works, CONVERTING Magazine, November 1995
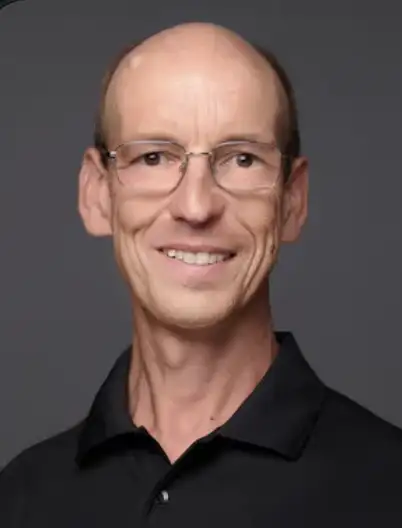
Joe Kotwis, P.Eng., co-founder of Webineering LLC holds a Bachelor of Science in Mechanical Engineering from Clemson University and a Master of Science in Management (Engineering Core) from North Carolina State University. He is a certified Six Sigma Black Belt and professional engineer. Joe retired in 2023 as a Dupont Technology Fellow with 34 years of web-handling experience. Dupont leveraged his skills to solve problems across many sites and customers within industries including electronics, automotive, packaging, NASA and the military. While with Dupont, Joe created and led the global web-handling and web-processes Community of Practice, conducted training and provided consulting. In 2022, he co-founded Webineering, a web consulting and engineering company that helps drive profitability in web manufacturing by leveraging the team’s web-industry knowledge and process-management expertise. Joe can be reached at email: joe@webineeringroup.com, www.webineeringgroup.com.
Alignment Considerations
- The following considerations must be reviewed for safe, accurate alignment.
- Perform safety audits throughout the job.
- Only toleranced, machined surfaces should be used as references during alignment (not painted surfaces).
- Alignment moves should be made as efficiently as possible. For instance, moving a side frame where many rollers are misaligned is preferred vs. moving each roller individually. If there is a mistake in a side frame during the CNC process, the rollers may have to be moved individually.
- Unique or complicated ‘moves’ should be discussed between the customer/process expert, local site maintenance and the alignment crew.
- If drive rollers are moved, the drive train alignment should be checked to prevent drive-train misalignment, belt wear, gear-box failures and associated problems.
- Obtaining a final report after alignment strongly is recommended. The report should include the original roller alignment (as found) and the final roller alignment (as left). It also should include additional commentary describing unique situations, reasons for movement decisions and/or recommendations for the future.
- If possible, following the alignment job, a representative for the alignment crew should be on site for the start-up and initial product run on the machine. The web is the customer and ultimately determines if the alignment is successful.
- When possible, a precision level and tram stick or pi tape should be used to spot check a few or all of the rollers. Any discrepancies should be reviewed with the alignment crew and/or other site experts.