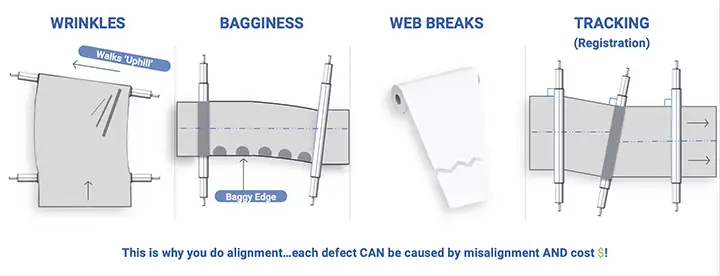
By Joe Kotwis, P.Eng., co-founder, Webineering, LLC
The job of a web-handling machine is relatively straightforward: Deliver the web from Point A to Point B at the specified quality, width and speed. Persistent web-equipment difficulties frequently center around issues with Rollers, Alignment and Tension (RAT). At this firm, we spend a lot of time preventing RAT infestations from processes. Because there are few alignment publications from a process-owner’s perspective, this three-part series will focus on the need for alignment, the precision required and the methods to achieve it.
Why is alignment important?
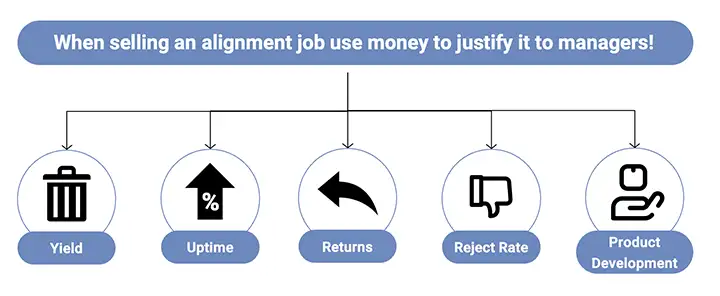
One of the early web-handling pioneers, Herbert Weiss, proclaimed that “Every web-fed machine should be checked for proper level and square alignment to minimize web breaks, baggy edges and web wrinkles.” Most experts also include the impact misalignment can have on edge control (see Figure 2, described below).
Every credible web-handling expert since Mr. Weiss’ publication 40 years ago has echoed versions of the same message. For alignment to be done well, it needs to be 1) financially justified to managers, 2) properly designed into the equipment, 3) properly toleranced by process technical, 4) properly maintained by the site and 5) properly diagnosed by operators/technicians during upsets.
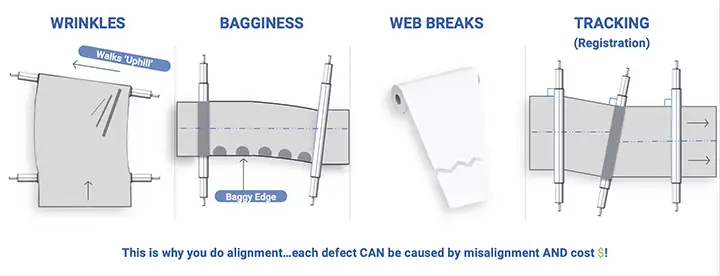
Decisions concerning alignment ultimately are about money and not just the cost of the alignment crew. Further, the “cost of alignment” is more than just paying for an alignment crew. There also are costs associated with taking a sold-out production line down and the related startup expenses. However, the equipment owner recoups the “investment” into alignment via improved equipment performance (aka $). That financial benefit should be evident through improvements to yield, rejects, web/roll quality, uptime, throughput and broader operating window or process capability (see Figure 1). Happily, to resolve any of these items also translates to a more environmentally sustainable line, because there will be less waste to the landfill, more efficient production and less post-processing energy required for the waste or recycle stream.
It is imperative to have new web equipment aligned. If you happen to have an operating line that is not exhibiting any alignment defects, then alignment may not be the best use of your money.
It is not always obvious when a web problem is created by misalignment. The most observable alignment defects in a web are shown in Figure 2; these include diagonal walking wrinkles, baggy edges, web breaks and tracking (or edge wander). It is possible to impact these defects without correcting misalignment by modifying tensions, rerouting thread paths, taping rollers, blowing air under the web, reducing roller friction by wrapping it with Tyvek® and charting sensitive materials away from problem equipment. However, modifying a process to compensate for misalignment can create secondary issues, such as wound-roll defects and contamination. Relying on a secondary knob like tension to “solve a problem,” when the problem is misalignment, can make it more difficult to drive a root-cause resolution.
Case histories
The precision required in alignment means that details matter, and the skills of a practitioner matter. I have seen many unfortunate startups after multi-day outages that delivered walking wrinkles, which required the embarrassing admission to area management and operators that the line still was misaligned (sometimes worse than before). In those cases, there was nothing left to do but wait until the alignment crew returned to resolve the issue while compensating temporarily by adjusting tensions or line speed, modifying thread paths, applying “faux reverse crown” spreader tape, wrapping the offending roll with Tyvek®, blowing air under the web and/or restricting certain materials away from that line. Paying someone to “align” your equipment is not the same as having equipment that is properly “aligned.”
Embarking on an alignment job also may include other complexities like managing tight project schedules, dealing with unforeseen complications (delays), bringing a non-union crew onto a union site and working around poor contractor-safety records. Alignment can be a major project. If your alignment experiences all have been successful to date, then be thankful. My personal journey with alignment has been a good mix of triumph and trouble.
Lay-On Roll Alignment: My first lessons in alignment began in Iowa. I was tasked with rebuilding a slitting/folding machine for a stretchy polyolefin. I wanted to apply what I learned during my formative years at a paper mill – very simply, that alignment is important…so, just do it. I convinced management to commit to (what seemed at the time) a large purchase order for each of the five rebuilt slitters. Precision alignment had never been done at the site, as the stretchy and slippery film tolerated significant misalignment. I felt all eyes were on me (super unlikely, but it felt like that as a 28-year-old). Unfortunately, the line started up with a massive wrinkle on the winding roll. If that was not bad enough, I arrogantly proclaimed to Marty, the seasoned mechanic, “I don’t know what is causing this, but it cannot possibly be an alignment issue.”
After a couple of days of digging my own grave with arrogance, I discovered in fact…it was an alignment issue. Despite the good intentions and money spent, there was a mistake. The small slitter had a 35-in. cantilevered mandrel with a pivoting lay-on roll. During the alignment, the crew suggested binding the lay-on roll to the mandrel with straps and then pin the lay-on arms to the pivot shaft. That made sense to me, and my fate was sealed. I had not yet been introduced to the importance of nip-impression paper but would discover it soon enough. The alignment crew was summoned back to the scene of the crime, resolved the issue and the slitter delivered a 2% reject rate vs. the 9.5% rate prior to rebuilding and alignment.
Lots of Shim: Another example of impacting web quality via alignment involved a vinyl line that had 1.5% yield loss due to web-handling issues (wrinkles and wrap ups in an oven). Following a >$100,000 alignment job, the associated yield loss dropped below 0.3%. The line was found to have up to ¾ in. of misalignment and 1-½ in. centerline offset across >75 rolls, which included many bowed rollers. The alignment crew said this was by far the most shim they used on a functioning line. The only reason the process survived so many years without alignment was due to the elasticity of the film. That stretchiness allowed the film to conform to the misalignment until it occasionally exceeded a critical oven temperature, at which point walking wrinkles and wrap ups appeared.
In both cases (and many more), there was a lot of compensation, accommodation and tolerance for misalignment before the root cause – misalignment – was addressed. In these cases, years of loss could have been prevented if the buyer had understood alignment defects, the builder had built robust equipment that maintained alignment, and a qualified alignment crew had been identified and given the opportunity to align the equipment to the properly defined tolerances.
Who is responsible for alignment and alignment specs?
Ultimately, the buyer is responsible for providing the specifications to the builder and the alignment crew and then holding them accountable for the deliverables in the specification. This perhaps is easier said than done. Builders are trying to stay cost-competitive and are not interested in adding features or making design modifications to their standard product line. Alignment crews also are under cost pressures, and they are encouraged to finish their jobs and leave the site, so the equipment can make money again. Alignment crews and electricians frequently are the last groups working on equipment during installations.
The best way to combat the pitfalls of an installation or existing equipment alignment is to have a well-documented and agreed-upon alignment specification included with the bid package and eventually included as part of the legally binding purchase order. The reason it is the buyer’s responsibility to create this specification is that it makes the bidding fair, and it allows the buyer to own the complete cost of the installation and startup…not just the equipment cost. Why? Because poor alignment costs money (see Part 2 of this series).
Alignment success: Critical aspects
The antidote to alignment problems is a capable team: Buyer, Builder and Alignment Crew (see Figure 3).

There is no need for a process owner to become an expert on alignment, but it is advisable to understand the fundamentals of alignment. There is a good handbook from OASIS describing some of those details. It is a free download here: www.oasisalignment.com/machine-alignment-handbook/. Alignment knowledge can be achieved by building fundamental knowledge on your own or enlisting support from someone that can bridge the understanding between web properties and machine mechanics.
In addition to understanding the general aspects of alignment, the buyer also needs to understand his or her web and equipment needs. The machine builder needs to know how to design and build machinery that is alignment “friendly.” The alignment crew needs to know how to leave the equipment aligned within the tolerances specified.
Relying exclusively on the equipment builder or alignment crew to resolve an issue will not always lead to a satisfying solution. Yes, they designed and fabricated the equipment and set up the tripods, but it is the process owner’s web. Web handling is the interaction between web and equipment, not one or the other alone, and the interaction between the two can make some problems challenging to overcome.
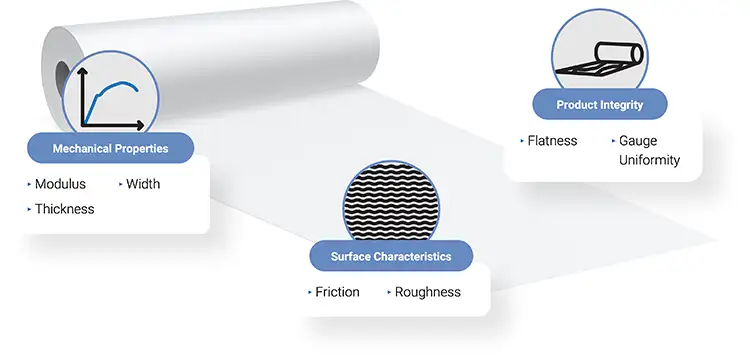
When considering critical web properties that may affect alignment specifications, the properties fall into three general categories (see Figure 4). Understanding critical web properties are important to developing a good alignment specifications.
Summary
Misalignment defects typically manifest as wrinkling, baggy edges, web breaks and tracking, which are tracked in the form of yield, uptime and capability. Alignment costs (including downtime) are expensive. Justifying alignment to leadership requires tying the relevant cost metric to misalignment, because the root cause of downtime or rejects usually is not labeled “misalignment.” Good alignment protocol begins with the initial purchase and design of the web equipment.
Successful alignment will depend on many groups of people, including the site representative, manufacturing area manager/sponsor, equipment supplier, alignment technician and adjustment crew. Alignment will be more effective if the process owner is informed and involved in the alignment of the equipment.
Most of the ~50 alignment jobs I have been part of have resulted in 25% to 100% reduction in the targeted defect. However, getting alignment done right can be a lot more than asking someone with a tripod to “align” your equipment. This three-part series will provide guidelines for the robust and accurate alignment of web-handling equipment from the perspective of the process owner or buyer.
Reference
Weiss, Herbert, “Yearly Machinery Alignment Controls Quality Loss, Cost,” Paper, Film and Foil Converter magazine.
Editor’s Note: Part 2 of this series will cover when alignment should be done and how precisely; and Part 3 will cover how exactly alignment is done, including key components and considerations.
Joe Kotwis, P.Eng., co-founder of Webineering LLC, holds a Bachelor of Science in Mechanical Engineering from Clemson University and a Master of Science in Management (Engineering Core) from North Carolina State University. He is a certified Six Sigma Black Belt and professional engineer. Joe retired in 2023 as a Dupont Technology Fellow with 34 years of web-handling experience. Dupont leveraged his skills to solve problems across many sites and customers within industries including electronics, automotive, packaging, NASA and the military. While with Dupont, Joe created and led the global web-handling and web-processes Community of Practice, conducted training and provided consulting. In 2022, he co-founded Webineering, a web consulting and engineering company that helps drive profitability in web manufacturing by leveraging the team’s web-industry knowledge and process-management expertise. Joe can be reached at email: joe@webineeringroup.com, www.webineeringgroup.com.
Equipment design considerations
The alignment product will be better if alignment is considered during the specification, design and fabrication of the equipment. Some areas to consider are included below:
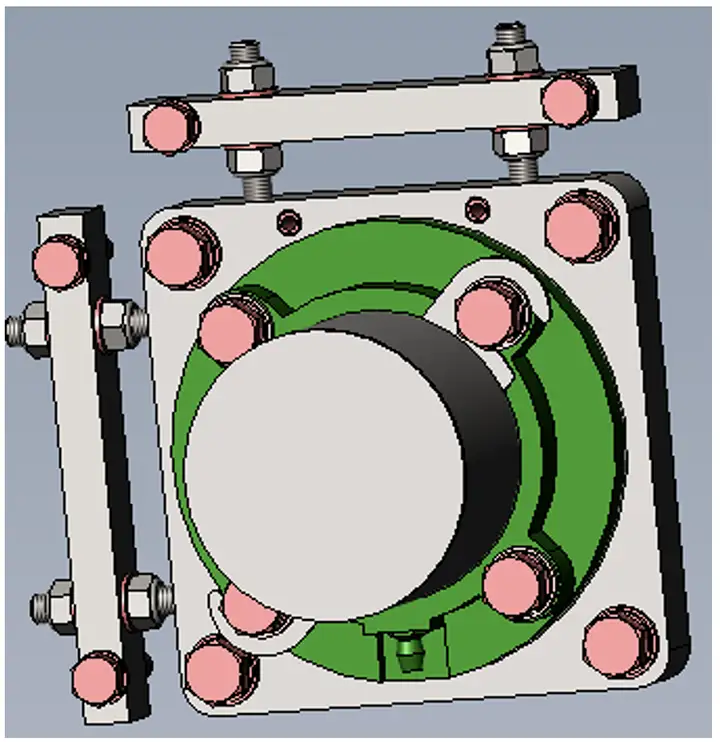
It is imperative to ensure that the equipment is designed with sustainability of adjustments in mind. Proper equipment frame design is foundational to alignment. Considering things like side-plate thickness, cross-member locations, mating surfaces, stress relief and sole plates are necessary to endure vibration, loads and transportation, not to mention all of the things that might happen on the midnight shift. Attention to these details reduces the likelihood of “losing alignment” or having a “racked” frame.
- Speed & accuracy of adjustments can be addressed by providing easy adjustment capability. One example is shown in Figure 5. Proper adjustment capability can dramatically reduce downtime and alignment crew costs.
- Integrity of captured rollers needs to be considered. Frequently, web equipment is a combination of rollers captured in a side frame and others capable of independent adjustment (i.e. pillow-block bearings). Both can work, but each comes down to proper design and execution. The captured rollers depend on the precision of the CNC. Once they are installed, they can be individually adjusted only with a lot of work (i.e. grinding holes bigger). The independently adjustable rollers need to be accessible for ease of movement and replacement.
- Stops that are used for dancers and pivoting gap rolls should be designed for ease of position adjustment.
- Pilot holes for pinning should be provided for each movable component associated with a roller or “alignment critical” component. Pre-drilling holes in bearing housings, brackets and key components makes pinning much faster.
- Thermal expansion can negatively affect alignment if not accounted for. If a roller or equipment will be exposed to temperatures that vary from ambient, then it will need to be designed for thermal expansion without losing alignment. This may be a fixed and floating bearing scenario or a dovetail expansion joint.