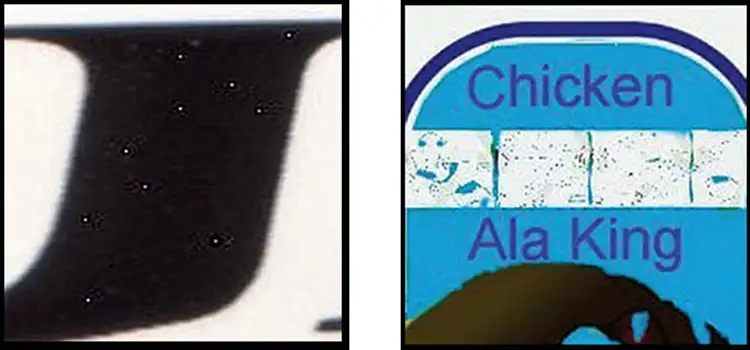
By Jay Downey, coatings business development mgr.-Flexible Packaging, Sun Chemical Corp.
Packaging that delivers strong product protection is essential for meeting consumer expectations that food is as safe and long-lasting as possible. Creating flexible packaging that meets these demands for enhanced food safety and shelf life, as well as achieving cost-effective sustainability improvements, and other benefits associated with lighter-weight packaging, is best achieved through advanced oxygen-barrier coatings. This article looks at the latest coatings and technologies converters can use to create flexible-packaging substrates with the highest levels of barriers to oxygen and moisture.
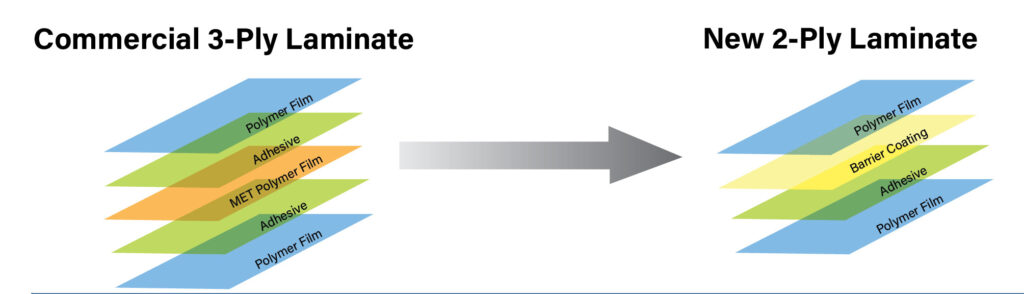
Addressing market trends
The robust flexible-packaging converting industry continues to grow year-over-year, largely because it provides solutions that support several trends important to both brand owners and consumers. These factors include the need to continually improve sustainability and efficiency, reduce waste, ensure the safety and integrity of foods and beverages, and extend the quality and shelf-life of packaged-food products.
At the same time, converters also focus on reducing the total cost of ownership for the equipment and technology they use to produce packaging that delivers on those market-driven initiatives. And, similarly to practically every category of manufacturers, converters and printers face supply-chain challenges, especially shortages – and resulting higher costs – of certain raw materials.
To address these and related factors, converters are exploring ways to consistently reduce the amount and type of substrate materials and consumables used to create packaging solutions. Lightweighting a package using oxygen-barrier coatings is one emerging technology that helps to achieve that goal while maintaining and even extending shelf life. Reducing layers in a package structure by finding ways to remove coatings or resins that impact the environment negatively, such as polyvinylidene chloride, enables converters to do more with less.
Benefits of oxygen-barrier coatings
Oxygen-barrier coatings are highly transparent coatings that bring strong durability for polymer materials. Some oxygen-barrier products include enhancement coatings for aluminum-oxide-coated (AlOx) films and metallized films, in which an oxygen-barrier coating can provide a stronger oxygen barrier and limit flex cracking of the film substrate or lamination. Limiting flex cracking allows those films to maintain their barrier properties while continuing to offer the best barrier protection for the product inside of those films. Barrier adhesives for vacuum-metallized substrates can serve as another solution that replaces standard adhesives. Paired with an oxygen-barrier coating, barrier adhesives can offer different and unusual structures that meet market-driven initiatives while improving shelf-life integrity of the product package.
Oxygen-barrier coatings are water-based (alcohol-containing) coatings that are applied to film during the converting process to improve shelf life by reducing the amount of oxygen entering the finished, sealed pouch, which typically is reported as oxygen transmission rate (OTR). Oxygen-barrier coatings can be applied using flexographic- or gravure-printing presses and/or solution-coating methods – both in-line or off-line.
It’s important to note that these coatings do not yet improve water-vapor transmission rate (WVTR).
Functional coatings enable the next generation of food-packaging technology, design and sustainability. Oxygen-barrier coatings are an integral part of implementing a model of lightweighting, such as replacing the layer of metallized film and one layer of adhesive in a commercial 3-ply laminate with a single layer of barrier coating to a 2-ply commercial laminate to thus produce flexible packaging.
Challenges in moving to a 2-ply laminate are that it may require a change of sealant-web substrate and an off-line coating process in flexographic printing and possibly an in-line process in gravure.
This less-complex laminate structure can reduce the weight of a package by up to 30%, improve laminate integrity for post-flexing oxygen-barrier improvement, extend the shelf life of food and beverage products, and improve recyclability. Two-ply laminates replace films coated with aluminum oxide (AlOx), ethylene vinyl alcohol (EVOH) or polyvinylidene chloride (PVDC) barriers and deliver the same WVTR managed by film-performance changes, same or better OTR, improved recyclability and a barrier to aroma and mineral oil (see Figure 2).
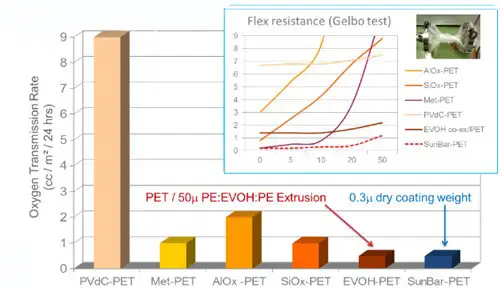
Choosing an ideal oxygen-barrier coating
Determining the right oxygen-barrier coating solution for various applications begins by answering questions such as:
- What is the product to be packaged?
- What are the critical specifications, such as OTR, WVTR, grease resistance or direct food contact (DFC) properties, which the packaging must meet?
- How will the package be filled and sealed?
- Will the packaging line include horizontal or vertical form-fill-seal, thermoform or lidding machines?
- What is the desired shelf life?
From there, the current structure and specifications are reviewed across several processes.
Coating process
- Whether the equipment is set up for gravure, flexo or roll-to-roll applications
- The type of drying and pumping systems
- The durometer of application rollers
- Blade-unit setup and type
- Available gravure or anilox inventory
Current running speed
Print process
- Gravure or flexo printing
- If solvent- or water-based inks will be used, as well as the chemistry of the ink system
- What specific solvents will be used
- Current running speed
Lamination process
- Extrusion, water-based, solvent-based or solventless adhesive
A key consideration that drives decisions about some of the above points is the ability to troubleshoot any potential problems that could occur. Ideally, any issues are identified and corrected early in the process. That begins with ensuring the printing and converting line is set up properly.
Machine-setup considerations for gravure printing
For gravure applications, there are several steps to achieve proper machine setup. These include ensuring that coating-applicator rolls are set at a minimum hardness of 75. This measurement is taken using a durometer gauge. Peristaltic pumps are preferred over gear-driven because the pumping method used to move fluids through a machine minimizes the degree of shear that is put onto the coating. Conversely, the gear creates more shear on the coating and leads to issues, such as foaming and inconsistent coatweight and appearance.
Other machine-setup considerations for gravure printing and coating lines include setting the cylinder at 10-16 bcm, 140-180 line screen, depending on the engraving of the cylinder; starting with new supply and drain hoses; and selecting the proper drying process, which is based on the substrate being used.
To maximize coating handling through a gravure system, begin by ensuring that all rollers, the coating unit, hoses and pumps are free of contamination. Once the coating has been applied to the film and the amount of material desired to run is complete, it now is time to clean up the coating. Drain the coating from the unit back into the pump, then use a 50% water to 50% isopropyl alcohol-blended (IPA) solvent to clean the coating unit and pump. Lastly, use ethanol as a final rinse on the coating unit and pump once they have been cleared of the wash solution.
Machine-setup considerations for flexo printing
For setting up flexographic applications, begin by ensuring that applicator rolls in the machine are set at a minimum hardness of 75, as measured by durometer gauge, setting the anilox roll at 10-14 bcm, 160-180 line screen, depending on the engraving of the cylinder, and, if plates are used, using a hard plate with a stiff, stickyback adhesive. Similar to a gravure application setup where peristaltic pumps are preferred over gear-driven, install new supply and drain hoses. The drying method will depend on the substrate used.
For the coating-handling step in a flexo process, start by ensuring that hoses and pumps are free of contamination. Rinsing with a solvent comprised of 50% water and 50% IPA prior to adding the barrier-coating material is recommended. In addition, ensure that a corona-type surface treatment is used, with a recommended minimum of 0.5 kW; target a coating weight of 0.4-0.5 lb/rm dry; and perform a 610 tape test to confirm adhesion of the coating to the film.
Once the coating has been applied to the film and the amount of material desired to run is complete, it is time again to clean up the coating. Drain the coating from the unit back into the pump, then use a 50% water to 50% IPA-blended solvent to clean the coating unit and pump. Lastly, use ethanol as a final rinse on the coating unit and pump once they are cleared of the wash solution.
Troubleshooting technical defects
While these setup steps are designed to improve effectiveness and efficiency during the process of applying coatings to substrates, technical defects can occur. Identifying and preventing production issues before they happen, or being able to troubleshoot problems as quickly as possible after they appear, will help minimize downtime. Here are four potential defects that may occur during the application of a coating and how to address them:
Foaming: This potential defect leads to foam emitting from the sump and pump, creating microbubbles on the surface of the substrate that lead to a poor OTR. Troubleshooting steps include using clean pump, sump and hoses to ensure zero contamination with coating; staying away from n-propyl acetate as a solvent; using a single blade or plastic blades if running a flexographic press; and using a peristaltic pump instead of a piston- or gear-driven pump (see Figure 3).
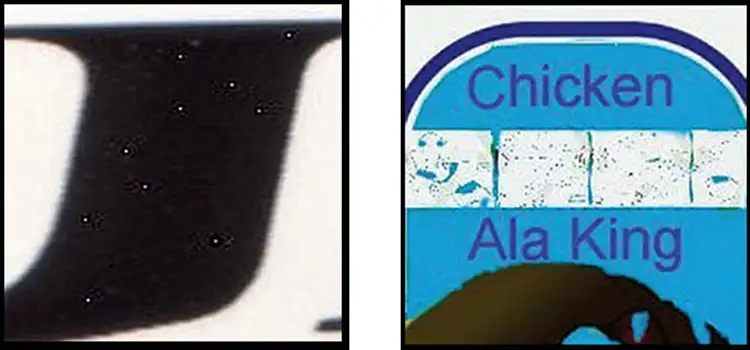
Poor appearance and wetting out on the substrate: This printing defect leads to the lack of a smooth, consistent coating across the web and insufficient OTR results. Troubleshooting steps include ensuring that the corona treater is turned on, the durometer of applicator rolls is at least 75, the coating was properly mixed (two to three minutes on low shear mixing is recommended) and ensuring that the surface energy of the film being coated is at least 38 dynes.
Inadequate or lack of adhesion to the substrate: This defect leads to inconsistent and poor OTR results. Troubleshooting steps include ensuring the substrate has a surface energy of at least 38 dynes through use of a corona treater and that proper drying occurs; don’t focus on adding heat but rather on increasing airflow (see Figure 3).
Rewetting of barrier coating during the lamination process: This common defect leads to a lack of interlaminate bonds and OTR. Troubleshoot by ensuring compatibility between the adhesive and barrier coating and by avoiding the use of acetate-reducible adhesives.
Conclusion
The packaging market today is focused on meeting important market trends, such as sustainability, package integrity and product shelf life. All three of these trends can be achieved using oxygen-barrier coatings on substrates. Oxygen-barrier coatings applied to flexible-packaging films create strong resistance to flex cracking, extending product shelf life and enhancing the quality of the packaged product. Reducing the number of layers in a package further reduces the weight of a package by as much as 30%. The coatings can be applied with standard flexographic or gravure units in a printing press, making it easier for investment without significant overhauls on existing equipment.
Reference
- https://inksta.sunchemical.com
Jay Downey is a coatings business development mgr.-Flexible Packaging at Sun Chemical Corp. (Parsippany, NJ). He can be reached at jay.downey@sunchemical.com, www.sunchemical.com/product/sunbar.