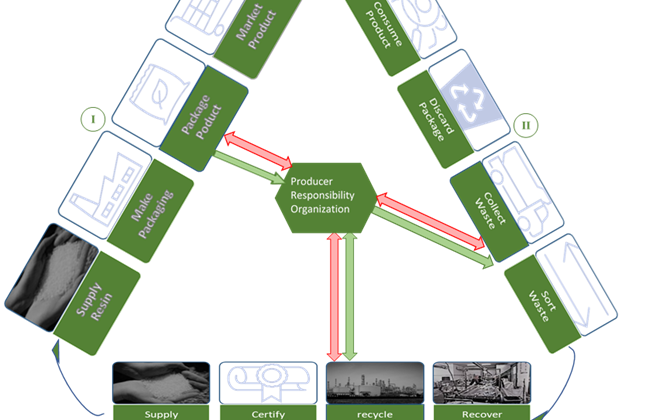
By Tom Dunn, managing director, Flexpacknology LLC
“Sustainable packages” will not solve our plastic waste problem. Empty plastic food packages are a big part of that waste. When today’s bread-bag film reappears in the market as a new bread bag next month, we have an effective “circular” solution. When ground-up, empty bread bags reappear as part of composite plastic/sawdust picnic tables, we will have no new food-grade bread bags. Industry also must make food packaging safe for its contents. Successful circular packaging creates new chemical-contamination risks to food safety. This analysis assesses the size of these new risks, suggests a technical solution and recommends the socio-political means of technology implementation.
Editor’s Note: This technical article is based on the author’s presentation at the AIMCAL R2R USA Conference / SPE FlexPackCon held in October 2021 in Orlando, FL.
Introduction
Single-use plastic packaging is guilty! The charges: “Plastic pollution” kills life in oceans and rivers; it fills up landfills where it pollutes groundwater and public water supplies. Canada already reached the verdict to add manufactured plastic items to the list of toxic substances under the Canadian Environmental Protection Act. The justification for the Canadian rule: Continued production, use and disposal of single-use plastics is unsustainable and prevents Canada from meeting its national and international environmental commitments, and the respected scientific journal, Nature, states, “This bold move should be applauded.” (doi:https://doi.org/10.1038/d41586-021-01701-9).
Other evidence for the prosecution of single-use plastics:
- Fossil fuels produce plastic resins, and fossil fuels are bad.
- Plastic with all of its commercial benefits for packaged goods is durable.
- Consumers dutifully believe that packages with the No. 1-7 Resin Identification Codes (RIC) represent a promise by the plastics industry to actually identify, separate, recover and recycle them.
While plastic “recycling” in the United States spent 25 years debating the obligation of anything that looks like a PET beverage bottle be made of PET, not PLA, PETG, etc., Europe evolved the principle that a circular economy is the optimum social system for resource use. Economic analysis demonstrates that the extraction of virgin resources for manufacturing new goods costs more and employs fewer workers than does the recovery, repair and refurbishment of the existing generation of goods. To realize the savings and economic growth of these findings, EU countries have endorsed Extended Producer Responsibility (EPR) Systems that enable circular use and reuse of goods such as electronics, batteries, tires and light bulbs, and perhaps, in the future, single-use plastic packaging.
Plastic recycling for a circular plastics economy requires “chemical” – or, euphemistically, “advanced” – recycling. The concept long has been expected by the US Environmental Protection Agency, which calls it “tertiary recycling,” and actually practiced for condensation polymers, PET especially. Essentially, chemical recycling depolymerizes plastic polymers, even addition polymers such as polyethylene and polypropylene, into constituent chemicals that then are used to make a new commercial cycle of polymers. Depolymerization facilities can be sized regionally to process mixed-waste plastics from surrounding households and the constituent chemicals they produce transported to existing polymerization facilities that now rely on virgin petrochemicals. In future renewable-energy economies, such a new source of polymer feedstock may well represent a scarce resource.
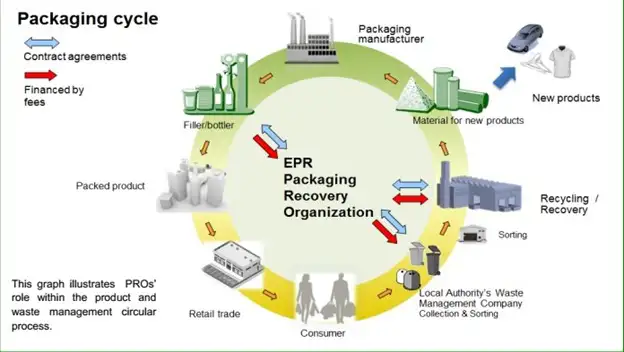
Why plastic recycling has not worked
Figure 1 shows how an Extended Producer Responsibility (EPR) System enables circular use and reuse of plastic-packaging materials. The Extended Producer Responsibility Alliance “EXPRA” developed this diagram. Since 2013, this group of 26 packaging and packaging-waste recovery and recycling systems from 24 countries, which is owned by obliged industries, has worked on a not-for-profit basis. It focuses on providing know-how and recommended best practices to systems on the collection and sorting of packaging waste in individual countries and represents the interests of its members toward European institutions and other policymakers and stakeholders.
A European innovation, EPR represents much more than a “Tax on Packaging” or “Subsidy for Recycling;” it integrates the interests of packaging producers, packaging users, product retailers, consumers, waste collectors, material recyclers and government solid-waste authorities into a sustainable (economic, ecological and socially equitable) set of relationships. These interests balance benefits with costs, minimize pollution, and inherently recognize and correct overpackaging.
EXPRA recognized that the indicated handoffs required for plastic material to move around the full 360° cycle from “material for new products” and back again do not happen as an inherent property of plastic. By linking the relationships with an “EPR Packaging Recovery Organization” at the cycle’s center, EXPRA has demonstrated that its member countries successfully can move materials through the cycle.
Three component sequences
The following analysis breaks the cycle into three component sequences to identify naturally sustainable handoffs and the gaps that prevent handoffs, and then explains how EPR functioning bridges the gaps. The result is circular plastic-packaging use, in which costs balance benefits, opportunity costs of plastic pollution are recognized and minimized, and all participants in the cycle gain. In turn, the central “Producer Responsibility Organization (PRO)” pays consumer utilities that collect packaging materials, and sort-recover-recycle or landfill or incinerate-for-energy. If some of the latter activities generate revenues, they may be shared with the PRO. Contract agreements determine the size and frequency of payments.
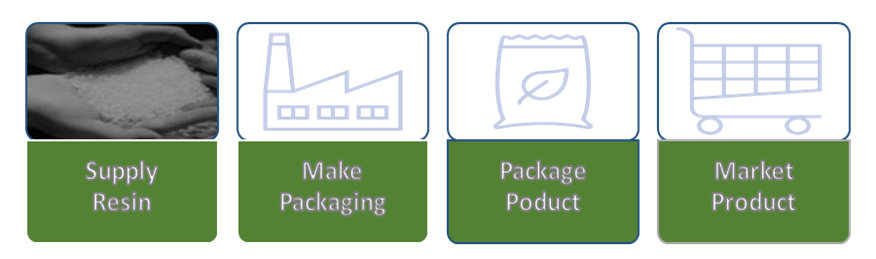
The first sequence (the only one that now exists) addresses the economic system that uses packaging materials for consumer goods with the result that they are offered for sale at retail (see Figure 2).
This sequence has recognized clear advantages in using plastic packaging to replace older packaging formats that use metal, glass and paper. The advantages include lower cost materials, less weight for transportation and storage and convenience, and portability for users. The sale of packaged goods generates funds that drive this sequence with no third-party intervention (In the United States, this sequence generates significant retail sales-tax revenues for state and local governments).
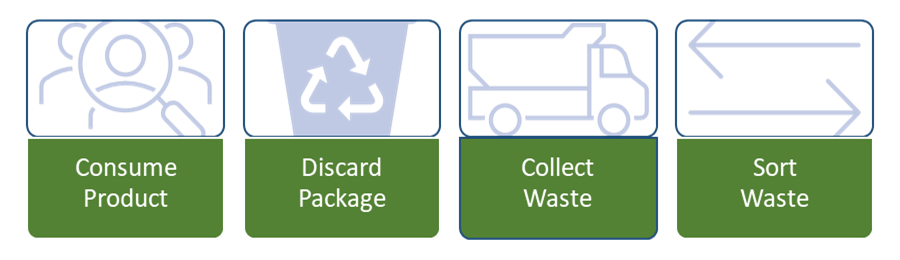
The second sequence depicts what consumers now assume happens (see Figure 3). Upon consuming packaged products, consumers discard the packaging material itself. Consumers do not recycle packaging materials. They do separate those materials that they think are “recyclable,” expecting others to realize that desirable objective. The presence of the RIC Nos. 1-7 indications on plastic containers, whether rightfully or wrongfully, give consumers the impression that a labeled plastic container is “recyclable.”
Taxes and fees paid by households pay for waste collection and handling services. Commercially recyclable containers (e.g. aluminum cans, No.1 PETE and No. 2 HDPE containers with necks, and paperboard boxes when separated and recovered for resale as recycled materials) supplement these taxes and fees. The remaining plastic containers and other improperly sorted materials “contaminate” this source of recovered materials, adding cost to collection and handling. The advantages of plastic packaging enjoyed by the participants in Sequence I cause real disadvantages in Sequence II. In basic economic terms, plastic packaging represents an “external diseconomy.” That is, economic decisions that benefit Sequence I activity impose costs on Sequence II activities.
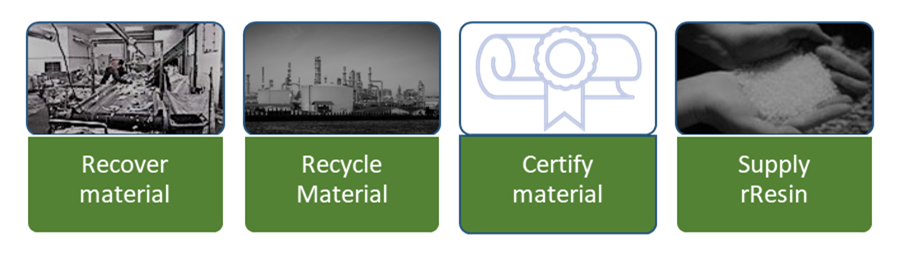
The proposed new Sequence III (see Figure 4) provides the means of recovering the plastic packaging “contaminants” resulting from post-consumer collection and handling services and cycling them back into new packaging needed in Sequence I. As proposed here, advanced (chemical) recycling processes them into a new generation of plastics, indistinguishable from those produced directly from fossil-fuel derivatives. An audit function would certify the post-consumer starting point of the post-consumer resin (PCR) to ensure the integrity of the system.
This new sequence supplements the existing supply chain that delivers petrochemical intermediates to polymerization facilities. It would provide the optimum “circular” re-use of plastics and would qualify all plastic materials as compatible with the sequence for legal labeling as “recyclable.”
The present gap between Sequence I and Sequence II leading to the external diseconomies reflects the diverse timing and mechanisms for funding that consumers, who are common to both, use to finance the two of them. They buy consumer products packaged in plastic materials and enjoy the savings and convenience compared to alternative material experiences. Then they pay taxes and/or fees to simply make the remains of their consumption “go away.” Government regulation, in the form of taxes and/or packaging-material rationing, possibly could force the gap to close; however, market forces would assumedly do a better job of preventing market distortions and causing unpopular personal restrictions.
PRO smooths diseconomies
The alternative to government regulation is the Producer Responsibility Organization (PRO) tasked with responsibility for “internalizing” the diseconomies that now are imposed on post-consumer waste-management activities. This involves imposing a fee on packaged products as they are marketed to consumers. Consumers packaged goods (CPG) companies pay the fees to the PRO using a schedule that reflects the net cost to “manage” discarded packaging after its product use. Customized agreements are made among the PRO and CPG companies, consumer waste-collection and handling services, and material recovery/recycle operations. If necessary, governments could regulate these activities much as they regulate monopoly public utilities.
The revised Packaging Cycle
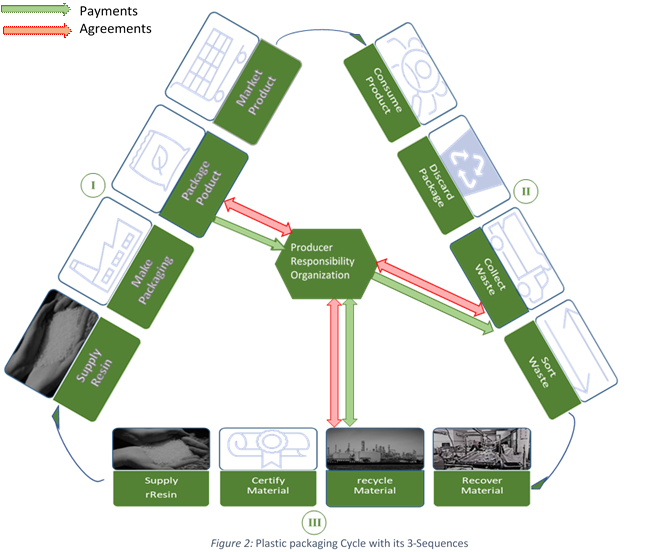
Figure 5 restates the Figure 1 cycle while emphasizing gaps that now separate the three sequences. Realizing the full cycle from “make packaging” and back again requires establishing the feasibility of all elements of (the proposed) Sequence III.
Mid-summer 2020 saw progress for all four elements:
Recover material: A May 2020 research report, Flexible Packaging Recycling in Material Recovery Facilities Pilot, from 56,000 households was prepared for the Materials Recovery for the Future (MRFF) project of the American Chemical Council. It reported 74% capture of flexible-plastic packaging (FPP) in feedstock from curbside collection of residential single-stream recycle carts, minimal (1 to 14%) paper contamination in FPP bales, reduced contamination by FPP in recycled paper bales from 1.5% to 0.4%, and provided a 38% reduction in the QC staff needed to avoid cross-contamination. The report indicated that sustainable markets currently do not exist for the recovered FPP (see next item).
Recycle material: Eastman (Kingsport, TN) introduced its Tritan Renew copolyester, a product that contains up to 50% recycled content derived from the company’s Advanced Circular Recycling technologies. The announcement followed a little more than a year after the company announced its chemical-recycling efforts. In 2019, the company began commercial-scale recycling for a broad set of plastics using its carbon renewal technology (CRT), which handles most types of mixed plastics except for PVC (polyvinyl chloride).
Certify material: GreenBlue (Charlottesville, VA) is working with NSF International, an Ann Arbor, MI-based standards organization, to develop a Recycled Material Standard (RMS) by early 2021. The RMS will attest to the amount of recycled content in products throughout the supply chain for use by both sellers and buyers. The Assn. of Plastic Recyclers (APR), an international trade association that represents the plastics recycling industry, introduced a similar post-consumer resin certification program this year. To support such efforts, the American Chemistry Council’s Mass Balance Certification Principles for Advanced Recycling system specifies requirements for material management within an organization to demonstrate that recycled-content claims regarding materials and products are true.
Supply R-resin: In May 2020, Dow commercialized a new formulated post-consumer recycled (PCR) plastic resin designed for collation shrink-film applications in Asia Pacific. The new polyethylene resin is designed with 40% PCR content, which creates a film with performance comparable to those made with virgin resin.
Chemical recycling (aka advanced or molecular recycling) has received millions of dollars of capital for semiworks and small commercial facilities now that the concept is proven on a pilot-scale. The process has the advantage of providing resin grades identical to those made from virgin petrochemicals. This avoids equipment/process changes in the methods that convert resin into packaging containers and eliminates any need for additional food-packaging clearances from food-safety regulators. The concept does have its critics. The Global Alliance for Incinerator Alternatives (GAIA) (www.no-burn.org) characterizes the concept as “a down stream techno-fix.” Its preference is very clear:
“In a society that urgently needs to transition from an extractive, fossil-fuel economy to a circular one, chemical recycling is a distraction at best. Far more mature and viable solutions are to be found in upstream, zero-waste strategies which focus on reducing the production and consumption of plastic.”
Such opinions snub the results of consumers’ “voting with their dollars,” and CPG companies’ stated intent to make significantly more use of recyclable- and recycled-packaging materials as soon as possible. GAIA’s position on using chemical recycling to rid the world of the waste plastic caught up in ocean gyres is not addressed in its July 2020 claims about “Chemical Recycling: All Talk and No Recycling.”
If this analysis has met its objective to explain why plastic recycling has not worked, it also has verified that restricting chemical recycling capacity will stop EPR from working.
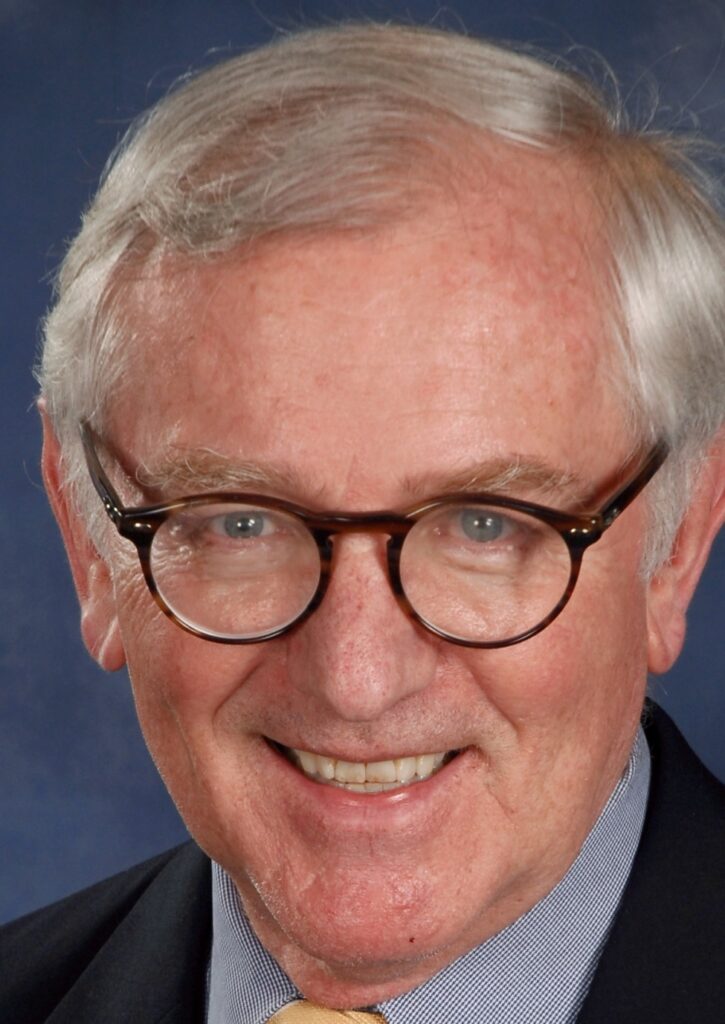
Tom Dunn, managing director of Flexpacknology LLC, holds undergraduate and graduate degrees from Yale University. He is a veteran developer of flexible-packaging products for food applications. His work emphasized materials and how their features benefit packaging users. Tom managed product development and food-safety compliance for 30 years at Printpack and now consults with producers and users of flexible packaging for food and medical products in his current consulting practice. He has received career achievement awards from IFT Food Packaging Div., Flexible Packaging Div. of TAPPI, the Packaging Hall of Fame and the Society of Plastics Engineers. Tom can be reached at 404-376-4866, email: tdunn@flexpacknology.com, http://Flexpacknology.com.