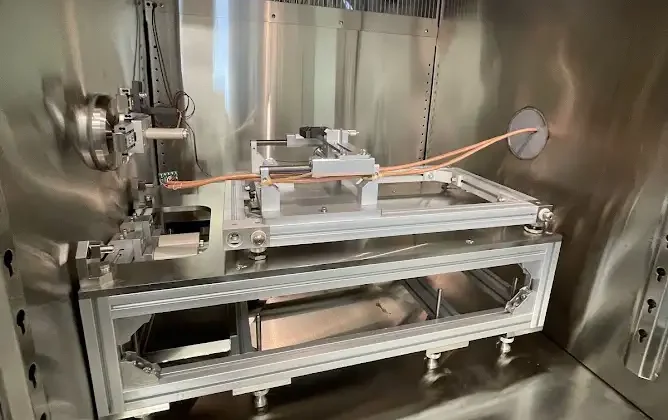
By Eisuke Tsuyuzaki, CEO, Bayflex Solutions
The growth of the flexible electronics industry has established a global market where both device manufacturers and component producers play pivotal roles. However, the industry now faces a critical challenge: moving beyond these initial successes to fully embrace new growth opportunities. Key areas include material robustness, manufacturing complexities, and reliability and cost management.
The flexible electronics industry has reached significant milestones, especially in the realms of printed displays and consumer electronics. These achievements have established a global market where both device manufacturers and component producers play pivotal roles. However, the industry now faces a critical challenge: moving beyond these initial successes to fully embrace new growth opportunities. The path forward involves overcoming several obstacles, including material robustness, manufacturing complexities and reliability and cost management.
Current landscape and challenges
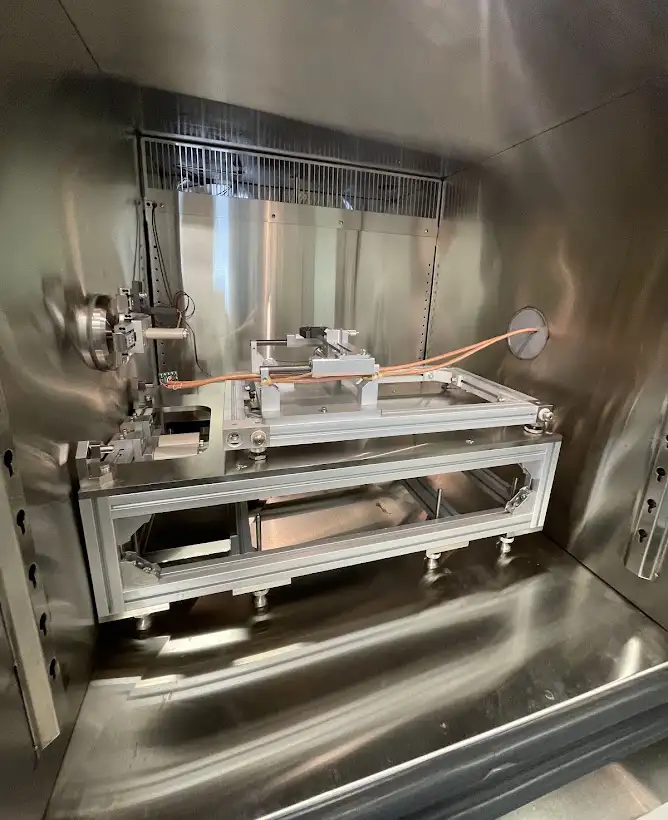
As the flexible electronics sector evolves, it confronts several pressing challenges. While there have been notable successes with printed displays and sensors, the industry must address several key issues to realize its full potential.
First, material robustness remains a significant hurdle. Despite ongoing advancements in flexible substrates, organic semiconductors and conductive inks, achieving commercial reliability continues to be a challenge. For flexible electronics to be widely adopted, the materials used must be durable enough to withstand everyday use and manufacturing processes.
Second, manufacturing complexities add another layer of difficulty. The production of flexible electronics, particularly through methods like roll-to-roll (R2R) printing, requires precise control and optimization to ensure consistent quality. The integration of various materials and technologies increases the complexity of manufacturing, impacting both reliability and cost. As the industry scales up production and diversifies product designs, it must find ways to manage these complexities effectively.
Combined, managing reliability and costs is crucial for maintaining competitiveness. Flexible electronics must meet rigorous performance standards to gain market acceptance. This requires robust testing and qualification processes to ensure that products perform consistently under various conditions (see Figure 1). At the same time, the industry must manage costs related to materials, production and quality assurance to remain competitive. Balancing these factors is essential for driving growth and market adoption.
Driving new growth
To achieve new growth and establish leadership in the market, the flexible electronics industry must focus on several strategic areas.
One of the most critical factors is more compelling pricing. To replace existing technologies, flexible electronics must be offered at attractive price points. This involves not only showcasing design advantages, such as lightweight, malleable and possibly sustainable properties, but also achieving economic efficiencies. By reducing costs associated with materials, production and testing, flexible electronics can become a more appealing alternative to traditional non-flexible technologies.
Enhancing economic efficiency also is crucial. This involves improving employee productivity, optimizing capital expenditures and managing variable costs. Investing in advanced manufacturing technologies, such as automated production lines and advanced quality control systems, can help reduce production costs. Additionally, improving material efficiency and reducing waste are important for achieving cost savings.
Meeting performance and reliability standards is another key area. Flexible electronics must undergo rigorous testing and qualification to ensure they meet performance requirements. Developing robust testing methodologies and standards is essential for verifying the reliability and durability of flexible electronics.
Observations from industry events
Recent industry events have highlighted significant trends and innovations in flexible electronics.
At the Consumer Electronics Show (CES) in Las Vegas in January 2024, there was a notable surge in hardware products that leverage the data-processing capabilities of cloud and AI technologies. Wearables, in particular, showcased a broad application of printed electronics technology. This included:
- Printed Displays: OLED devices and other flexible display technologies are becoming increasingly prevalent in consumer electronics.
- Sensors: A range of thin, flexible, wired and wireless sensors for monitoring vital signs is advancing rapidly.
- E-Textiles: Stretchable components and fabrics with continuous power solutions are emerging as a significant segment of flexible electronics.
This diverse range of products requires various reliability testing methods and performance evaluations. Manufacturers must ensure that their products can withstand real-world conditions and meet the performance standards necessary for commercial success.
At SID in San Jose this spring, the focus on OLED display testing revealed the need for more realistic assessments. While traditional clamshell flexing tests remain a standard practice, there is a growing demand for evaluations that reflect complex real-world experiences. This includes assessing hinge mechanisms and user interactions in a way that goes beyond simple mechanical repetition.
Furthermore, there is an increasing emphasis on wearables designed for harsh outdoor conditions. Historically, testing involved single-use environmental chambers that measured temperature, humidity, vibration and rain. These methods were adapted from automotive and military standards. Many now refer to the US MIL-810H specifications, originally intended for military materials, and adapt them for broader applications. This includes extreme environmental conditions, mechanical shocks, liquid/gas immersion, dust/dirt and altitude, with a focus on both passive (in-situ) and multi-axis movement assessments (see Figure 1).
Advancements in testing and simulation
Recent advancements in testing and simulation are paving the way for more accurate and comprehensive evaluations of flexible electronics.
The introduction of a benchtop multi-roller system in Europe is a notable development. This system supports component or device manufacturers in qualifying their products for roll-to-roll (R2R) production. It helps assess whether final products can endure the rigors of R2R manufacturing before making significant commitments. The system enables manufacturers to evaluate material performance and determine if additional R&D is needed for material selection, thickness, alignment and speed.
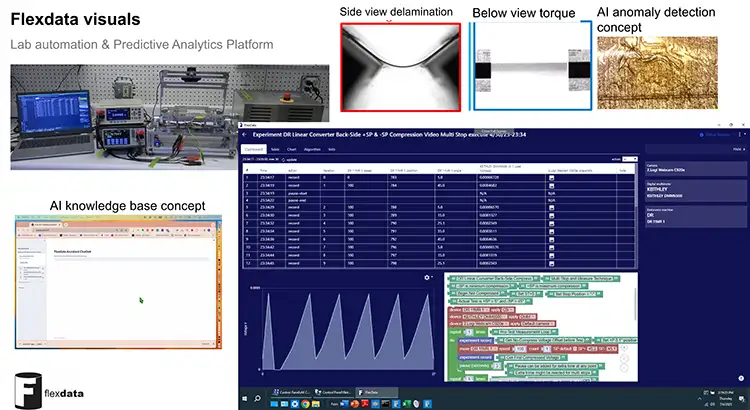
In addition, advancements in mechanical testing and extreme conditions are improving the ability to evaluate flexible electronics. Recent work, supported by SEMI and NextFlex, includes efforts with American Semiconductor and Auburn University to phase in uniaxial mechanical movement testing in extreme temperatures ranging from -40° C to over 150° C. This involves retrofitting legacy chambers with redesigned components to withstand higher thermal conductivity, high humidity and thermal expansion. This testing ensures that materials and components can endure challenging conditions and maintain performance.
Advanced simulation tools are emerging as crucial components in testing flexible electronics. Computer-aided design (CAD) software now allows for the creation of virtual models of devices, simulating stress tests, thermal analysis and fluid dynamics evaluations (see Figure 2). While digital prototyping offers cost savings with multiple simulations, real-world hardware testing remains essential for accuracy and repeatability. Advanced simulation and modeling also are used to ensure that electronic sensors, such as those for audio, vital signs and biofluid status monitoring, function correctly under various conditions.
Integration of imaging systems, including optical, infrared, x-ray and CT, is advancing. These systems capture the evolution of metal fatigue and detect anomalies using AI computer vision tools. By analyzing numerous samples, these tools can identify issues such as metal fatigue and develop more sophisticated reliability models for supplier qualification and commercial licensing.
Enhancing productivity and labor efficiency
Optimizing productivity and labor efficiency is crucial for the growth of the flexible electronics industry.
Addressing the current shortfall in experienced workers is essential. At LOPEC, a proprietary knowledge base was demonstrated, containing client-specific standards and methodologies. This system provides a step-by-step menu of best practices for performing assessments and can be customized for specific operations. It aids in training new recruits and cross-training existing staff, thereby improving overall productivity.
Machine learning practices are being employed to manage the vast amounts of data generated by flexible electronics testing and monitoring. By running numerous experiments, performance decay models can predict and potentially self-correct to preserve product life. Sophisticated data frameworks from multiple sensors, such as resistance, capacitance, temperature, and humidity, enhance the accuracy of failure mode predictions. Additionally, AI-driven imaging systems help detect anomalies and improve product reliability.
Continuous performance monitoring
Continuous performance monitoring is critical for many wearable and medical devices.
For devices requiring high reliability, such as medical devices, continuous performance monitoring is essential. This supports US FDA 501(k) performance testing requirements & certification and helps medical start-ups secure funding. The process involves:
- R&D Prototyping: Rigorous testing of materials and components to determine reliability levels.
- Manufacturing Data Utilization Concept: Leveraging batch lot and manufacturing condition data to assess reliability and predict individual device performance.
Machine learning is used to predict device performance decay and self-correct to extend product life. This attribute seems to be missing in many flexible electronics presentations. Adding predictive maintenance / intelligence seems just as compelling as form factor. Data from multiple sensors allows for more accurate predictions of failure modes. AI-driven imaging systems further enhance the ability to monitor and maintain device performance.
Conclusion
The flexible electronics industry is at a critical juncture, with significant advancements and opportunities for growth. By focusing on technological innovations, improved testing methods and enhanced productivity measures, the industry can overcome current challenges and position itself for future success. Competitive pricing, economic efficiency and rigorous performance evaluations are key to driving growth and market adoption. The integration of advanced testing, simulation and data management tools will support the industry’s evolution, paving the way for new applications and increased market potential.
Eisuke Tsuyuzaki is the CEO of Bayflex Solutions, an innovator in lab automation and data analytics founded in Silicon Valley in 2015. The company provides solutions for the printed and organic electronics industries, specializing inadvancing reliability technologies for printed displays, consumer electronics & IOT devices, healthcare & wearables, aviation / mobility and new energy systems, integrating advanced mechanical and climate systems. Eisuke is a flexible electronics industry advocate and leader who is committed to industry development of reliability systems for flexible and additive electronics. He has more than 30 years’ experience in product management, corporate alliances & ecosystem development in consumer electronics as CTO, Panasonic and SVP, Sony Corporation. Eisuke holds a BS from Sophia University, Tokyo & a Stanford MBA. Eisuke can be reached at email: etsuyuzaki@bayflextechnologies.com, www.bayflextechnologies.com.