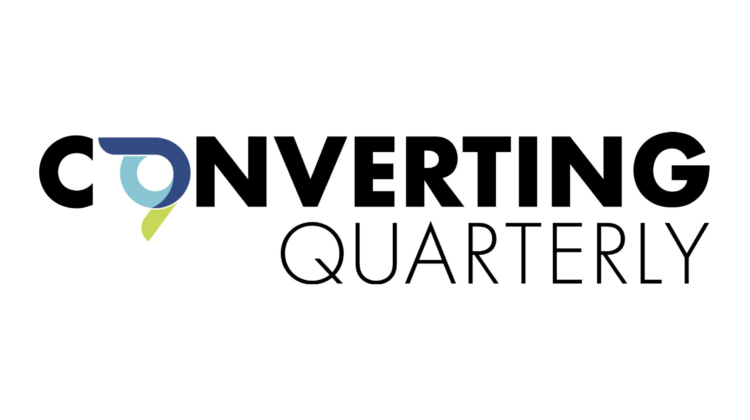
By Charles A. Bishop, Ph.D., C.Eng., principal., C.A. Bishop Consulting, Ltd.
Introduction
The ProFlex series of technical conferences is held at the Fraunhofer Institute, FEP, in Dresden, Germany, every three years and is part conference and part advertisement for the research carried out by the institute. This year, the focus was on “Technology Cross-Over,” and to highlight this theme, the roll-to-roll (R2R) coating conference started with an optional afternoon tutorial given by FEP personnel. The talks highlighted a selection of the individual technologies that need to be combined to make some of the newer, challenging electronics products.
This report will be my view of what I think were the highlights of the two days of presentations. If anyone wants to see the full list of papers, they are listed on the Website www.fep.fraunhofer.de/proflex, and access to the presentations may be purchased by email from events@fep.fraunhofer.de.
Many of the newer products – such as photovoltaics, flexible organic light emitting diodes (OLEDs), elecrochromics, flexible electronics and barrier coatings – require a mixture of different technologies to achieve the end result. This might include atmospheric wet coating along with vacuum coating and lamination to achieve all of the functionality required in the end product. Along with technology cross-over, many of the papers also included references to sustainability, the circular economy and recycling.
Presentation summaries
The presentations were split between large research and development companies or institutes, equipment suppliers and some end users.
To start the proceedings was a presentation by Ralf Fellenberg of VDI Materialsogiezentrum GmbH, a contract research laboratory. The laboratory highlighted a study done in 2017 about the relevance and prospects of surface technologies for the economy. In the area of vacuum-deposition processing, chemical vapor deposition (CVD), laser processing and atomic layer deposition (ALD) were deemed to be most important for the future. Of these, most emphasis was placed on ALD as the key future technology. Other work was being done on developing alternative materials, such as those to replace tungsten oxide in electrochromic devices.
In other technology areas, work was being done to make improvements on gravure printing by using plasma processing for wetting, adhesion and improved resolution. Developed was a high plasma-density source to reduce line widths to help better quality of security printing. Elsewhere in printing, it was suggested that there was not a big market for 3D printers but a large requirement for 3D inks. Another research topic investigated was combining biological materials with conventional materials to produce new materials.
Digitalization, which was defined as the better use of data to develop theoretical models and simulations, was viewed as a key competence. Good quality modeling can clarify what real knowledge is known about a process, as well as enable the testing of process changes while minimizing machine time.
Eco-improved flexible packaging
Following this, Dr. Vicent Martinez Sanz of AIMPLAS talked about the organization’s work on sustainability, the circular economy, reduction of food waste and lower environmental impacts. Too many modern packaging materials are made up of multilayers combining different polymers, making them difficult to separate and recycle. It was pointed out flexible packaging is estimated to take up only 1.6% of landfill space but it still is worth reducing.
The aim is to change flexible packaging from a linear-economy chain to a circular-economy chain where the end is recycling and re-use. This is directed at meeting the European Union directive that by 2030 sorting and recycling has to be increased four-fold over 2015 levels. The specific project being undertaken is to replace virgin material by recycled materials into multilayer, barrier flexible packaging. By multilayer, this does not mean multi-polymer but instead aiming for homo-polymer multilayers, such as virgin-recycled-virgin layers as per some coextruded, blow-molded bottles. Coextrusion and thermoforming are critical processes that can promote diffusion of contaminants, and AIMPLAS used supercritical carbon dioxide as a way of removing volatiles, including odors. This is done by bubbling the supercritical CO2 through the polymer and then later removing the carbon dioxide by vacuum extraction of the melt stream or as part of the extruder.
Keeping on the sustainability topic, the paper following was from Prof. Lorenzo Pastrana of the International Iberian Nanotechnology Laboratory (INL). Starting with the same EU directive for 2030 – and supporting this with the premise that with the increase in e-commerce expected to reach 20% of the food market by 2025, the use of plastic bags will increase unless there is a viable alternative – INL is proposing a wider use of paper packaging. Its aim has been to overcome problems associated with paper – poor mechanical properties, particularly when wet, and the high permeability to liquids. By using nanofibers, nanostructures or nano-layers of cellulose and combining various structures such as cast, electro-spun or micro-fibrillated cellulose, modified properties can be obtained. The functionality can be customized to obtain anti-microbial properties and, by using structure, hydrophobicity can be improved as well as increasing mechanical and barrier properties. These improvements will enable paper to compete with petroleum-derived packaging materials and so help meet the EU directive.
Transparent conductive layers
Changing topics, Takayoshi Saitoh of Nippon Electric Glass Co., Ltd. presented details on how transparent conducting oxides (TCOs) can be improved by either increasing the substrate temperature during deposition or by post-deposition annealing of the indium tin oxide (ITO). Using thin flexible glass and wrapping it around a heated quartz roll for as little as 1 second in a controlled atmosphere (hydrogen, nitrogen or oxygen) at a temperature of between 300-600o C can reduce the resistivity by almost a decade by increasing the carrier concentration. The quartz roll is heated to ~800o C, but the ITO reaches a reduced temperature due to the difference in emissivity. Using the high-temperature quartz tube enables fast annealing that is quicker and more efficient than using a linear oven-annealing process.
A competing technology to TCOs, which was presented at the last ProFlex conference, appeared in two papers at this event. The first was in the paper by Dimitri Kossakovski of Iglass Technology, Inc., where metal mesh was being used as the electrodes on flexible substrates in the manufacture of redox-based electrochromic windows. The redox chemistry allows for some customization of the color. The electrodes were a random-patterned metal mesh made up of electrode traces 0.50 microns thick by 2 microns wide. These are not as good as ITO and can have an issue with increased haze but then are more flexible. The flexible electrochromic is produced R2R and then is cut with one option into strips down the web that are subsequently butt-jointed together to make a much larger window size. Although this does give a much easier route to manufacturing windows of many different sizes, it does have a weakness: the butt joints. It is very difficult to seal the joints to prevent moisture or oxygen ingress, which degrades the chemical reaction, making the joints very much more visible and aesthetically displeasing.
A third paper was about the manufacturing of the metal-mesh electrodes. This time, the presentation was by Christoph Hunger of Paperfabrik Louuisenthal GmbH. The core technology uses a printed dispersion that, as it dries, cracks open in a random pattern as the coating shrinks. The substrate then is metallized, and the original cracked coating is removed. This leaves behind the metal tracery that is a few microns apart. This metal-mesh structure is thinner than can be obtained by nanowires and, if the structure is filled in and smoothed by using a conducting polymer, it can have a visible light transmittance of ~92% and be more flexible than metal oxides. The next step is to further increase conductivity by using a graphene in-fill coating as the smoothing layer.
Going back one manufacturing step further to the substrate, we then had Valentijn von Morgen of DuPont Teijin Films (DTF) present details of the company’s peelable clean-on-demand film. So many applications need to have a good barrier coating, and to produce this, the coating needs to be defect-free, which, in turn, requires the substrate to be free of any surface contamination at the time of coating. The most secure way of achieving this is to use the coextruded film and peel off one layer immediately before the coating zone so there is the least amount of time between peeling and coating in which the substrate surface can be contaminated. It also has found that not only does the film surface need to be clean, but there also are advantages in the film being smooth.
The presentation went on to show the range of film options that can be obtained by combining coextrusion with in-line coating and additives. Examples included the control of the refractive index of primers at the surface to optically match the downstream coatings and work to eliminate iridescence. Recent developments include improved UV and hydrolysis lifetime, flame-retarding, as well as the heat-stabilized, low-haze, low-oligomer, high optical-clarity films. Slightly more unusual is the moldable-PET film that makes use of the chemical stability and flexibility of PET that has been developed to also match the formability of polycarbonate normally used for molding.
Inspection and gauging
I find it interesting that every few years someone produces a new vacuum gauge. Over my working life, I have seen a few produced, but most have not gone on to become the gauges of first choice. Dr Klaus Bergner of VACOM presented a new gauge design that looks to be a worthwhile option, but time will tell. The gauge works using a modified Bayert Alpert gauge designed to trap ions and then release them after a short collection time. Using the ion current and the accumulation time, the pressure can be measured. The collected ions are accelerated to a detector, and so the different gasses arrive at different times, depending on mass. This time-of-flight route to the Faraday cup detector enables it to be used as a residual gas analyzer (RGA), as well as a pressure gauge.
Dr. Dermot Monaghan of Gencoa described the Remote Optical Emission Spectroscopy (ROES) technique, where a plasma is produced inside the sensor of the gas sample, and the optical emission of the plasma then is used to identify and quantify the composition of the gas sample. This technique has been around for a while and that has allowed experience of how it has been used in practical applications and thus be included in the presentation. These examples help in showing how versatile the system is for everything from direct process control to leak-testing of systems and gas lines, as well as troubleshooting when things go wrong. The sensitivity of the system was demonstrated by monitoring a metallizer where the different process steps, such as starting the winding, heating the boats, starting the wire feed, starting the plasma treatment and switching off the different process steps, can be seen clearly. In addition, the ROES was compared to the more established residual gas analyzer (RGA). This showed how well the results compare and how ROES has a wide operating pressure range but without the differential pumping necessary for the higher pressure operation of RGA.
I was somewhat surprised by the presentation from Seragus GmbH given by Marcus Klein on the monitoring of transparent conductive coatings. I have used eddy-current monitors for decades, and, although I was aware of some of the improvements, I had not realized how much had been done to the systems so they could map a whole area. This ability to map an area and show variations in resistivity, as well as produce a coincidental measure of the transmittance, reflectance and haze, provides a much better view of coating uniformity. The combination of these measurements also enables the mapping to highlight defects. Another thing I had not really thought about is that the newer options, such as nanowires, metal meshes and conducting polymers, also can be measured by these systems. Although the measurement range has been increased, it still is necessary to optimize the design of the measurement and detection coils to be able to maximize sensitivity for a particular material and thickness of conducting layer.
Presenting a new idea in in-line monitoring was Dr. Wulf Grahlert of Fraunhofer IWS where the company was using hyperspectral imaging on-line to identify surface defects in the coating and correlating these to the barrier performance that typically was measured for the density and size of defects measured. This process was working, but there was a limited amount of data obtained to make the correlation, so I am sure in future presentations there will be a lot more evidence to demonstrate the benefits of this technique.
Yuasa System Co., Ltd., is a company that builds testing equipment, and Kei Hyodo presented the company’s novel method of watching the progression of stress as applied to a material or coated material. This was demonstrated by watching how a material behaved during a bending test and how the application of the bend could affect the concentration of the stress in the material. If you are imaging a transparent conductive coating onto a flexible polymer substrate, the material can be bent to the same radius of bend in free space, or it can be bent around a backing former. Then there can be variations of this where there is partial support at each side of the bend, and the shape and position of these supports can alter the spread and intensity of the stress. This is accomplished by using a mechanoluminescent material – a material that emits light as it is stressed. (Just as an aside, some self-stick envelopes use a tack adhesive that has these properties, so if you open the envelope by peeling up the flap, at the point of peel you can see a faint blue light emitted. This can be seen more easily if you do this in the dark.)
Presented was a video of four variations of the bending test on this material and, by using a high-speed camera that could later be viewed at a slower speed, the differences of peak stress and spread of the stress could be seen clearly. Using this they have optimized the bending-test devices to minimize peak stress. This mechanoluminescent material also allows anyone to evaluate other mechanical testing to know how the stress is put onto the test materials and compare the performance of competitive testing machines.
Developments in OLEDs
Toward the end of the conference, there was a group of papers on organic light emitting diodes (OLED), of which the paper presented by Norman Bardsley of Bardsley Consulting was the most interesting. It highlighted the manufacturing challenges that have to be overcome. These were grouped under three main headings of performance, lifetime and cost.
The performance challenges include such things as light-extraction efficiency or color-tuning. Lifetime issues are management of defects (a euphemism for elimination of defects) and incorporation of an effective oxygen and moisture barrier to the device. Costs always are present, and the problem of trying to improve the barrier or minimize defects is that the price of doing this can, at least initially, increase the cost. Having demonstrated a process that has improvements over current manufacturing, it then has to be transferred to a production line and work with a high yield. If you consider that an OLED may comprise a stack of more than 40 layers, each of which has to be optimized in conjunction with the other layers and all working at a common line speed, this is not a trivial task.
It has been shown that for a simple (~14 layers) OLED, if the barrier layer can be produced with zero pinholes per cm2, the water-vapor transmittance performance is good enough that the lifetime of the OLED will be greater than 10 years. This has demonstrated that it can be done, but it now has to be done on more complex-OLED structures, uniformly and reproducibly. Also, somehow the costs need to be reduced. This challenge was further highlighted as one of the low-cost substrate suppliers that was being trialed went bankrupt a couple of weeks before the conference.
To get the most out of R2R processing, the ideal would be to have a single unwind and a single rewind roll, and every stage of manufacturing is between the two rolls. This means that vacuum systems must be air-to-air systems. To keep the manufacturing going, rolls are spliced together without a change in speed, and splices have to be accommodated throughout the winding system. Within the vacuum chamber, the deposition has to be done with the best possible material efficiency, and to maintain high yields the system cannot be stopped for shield cleaning too often. In conventional vacuum systems, material efficiency can be down around 50%, which is unacceptable for this more continuous production goal. Confined, jet-type deposition sources can operate at >99% material efficiency and are no doubt being evaluated for this type of application.
Conclusion
As stated in the introduction, this review has not included every paper, but I hope it has shown how diverse and interesting the ProFlex 2019 conference was and why it is worth making a note to attend the next one.
Dr. Charles A. Bishop holds a Bachelor’s degree in Materials Engineering with a Diploma in Industrial Studies. His research led to developing a process for manufacturing titanium-based bone implants for tendon location. He went on to obtain a Master’s degree and Ph.D. following further research into vacuum-deposition processes. Bishop has more than 35 years of experience in vacuum deposition, mainly onto flexible webs. He has published two books, writes the “Vacuum Verbiage” Q&A technical column for this publication and moderates the online “Vacuum Web Coating” Technical Channel. Bishop can be reached at +44-1509-502076, email: cabuk8@btinternet.com.