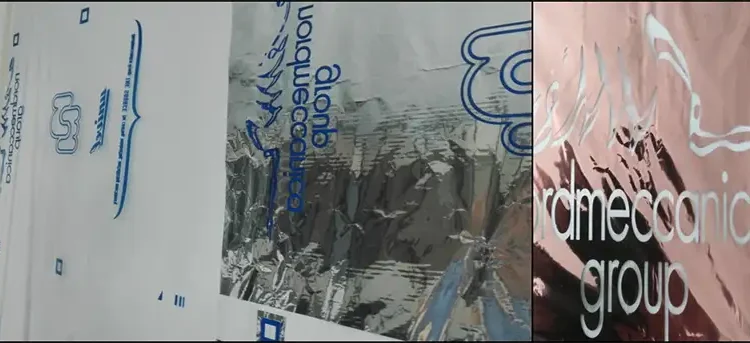
By Fabiano Rimediotti, vacuum technologist, Nordmeccanica N.A., Vacuum Div.
Abstract
Selective, or pattern, metallization produces metallized substrates with metal-free areas, resulting in a variety of graphic effects. It is done by “masking” the incoming metal vapor by means of a special oil applied on selected areas of the film substrate with a dedicated flexographic-printing process. A very recent innovation is registration control, enabling converters to metallize on a previously printed film accurately matching the graphic motifs. This article will illustrate and discuss the main process features, the quality performance and the potentially vast variety of applications, ranging from decorative, functional and “smart” packaging to security and flexible electronics.
Introduction
Metallized films represent an important segment among the materials and technologies that make up the flexible-packaging sector. More than one million tonnes are produced each year for a value in excess of US$3 billion. Most of these metallized films contribute to the protective properties required for food packaging. There are, however, many other applications with lower volume – but often with higher added value – in which the unusual characteristics of metallized films represent a key functional or aesthetic attribute. It is the case of selective metallization, which represents a particular variant of the classic metal-deposition process under high-vacuum conditions and allows producing areas with no metal on an otherwise metallized film. For this reason, it also is called “pattern metallization” or “window metallization.” The absence of metal in certain areas (“windows”) allows the customer to see the product directly, or writings and graphics of any kind can embellish the packaging or give it a more personalized look.
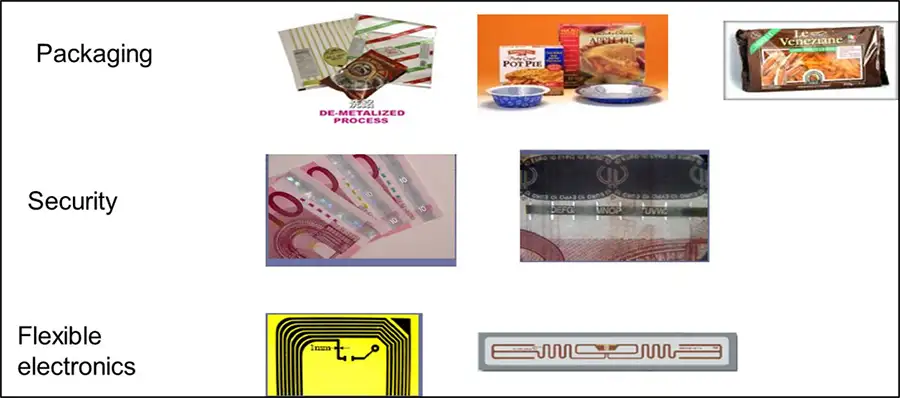
Pattern metallization represents a more ecological and more economical alternative to traditional de-metallization that consists of the removal of metal by chemical processes, which has had and still has an important place in the areas of safety, anti-counterfeiting and the packaging itself. The next sections briefly describe the process and its most recent variant – the so-called “in-register pattern metallization,” which combines traditional printing and selective metallization to produce products of great visual impact and combinations used in security products. Examples are shown in Figure 1.
Selective metallization: The process
The principle of selective metallization can be described as an “oil masking” process. As the simplified schematic in Figure 2 shows, it consists of the in-line application of a special oil by means of a printing unit placed immediately before the film entering the metal-deposition zone. The oil’s sudden evaporation prevents the metal vapors from reaching the film’s oil-printed areas, leaving clear and high-definition structures. A pattern-metallized unit is, therefore, a printing station installed in the vacuum chamber, with the traditional ink replaced by a special oil characterized by purity and chemical stability. The most commonly used oils belong to the family of fluorinated polymers.
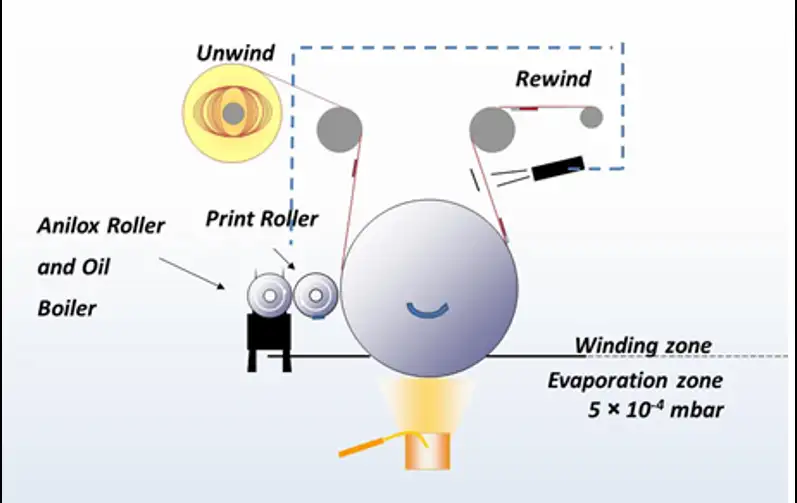
The system consists of a three-roller flexo-printer design with an enclosed doctor blade and a tank for the oil containment: 1) an engraved anilox roll for the fluid transportation and dosing to the printing roller, 2) with a mounted relief plate or sleeve, and 3) the process drum of the metallizing machine, which represents the “impression cylinder,” supporting the film as the printing plate is pressed against it. In this flexo unit, the oil delivery to the anilox roll is done by evaporating the fluid from the heated oil tank. The very low pressure at which the whole process works allows the use of low temperatures and guarantees minimization of the oil entering the process chamber. A more detailed description of “oil masking” principles can be found in Reference 1.
Pattern metallization is not a new process: It has been used by film-capacitor metallizers for almost 20 years. Its introduction to other industrial sectors, such as flexible packaging or security, is more recent and still relatively rare in the vacuum-metallizing industry.
Registration control in selective metallization
The most recent development is selective metallization with registration control, which allows vacuum metallizing on a previously printed film (see Figure 3). This greater system versatility opens opportunities to extend its use to a more universal range of end-use applications.
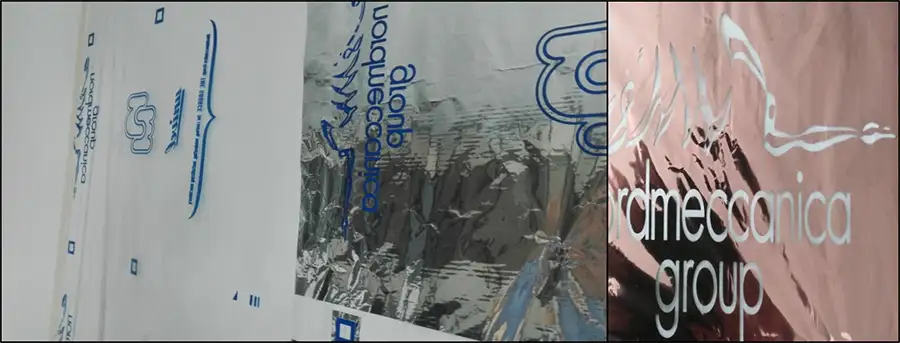
The registration control is represented schematically in Figure 2. It uses the same concept as a multiple-color printing press; that is, an optical sensor detects the misalignment between the two marked positions of the printed and metallized film. The registration error is automatically and continuously corrected by acting on the printing-roll system to finely synchronize the printed and the metallized pattern. The optical sensor can be complemented by a video web-inspection camera to visually check registration accuracy.
Although printing-press multiple-color registration is a well-established technique, its application inside a vacuum chamber presented a number of challenging issues, requiring special designs and solutions:
- All processing takes place in a closed and inaccessible space, and all adjustments must be made by remotely controlling speed and positions from instrument signals. It is, in fact, only by starting metallization at a certain speed that the position control can be operated by reading of registration marks. It requires a fast and accurate predictive positioning to minimize waste materials.
- Metallization is a thermal process, and the possible effects on film must be controlled to avoid deformation with the consequent negative impact of graphic reproduction.
- Graphic definition is achieved by means of a controlled, “masking-oil” application, tuned to the amount and type of metal evaporation. Moreover, registration accuracy depends on the position and motion control of the flexo-printing system governing the oil application on the film.
In-register pattern metallization: Printing quality
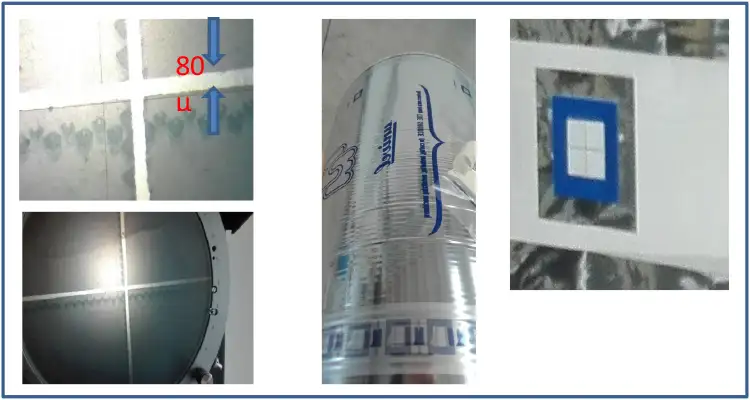
In terms of accuracy and definition, the indicative features of selective metallization graphic properties are described below and represented in Figure 4.
Print resolution: In selective metallization, this represents the minimum thickness of a line or of a representative graphic item, which is detectable, measurable and has a reasonable width uniformity. Process capability is about a 50-micron line width (+/-5.0).
Repeat length: Represents the space between two successive and corresponding images, which is determined by the printing-roll diameter. It is crucial that the repeat length is consistently maintained along and across the web, controlling the possible web deformation due to heat and tension. Length tolerance is typically +/-0.20 mm.
Registration tolerance: This characteristic represents the ability of the selective-metallization registration control to track the previously printed-film graphic pattern. Being the most innovative part of the project, this feature is being tested and qualified for multiple patterns, including multiple-color printed and embossed film. Indications are for a tracking accuracy of +/-0.30 mm in both directions.
Current applications and future opportunities
The fact that in-register pattern metallization can be used consistently on industrial equipment can extend the opportunities for using this technology to replace chemical de-metallization and be considered for new applications on a roll-to roll (R2R) basis. Current uses are for decoration and brand signatures in flexible packaging or with the production of security features for anti-counterfeiting, document verification and currency protection. Metallizing with different metals, in particular copper, can add color effects to the toolbox for creating multiple graphic structures.
Another potential use of pattern metallization will be for flexible electronics, such as integrated circuits, RFID tags and transistors, parts of flexible displays and many other applications, currently in rapid growth mode. They often include miniaturized conductive tracks of different shapes and complexity. From the traditional etched, metal-foil laminate, the advantage of producing large quantities of electronic devices is driving the path to R2R printed electronics using conductive inks.
Pattern metallization can be a more efficient and less expensive alternative to existing technologies. If thin metallic films, characterizing the traditional vapor-coating process, can result in a too-poor conductor for most of electronic-product requirement, in-register pattern metallization makes it possible to deposit metal in successive steps with exact pattern replication, building up a thicker and more conductive track.
Conclusion
The recent setup of an industrially proven process of pattern metallization with registration control opens new opportunities for more widespread use of this technology, due to creating multiple combinations of ink printing and aluminum or copper metal coating. Beyond the realm of flexible packaging, future developments could involve products as cutting-edge as components for flexible electronics. A complete analysis of the possible advantages of vacuum deposition as an alternative to traditional processes is certainly worthwhile.
Reference
- Pagani, A. and others, Pattern Metallized Film: State-of-the-art and Growing Opportunity, SVC Technical Conference, 2007.
Fabiano Rimediotti, vacuum technologist for Nordmeccanica N.A., Vacuum Div. (Hauppauge, NY), holds a university degree in Chemical Engineering and has spent most of his professional career in the field of vacuum technology, in particular vacuum metallization. He worked for 25+ years with Galileo Co., specializing in the design and construction of vacuum metallizers for flexible packaging and other applications. He has been with Nordmeccanica since 2014. He can be reached at 631-242-9898, email: rimediotti@nordmeccanica.com, www.nordmeccanica.com.