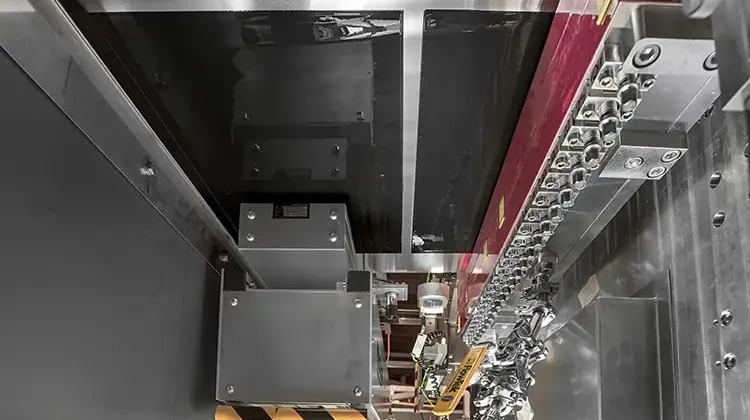
By Eric Maki, development center mgr., and David Ventola, dir. of business development-Engineered Products,
Clean Technology Systems, Dürr Systems, Inc.
Abstract
As the lithium-ion (Li-ion) battery industry matures, pressure to decrease costs continues to mount. Battery manufacturers are seeking to reduce material and processing costs. Simultaneous two-sided coating using a tensioned-web over slot-die (TWOSD) process developed by Dürr Megtec enables battery manufacturers to be more cost-effective, and therefore, more competitive. Besides doubling the throughput of single-side coaters and needing only one pass through the dryer, other benefits of this two-sided process include a smaller manufacturing footprint, lower capital and operating costs, a broader range of coatweights for Li-ion slurries and fewer problems with substrate wrinkles, among others.
Introduction
The inflection point for the increasing demand of lithium-ion (Li-ion) batteries is now. As the end-use adoption curve rises exponentially for e-mobility manufacturers, from electric vehicles to stationary energy-storage systems and consumer product goods, so too does the pressure to reduce costs, improve quality and enhance speed-to-market capabilities.
One of the key steps to produce a Li-ion battery cell is coating active materials to both sides of the current collector – copper and aluminum foils. A typical coating chemistry slurry is lithium salts dispersed in NMP (N-Methyl-2-pyrrolidone) and graphite dispersed in water, which are slot-die-coated in sequential steps to both sides of the foils. Optimizing battery performance requires controlling every step throughout the coating process – from powder handling and slurry mixing to coating and drying.
Aspects of slot-die coating
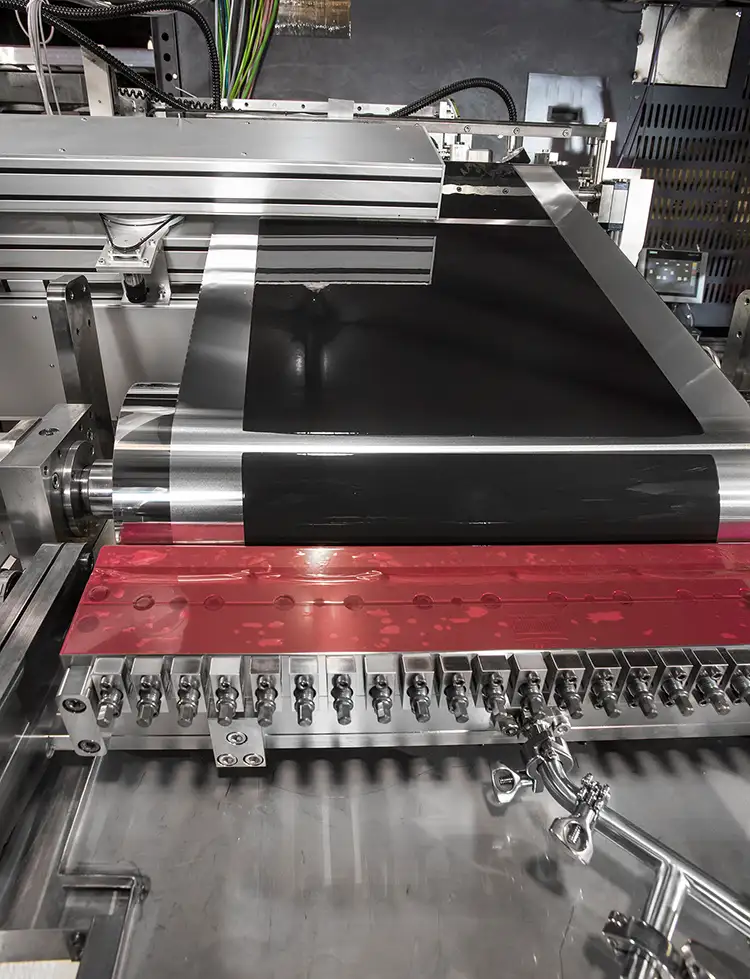
Slot-die coating against a backing roll is the most common method for applying Li-ion-battery electrode slurries (see Figure 1). The mixing conditions and the related equipment directly influence slurry quality, as do the coating and drying processes, which collectively affect battery performance. Maintaining the integrity of the electrode chemistry hinges on closely managing the precise combination of dry solids and liquid components.
Because the slurry carries particle dispersions, the particles can become trapped in the gap between the slot-die lips and the foil against the backing roll. This can result in a streak – or worse, cause the web to break. For energy cells, which require heavier/thicker coat loads, the trapped particles occur infrequently. However, power cells call for lighter and thinner coat loads, which require tighter control to keep the particles from becoming trapped and affecting the coating run.
The largest challenge when slot-die coating against a backing roll occurs when applying the active materials to both sides of the current collector. The substrate is supported by and wraps a roller when coating against a backing roll. Here, the backing roll provides a solid platform to produce an accurate wet coating layer.
Whatever the coating process, it is imperative the coating be uniform on each side. If the Side A coating is not uniform, the condition will have a negative influence on the coating of Side B, thereby resulting in an uneven distribution of the active material. This ultimately affects battery performance.
A slot die with a backing roll allows coating battery electrodes only one side at a time. This production set up requires two separate passes through the same coating line, whereby a second coating station is installed after the drying oven. However, a more efficient method is to coat both sides in a single pass. Two ways to do this include: 1) with a sequential or tandem coating system or 2) with simultaneous two-sided coating (see Figure 2).
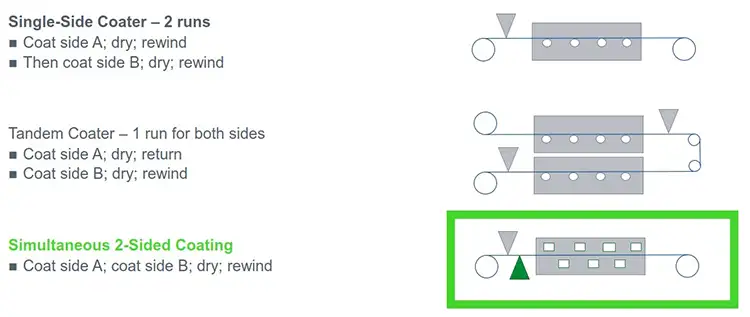
The promises behind TWOSD
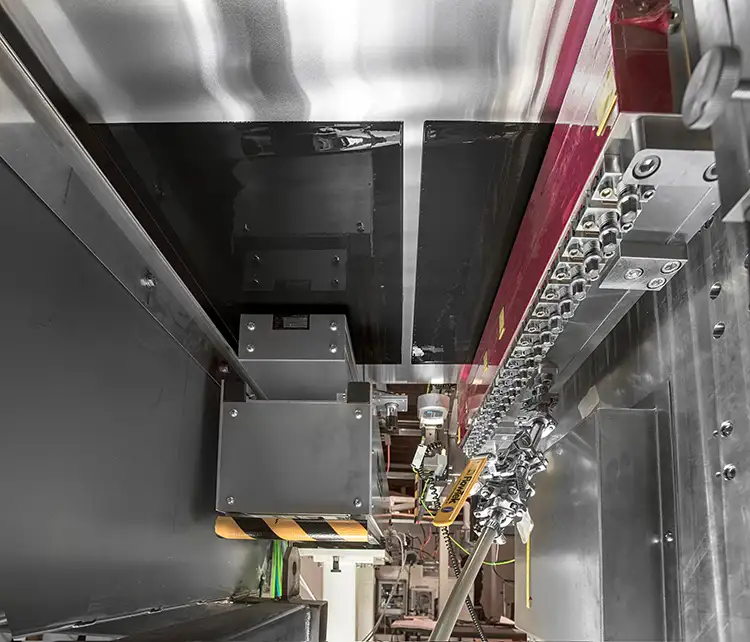
The promise of simultaneous two-sided coating for battery manufacturers is the ability to enhance production efficiencies and effectively double yields without expanding the production footprint. This firm’s engineers developed a tensioned-web coating process using a slot-die (TWOSD) mounted in a vertical orientation to simultaneously coat both sides of electrode foil traveling horizontally (see Figure 3). The process delivers a uniform coatweight matched to that of backing-roll coating with the proper configuration and process parameters. Without a backing roll, there is no gap between the slurry coating and the foil.
For light coatweights used in power cells, this method provides uniform coatings down to a coatweight of 20 gsm or loading with enough flexibility to meet the needs of energy cells at coatweights up to 200+ gsm. In addition, by removing the backing roll, particles of active material no longer are trapped between the slot die and foil, which eliminates the risk of streaks. The viability of tensioned-web coating is further confirmed by its use in the production of primer coating on aluminum foil, which means it has been used to coat carbon slurry as thin as 2 gsm.
Key benefits of simultaneous two-sided electrode coating include:
- Twice the throughput compared to single-side coaters
- Requires only one pass through the dryer, delivering equal drying of both coated sides
- Smaller overall manufacturing footprint compared to tandem lines – the overall length is 5 to 10 meters shorter, and the height is 5 to 6 meters less
- 30% to 50% lower capital and operating costs compared to tandem coating lines
- Increased range of coatweights for lithium-ion slurries
- Reduced incidents of particles being trapped at the coating point (no streaks or no foil breaks)
- Fewer problems with wrinkles at the coating point.
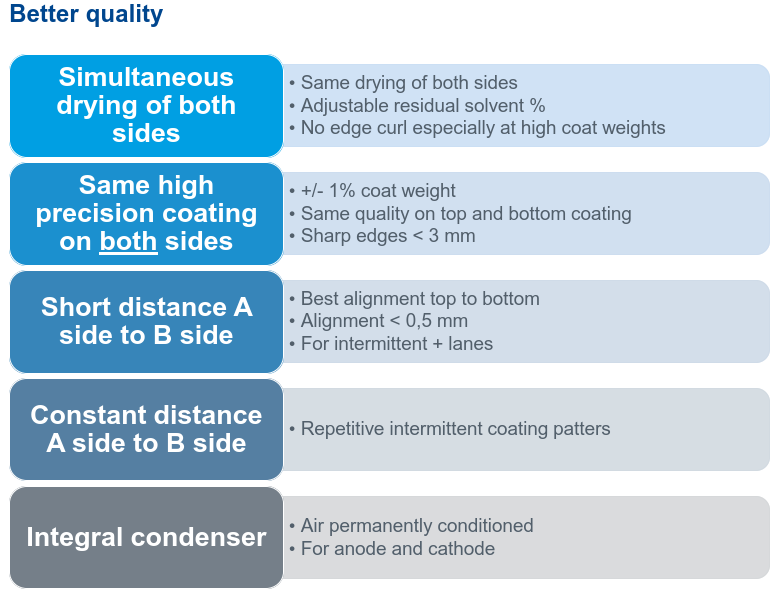
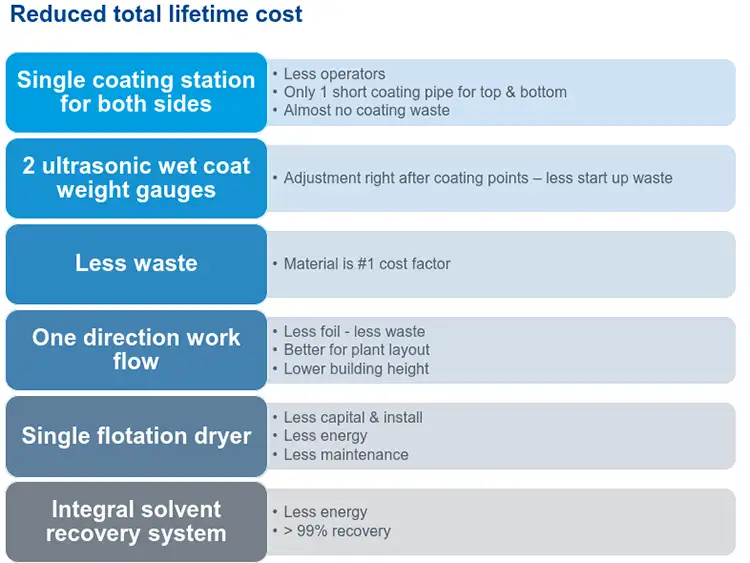
Tables 1 and 2 provide details on the improved quality and reduced total lifetime cost for a two-sided coating process.
Other benefits of electrode coating via TWOSD include allowing for placing both coating dies in close proximity to one another. The setup practically eliminates registration problems of the top-to-bottom side patches for intermittent (aka patch) coating applications. The top-to-bottom registration also is more precise with a position-based coating control scheme, especially with the coating heads in close proximity.
Conclusion
The energy-storage industry is demanding reduced production costs in combination with increased yields and product quality. Manufacturing large quantities of Li-ion battery cells requires a significant change and dimensional upscaling of the production equipment and output per line to achieve industry targets. At the same time, the benefits of simultaneous, two-sided coating technology become increasingly important the wider and faster coating lines are required to get.
As the lithium-ion battery industry matures, pressure to decrease costs mounts. Battery manufacturers are seeking to lower material and processing costs. Simultaneous two-sided coating using the tensioned-web (TWOSD) process enables battery manufacturers to be more cost-effective, and therefore, more competitive.
The full limit of the tensioned-web coating process continues to be refined in the context of lithium-ion batteries increasingly powering the new engine for e-mobility.
David Ventola, dir. of Business Development, Engineered Products at Dürr Systems, Inc. (De Pere, WI), holds a B.S. and M.S. in Chemical Engineering and an MBA. Prior to Dürr Systems, he spent most of his career in the roll-to-roll coating and converting industry at Polaroid and Presstek. Just prior to joining Dürr Systems, Ventola worked at A123 Systems, where he focused on Lithium-ion battery-electrode manufacturing. He also is active in NAATBatt. Ventola can be reached at 920-321-6475, email: david.ventola@durrusa.com, www.durr-megtec.com/en/industries/battery-electrode-manufacturing/.
Eric Maki, development center mgr. for Dürr Systems, Inc., has more than 20 years of experience in mixing and coating process design and development. His experience includes quality and process engineering in both R&D and production from plastic extrusion to lithium-ion batteries, and high-performance specialty products and labels. He holds a Bachelor’s in Chemical Engineering and an MBA. Maki also is active in AIMCAL. He can be reached at 920-337-1234, email: eric.maki@durrusa.com.