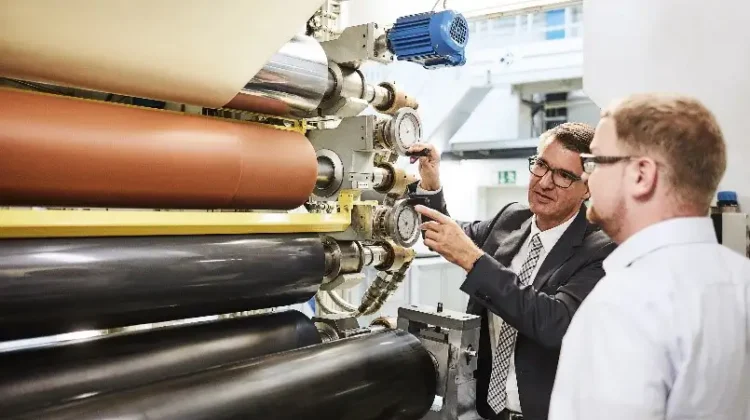
By Andrea Glawe, regional sales dir.-KROENERT GmbH & Co. KG
Editor’s Note: This technical paper is based on a presentation at the AWA Global Release Liner Industry Conference & Exhibition, held in Amsterdam, The Netherlands, in February 2020. More info: www.awa-bv.com
Abstract
The expected annual growth in manufacturing of release liner worldwide is evaluated with 3% and in Asia even higher at 5% [1]. The end use for label stock still dominates. However, today we see increasing demands in applications for composites and printed electronics. Composite applications are assessed as the future base material for the aerospace and automotive industries, as well as for wind-power stations. For printed electronics, an increasing number of applications for optically clear adhesive and labels for information transfer, RFID and NFC can be observed. These new applications define different quality standards for the requested release liner.
1.1 Applications for printed electronics
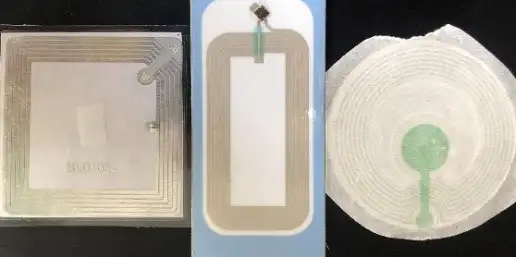
Functional labels with RFID (radio frequency identification device) or NFC (near-field communications) functions gain importance in the label stock market. These “smart” labels partly have hybrid features with integrated chips and sensors and are one key solution for information transfer about the product itself, as well as the used packaging compound. The labels can be loaded with all necessary data about the used raw materials, such as polymer films for the packaged products, necessary storage conditions and important handling information, as well as optimal recycling solutions when it comes to the end of its use. Release liners are necessary for the realization of the self-adhesive function of the labels.
For instance, applications include the following (see Figure 1):
- Labels with RFID function to detect products and to transfer signals electronically
- Labels with NFC function, such as storage-temperature measurement and detection of substances with negative effects on the product and the person using the product
- Labels for brand protection and product security
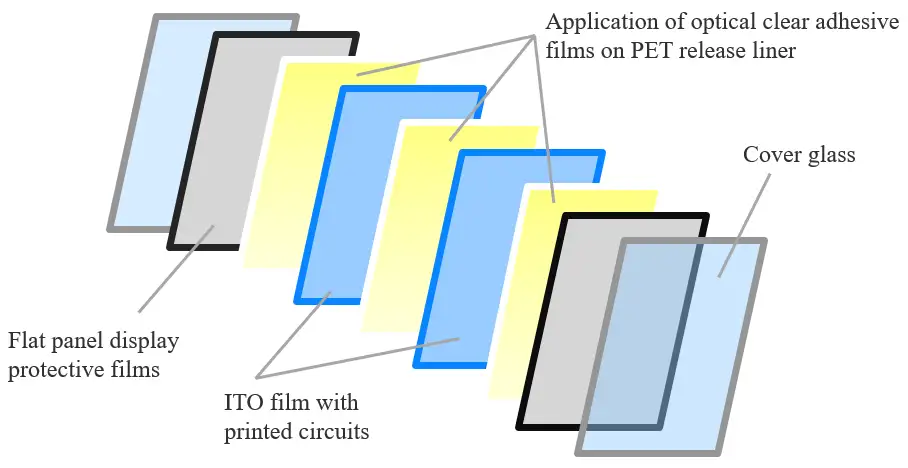
Another application with a growing demand for release liners is the display market (see Figure 2). These liners are used to produce high-precise, optically clear adhesive (OCA) films, which are necessary to laminate the different functional layers in a display. The release-liner requirements for PET-film release liners (25-200 µm) are within a wide range of release strength and anti-static properties.
Special demands for OCA release liners include the following:
- Low haze and high transparency
- Adhesive easy-to-peel-off (ideally no release force necessary to avoid destroying the adhesive layer)
The film is manufactured under cleanroom conditions (Class 1000 and higher) with precise adhesive-coating processes for the acrylic and epoxy adhesives.
1.2 Applications for composites
Release liners are used in an increasing degree for composite applications, which comprise unusual sectors such as:
- Aerospace – lightweight parts for fuselage, wings, and horizontal and vertical stabilizer
- Transport – automotive, railway, bus, caravan
- Sport – bike, ski, golf
- Wind energy – rotors and blades
- Personalized medical products – orthosis, artificial joints
- Building – fiber-reinforced concrete
- Pipelines – submarine pipelines for gas and oil
The challenging situation for composite applications is the versatility in requested release functions. Depending on the kind of resin, the viscosity of the resin and the required resin-film thickness, different release-liner qualities are necessary. The viscosity of resin films can vary from 100 mPas to 1,000 Pas, which means coating materials such as oily up to high-viscosity, paste-like qualities. It is definitely necessary to allow the resin to detach from the coating equipment to be transferred to the release liner. The optimal adaption of the adhesion force in relation to the release force can be very challenging.
2. Production processes for release liners
2.1 Overall information: Depending on the particular purpose of the release liner, different silicones are used for its production. In general, these are differentiated between solvent-free (thermal-cured and radiation-cured), solvent-based and water-based silicones.
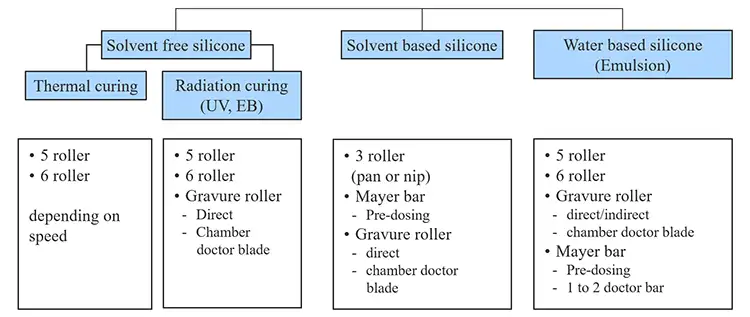
The decision about the optimal application method is affected by the kind of silicone, the requested coating thickness, the viscosity and, in case of solvent-based and water-based silicones, the solids content of the silicone solution (see Figure 3).
2.2 Solventless silicones: Release liner produced with solventless silicones are used mainly for label stock and tape applications. These silicones can be cured by thermal or radiation processes.
The close cooperation between prepreg manufacturers and release-liner manufacturers is very important to define the right quality for the different applications. As already mentioned, is it necessary to transfer the resin at one side from the application roller to the release liner but delaminate the resin from the release liner easily for the reinforcement, fiber-impregnation process.
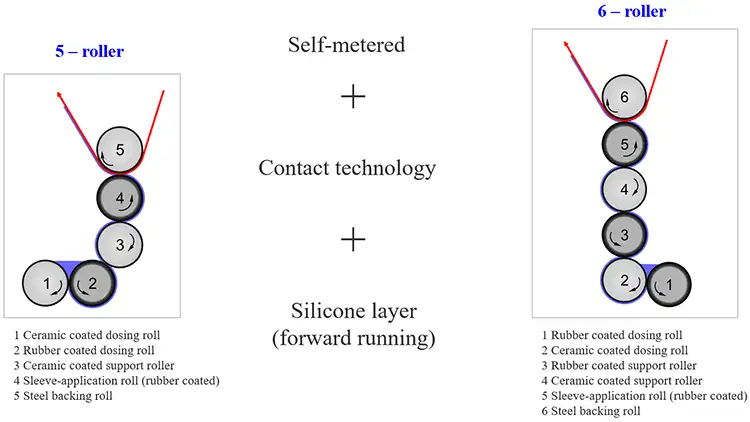
The splitting of the silicone between the application roller and the substrate is the most critical quality parameter in using solventless silicones. For applications where transparent, perfect silicone layers are necessary, this is a criterion for exclusion and means the requested quality cannot be reached. In this case, it will be necessary to use solvent-based or water-based silicones with a very low viscosity and a very low solids content.
Most of the solventless, silicone-based release liners are produced by multi-roller systems with smooth rollers (see Figure 4). Self-metered 5- and 6-roller systems are used largely for silicone coating. The wet film will be stretched due to the relative speed between the rollers. Dry coatings with a thickness of 300 nm (0.3 gsm) can be reached accurately.
The number of rollers in the coating system is defined mainly by the speed of the coating line and the individual coating parameters (see Figure 5). The important adjustment criteria are the relative speed between the different rollers and the accurate adjustment of the “footprint” between the rollers. Besides that, the bending stability of Roller 1 and 2, the type and quality of the dosing of Roller 2 and the hardness and quality of the rubber-coated roller mainly influence the coating quality.
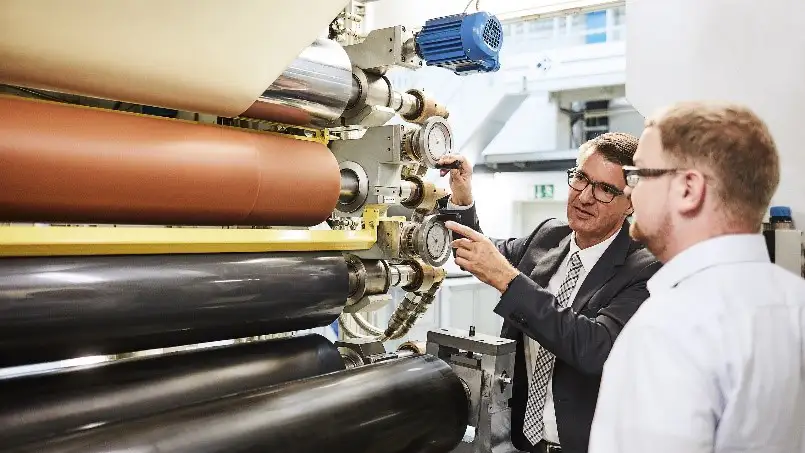
2.3 Solvent-based silicones: Solvent-based silicones are essential for very thin, high-precise and, combining these, transparent silicone films. Due to the solvent-based silicone type, it is possible to apply a thicker wet film with a very high accuracy. The precise definition of the coatweight is possible with the right roller design.
This firm also is proposing the multi-pressure gravure system (MPG) for silicone application (see Figure 6). In this case, the definition of the coatweight is affected by the engraved roller design, the relative roller speed and the pressure within the pressure chamber for applying the coating material to the roller. Due to the low viscosity, it is possible to apply a precise wet silicone film, which nearly is invisible after the dryer due to the thin film thickness and high accuracy. The best way to evaluate the accuracy of the wet film in front of the dryer is to watch the so-called “rainbow effect,” which results in a different light interference due to an unequally coated silicone film.
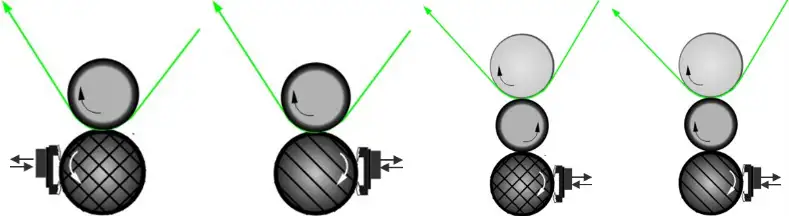
The gravure roller quality is characterized with the following parameters:
- Cellular volume in ml/m²
- Grid number in L/cm
- Grid depth
- Grid angle
- Surface: chrome, ceramic, titanium nitride
The coating process can be realized in synchronized or reverse rotation and direct or indirect.
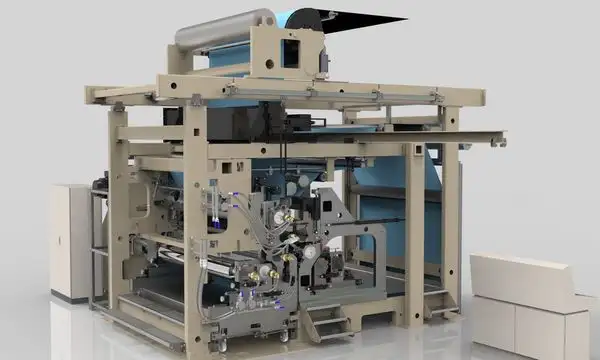
2.4 Double-sided simultaneous coating techniques: In 2018, this firm introduced the first coating unit for simultaneous siliconizing both sides of a web with solventless silicones (see Figure 7). Expanding its range of products, we redesigned a roll-to-roll system especially for this purpose. This coating unit can be included in new plants or retrofitted in existing facilities. Retrofits offer a special advantage: The flotation dryer already installed in many plants can be used for the non-contact transport of webs and combined with a non-contact air turn in front of the dryer. This feature cuts down on costs for equipment and operations and minimizes environmental impact.
The process of double-sided siliconizing is suitable especially for paper webs used as release liners for adhesive tapes and for graphic-arts products and for some composite applications. The simultaneous coating of the front and back of paper webs substantially prevents paper from drying out, and the coating machine can be considerably shorter in length, taking up less space. Moreover, the system needs fewer operators, allowing one person to observe two coatings at the same time. As only one dryer is needed, this process is very resource-efficient and consumes less energy. The siliconizing unit also can be used for one-sided coating and operate flexibly with other substrates and silicones at any time.
3. Machinery concepts
3.1 Silicone-coating machines: The typical arrangement of a release-liner production line is shown in Figure 8.
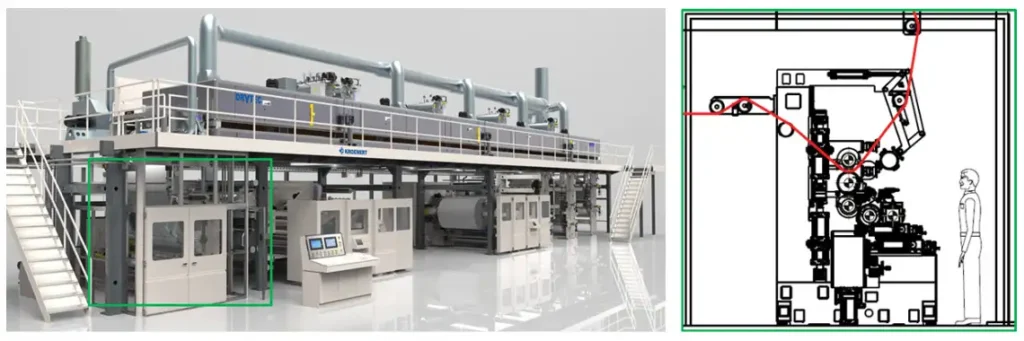
Each machine consists of the following elements: unwinder (usually a fully automated turret unwinder), multiple-roller coating system for solventless silicone, curing oven, cooling, remoistening in case of paper coating and rewinding of the finished release liner. A typical setup will be:
- Speed: 500 mpm
- Working width: 1,650 mm
- Coatweight: below 0.5 gsm
- 5-roller silicone-application unit
- 20-meter flotation dryer
As an alternative to the multiple-roller system, the coater can be equipped with gravure-roller coating systems or even simultaneous double-sided coating systems. The requested release-liner quality defines the optimal machine layout.
3.2 Machinery solutions for resin-film coating lines for composites: The prepreg tape production is divided mostly in two process steps: 1) The resin film formation; and 2) The transfer of the resin film to the fibers, which have to be impregnated. Typically, the resin film is applied on a release liner, and the release force is adapted to the resin quality.
The challenging situation is to adjust the release liner precisely to the quality of the resin. Usually smooth, heated-roller systems apply the melted resin to the release liner as shown in Figure 9. The release liner is being processed to the coating unit. The melted resin is transferred to the release liner, cooled down with cooling tables and sometimes covered with protective films. The final compound of release liner, resin film and protective film is wound up precisely at the process end.
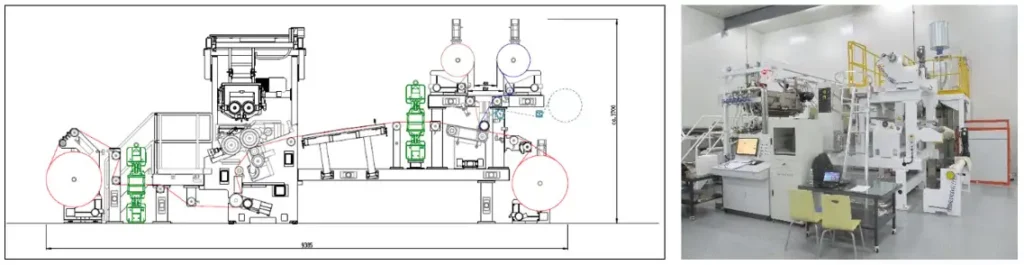
The partly high-viscosity resin has a certain adhesion to the application roller due to its stickiness. The adhesion force between the resin and the release liner needs to be higher for transferring the resin to the release liner. It also has to be low enough for its delamination in the second step, the transfer of the resin from the release liner to the fiber reinforcement during the fiber-impregnation process. Multiple tests often are necessary to define the right release-liner quality.
1.3 Machinery solutions for optically clear adhesives (OCA): Increasing applications for release liner are related to OCA films (see Figure 10). The process steps for the production of optical clear adhesive layers are:
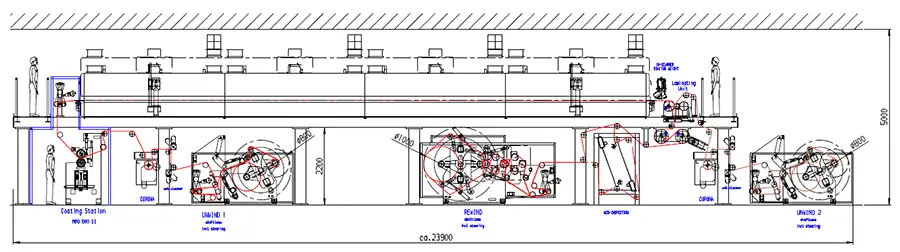
- Unwinding PET-film with silicone release layer
- Coating and curing of OCA-layer
- Lamination of PET-film with silicon release layer
The differentiation of release forces is very important to the definition of the release function of release liners for OCA films. The delamination of the adhesive film should take place without changing its adhesion properties, and the adhesive should be easy to peel – low release force to avoid destruction of the adhesive layer. The application of the adhesive film is realized in three steps: 1) delamination of the top release liner without any delamination of the adhesive film from the bottom release liner, 2) transfer of the adhesive film to the product and 3) delamination of the bottom release liner without any delamination of the adhesive film from the product. It is obvious that two different release-liner qualities are necessary to fulfill the described requirements.
Applications for such optically clear adhesive films are, for example, flat-panel displays, optically transparent protective films, lamination of flexible copper-clad laminate (FCCL) layers and smart-film applications.
Conclusion
Processes and developments for sustainable release-liner solutions are necessary to fulfill market requirements. We see increasing applications for release liners. We showed new coating solutions depending on the product, and we defined machinery concepts, which are adapted to the end product. Customized machine solutions provided by leading machinery suppliers are necessary to follow the increasing market requirements for high-quality release-liner products. This firm can demonstrate all described processes in its Technology Center.
References
1. Reardon, Corey M., “Market Overview” presentation, AWA Global Release Liner Industry Conference & Exhibition, Amsterdam, The Netherlands, Feb. 2020.
Andrea Glawe, regional sales dir. with KROENERT GmbH & Co. KG, completed her studies in 1992 with a Master’s degree in Technical Textiles and Process Engineering at the Chemnitz University of Technology (Germany). She began her career as scientific assistant and project manager in the Textile Research Institute Thüringen-Vogtland Greiz. In 2001, Glawe switched from research to industry and worked as deputy sales director with responsibility for technical sales and project management at Coatema Coating Machinery GmbH in Dormagen, Germany. In 2011, she began working for ATH, Hamburg, first as R&D manager at DRYTEC GmbH & Co KG in Norderstedt and later as R&D director, responsible for business development at KROENERT. Since October 2015, Glawe is regional sales dir.-Asia/ Pacific Market at KROENERT. She also is dir.-Strategic Advisory Board of LOPEC, the world-leading exhibition for printed electronics. Glawe can be reached at +49-17-326-3327, fax: +49-40-853-93117, email: andrea.glawe@kroenert.de, www.kroenert.de.