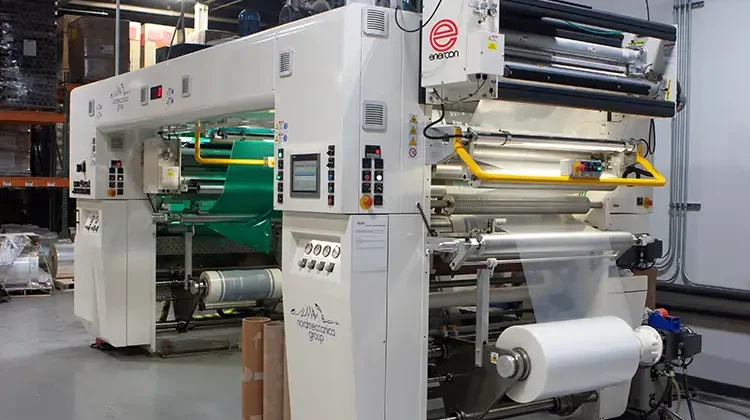
By Giancarlo Caimmi, commercial dir., Nordmeccanica Group; Amira Marine, senior technical service and development specialist, Dow; Tom Gilbertson, vp-application engineering; and Mark Plantier, vp-marketing, Enercon Industries
Introduction
Printers and converters who integrate solventless laminating enjoy a competitive advantage by offering their customers a single source for flexible packaging. Thanks to recent advancements in laminating-process technology, adhesive chemistry and equipment design, implementing a solventless-laminating operation now is much easier. However, it’s important that operators understand the basic principles and variables of the process to maximize production and reduce waste.
Choosing the right adhesive
Factors that affect choosing the right adhesive for the job include the substrates that are going to be used, any regional regulatory considerations and requirements for chemical-, product- or UV-resistance. Choosing the correct adhesive means analyzing every aspect of the converting process, not just the adhesive price. The return on adhesive investment must take into consideration scrap rate and ability to run at competitive speeds.
USA food-packaging regulations include Code of Regulations 21 CFR Part 175, which are indirect food additives for adhesives and components of coatings. Some examples include:
- Regulation 175.105 specifies adhesives for food-containment applications up to 121° F. This application is considered a general-purpose adhesive system.
- Regulation 177.1395 is for laminated structures used at temperatures between 120° and 250° F. This is considered medium-performance adhesive systems, which usually are for hot-fill applications, microwave and boil-in-bag applications.
- Regulation 177.1390 pertains to laminated structures over 250° F. These adhesive systems would be used for retort applications.
The adhesive system must be compatible with the ink. Otherwise, problems occur with poor appearance in printed areas due to high retained solvent from ink or even incorrect adhesives. Impurities on the surface and high slip in the film can result in poor or no adhesion.
Poor adhesive heat- and chemical-resistance in the printed area is an indication that the mix ratio of the adhesive is off. Retained solvents or other high-boiler additives in inks also can alter the cure.
Taking a closer look at retained solvent in lamination, one of the main factors that comes into play is the incomplete drying of inks. This is a chain termination of the adhesive polymer resulting in the poor heat- and chemical-resistance. The adhesive will remain tacky, have low bond strength and also contain residual odors.
Mixing
Most two-component, solventless-adhesive systems require the use of a mix-meter dispensing unit to properly proportion the adhesive. The correct mixing ratios are available on technical datasheets provided by your supplier. Before laminating, make sure the mixing unit is calibrated. This normally is done gravimetrically by weighing the two components after they are pumped into two separate containers.
The adhesive mix ratio needs to be monitored on a regular basis. Most mix-meter units have real-time monitoring with triggered alarms should the adhesive-mix ratio exceed the allotted tolerance.
A turning point in the industry came 20 years ago when solventless lamination evolved into an easier-to-use technology with the development of new mechanical hardware for meter-mixing dispensing of two-component adhesives. The operator-friendly system uses gear pumps, which enable digitally setting mixing ratios without any mechanical adjustments.
In this design, the two components are contained in reservoirs that are shielded from moisture in the atmosphere. Moisture is a potential trigger of catalyzation to begin. Nitrogen can be used as a neutral gas to refill the atmosphere above the adhesive in the reservoir whenever some early polymerization may be experienced.
A volumetric pump is used for this system; therefore, the mixing ratio needs to be moved from weight (the unit used in most adhesive TDS) to volume through the gravity weights. Gravity weights normally are listed because specifications may change for the adhesive in different environmental conditions.
A good mixer is equipped with three different levels of temperature control: the resin, the hardener and the hose that delivers the adhesive to the laminator. It should be noted that viscosity of even low-temperature adhesives is influenced by small temperature variations. It is important to consider that even adhesives that are handled at low temperatures (room-temperature adhesives) are influenced heavily in viscosity by small variations of temperature.
Implications of poor adhesive mix
If the adhesive mix ratio is off, you’ll have either an excess of hydroxyl or isocyanate.
- If there is excess hydroxyl, the adhesive will not cure properly and remain tacky, and thus exhibit poor heat-, chemical- and product-resistance. Generally speaking, bond strength also will be low.
- If there is excess isocyanate, it will take longer to cure, as the adhesive will be even more dependent on moisture to complete the curing. The adhesive will remain tacky until enough moisture has entered into the laminate. If it’s MDIbased, you could see some antiseal issues.
These systems are designed to handle chemicals in a liquid form with precision accuracy; therefore, following routine maintenance on the mixing system is critical.
Rolls
All the coating-head rollers for solventless laminating are engineered, sized and surface-finished to deposit the selected amount of adhesive precisely and evenly to the web. It should be noted that roll temperature and roll quality will impact the adhesive’s appearance. Roll heaters should be set to appropriate temperatures for specific adhesive systems. Recommended starting points for temperatures for each adhesive system are found on the adhesive supplier’s technical datasheets. Coating-roll cleaning is of paramount importance for the process. Any residual adhesive left on a roll surface during a job changeover will cure and result in imperfect deposition of adhesive for the next job.
Controlling the coating weight (thickness of the adhesive layer)
Technically, the aim of the coating head of a solventless laminator is to reduce the adhesive layer of a high-viscosity, chemical compound to the order of magnitude of metric microns (the range of about 0.04 mil).
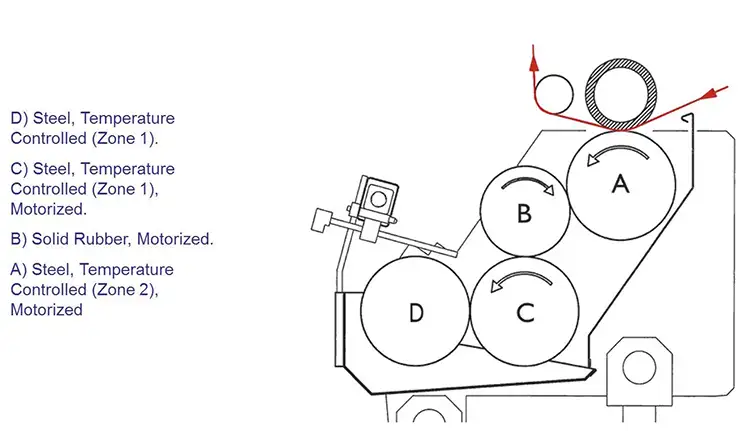
As shown in Figure 1, the process starts by dosing the adhesive between Rollers C and D. Both are chromed-polished and temperature-controlled to guarantee the maximum accuracy of their outside diameter. The distance between Rollers C and D is the first calibration of the coating weight.
The gap is adjustable and used in most applications in the 3 mils in Imperial setting (80 microns). Rollers in the coating head turn at about 10X the speed of the previous roller. If Roller B turns 10X faster than Roller C, the thickness of the layer carried by Roller C will be reduced by 10X when passing to Roller B. The same will happen when passing through Roller A. That will allow you to go from an order of magnitude of around 80 microns at the gap between Rollers C and D to an order of magnitude of about 0.80 microns, or from 3 mils to 0.03 mil at the coated layer. It is very difficult to reliably control the thickness of a chemical layer at production speed; therefore, proper engineering of the coating station is required.
Engineering overcomes the technical difficulty of compensating the normal tolerance in accuracy of rotating mechanisms in regular mechanics. Roller B, specifically, is rubber-covered and is the one that determines the coated width of the job that you are running.
That roller will need substitution and different undercuts at different web widths handled within the production process. This roller is the “weak link” in the station and needs to be superbly engineered as a solid roller to not trigger coating-weight inaccuracy. Roller A, the final roller in the transmission chain, or the glue-handling chain, turns at the machine speed and about 100X faster than Roller C.
Typical coating weights
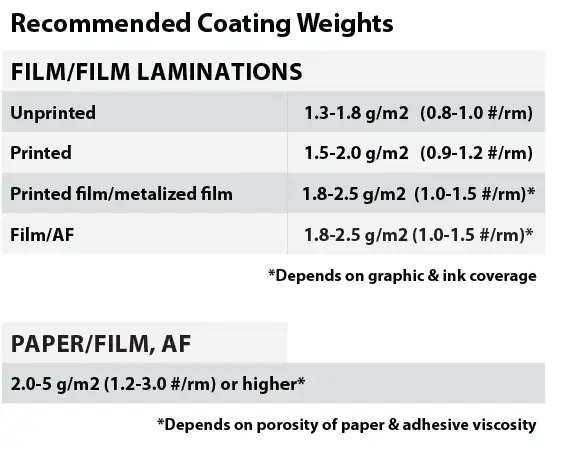
Table 1 shows typical coating weights that we recommend as a starting point based on the substrates being coated. For film-to-film laminations that are unprinted, using lower coatweights of 0.8 to 1.0 lb per ream is sufficient. For printed substrates, increasing the coating weight slightly will make up for the difference of the surface area of the print.
For metalized films and foils, coating from 1.0 to 1.5 lbs per ream is appropriate, depending on graphics and ink coverage. For applications with paper to film or foil, we recommend a higher coatweight. It also depends on the type of paper and the adhesive viscosity as well.
It is recommended to check the coatweight with fresh adhesive to avoid any buildup in the viscosity, and it’s advisable to check the coatweight across the web to ensure the adhesive coverage is uniform.
Nip conditions & tension control
Nip conditions are very important when running a solventless lamination. Just like the coating-head rollers, nip rollers need to be clean and free of defects to prevent transfer to the final laminate.
Optimal appearance is achieved when using the hottest nip temperature possible based on the substrates being laminated. A much lower temperature is used when laminating PE to PE film, as opposed to laminating PET to PE. The substrate dictates the nip temperature, and excessive nip temperatures may lead to curling and tension-control problems.
Tension control is important due to the low bond and sheer strength of the solventless adhesive. You want to balance the film elongation so that there will not be any curling or tunneling when the tension is removed.
Solventless laminators are mechanically designed for a low-friction web path with dynamic balance of the rollers. Maintenance in web handling is important. Bearings need to be monitored and replaced if they cause any friction. A bad idler roll can ruin the process and affect quality of the finished product.
A properly designed laminator for a two-ply lamination should have up to six tension-control zones, each one independently motorized with dancer rollers or load cells to ensure correct feedback from the system. This will self-adjust within the operator’s settings to guarantee the proper outcome.
Web handling should be closed-loop, and every single unwind needs to be motorized. Digital vector drives provide the best results while also allowing fewer controls. Compared to previous technologies, new laminators feature a much simpler operator interface, a significantly reduced number of control buttons and are easier to operate.
Adhesive cure
The technical definition for adhesive cure is the disappearance of any free isocyanate over time, tracked via IR analysis. The converter’s definition is how soon a laminate can be further processed. The adhesive must be fully cured to withstand slitting and pouching processes, and to be compliant for food safety.
Consult with your adhesive suppliers to identify cure times needed for safe food contact over federal and regional regulations. Generally speaking, adhesive cure depends on adhesive type. Some adhesives are fast-curing, while others require a hot room or days of storage.
Improper mixing ratios will impact adhesive cure. If the adhesive coatweight is excessive, it may take longer for the adhesive to cure. Improper storage temperatures and conditions also impact cure time of the laminate. Ideally, you should cure the laminate at a consistent temperature all year round, if possible.
Corona treaters in the solventless-laminating process
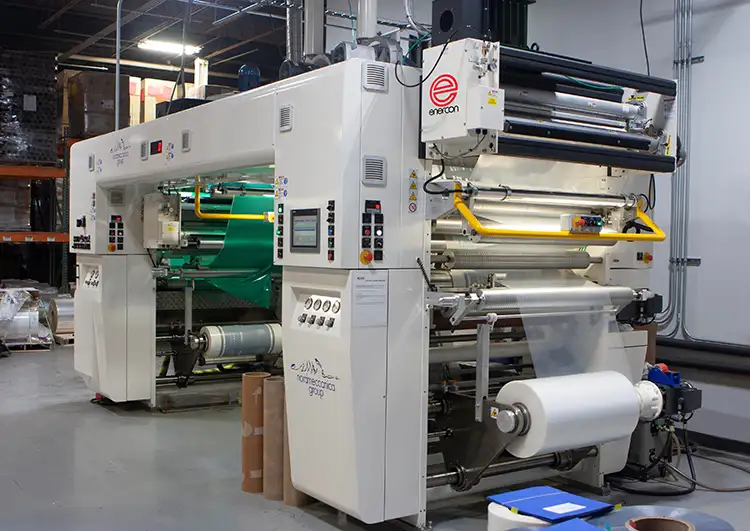
Corona treaters prepare film surfaces for bonding with solvent chemistry. Corona treaters clean, etch and functionalize surfaces to eliminate surface energy as a process variable. Industry best practice is to install treaters after the primary and secondary unwinds (see Figure 3). A corona-treater power supply generates energy to a high-voltage transformer, which boosts the energy to a higher value. That energy is sent on to the corona treater’s electrode, which generates corona.
Do pre-treated films need to be treated?
Polyethylene films are inert with initial dyne levels of 30 or 32 and no polarity. Although polyethylene films are treated at the time of extrusion, they are unable to retain the dyne levels required for successful wetting. Dyne levels diminish due to migrating surface additives, contamination, humidity and time. Bump-treating or re-treating films as part of the laminating process enable wetting-out of the adhesive chemistry.
Measuring the effect of surface treating
Dyne levels are used to measure the effect of treatment. Dyne pens are ideal for a quick check when loading a roll of film on a laminator to verify which side has been pretreated. For a more accurate dyne reading, we recommend using dyne solutions with a cotton swab as outlined by ASTM Method D2578. For more process control, follow the TAPPI method, which calls for a Mayer Rod to meter the solutions over a larger area of film consistently.
Train your employees how to conduct these tests and interpret the results. Dyne-level readings are subject to human interpretation and slight differences in results may not be significant enough to affect the success of your process. Always document your results so you can compare what has changed should you run into future problems. Remember, achieving a target dyne level does not guarantee adhesion. Dyne level is the measurement of wetting, not the measurement of adhesion.
How much treatment do I need?
Always use the least amount of corona treating required to consistently meet your application’s dyne-level target. Required power levels are based on the width of the treater station’s electrodes, the speed being run and the film’s responsiveness to corona treating. If you run different speeds or different films, your treater can be designed to handle a range of applications.
We recommend high-definition corona with ceramic electrodes and a proprietary nonconductive, ceramic ground roll. This combination treats both conductive and nonconductive films and provides the industry’s best insurance against backside treatment, pin-holing and film wrinkling.
To properly control the power output, use a power supply with watt density control. This technology adjusts the power output of the treater according to changes in line speed to ensure consistent treatment is applied. The power level needed for the primary and secondary films will not always be the same.
Installation considerations
Follow all the exhaust ducting recommendations when installing your corona treaters. Improper exhaust ducting reduces airflow and leads to problems including electrode overheating, excessive moisture and failure to remove ozone (a byproduct of corona treating.). Based on your locality, you may be able to exhaust ozone into the atmosphere. Or, if local regulations require, you can add an ozone decomposer to break down the ozone in the exhaust prior to being released to the atmosphere.
Future improvements
Adhesive suppliers and equipment manufacturers are working to develop technologies that close the processing gap and increase the speed of curing while maintaining global compliance. Advances in these areas will greatly expand the uses of solventless laminating. Reducing curing time accelerates the speed-to-market for final packaging. With recent material and equipment developments, it is now possible for it to take only six hours to reach the bagmaking stage, down from one to two days, depending on the substrate, to full curing and safe food contact. Additional developments have been made for producing higher-barrier structures with OPA and EVOH coextrusions to avoid outgassing at higher speeds than previously achievable.
Giancarlo Caimmi, commercial dir. for Nordmeccanica Group (Hauppauge, NY), holds a Ph.D. in Mechanical Engineering from University Federico Secondo (Italy). He has 35+ years of experience. In the converting-machinery manufacturing field. Caimmi can be reached at 631-242-9898, email: caimmi@nordmeccanica.com, www.nordmeccanica.com.
Amira Marine, senior technical service and development specialist at Dow (Midland, MI), holds a Bachelor’s degree in Chemistry from Roosevelt University (Chicago, IL). She has more than 12 years of experience in the laminating-adhesive field with contributions and implementation of solventless technologies in North America. Marine can be reached at 979-236-1815, email: amarine@dow.com, www.dow.com.
Tom Gilbertson, vp-application engineering at Enercon Industries Corp. (Menomonee Falls, WI), holds a degree from Lakeshore Technical College. He has over 30 years of experience in surface-treating technologies and applications for printing, coating, laminating, and film-extrusion lines. Gilbertson can be reached at 262-255-6070, email: tgilbertson@enerconmail.com, www.enerconind.com.
Mark Plantier, vp-marketing at Enercon, holds a degree from Siena College. He has 25+ years of experience in industrial packaging and converting equipment & technology. Plantier can be reached at 262-255-6070, email: mplantier@enerconmail.com.