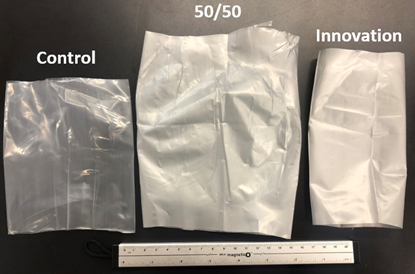
By Dante Ferrari, president, Celplast Metallized Products, Ltd., and Zheng Tian, Ph.D., scientist, Flexible Products Group (FPG), Applied Materials, North America
Currently, the only path to have flexible packaging recycled in North America is via Store Drop-Off programs, which require these packages to be predominantly based on polyethylene (PE). For many barrier applications, these PE packages must use an EVOH layer, metallizing or top-coating. We will look at all three as we investigate whether these innovations can meet the technical requirements to make a package recyclable. These requirements are: 1) passing metal detection; 2) not clogging melt-filtration systems; and 3) using these pellets to blow new film with acceptable performance characteristics. In addition, there are economic issues for the recyclers that need to handle this material.
Editor’s Note: This technical paper is based on the authors’ presentation at the AIMCAL R2R USA Conference / SPE FlexPackCon held in October 2021 in Orlando, FL.
Introduction
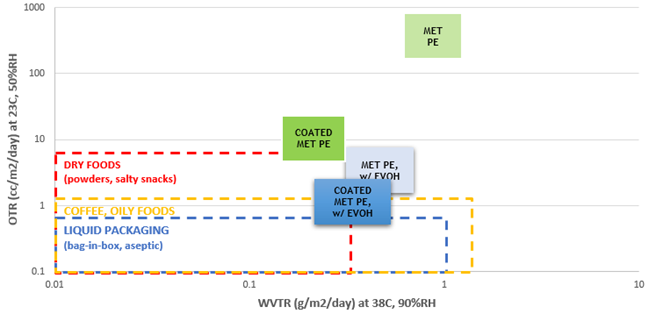
There are two main sets of market drivers when it comes to developing sustainable packaging. The first are consumer packaged goods (CPG) companies, which are trying to meet the demand from consumers and NGOs to develop more sustainable packaging. In response, most major CPGs have committed to making 100% of their packaging reusable, recyclable or compostable by 2025. Reuse programs such as Loop still are in the early stages of development. Currently, compostable-film solutions such as PLA, PHA and PBAT cannot economically meet the functional needs of most packaging applications. Therefore, CPGs continue to focus on developing recyclable packaging.
The second set of drivers are governments around the world. Their approach is to push sustainable packaging through regulation, mainly via Extended Producer Responsibility (EPR) laws. EPR allows governments to shift costs off the taxpayer, and onto the consumer, typically through municipal solid-waste tipping fees or taxes. The Province of Ontario [1], in Canada, recently announced it was transferring its Blue Box program entirely from local taxpayers to producers, which are defined as CPGs and retailers. Two US states, Maine [2] and Oregon [3], passed EPR laws in summer 2021, with more legislation imminent in other states. The main outcome of these laws is to make packaging that is hard to recycle or that doesn’t contain recycled content be more expensive.
Store drop-off programs are the most widely available recycling option for flexible packaging today, with over 40,000 retail stores participating in North America. Retailers still are educating their employees on how to segregate PE-based secondary packaging, such as stretch wrap, in the back of store, and consumers still are learning what can and can’t go into front-of-store bins. The majority of flexible packaging collected this way goes to Trex, which consumes over 1 million lbs/day of post-consumer polyethylene (PE) films in its decking products and claims to be the largest PE film recycler in the United States” [4]. Celplast and others have had several finished packages containing metallized-PE approved by Trex, which have been accepted by the NexTrex® program.
The remainder goes to other film recyclers, which convert this post-consumer material back into PCR pellets to sell on the open market or to companies such as Novolex [5], which reuses the pellets internally to produce industrial bags. These film recyclers depend on standardized labeling to ensure they are getting clean, dry material that is predominantly PE. In North America, the most widely accepted labeling system is the How2Recycle® logo. The Sustainable Packaging Coalition’s (SPC) GreenBlue® program controls what CPG products can use the How2Recycle logo. For flexible packaging, SPC bases its technical approvals on the Assn. of Plastic Recyclers’ (APR) Critical Film Guidance Protocol [6]. There are some differences between the two group’s acceptance guidelines. As both associations have stated, being acceptable under APR’s guidelines doesn’t necessarily mean you can get the How2Recycle logo, and vice-versa.
Opportunities for metallized-PE films
One thing is clear. Regardless of whether bags and pouches are going to Trex, Novolex or a PCR resin recycler, only all-PE film structures are acceptable for store drop-off in North America.
Many applications do not require a barrier layer, and standard PE films can be used. However, there are a substantial number of applications where barrier is required. Figure 1 shows a barrier map, with oxygen-transmission rate (OTR) along the y-axis and water-vapor transmission rate (WVTR) along the x-axis. This is in metric units, on a log-log scale. The barrier windows for some common food products are shown with dotted lines.
In these cases, a standard metallized-PE blown film, as shown in light green in the top right of Figure 1, typically will not be suitable for use. Either an in-line top-coated, metallized-PE film (dark green), a metallized EVOH coextruded film (light blue) or both technologies (dark blue) are required.
All of the metallized-PE films shown in Figure 1 have been approved by NexTrex, either on their own or in a finished package where they have been printed and/or laminated to other PE films. CPGs can use the NexTrex logo on their packaged goods today for store drop-off, and it will be accepted. Some have stated that through the store drop-off program their flexible packaging will be turned into “synthetic lumber and decking” [7] without explicitly using the NexTrex logo.
Challenges for metallized-PE films
Most CPGs currently consider the How2Recycle logo as the best way to communicate the recyclability of a flexible package to consumers. Working within the APR guidelines remains the most viable path to getting a package approved. This requires an open dialogue with the PE-film recyclers within APR to understand the challenges they face when attempting to process metallized-PE films.
Challenge #1: Metal detection: All PCR-film recyclers have metal detectors at the front end of their shredding and extrusion equipment. This allows recyclers to separate out keys, coins, foil pouches and other materials that could cause damage to their equipment.
An electromagnetic field is generated in the tunnel, then the system looks for an electrical disturbance in the field to indicate if any ferrous or non-ferrous metals are present. Flexible packages are passed through the conveyor in different orientations, and the orientation that gives the strongest signal is recorded. Next, mild steel spheres are passed through the conveyor until a sphere size matching the signal of the package is obtained. This is referred to as the “sphere-size equivalent.” The recyclers’ experience is that any object with a sufficiently large sphere-size equivalent will damage their equipment, while smaller objects can be detrimental, affecting operations, and still smaller objects are fine.
The three categories as defined in APR’s SORT-B-03 Metal Sorting protocol [8] are:
- 0-2 mm: APR Design Guide Preferred
- >2 to <12 mm: Detrimental to Recycling – can affect quality, yield or operating costs of the recycler
- ≥12 mm: Non-recyclable per APR Definition
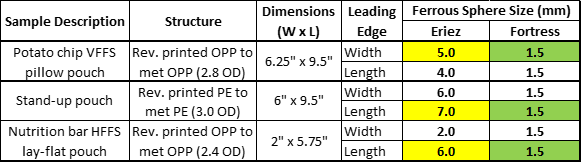
To test how metallized films performed, we first sent three different commercial product samples to two different metal detector OEMs, Eriez and Fortress Technologies, which ran them through their equipment and reported back the results. A summary is shown in Table 1, with “worst case” values highlighted in yellow for Detrimental, and then green for Preferred.
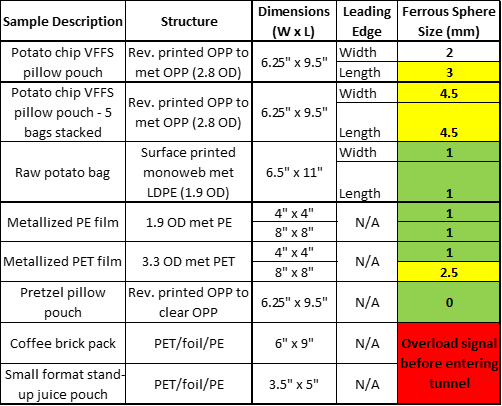
There are obviously measurement differences between the different test labs. We then carried out a subsequent study with several other samples at Fortress Technologies (see Table 2).
These findings, and additional data, lead to several conclusions:
- Even within a single test facility, there can be variation in sphere-size values when different samples of the same package (for Lay’s Potato Chips in this case) are tested.
- Multiple pouches stacked together give a diminishing signal. Five bags stacked gave only a 50% signal increase over a single bag.
- The substrate being metallized doesn’t have a significant impact on sphere size.
- Any printed or laminated webs on top of the metallized layer don’t have a significant impact on sphere size.
- 1.9 OD metallized films are Preferred, at a variety of different sample sizes.
- 3.3 OD metallized films are Preferred at small sizes, Detrimental at larger sizes.
- Clear films give no metal detection value.
- Foil pouches, even relatively small ones, give values ≥12-mm sphere size and clearly are non-recyclable according to the APR Metal Sort protocol.
Challenge #2: Melt filtration: Some APR film recyclers have claimed that metallized pouches plug up their melt filtration systems. The size of aluminum crystals in metallized layers are orders of magnitude smaller than particles such as antiblock or some pigments, both of which do not plug melt filtration, so these results are confusing. There could be other factors involved, such as what were assumed to be metallized pouches actually were foil pouches or other non-compatible materials in the pouches caused the clogging. Celplast recently visited the operation of post-industrial recycler Vision Plastics in Toronto. Its experience was that printed, metallized-PE bags did not lead to any screenpack build-up or gelling during commercial-scale recycling runs of 1-2 tonnes at a time.
APR is coordinating a large-scale melt filtration study, which will include comparing metallized to clear PE films, to further investigate this. The current APR Critical Film Guidance Protocol [9] uses a series of standard procedures to evaluate melting process and final product differences between clear and metallized-PE films. This guidance protocol sets difference / delta limits.
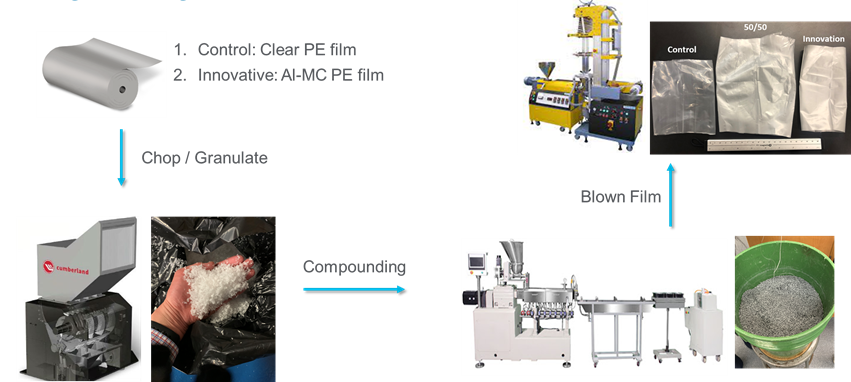
Figure 2 shows the recyclability testing flowchart of a metallized-PE product, following APR testing protocol, counter-clockwise from upper left. All evaluations were completed by external third parties.
- Step 1: Unwind and grind clear PE (Variable 1, as Control) and aluminum metallized-PE with functional topcoat (Variable 2, as Innovative) film rollstocks into small flakes, separately. Dump flakes into water bath for bulk density evaluation. Then three flake blends were prepared for later compounding. Flake Blend 1: 100% Variable 1; Flake Blend 2: 50% Variable 1 + 50% Variable 2; and Flake Blend 3: 100% Variable 2.
- Step 2: Compounding and pelletizing of three flake blends at twin-screw compounder, separately. Such repelletized resins were tested in an analytical laboratory, including melting temperature, flow index/rate, FTIR for composition, etc.
- Step 3: Convert repelletized resins into thin single-layer films at blown-film extrusion machine. Optical and mechanical properties of resulting films were collected and compared.
For Step 2, APR Critical Film Guidance Protocol requires the evaluation of backpressure changes and screenpack clogging after 45 mins of run time on a lab extruder, with 40/150/40-mesh screenpack.
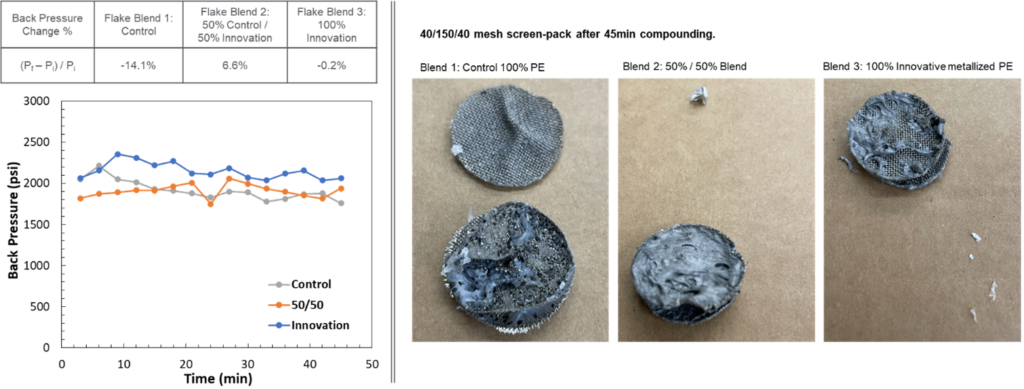
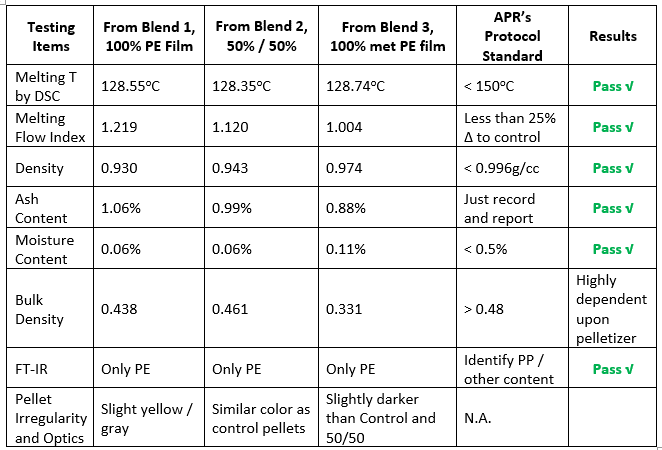
Extruder backpressure variations over 45 mins of all three flake blends were tracked in Figure 3, and then screenpacks were opened to check for clogging. Melting zones and die of extruder were set at 138 ~ 232° C. Screw speeds were selected to achieve the maximum output rate possible for each blend – 70 RPM. There was no trend of significant pressure change with time, suggesting no contaminants were trapped and clogged the screen pack (see Figure 3 left). All materials satisfied APR’s standard that end pressure is no greater than 25% over starting pressure value. Visual inspection of the screen pack removed after the compounding process revealed no trapped hard particles (see Figure 3 right). After pelletizing, the new resins were dried at 90° C for 3 hrs.
Challenge #3: Properties of re-pelletized resins with metallization content: Lab analysis was conducted on these new resins, as summarized in Table 3. For most thermal and mechanical properties, the difference between Blend 1, 2 and 3 is quite small, satisfying APR’s standard. The only property out-of-spec is resin bulk density, with all resins below 0.48 g/cc. We believe pelletizer blade maintenance and running status have a certain impact on this. The blown-film converting process using these resins didn’t raise any processing issues. For resin color, re-pelletized resin with metallized-PE content has a grayish color.
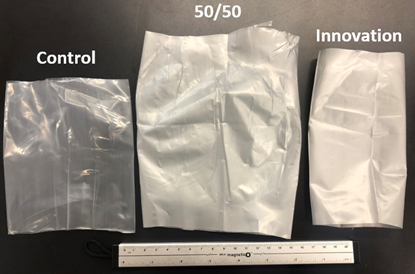
Challenge #4: Properties of recycled blown films with metallization content: With these re-pelletized resins, the next step was to run blown film following the APR standard. Blown-film converting was conducted on a lab-scale machine, with a 30-mm annular die and extruder with 40/60/40-mesh screenpack. Processing temperature was 204 ~ 238° C, with blow-up ratio between 2.2 and 2.7 among all three resin variables.
Representative pictures of three final film samples are shown in Figure 4. As already observed in re-pelletized resins, film samples with innovative metallized-PE content are optically transparent, but with a grayish color. This can be compensated for by adding color masterbatch in commercial applications.
Following APR’s testing protocol, Table 4 compares the mechanical properties of all three film products, including gauge, tensile strength, elongation ratio at yield, tear and dart drop resistance. Specifically for Blown Film 2 with 50% wt. control PE and 50% wt. innovative metallized-PE, most mechanical performances are even higher than film made from 100% control PE. Only Dart Drop resistance dropped out-of-spec. This could be further improved by introducing a compatibilizer for a better material distribution across the majority PE matrix.
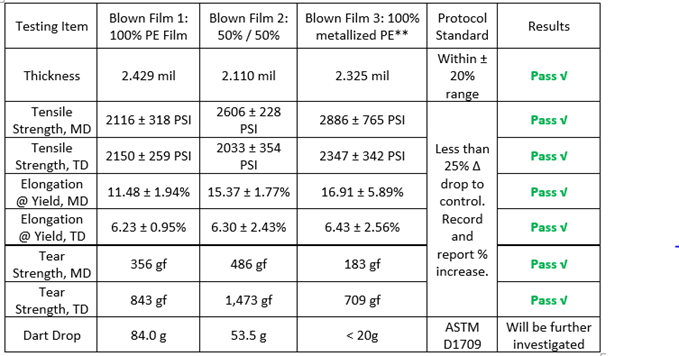

Besides mechanical strength of recycled-PE films, plastics recyclers and converters also have high standards for optical quality, requiring minimal visual defects like gels, carbon black, pinholes, etc. Accordingly, visual appearance of both the control and test films were independently evaluated by a third-party lab using Critical Film Guidance Protocol criteria. The results in Table 5 show that metallized-PE content doesn’t hurt optical quality, with an A Grade achieved.
Summary and Conclusions
The metallization process of PE film can be improved with an additional EB top-coating for high-barrier packaging applications. Independent studies were carried out to determine if metallized PE film products could meet the technical requirements of being labeled recyclable. Findings: 1) Laminated structures containing metallized barrier films can meet APR “Preferred” metal detection requirements if those packages are of sufficiently low aluminum optical density or size; 2) Metallized + coated PE film could be flaked and re-pelletized without any clogging at melting filtration; 3) Blowing film with recycled metallization content showed acceptable mechanical and optical characteristics. These results suggest that metallization and top-coating technologies will have a role to play in providing recyclable high barrier solutions to the flexible packaging industry, can be accepted into the recycling stream and provide an additional feedstock for sustainable reuse.
References
- https://ero.ontario.ca/notice/019-2579
- https://www.natlawreview.com/article/maine-becomes-first-state-to-sign-extended-producer-responsibility-law-packaging
- https://www.waste360.com/legislation-regulation/oregon-joins-maine-and-passes-epr-legislation
- https://recycle.trex.com/view/educate
- https://www.packaginginsights.com/news/novolex-reinvigorates-us-store-collection-recycling-with-plastics-water-treatment-investment.html
- https://plasticsrecycling.org/images/pdf/design-guide/test-methods/APR-pe-film-cg-fpe-cg-01.pdf
- https://www.generalmills.com/en/News/NewsReleases/Library/2021/February/Nature-Valley-Launches-First-Ever-Store-Drop-Off-Recyclable-Snack-Bar-Wrapper
- https://plasticsrecycling.org/images/Design-Guidance-Tests/APR-SORT-B-03-metal-sort-protocol.pdf
- https://plasticsrecycling.org/images/pdf/design-guide/test-methods/APR-pe-film-cg-fpe-cg-01.pdf
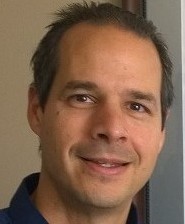
Dante Ferrari, president of Celplast Metallized Products, Ltd. (Toronto, Ontario, Canada), holds Bachelor’s and Master’s degrees in Engineering Chemistry from Queen’s University (Kingston, ON) and an MBA from the Ivey School of Business, University of Western Ontario (London, ON). He has 25 years of experience in the flexible packaging industry, with nearly 20 years at high-barrier film solutions provider CMP. Dante also currently serves as President of the AIMCAL Board of Directors. He can be reached at office: 416-644-3507, mobile: 416-918-8790, email: dante@celplast.com, www.celplast.com.
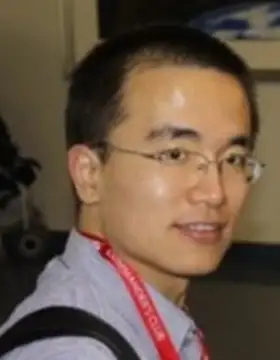
Zheng Tian, scientist, Flexible Products Group (FPG), with Applied Materials, North America (Santa Clara, CA), holds a Bachelor of Science in Chemical Engineering from Tsinghua University (Beijing, China), and a Ph.D. in Chemical Engineering from Lehigh University (PA). His current work is focused on metallization and coating processes on various packaging substrates. Before joining Applied Materials, Zheng worked in research and development at flexible-packaging converters Bemis and Amcor. He can be reached at 484-767-1305, Zheng_Tian@amat.com, www.appliedmaterials.com.